In today’s industrial world, hydraulic systems power countless operations across construction and manufacturing sectors. The hydraulic hose assembly—often overlooked until failure—forms the critical link in these systems, transferring power through pressurized fluid. The crimping process, particularly accurate volume calculation, directly determines connection performance, safety, and longevity. Improper crimping can cause catastrophic failures leading to downtime, environmental hazards, and injuries.
Fundamentals of Hydraulic Hose Assemblies
Structure and Components of Hydraulic Hose Assemblies
Hydraulic hose assemblies consist of several layers, each serving a specific purpose in maintaining the integrity and functionality of the system. Understanding these components is crucial for proper crimping calculations.
The innermost layer, or tube, is typically made of synthetic rubber or thermoplastic material designed to contain the hydraulic fluid without degradation. Surrounding this is the reinforcement layer—often steel wire braided or spiraled—which provides the strength necessary to withstand high operating pressures. The outer cover, usually rubber, protects the reinforcement layer from environmental factors such as abrasion, UV exposure, and chemical contact.
The steel wire reinforcement layer deserves special attention as it significantly influences crimping calculations. This layer can be:
- Single wire braid (for medium pressure applications)
- Double wire braid (for high pressure applications)
- Spiral wire (for very high pressure applications)
Each configuration requires different crimping parameters to ensure optimal performance.
Common Hydraulic Hose Types and Their Characteristics
Hose Type | Pressure Rating | Reinforcement | Common Applications | Temperature Range |
SAE 100R1 | Medium (225-350 bar) | Single wire braid | General hydraulic systems | -40°F to 212°F |
SAE 100R2 | High (350-420 bar) | Double wire braid | Heavy equipment, construction | -40°F to 212°F |
SAE 100R12 | Very high (420-630 bar) | Four or six spiral wire | Mining equipment, high-pressure tools | -40°F to 250°F |
SAE 100R13 | Extremely high (630+ bar) | Six spiral wire | Specialized high-pressure applications | -40°F to 250°F |
Performance Requirements of Hydraulic Hose Assemblies
Hydraulic hose assemblies must meet stringent performance criteria to ensure safe and reliable operation. The crimping process directly affects these performance metrics:
Strength Stability: The assembly must maintain consistent strength throughout its service life, even under fluctuating pressures and temperatures. Proper crimping ensures the fitting remains securely attached to the hose under all operating conditions.
Tensile Performance: Hydraulic assemblies frequently experience pulling forces during operation. A properly crimped fitting creates sufficient grip to resist these forces without separation.
Pressure Resistance: Perhaps the most critical requirement, hydraulic assemblies must withstand operating pressures with an appropriate safety factor (typically 4:1). Improper crimping can significantly reduce this pressure rating.
Service Life and Reliability: Well-crimped assemblies can last for years in appropriate applications, while poorly crimped ones may fail prematurely, leading to costly downtime and potential safety hazards.
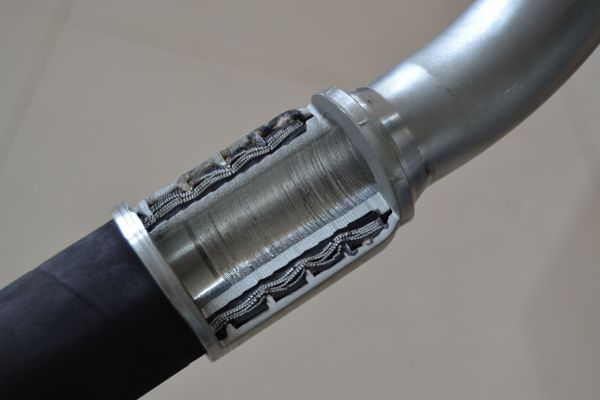
Types of Crimped Fittings and Selection Criteria
Selecting the appropriate fitting type is a prerequisite for accurate crimping calculations. Common types include:
Permanent Crimped Fittings: These one-time-use fittings provide excellent reliability but cannot be reused once crimped.
Field-Attachable Fittings: These allow for on-site assembly without specialized crimping equipment but generally offer lower pressure ratings.
Reusable Fittings: These can be disassembled and reattached, offering flexibility but typically at the cost of reduced pressure capabilities.
