Hydraulic hoses are the lifelines of countless industrial and mobile equipment systems, transferring power that keeps operations running smoothly. When these critical components fail—whether from age, abrasion, excessive pressure, or environmental damage—every minute of downtime translates to lost productivity and revenue. Understanding emergency repair methods like patching, binding, and splicing isn’t just helpful—it’s essential for minimizing costly interruptions.
Understanding Hydraulic Hose Damage: Diagnosis Before Repair
Before attempting any hydraulic hose repair, proper diagnosis is essential. Like a doctor examining a patient, you need to thoroughly assess the damage to determine the most effective treatment approach.
Visual Inspection Techniques to Identify Damage Types
Start your diagnosis with a methodical visual inspection. Look for these common damage indicators:
- External Abrasion: Examine the outer cover for scuffing or worn areas where the reinforcement layer might be exposed. This typically occurs when hoses contact with moving parts or rough surfaces.
- Kinking and Crushing: Check for sharp bends or flattened sections that restrict flow and weaken the hose structure. These deformations often indicate improper installation or external impact.
- Blistering and Bubbles: These raised areas suggest internal damage where fluid has penetrated between hose layers. This is a critical warning sign of imminent failure.
- End Fitting Damage: Inspect for corrosion, cracks, or deformation at connection points. Look for weeping or seepage around fittings, which indicates seal degradation.
- Age-Related Cracking: Small surface cracks perpendicular to the hose length indicate UV damage or chemical exposure. These hairline fractures can quickly develop into leaks under pressure.
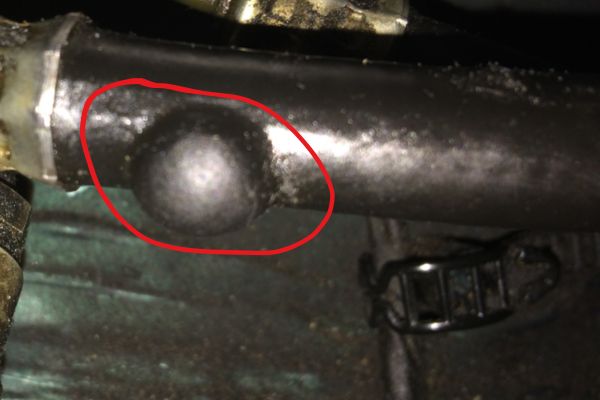
Pressure Testing to Locate Hidden Leaks
Not all damage is visible to the naked eye. For suspected leaks that aren’t immediately apparent:
- Low-Pressure Air Test: Apply 10-15 PSI of air pressure and spray the hose with soapy water. Bubbles will form at leak points.
- Controlled Hydraulic Test: Gradually increase system pressure to 50% of the operating level while carefully inspecting for seepage or spray. Never exceed safe pressure ratings during testing.
- Ultrasonic Testing: For critical applications, ultrasonic leak detectors can identify microscopic leaks before they become catastrophic failures.
The Anatomy of a Hydraulic Hose and How It Affects Repair Options
Understanding hose construction is crucial for effective repairs:
- Inner Tube: The innermost layer that contains the hydraulic fluid. Damage here requires more extensive repair or replacement.
- Reinforcement Layer: Typically braided or spiraled wire that provides pressure resistance. If this layer is compromised, repair options become limited.
- Outer Cover: Protects against environmental damage and abrasion. Surface damage limited to this layer often permits successful repair.
- End Fittings: Connect the hose to system components. Fitting damage may require specialized repair techniques or complete replacement.
The depth of damage through these layers directly determines your repair options. Surface-level repairs can address outer cover damage, while reinforcement layer damage requires more robust solutions.
When Repair is Possible vs. When Replacement is Necessary
Make this critical decision based on these factors:
Repair is Generally Possible When:
- Damage is limited to outer cover
- The leak is small and localized
- Operating pressure is below 3,000 PSI
- The hose is in otherwise good condition
- The repair is temporary until replacement is available
Replacement is Necessary When:
- Multiple layers are compromised
- The reinforcement layer is severely damaged
- The hose operates at very high pressures (4,000+ PSI)
- The hose shows signs of widespread deterioration
- The application is safety-critical (e.g., lifting equipment)
- The hose has exceeded its service life
Essential Tools and Materials for Emergency Hydraulic Hose Repair
When hydraulic hoses fail unexpectedly, having the right tools and materials on hand can mean the difference between a quick fix and costly downtime. A well-prepared emergency repair kit is an investment that pays dividends when pressure is mounting—both in your hydraulic system and on your timeline.
