At 3:00 AM, a sudden hydraulic pump failure in a manufacturing facility caused a high-pressure oil leak that reached the ceiling. Within three minutes, 200 liters of hydraulic fluid had completely drained. Emergency repair teams arrived within two hours, but the production line was forced to shut down for 48 hours, resulting in direct losses exceeding $40,000.
Why do most hydraulic hose bursts have clear warnings? Which critical signs must never be ignored?
Danger Signal 1: Bulging on Hose Surface Indicates Imminent Wire Breakage
A bulging hose surface is an early warning sign of structural failure, often caused by internal wire reinforcement breakage. Understanding hydraulic hose construction is key to identifying these risks:
Technical Analysis:
Hydraulic hoses typically have a robust three-layer construction designed for high-pressure operation:
- Inner Rubber Layer: This layer directly transports hydraulic fluid, providing a leak-proof conduit and resistance against fluid corrosion.
- Wire Reinforcement Layer: Usually composed of high-strength steel wire braided or spiral-wrapped, this critical layer supports and withstands internal pressures.
- Outer Rubber Protective Layer: This layer acts as a shield, protecting the wire reinforcement layer from external damage, abrasion, weathering, and environmental factors.
When a hydraulic hose exhibits bulging on its surface, it indicates internal damage—specifically, wire reinforcement breakage or severe degradation. This failure typically occurs due to continuous exposure to fluctuating pressures, bending stress, or external impacts. Once the wires are compromised, the inner rubber layer alone attempts to sustain the pressure, causing the rubber to expand outward and form noticeable bulges.
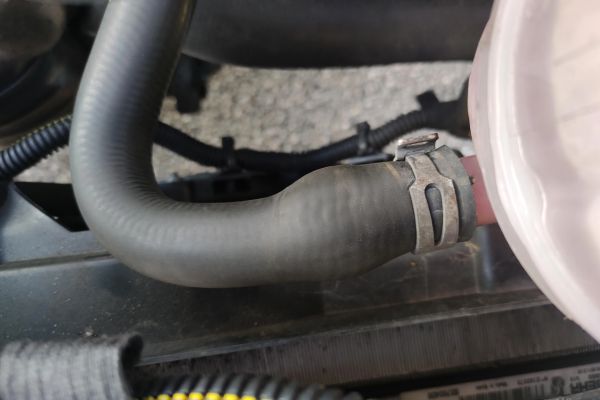
According to the ISO 1436 testing standards, the presence of such bulges significantly reduces the hose’s original pressure resistance by approximately 70%. Continuing to operate a hose under these compromised conditions drastically increases the likelihood of sudden catastrophic rupture, risking severe equipment damage, production downtime, costly repairs, and potentially serious injuries to operators nearby.
Routine Inspection Method:
To effectively identify early signs of bulging and proactively manage risk, implement the straightforward yet highly effective “Touch + Light” inspection method:
- Touch Inspection: Carefully and gently run your hand along the entire length of the hydraulic hose, paying close attention to areas near fittings, bends, or points subject to frequent flexing. Feel for irregularities such as lumps, soft spots, or unexpected bulging, which could indicate internal structural damage.
- Light Inspection: Complement tactile checks by visually inspecting the hose using a powerful flashlight or inspection lamp. Shine the light at a slight angle across the hose surface to highlight subtle deformities or irregular shadows. Focus especially on hard-to-reach or visually obscured hose sections, as hidden bulging often goes unnoticed through casual inspection.
Danger Signal 2: Continuous Oil Seepage at Connections (More Than 3 Drops/Minute)
Technical Analysis:
Continuous oil seepage at hydraulic hose connections is often mistakenly considered a minor nuisance rather than a critical issue. In reality, even seemingly small leaks can escalate quickly into serious problems.
Consider this scenario: A leakage rate of merely 3 drops per minute results in approximately 16 liters of hydraulic oil lost each year. This loss not only impacts operating costs but also poses substantial threats to the reliability of the entire hydraulic system.
Persistent seepage allows hydraulic oil to accumulate around connections, creating an ideal environment for corrosion. Corrosion progressively weakens hose fittings and connection integrity. According to the GB/T 7939 standards, corrosion weakens the joint’s burst resistance by up to 40%, increasing failure risk.. Consequently, weakened joints are more likely to fail under operating pressures, risking sudden rupture and serious equipment damage or personal injury.