Selection criteria should consider:
- Operating pressure requirements
- Fluid compatibility
- Environmental conditions
- Frequency of maintenance or reconfiguration
- Available crimping equipment
- Industry standards and specifications
The material compatibility between the fitting and hose is particularly important, as dissimilar metals can lead to galvanic corrosion, compromising the connection over time.
Theoretical Foundation of Crimping Volume Calculation
Concept and Importance of Crimping Volume
Crimping volume refers to the amount of compression applied to the fitting during the crimping process. This compression creates a mechanical bond between the fitting and the hose, ensuring a leak-free connection capable of withstanding system pressures.
The physical principle behind crimping involves plastic deformation of the fitting’s outer shell, which compresses the hose material against the fitting’s stem. This compression must be sufficient to create adequate grip without damaging the hose’s reinforcement layer or reducing the internal diameter excessively.
Consequences of Improper Crimping:
Insufficient Crimping: When crimping volume is too low, the fitting may pull off under pressure or during operation, causing catastrophic failure and potential safety hazards.
Excessive Crimping: Over-crimping can damage the reinforcement layer, cut into the inner tube, or reduce the hose’s internal diameter, restricting flow and potentially causing system failures.
The optimal crimping volume creates a balance—sufficient compression to ensure grip while maintaining the structural integrity of all components.
Key Parameters Affecting Crimping Volume
Several parameters influence the calculation of appropriate crimping volume:
Hose Wall Thickness Compression Percentage: This factor depends on the physical and mechanical properties of the inner rubber layer. Different rubber compounds have varying compression characteristics.
Reinforcement Layer Outer Diameter: The diameter of the steel wire reinforcement layer is a critical measurement for calculating proper compression.
Hose Inner Diameter: This measurement affects how the hose fits over the fitting stem and influences the final crimped assembly’s flow characteristics.
Ferrule Diameter Before and After Crimping: The change in the ferrule’s diameter during crimping directly relates to the compression applied to the hose.
Fitting Stem Outer Diameter: This dimension must be considered to ensure proper fit and compression.
Steel Wire Layer Thickness: The thickness of the reinforcement layer affects its resistance to compression and the overall crimping requirements.
Compression Rate: This percentage indicates how much the hose wall should be compressed during crimping, typically ranging from 15% to 25% depending on hose construction.
Typical Compression Rate Ranges by Hose Type
Hose Type | Recommended Compression Rate | Factors Affecting Rate |
Single wire braid | 15-20% | Wire diameter, braid angle, rubber hardness |
Double wire braid | 18-23% | Wire diameter, braid layers, rubber compound |
Four-spiral wire | 20-25% | Wire size, spiral pitch, rubber elasticity |
Six-spiral wire | 22-27% | Wire thickness, layer configuration, rubber type |
Detailed Crimping Volume Calculation Methods
General Crimping Volume Calculation Formula
The calculation of crimping volume typically involves several parameters and can be approached through different formulas depending on the specific standards being followed. The general principle remains consistent: determine the appropriate compression of the hose wall to create a secure connection without damaging the hose structure.
A basic approach to crimping volume calculation follows this sequence:
- Measure all relevant dimensions of the hose and fitting components
- Determine the appropriate compression percentage based on hose type
- Calculate the target crimped diameter using the appropriate formula
- Set up the crimping machine to achieve this diameter
The general formula considers the relationship between the hose dimensions, fitting dimensions, and the desired compression rate.
3.2 Specific Crimping Formula Example and Analysis
A specific formula commonly used in the industry is:
D = (d₁ – d₂) + [D₀ – (D₂ – D₁)] – E(D₁ – d₂ – A)
Where:
- D: Final diameter after crimping
- D₀: Ferrule outer diameter
- D₁: Reinforcement layer outer diameter
- D₂: Ferrule inner diameter
- d₁: Fitting stem outer diameter
- d₂: Hose inner diameter
- A: Reinforcement layer thickness
- E: Compression rate
Measurement Methods for Parameters:
Ferrule Dimensions (D₀, D₂): These can be measured using precision calipers or micrometers. For most standard fittings, manufacturers provide these specifications.
Hose Dimensions (D₁, d₂, A): These require careful measurement of a clean-cut hose end. A digital caliper is recommended for accuracy.
Fitting Stem Diameter (d₁): This should be measured at the sealing area where the hose inner tube will contact the stem.