Must-have Items in Your Hydraulic Repair Kit
Every professional hydraulic technician or equipment operator should maintain a comprehensive repair kit containing:
- Hose Cutters: High-quality cutters designed specifically for hydraulic hoses ensure clean, square cuts essential for proper repairs. Standard utility knives or hacksaws often create jagged edges that compromise repair integrity.
- Measuring Tape: Precision is critical when measuring replacement sections or determining repair area dimensions. A flexible steel measuring tape with both imperial and metric markings is ideal.
- Cleaning Supplies: Microfiber cloths, brake cleaner, and isopropyl alcohol (90%+) for thoroughly cleaning damaged areas before repair. Contamination is the enemy of effective adhesion.
- Portable Pressure Gauge: A glycerin-filled gauge with appropriate pressure range allows you to test repairs incrementally before returning to full system pressure.
- Assorted Clamps: Various sizes of hose clamps, including T-bolt, worm-drive, and emergency pipe repair clamps for temporary containment of leaks.
- Containment Materials: Absorbent pads, drip trays, and containment barriers to manage hydraulic fluid during repair operations and prevent environmental contamination.
- Basic Hand Tools: Adjustable wrenches, socket sets, and screwdrivers for removing fittings and accessing damaged hoses in tight spaces.
Specialized Adhesives and Their Applications
Different hydraulic repair scenarios require specific adhesive solutions:
- Epoxy Putties: Two-part epoxy putties like Devcon Plastic Steel or Loctite Fixmaster can withstand pressures up to 3,000 PSI when properly applied. These are ideal for patching small holes or cracks in straight sections of the hose.
- Hydraulic Repair Tapes: Self-fusing silicone tapes like Rescue Tape or FiberFix can withstand temperatures from -65°F to 500°F and pressures up to 950 PSI when wrapped with sufficient tension and layers.
- Liquid Sealants: Products like Permatex Hydraulic Sealant or Loctite 567 are designed for thread sealing but can reinforce minor seepage areas when used with other repair methods.
- UV-Curable Resins: Advanced repair compounds like 3M Scotch-Weld or BlueDevil Hydraulic Stop Leak cure rapidly when exposed to ultraviolet light, creating a durable, pressure-resistant seal.
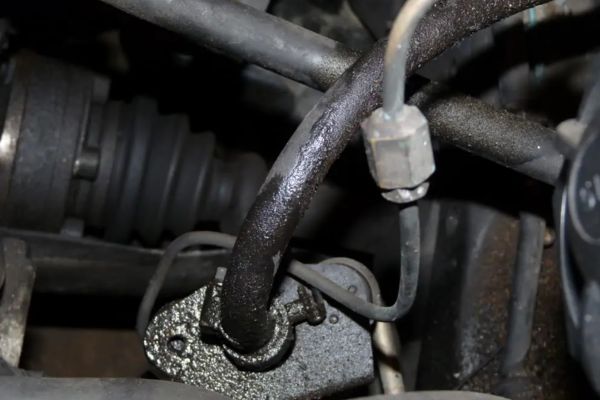
Reinforcement Materials for Different Pressure Ratings
The pressure rating of your hydraulic system dictates the appropriate reinforcement materials:
- Low Pressure (Under 1,000 PSI):
- Rubber repair patches with self-adhesive backing
- Standard hose clamps with rubber backing
- Self-amalgamating tape (minimum 4 layers)
- Medium Pressure (1,000-3,000 PSI):
- Stainless steel repair sleeves with rubber lining
- Fiber-reinforced repair tapes (minimum 6 layers)
- Two-part epoxy with fiberglass reinforcement mesh
- High Pressure (3,000+ PSI):
- Split-sleeve hydraulic clamps with urethane seals
- Carbon fiber repair kits with specialized epoxy
- Kevlar-reinforced repair wraps (minimum 8 layers)
Always remember that reinforcement materials must extend at least 2-3 inches beyond the damaged area in both directions to distribute pressure effectively.