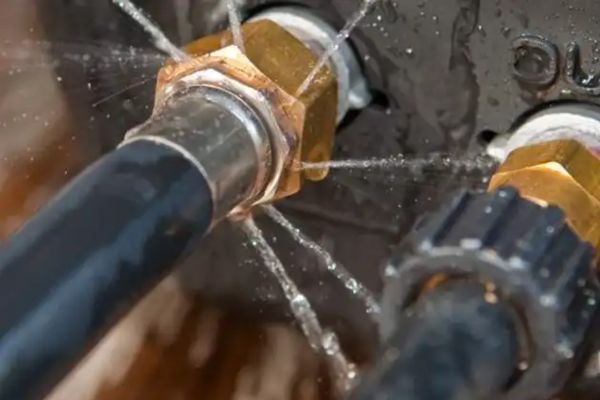
Emergency Inspection and Handling:
To promptly identify and address seepage issues, utilize the effective two-step detection method:
Step 1: Tissue Paper Test
- Procedure: Thoroughly clean the suspected leak area using a dry tissue or absorbent cloth. After cleaning, wait approximately 10 minutes without operating the equipment.
- Observation: Re-inspect carefully. Any new oil droplets or stains appearing on the tissue indicate active leakage and warrant immediate further action.
Step 2: UV Fluorescence Detection
- Procedure: Apply a UV fluorescence leak detection fluid designed specifically for hydraulic systems around the suspicious connection area. After running the system briefly under normal operating conditions, use a UV flashlight to inspect the connection.
- Observation: Leaks—even minuscule ones—will be clearly highlighted as glowing areas under UV light, pinpointing the precise leakage source for accurate repair.
Danger Signal 3: Abnormal Hose Vibration (Frequency Over 2Hz)
Technical Analysis:
Under normal operating conditions, hydraulic hoses experience slight vibrations with frequencies typically at or below 1Hz. Such minor vibrations are usually harmless, reflecting standard fluid movements and normal operational patterns.
However, when vibrations consistently exceed 2Hz, it’s a clear and urgent indicator of underlying system instability. Excessive hose vibration often signals critical issues such as:
- Pump Malfunction: Worn or damaged pump components can introduce irregular fluid pulses, resulting in rapid vibration.
- Valve Issues: Malfunctioning or improperly adjusted valves cause erratic flow patterns and fluid pulsation, contributing to instability and accelerated wear.
- Pipeline Blockages: Partial obstructions within hydraulic lines lead to irregular pressure fluctuations, significantly raising the risk of hose fatigue and eventual rupture.
Continuous exposure to excessive vibrations weakens hose structures, damages fittings, and drastically reduces the operational lifespan of hydraulic components. If overlooked, these issues can culminate in sudden and catastrophic hose failure, system downtime, substantial financial losses, and potential injuries to nearby operators.
Detection Method:
Regular monitoring of hydraulic hose vibrations enables early detection of problems, allowing maintenance personnel to intervene before failure occurs. Two practical approaches for vibration detection include:
Quick Detection Method (Smartphone Application):
- Download a reliable vibration measurement application such as “Vibration Meter“ available for both iOS and Android devices.
- Firmly place your smartphone against the hose or associated fittings, ensuring direct contact.
- Activate the measurement and observe real-time frequency readings. Any persistent reading above 2Hz warrants immediate system evaluation.
Professional Solutions (Industrial-Grade Monitoring):
- Install professional vibration monitoring equipment designed explicitly for industrial environments, such as the SKF Multilog System.
- These systems continuously monitor vibration levels and provide automated alerts when abnormal frequencies or patterns emerge, enabling predictive maintenance.
- With professional monitoring in place, operators receive real-time insights into system health, facilitating proactive interventions and significantly reducing the risk of catastrophic failures.
Danger Signal 4: Sustained Oil Temperature Above 80°C Accelerates Hose Aging
Technical Analysis:
Hydraulic hoses are highly sensitive to temperature, with heat exposure dramatically influencing their longevity. The relationship between temperature and hose lifespan can be explained scientifically using the Arrhenius equation, which states that for every incremental rise in temperature (typically every 8°C increase), the rate of chemical aging in rubber compounds approximately doubles.
In practical terms, continuous operation at elevated temperatures drastically accelerates the aging process of the hose’s rubber material. For instance, a standard nitrile rubber hydraulic hose, which normally has a lifespan of around 5 years under ideal operating conditions (below 60°C), will see its effective lifespan reduced dramatically to roughly 6 months when consistently exposed to temperatures of 80°C or higher.
Such accelerated aging results in embrittlement, reduced flexibility, increased susceptibility to cracking, and weakened structural integrity, significantly raising the risk of sudden hose failure under normal operating pressures. Neglecting the thermal conditions of your hydraulic systems can thus lead directly to costly breakdowns, unexpected downtime, and hazardous safety incidents.
Quick Cooling and Long-term Solutions:
Addressing elevated temperatures in hydraulic systems requires both immediate corrective actions and strategic long-term planning:
Immediate Solutions (Rapid Cooling):
To quickly bring down excessive hose temperatures and temporarily alleviate thermal stress, take the following steps to install air-cooled heat sinks effectively:
- Identify High-Temperature Sections: Use thermal imaging or handheld infrared thermometers to pinpoint overheating sections in your hydraulic hose assembly.