Calculation Example:
Consider a hydraulic hose with the following parameters:
- D₀ = 26.0 mm (Ferrule outer diameter)
- D₁ = 22.0 mm (Reinforcement layer outer diameter)
- D₂ = 24.0 mm (Ferrule inner diameter)
- d₁ = 16.0 mm (Fitting stem outer diameter)
- d₂ = 12.5 mm (Hose inner diameter)
- A = 2.0 mm (Reinforcement layer thickness)
- E = 0.20 (20% compression rate)
Substituting these values:
D = (16.0 – 12.5) + [26.0 – (24.0 – 22.0)] – 0.20(22.0 – 12.5 – 2.0)
D = 3.5 + [26.0 – 2.0] – 0.20(7.5)
D = 3.5 + 24.0 – 1.5
D = 26.0 mm
This means the final crimped diameter should be 26.0 mm to achieve optimal compression.
Common Errors and Prevention:
- Measurement errors: Always use calibrated measuring tools
- Using incorrect compression rates: Consult manufacturer specifications
- Neglecting temperature effects: Adjust calculations for extreme operating temperatures
- Ignoring hose construction variations: Different hose constructions require different approaches
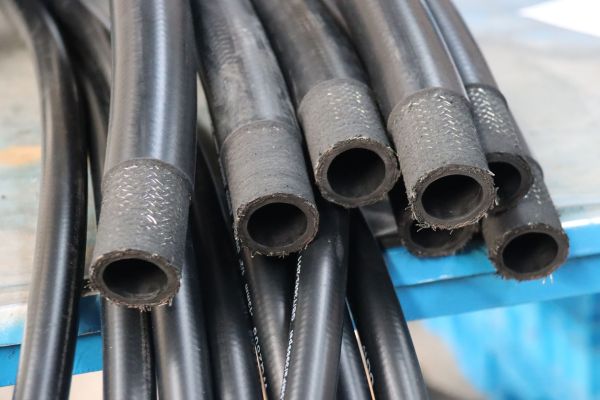
Crimping Force Calculation Formula Application
Beyond calculating the target crimped diameter, it’s often necessary to determine the required crimping force. This is particularly important when selecting appropriate crimping equipment or troubleshooting crimping issues.
The formula for total crimping force is:
F = K × (D × L × P)
Where:
- F: Total crimping force
- K: Compensation coefficient (typically 1.3-1.5)
- D: Crimped diameter
- L: Crimping length
- P: External pressure (pressure applied by the crimping machine)
The compensation coefficient K varies based on hose size:
- For smaller hoses (up to 1/2″): K = 1.3
- For medium hoses (5/8″ to 1″): K = 1.4
- For larger hoses (above 1″): K = 1.5
Typical Crimping Force Requirements by Hose Size
Hose Size | Typical Crimping Force (tons) | Recommended Crimper Capacity | K-Factor |
1/4″ | 10-15 | 20 tons | 1.3 |
3/8″ | 15-20 | 25 tons | 1.3 |
1/2″ | 20-30 | 35 tons | 1.3 |
3/4″ | 30-40 | 50 tons | 1.4 |
1″ | 40-60 | 75 tons | 1.4 |
1-1/4″ | 60-80 | 100 tons | 1.5 |
1-1/2″ | 80-100 | 120 tons | 1.5 |
2″ | 100-130 | 150 tons | 1.5 |
For reference only, actual figures should be calculated on a case-by-case basis.
Practical Application of Crimping Volume Calculation
Crimping Volume Calculation Tools and Software
While manual calculations provide a solid foundation for understanding crimping principles, modern technology offers several tools to streamline the process:
Manual Calculation Methods:
- Gather all necessary measurements using precision tools
- Apply the appropriate formula based on hose type
- Calculate the target crimped diameter
- Verify results against manufacturer recommendations
Professional Calculation Software:
Several manufacturers offer proprietary software that:
- Stores specifications for common hose and fitting combinations
- Automatically calculates optimal crimping parameters
- Provides documentation for quality control purposes
- Updates with new product specifications
Mobile Applications:
Mobile apps are increasingly popular for field calculations, offering:
- Quick reference guides for common combinations
- Simple calculators for standard formulas
- Barcode scanning of components to retrieve specifications
- Cloud synchronization with enterprise systems
For critical applications, it’s advisable to verify software calculations with manual methods to ensure accuracy.