Safety Equipment You Shouldn’t Work Without
Hydraulic systems store tremendous energy, and fluid can be injected into skin at pressures as low as 100 PSI. Never compromise on these safety essentials:
- Eye Protection: ANSI Z87.1-rated safety glasses or goggles with side shields protect against hydraulic fluid spray, which can cause permanent eye damage.
- Chemical-Resistant Gloves: Nitrile or neoprene gloves (minimum 15 mil thickness) shield skin from both hydraulic fluid and repair chemicals.
- Face Shield: When working with systems above 2,000 PSI, a full-face shield provides additional protection against high-pressure fluid injection.
- Fire Extinguisher: A Class B fire extinguisher should always be within reach, as hydraulic fluid is flammable under certain conditions.
- First Aid Kit: Must include specialized instructions for hydraulic fluid injection injuries, which require immediate medical attention even if initially painless.
- Pressure Relief Tools: Safe methods to depressurize the system before attempting repairs, including pressure gauges with bleed valves.
Remember that even the best emergency repair is temporary. Always plan for proper replacement of damaged hoses as soon as feasible, and never exceed the manufacturer’s pressure ratings for your hydraulic system, especially after performing emergency repairs.
The Patching Method: Quick Fixes for Minor Leaks
Small leaks are one of the most common problems in the daily operation of hydraulic systems. The patching method provides a quick and effective solution that allows the equipment to continue operating until a permanent replacement is possible. This method is particularly suitable for addressing pinhole leaks, small cracks, and minor abrasions that haven’t compromised the structural integrity of the hose.
Depressurize and Secure the System
Completely relieve system pressure following manufacturer guidelines
Lock out power sources to prevent accidental pressurization
Place containment materials under the repair area to collect residual fluid
Use a pressure gauge to confirm the system is fully depressurized, a critical safety step
Record the original working pressure of the system for reference during testing
Prepare the Damaged Area
Clean a section extending at least 3 inches beyond the damage in all directions
Use brake cleaner or isopropyl alcohol to remove all hydraulic fluid, dirt, and contaminants
For stubborn oil residue, use professional degreasers such as CRC Brakleen or WD-40 Professional Degreaser
Thoroughly blow dry the area with compressed air, ensuring no solvent remains
Allow the area to dry completely—moisture is the enemy of proper adhesion
Use a UV detection light to confirm no hydraulic oil remains, as even invisible residue will affect bonding
Roughen the Surface
Use 80-120 grit sandpaper to create a slightly rough texture on the hose exterior
For hard outer layer hoses, consider using diamond grit or a small electric sander
The roughened area should be 2-3 inches larger than the actual damaged area, creating a “transition zone”
This mechanical preparation significantly improves adhesive bonding
Wipe away all sanding dust with a clean, lint-free cloth
Avoid touching the prepared surface with fingers, as skin oils reduce adhesion effectiveness
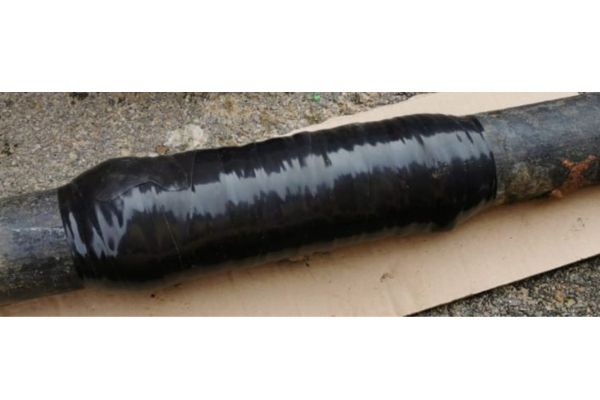
Apply the Primary Sealant
For epoxy putties: Mix according to manufacturer instructions until the color is uniform
Use plastic spatulas or wooden tools for mixing, avoiding contamination from metal tools
Mix small quantities in multiple batches rather than one large batch to prevent failure before curing
Create a “swirl” pattern in the mixture to ensure components are fully incorporated
For liquid sealants: Apply thin, even coat directly over the damaged area
Use a small brush to ensure even coverage
For vertical surfaces, use non-drip formulations or thickening agents
Apply a first thin coat, and allow partial curing (about 5-10 minutes) before applying a second coat
For repair tapes: Begin wrapping with 50% tension and 50% overlap