- Install Air-cooled Heat Sinks: Secure specialized air-cooled heat sinks (available commercially) directly onto overheated hydraulic hose segments.
- Ensure Adequate Ventilation: Arrange hoses and surrounding equipment to optimize airflow around installed heat sinks, maximizing cooling efficiency.
- Continuous Monitoring: Regularly monitor temperatures post-installation to ensure effective heat dissipation.
Long-term Recommendations (High-Temperature Resistant Hoses):
For permanent mitigation of overheating risks and prolonged hose lifespan, consider transitioning your hydraulic system to advanced, heat-resistant hose materials:
High-Temperature Hose Materials: Upgrade to hydraulic hoses made from polyurethane reinforced with aramid fiber layers, specifically engineered to withstand continuous exposure up to 120°C.
Material Benefits:
Aramid Fiber Reinforcement: Provides exceptional strength, stability, and resistance to thermal degradation.
Polyurethane Outer Layer: Enhances overall durability, flexibility, and heat resistance compared to traditional nitrile rubber hoses.
Danger Signal 5: Pressure Fluctuations Exceeding ±15%, Indicating System Collapse
Why Pressure Fluctuations Matter?
If your hydraulic system is experiencing pressure fluctuations greater than ±15%, it’s a clear and serious warning sign that the system is dangerously unstable. Hydraulic systems, by design, require minimal variations in pressure to operate efficiently and safely. According to the GB/T 3766 standard, hydraulic systems should typically maintain pressure fluctuations within ±10%. When fluctuations exceed ±15%, the resulting frequent and severe changes in internal stress can dramatically shorten hose lifespan, weaken fittings, and potentially cause catastrophic damage to pumps and other critical system components.
Prolonged instability, characterized by significant pressure oscillations, imposes continuous mechanical stress on the hose structure, accelerating the fatigue of the wire reinforcement layer. Over time, these persistent stresses lead to cracking, leaks, or even complete hose rupture, causing severe downtime, production disruptions, expensive repairs, and serious safety hazards.
Technical Analysis
Hydraulic pressure fluctuations typically stem from underlying system issues, including:
- Pump Malfunctions: Worn, damaged, or improperly functioning pumps introduce irregular pulses and unpredictable fluid delivery, resulting in significant pressure oscillations.
- Poor System Design: Improperly sized components, incorrect pipe routing, or insufficient fluid capacity can exacerbate flow turbulence, leading to pressure instability.
- Inadequate Buffer Mechanisms: Systems lacking appropriate accumulators or damping devices fail to absorb and smooth out pressure spikes, increasing the likelihood of damaging fluctuations.
Continuous oscillation creates cyclical stresses that significantly compromise the structural integrity of hydraulic hoses and fittings. This cumulative damage dramatically raises the likelihood of sudden hose failures, often without sufficient warning, thereby endangering both machinery and operators.
Practical Handling Solutions
To effectively manage and mitigate dangerous pressure fluctuations, implement the following practical solutions immediately:
1. Accumulator Installation
An accumulator serves as a crucial buffering device to smooth pressure variations and absorb hydraulic shocks. Select and install an accumulator with appropriate capacity by:
- Calculating the accumulator volume accurately using your system’s specific flow and pressure requirements. Typically, a good rule of thumb is to set the accumulator volume at approximately 20% of your hydraulic system’s flow rate (e.g., a 100 L/min flow rate would require around a 20-liter accumulator).
- Positioning the accumulator strategically near pumps or control valves where pressure fluctuations originate to effectively minimize stress.
2. Digital Pressure Gauge Monitoring
- Regularly monitor and record system pressure using high-quality digital pressure gauges. Recommended brands include WIKA or similar industrial-grade gauges with built-in fluctuation alarms.
- Program gauges to trigger immediate alerts if pressure fluctuations surpass the safe ±10% operating threshold, allowing maintenance personnel to intervene swiftly before severe damage occurs.
3. Routine Inspection and Maintenance
- Incorporate regular checks of hoses, fittings, pumps, and valves into your preventive maintenance schedule. Identify and rectify underlying issues such as worn pumps, faulty valves, or clogged lines promptly.
- Train personnel to recognize early symptoms of pressure instability, ensuring quick and effective corrective action.