Standard Crimping Operation Procedure
A standardized approach to crimping ensures consistent results:
Preparation:
- Verify that hose and fitting are compatible and appropriate for the application
- Inspect components for damage or contamination
- Measure and record all relevant dimensions
- Calculate the target crimped diameter
- Cut the hose squarely using appropriate tools
Parameter Measurement and Recording:
- Measure and record the hose inner and outer diameters
- Measure and record the reinforcement layer dimensions
- Verify fitting dimensions against specifications
- Document all measurements for quality control
Crimping Equipment Selection and Setup:
- Select a crimper with sufficient capacity for the application
- Ensure dies are appropriate for the specific fitting
- Verify crimper calibration
- Set the crimping diameter based on calculations
Crimping Process Control:
- Insert the fitting into the hose to the proper depth
- Position the assembly in the crimper correctly
- Perform the crimping operation
- Measure the crimped diameter to verify it meets specifications
Quality Inspection Standards:
- Measure the final crimped diameter at multiple points
- Verify that measurements fall within acceptable tolerances
- Inspect for visual defects such as uneven crimping or damage
- Perform pressure testing when required
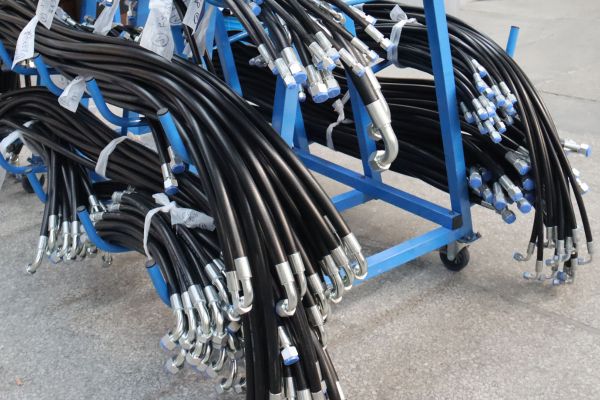
Crimping Volume Adjustments for Different Working Conditions
Different operating environments and applications may require adjustments to standard crimping calculations:
High-Pressure Applications:
- Reduce the compression rate tolerance range
- Consider using a smaller target diameter
- Increase inspection frequency and stringency
- Implement additional pressure testing
Low-Temperature Environments:
- Increase compression rate by 2-5% to account for material contraction
- Select fittings and hoses with compatible thermal expansion properties
- Consider pre-warming components before crimping
- Implement cold-temperature testing protocols
Special Media Considerations:
- Adjust compression for aggressive fluids that may affect rubber properties
- Consider special fitting materials for compatibility
- Implement additional sealing measures when necessary
- Adjust inspection criteria based on media characteristics
Vibration Environments:
- Increase compression slightly to enhance grip
- Consider using fittings with mechanical locks or serrations
- Implement vibration testing in quality control
- Reduce inspection intervals for assemblies in high-vibration applications
Crimping Quality Control and Troubleshooting
Crimping Quality Assessment Methods
Ensuring crimping quality requires systematic assessment methods:
Visual Inspection Standards:
- Even crimping around the entire circumference
- No visible damage to the ferrule or hose
- Proper insertion depth of the hose on the fitting
- No extrusion of inner tube material
Dimensional Measurement and Tolerance Control:
- Measure crimped diameter at multiple points (typically 0°, 45°, 90°, 135°)
- Maximum variation should not exceed ±0.2 mm
- Overall diameter must be within ±0.3 mm of target
- Document all measurements for traceability
Pressure Testing Methods:
- Proof testing at 1.5-2 times working pressure
- Burst testing for qualification of new assemblies
- Impulse testing for fatigue resistance
- Vacuum testing for suction lines
Life Prediction and Assessment:
- Accelerated aging tests
- Cycle testing to simulate service conditions
- Statistical analysis of field performance data
- Correlation of crimping parameters with service life
Quality Control Acceptance Criteria
Test Parameter | Acceptance Criteria | Test Method | Frequency |
Crimped diameter | Within ±0.3 mm of target | Digital caliper | 100% |
Diameter variation | Max ±0.2 mm around circumference | Multiple measurements | 100% |
Pull-off strength | >70% of hose minimum burst pressure | Tensile tester | Sampling |
Proof pressure | No leakage at 1.5× working pressure | Pressure tester | 100% or sampling |
Burst pressure | >4× working pressure | Burst tester | Qualification only |
Impulse resistance | 500,000 cycles minimum | Impulse tester | Qualification only |
Common Crimping Issues and Solutions
Even with careful calculation, crimping problems can occur. Here are common issues and their solutions:
Insufficient Crimping Identification and Handling:
- Symptom: Fitting can move or rotate within the ferrule
- Cause: Target diameter too large or crimper not achieving target
- Solution: Recalculate target diameter, verify crimper calibration, re-crimp with correct settings