Start wrapping 2 inches below the damage point
Maintain constant tension, avoiding tape wrinkles or folds
Gently squeeze after completing each layer to expel possible air bubbles
Add Reinforcement Layers
Apply fiberglass mesh or repair fabric over the initial sealant layer
Pre-cut appropriately sized reinforcement materials to avoid adjustments during application
For round hoses, prepare material that can completely wrap the circumference plus 50% overlap
Saturate the reinforcement with additional adhesive or epoxy
Use a roller or brush to ensure complete saturation with no dry areas or air bubbles
For high-pressure applications, consider using multiple layers of reinforcement, fully saturated between layers
Extend reinforcement at least 2 inches beyond the damage in all directions
For systems operating above 2000 PSI, extend at least 3 inches
Ensure reinforcement material edges transition smoothly to avoid stress concentration points
Secure and Cure
Wrap the entire repair with self-amalgamating tape to compress and secure layers
Use at least three layers of self-amalgamating tape with 50% overlap
Start wrapping from one end of the repair area and move evenly to the other end
Follow the manufacturer’s curing time—typically 1-4 hours depending on the product
Environmental temperature affects curing time: below 65°F, curing time may double
High humidity environments also extend curing time, consider using heaters or dehumidifiers
Protect the repair from contamination during curing
Consider using temporary protective covers or barriers
Avoid final curing in dusty or humid environments
For rapid curing needs, a heat gun can carefully accelerate the curing process
Keep the heat gun moving to avoid localized overheating
Follow adhesive manufacturer recommendations regarding maximum temperature
Test Gradually
Begin with low pressure (10-15% of operating pressure)
Use an accurate pressure gauge to monitor test pressure
Maintain this pressure for at least 5 minutes, observing any changes
Inspect for leaks or bulging
Use a magnifying glass to carefully examine the repair area
Gently wipe with a clean white paper towel to check for fluid traces
If the initial test is successful, gradually increase to 50% of operating pressure
Increase pressure in increments of no more than 10%, holding each level for 3-5 minutes
Document observations at each pressure level
Monitor the repair closely during the first few hours of operation
Schedule regular checks: every 15 minutes for the first hour, then hourly for the next 4 hours
Consider installing temporary pressure sensors in the repair area for continuous monitoring
Establish a monitoring log to record repair performance over time
Include date, time, pressure readings, and observations
Take photographs of the repair area for comparison and documentation
Comparison of Hydraulic Repair Materials
Repair Type | Best For | Max Pressure (PSI) | Temp Range (F) | Cure Time | Features/ Advantages | Small cracks, pinhole leaks (linear) |
Epoxy Putty | Small cracks, pinhole leaks (linear) | 3,000 | -60~350 | 15 min initial set, 24h full cure | Strong adhesion, heat/chemical resistance, moldable | High strength reinforcement suitable for layered repair |
Silicone Repair Tape | Bends, irregular surfaces | 950 | -65~500 | Self-fusing in minutes 24h full | Fast bonding, UV/chemical resistant flexible wrapping | Rescue Tape, 3M 2228, Tommy Tape |
Fiberglass Kits | Multi-material strength+ flexibility multi-layer capable | 2,500 | -20~400 | 30 min~ 2h | High strength reinforcement suitable for ayered repair | Permatex FiberFix, West System |
UV-Cured Materials | Quick fixes, small surface defects | 1,500 | -40~300 | 30s~2min (with UV light) | Medium-high pressure structure cracks | 3M UV Repair Bondic, FORTIVO |
Hybrid Repair Systems | Complex pressure/temp requirements | 3,500 (combined) | -40~450 | 1h~8h (system dependent) | Devcon + FiberFix, Loctite +Carbon Fiber | Devcon + FiberFix,Loctite +Carbon Fiber |
Pressure Limitations of Patched Repairs
Understanding the limitations of patched repairs is critical for safe operation.