Emergency Self-Rescue Guide for Hose Burst Situations
A hydraulic hose burst is a critical and dangerous event, and immediate response can prevent severe injury and damage. Here’s a detailed guide to effectively handle the situation if you experience a hose burst:
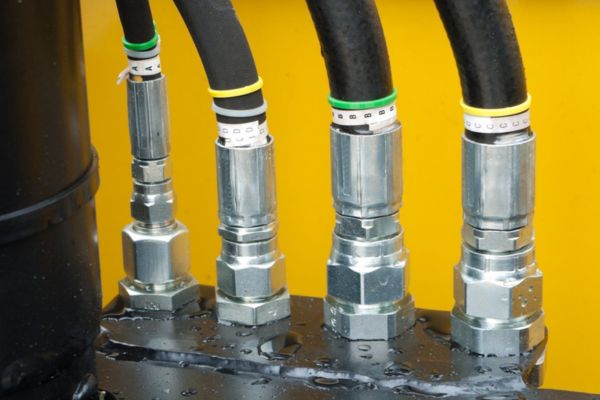
Step 1: Immediately Move to Safety
The first and most crucial action is to move swiftly away from the area of the burst. Position yourself perpendicular to the direction of the hose. This orientation significantly reduces the risk of being struck directly by high-pressure oil spray or any flying debris. Maintain a safe distance until the immediate hazard has been mitigated.
Step 2: Quickly Shut Down the System
As soon as you’re safely away, activate the emergency stop button to halt system operations. Then, proceed carefully to turn off the main power supply to the hydraulic pump. This action immediately stops further fluid flow and reduces internal pressure, minimizing potential damage and safety risks.
Step 3: Temporarily Contain the Leak
Once the power is safely cut and pressure has dropped to safe levels, carefully approach the site of the leak. Use wooden wedges or specialized hydraulic leak plugs to temporarily block the rupture and prevent further fluid loss or contamination. Under no circumstances should you attempt to handle or block the leak with bare hands or non-specialized tools, as high-pressure fluid can cause severe injuries.
Following these steps promptly and carefully can greatly reduce the severity of damage and risk of injury from hydraulic hose bursts.
Core Safety Principles (Maintenance Guidelines and Advice)
Effective maintenance and careful management of hydraulic systems significantly reduce the risk of catastrophic failures. Adhering strictly to these core safety principles is critical for ensuring continuous and safe operations:
Principle 1: “Better Safe Than Sorry”
Any abnormal sign, regardless of its perceived seriousness, must be investigated promptly—ideally within 30 minutes. Immediate action reduces the risk of minor issues escalating into catastrophic events, safeguarding personnel, equipment, and operational continuity.
Principle 2: Purchase Quality-Assured Hoses
Always choose hydraulic hoses that meet stringent quality standards, ensuring reliability and performance. Adhere strictly to the “Three-code” identification system for hydraulic hoses:
- Production Batch Code: Ensures traceability and accountability of manufacturing processes.
- Quality Inspection Code: Confirms the hose has undergone thorough testing and inspection.
- Anti-Counterfeit Code: Guarantees authenticity, preventing substandard or counterfeit products from entering critical systems.
Principle 3: Never Substitute Hydraulic Clamps
Specialized hydraulic clamps are designed specifically to handle intense pressures within hydraulic systems. Replacing them with ordinary hose clamps is highly dangerous, as the pressure resistance difference between the two can be as much as tenfold. Always use clamps and fittings explicitly engineered for hydraulic applications to prevent dangerous failures.
By diligently applying these safety principles, organizations significantly enhance operational reliability and personnel safety.
Conclusion
Hydraulic hose bursts pose severe risks, both economically and physically. Regular and systematic maintenance is vital to ensure safety and operational continuity. Don’t wait for disaster; follow these guidelines, carry out regular checks, and take immediate action when warning signs appear. If you need quality hydraulic hoses, please contact us, Topa can provide the best products!
FAQ
Does a bulging hydraulic hose mean it must be replaced?
Yes. A bulge usually indicates that the internal wire layer has been broken or damaged, and should be replaced immediately as there is a risk of bursting if the hose continues to be used.
Is it normal to have a small amount of oil leakage from a hose connection?
No, it is not. Even a few drops per minute can lead to corrosion, pressure loss and coupling failure in the long term and must be addressed promptly.
How can I quickly check for abnormal hose vibration?
You can use your cell phone’s vibration test app (e.g., Vibration Meter) to get close to the hose, and if the frequency exceeds 2Hz, you need to check the system.
How does high temperature affect hydraulic hoses?
Continuous temperatures over 80°C will accelerate the aging of rubber and shorten the life of the hose to 1/10 of the original, so you should use high temperature resistant materials or install heat dissipation devices. 5.
How are pressure fluctuations harmful to the system?
Pressure fluctuations of more than ±15% can cause system instability, hose fatigue, and seal damage. It is recommended that an accumulator be installed and pressure monitored.
What should I do in the event of a pipe bursting?
Stay away from the injection area, disconnect the power supply, use a special tool to temporarily seal the leak after the pressure has been relieved, and contact your service team.