Excessive Crimping Consequences and Prevention:
- Symptom: Visible damage to ferrule, reduced inner diameter
- Cause: Target diameter too small or incorrect die selection
- Solution: Verify calculations, check die selection, ensure proper measurement techniques
Uneven Crimping Cause Analysis:
- Symptom: Variation in diameter around circumference
- Cause: Misalignment in crimper, worn dies, improper positioning
- Solution: Check crimper alignment, replace worn dies, ensure proper assembly positioning
Fitting Leakage Troubleshooting Steps:
- Verify correct hose and fitting compatibility
- Check for proper insertion depth
- Inspect for damage to sealing surfaces
- Verify crimped diameter meets specifications
- Check for contamination during assembly
- Consider fluid compatibility issues
Crimping Process Optimization Recommendations
Continuous improvement of the crimping process ensures consistent quality:
Crimping Equipment Maintenance and Calibration:
- Implement regular calibration schedule
- Inspect dies for wear and damage
- Maintain hydraulic systems on crimpers
- Keep detailed maintenance records
Operator Training Key Points:
- Proper measurement techniques
- Understanding of calculation principles
- Recognition of quality issues
- Documentation requirements
- Safety procedures
Quality Control System Establishment:
- Implement statistical process control
- Maintain calibration records for all measuring equipment
- Establish clear acceptance criteria
- Implement traceability systems
- Conduct regular audits
Continuous Improvement Methods and Tools:
- Root cause analysis for failures
- Process capability studies
- Feedback loops from field performance
- Regular review of industry standards and best practices
- Benchmarking against industry leaders
Conclusion
The field continues to evolve, with developments in materials science, digital measurement technologies, and automated crimping systems promising even greater precision and reliability. Staying current with these advancements, while maintaining a solid understanding of the fundamental principles, will ensure success in hydraulic hose assembly applications.
References:
- Society of Automotive Engineers. (2020). SAE J517: Hydraulic Hose. SAE International.
- International Organization for Standardization. (2018). ISO 8434: Metallic tube connections for fluid power and general use. ISO.
- Parker Hannifin Corporation. (2019). Industrial Hose Products Division Engineering Guide. Parker Hannifin.
- Gates Corporation. (2021). Hydraulic Hose, Couplings and Equipment Catalog. Gates Corporation.
- Eaton Corporation. (2020). Aeroquip Technical Manual. Eaton Hydraulics Group.
- Manuli Hydraulics. (2018). Crimping Manual for Hydraulic Hose Assemblies. Manuli Hydraulics.
FAQ
What is hydraulic hose crimping volume, and why is it important?
Crimping volume refers to the amount of compression applied to the hose fitting during the installation of a hydraulic hose assembly. It directly affects the seal, strength, and service life of the connection.
How do you determine the correct crimping volume formula?
The correct crimping formula depends on the hose type, working pressure, and operating environment. A commonly used formula is:D = (d₁ – d₂) + [D₀ – (D₂ – D₁)] – E(D₁ – d₂ – A).
What problems can under-crimping or over-crimping cause?
Under-crimping can lead to the fitting loosening or detaching under pressure. Over-crimping may damage the wire reinforcement, cut into the inner tube, or reduce the inner diameter, restricting flow. Both can result in system failure.
How should crimping volume be adjusted for different working environments?
For high-pressure applications, tighter tolerances are required. In low-temperature environments, increase the compression rate by 2–5%. For special fluids, adjustments to the compression rate and fitting materials may be needed. In high-vibration environments, slightly increasing crimping can enhance grip.
How can you verify if the crimping quality is acceptable?
Verify crimp quality through visual inspection (uniformity, no damage), dimensional measurements (multi-point diameter checks), pressure testing (1.5–2× working pressure), and pull tests. A proper crimp should fall within specified tolerances and show no signs of leakage.
What tools are needed for accurate crimping volume calculation?
You’ll need precision measuring tools (such as digital calipers and micrometers) to gather parameters, calculation software or apps for support, and a well-calibrated crimping machine.