Pressure Derating
Always reduce the maximum working pressure of a patched hose by at least 25% for safety.
Use the following derating formula for accurate calculation:
Max Safe Pressure After Repair = Original Working Pressure × (1 – Safety Derating Factor)
Safety Derating Factors by Repair Type:
Surface Repair (outer layer only): 0.25 (25% reduction)
Moderate Repair(outer + partial reinforcement): 0.40 (40% reduction)
Deep Repair (near or includes inner layer): 0.60 (60% reduction)
Dynamic vs Static Applications
Patched hoses perform better in static applications. For systems with significant vibration or movement, reduce pressure by an additional 15%.
Vibration Frequency Impact:
Low frequency (<10Hz): additional 10% reduction
Medium frequency (10–50Hz): additional 15% reduction
High frequency (>50Hz): additional 25% reduction
Movement Type Impact:
Axial movement: additional 10% reduction
Bending motion: additional 20% reduction
Torsional movement: additional 30% reduction
Temperature Factors
High temperatures further reduce pressure capacity.
For every 50°F above the rated temperature, reduce pressure by an additional 10%.
Temperature Adjustment Formula:
Temperature Coefficient = 1 – (0.1 × (Current Temp – Rated Temp) ÷ 50)
Cold Start Consideration:
At temperatures below 32°F, limit system pressure to 30% of the normal working pressure until fluid temperature rises.
Temperature Cycling:
Frequent temperature fluctuations accelerate repair degradation. If there are more than 3 full temperature cycles per day, reduce pressure by an additional 5%.
Binding Techniques: Reinforcing Damaged Sections
When Binding Is Your Best Emergency Option
In emergency maintenance scenarios—particularly in remote locations or when replacement parts are delayed—binding becomes an essential first-response technique to prevent fluid loss and pressure drops. While not a permanent repair method, it can provide crucial temporary reinforcement and restore operational capability for limited durations.
Binding is most effective in:
- Static hydraulic lines with minimal vibration
- Low- to mid-pressure systems (typically <2,500 PSI)
- Situations requiring transport or system repositioning before permanent repair
- Non-critical auxiliary lines (e.g., return lines or drain hoses)
However, even with ideal execution, binding repairs should be closely monitored and marked for replacement at the earliest opportunity.
Binding Materials for Emergency Hydraulic Hose Repairs
Material | Key Properties | Typical Pressure Range | Best Use Case |
Stainless Steel Wire (Annealed or Braided) | -High tensile strength -Excellent heat & corrosion resistance -Withstands mechanical fatigue | Up to 3,000 PSI | High-pressure static lines Best when paired with epoxy sealing |
KevlarR/Aramid Fiber Cord | -Lightweight &flexible -Heat/chemical resistant -Works well in tight spaces | Medium pressure (up to ~2,000 PSI) | Medium-pressure repairs Limited wrapping space |
Industrial Zip Ties (Polyamide or Nylon) | -Fast to apply -Low tensile load -Degrades with heat/UV | <500 PSI(very low risk only) | Temporary containment Return or drain lines only |
Cloth Bandage+ Epoxy Resin | -Good adhesion on regular surfaces -Semi-rigid seal when cured | Up to 1,000 PSI | Field repairs without access to metal or fiber binding materials |
The Wire-Wrap Method for High-Pressure Applications
For high-pressure or structurally compromised hose sections, the wire-wrap method offers the strongest field-appropriate reinforcement. When done correctly, it mimics the hoop-strength behavior of internal braid reinforcement.
Step-by-Step Procedure:
Clean and dry the hose thoroughly—remove all hydraulic fluid residue, dirt, and oxidation.
Apply a Base Sealant Layer using high-strength epoxy putty or self-fusing rubber tape.
Anchor the First Wrap at least 1–2 inches below the damaged section.
Spiral Wrap Upward using stainless wire, maintaining uniform tension (avoid slack or kinks).
Overlap Each Layer by 50%, ensuring there are no gaps in coverage.
Wrap Beyond Damage Zone: Extend 1–2 inches above the damaged area for full containment.
Double Back Downward for added strength and compression.
Secure Wire Ends with clamps, tie-off knots, or additional epoxy sealing.
Cure (if epoxy used), and allow cooling to ambient temperature before re-pressurizing.
Splicing Methods: Reconnecting Completely Severed Hoses
When a hydraulic hose is completely severed, splicing provides a field-repair solution to reconnect both ends—restoring system integrity until full replacement is possible. While not always suitable for high-frequency or dynamic systems, proper splicing with rated components can restore pressure containment and fluid flow in static or moderate-duty lines.
Cutting and Preparation Techniques for Clean Splices
A clean and precise cut is critical for achieving a leak-free, pressure-rated connection. Poor preparation is the number one cause of splice failure.
Preparation Steps:
Depressurize the system fully before handling the hose.
Cut square using a hose saw or a fine-toothed blade—ensure edges are flat, not frayed.
Clean internal bore and external cover using solvent wipes to remove hydraulic fluid and debris.
Deburr if needed using abrasive cloth or file—especially with steel-reinforced hoses.
Mark insertion depth for each fitting to ensure full engagement.
Connector Types and Their Pressure Ratings
Choosing the correct connector is essential to match the hose size, pressure rating, and application type.
Connector Type | Typical Pressure Rating | Use Case |
Barbed Couplers | < 1,000 PSI | Low-pressure, static fluid lines |
Compression Fittings | 1,000–2,500 PSI | Medium-pressure, fixed installations |
Reusable Hydraulic Fittings | Up to 3,000 PSI | Field repair of reinforced hoses (2-wire) |
Permanent Crimp Fittings | 3,000–6,000+ PSI | OEM or shop repair requires crimp tool |
Step-by-Step Splicing Procedure
Prepare Both Hose Ends as described above.
Insert Connectors Fully to the marked depth—apply light lubricant (if specified).
Tighten Compression or Clamp Fittings per torque spec. For reusable fittings, thread ferrule first, then insert nipple.
Secure and Align hoses to prevent twisting.
Re-pressurize slowly while inspecting for leaks.
Perform Function Test under full operating pressure before returning to service.
Common Mistakes to Avoid When Splicing Hydraulic Lines
Mistake | Risk Introduced |
Uneven or angled cut | Poor seal → leakage or fitting blow-off |
Using mismatched connector sizes | Underrated pressure capacity → failure risk |
Skipping cleaning step | Fluid contamination or reduced seal integrity |
Over-tightening compression nuts | Fitting damage or thread stripping |
Applying splice to flexing zone | Premature fatigue, especially near elbows |
Failing to label or log repair | Missed inspection/replacement cycle |
Best Practices Summary
Always use pressure-rated, field-repairable connectors.
Maintain a mobile hose repair kit with common fittings.
Log all spliced sections with location, date, and pressure rating.
Replace spliced hoses at the next scheduled downtime.
Conclusion
A proactive emergency response plan can make the difference between a quick recovery and costly downtime. While temporary fixes like patching, binding, or splicing can restore function in the short term, they should never replace a proper hose replacement. Once the immediate issue is under control, it’s critical to replace the damaged hose with a new, pressure-rated hydraulic hose to ensure long-term safety and system reliability.
Contact us now to get expert recommendations or place your order today!
FAQ
Can a hydraulic hose be permanently repaired?
No. All field repairs such as patching or binding are temporary. A full hose replacement is always recommended for long-term safety and reliability.
What is the maximum pressure a patched hydraulic hose can handle?
It depends on the repair method, but generally, you should reduce the original working pressure by at least 25% after patching.
How long can I use a spliced or patched hydraulic hose?
Most temporary repairs are safe for 24–48 operating hours or up to 3 weeks in low-pressure static applications. Regular monitoring is required.
What tools do I need for emergency hose binding?
Basic tools include stainless steel wire, epoxy putty, wire tensioner, rubber padding, and cleaning materials. A repair kit is strongly recommended.
Can I use zip ties for hydraulic hose repair?
Only in very low-pressure, non-critical applications. Zip ties are not rated for pressure sealing and should be used cautiously as a last resort.
Is it safe to use repaired hoses in high-temperature environments?
Only temporarily. Temperature extremes reduce repair reliability. Always consider derating pressure and plan for prompt hose replacement.