Hydraulic hoses are crucial components in hydraulic systems, playing a direct role in the stability and safety of the entire system. However, hydraulic hose problems often crop up during use, such as oil leaks, dislodged hose heads, leaks, and cracked hose bodies. These problems can lead to operational inefficiencies, system failures, and even safety hazards.
Oil Leakage Problems
Oil leakage in hydraulic hoses is one of the most frequent and troublesome issues faced in hydraulic systems. It typically manifests as hydraulic fluid seeping through the joints of the hose, especially at the connection points between the hose and fittings.
Cause | Symptoms / Issues | Solution |
Incorrect Crimping Pressure | – Low pressure → loose ferrule, gaps at joint, leaks appear soon after installation. – Excessive pressure → fitting deformation, hose material damaged, leaks after prolonged use. | – Set crimping machine pressure according to manufacturer’s specs. – Regularly calibrate crimping equipment. – Adjust pressure (increase if leaks appear immediately, reduce if leaks occur later due to deformation). |
Defective Hose Body (Porosity) | – Fluid seeping through hose wall. – Weak points from sand holes, material flaws, or poor curing. – Leaks even with correct crimping. | – Use hoses from certified manufacturers. – Choose high-quality materials with proper testing (porosity/pressure). – Check for quality labels and standards before purchase. |
Incorrect Crimping Pressure
The crimping process is essential for creating a secure and leak-free connection between the hose and its fitting. The crimping machine applies pressure to the ferrule (the metal sleeve) around the hose to secure it tightly to the fitting. If the crimping pressure is not set correctly, it can cause a failure in the sealing process, resulting in leaks. There are two common scenarios when incorrect crimping pressure leads to oil leakage:
Low Crimping Pressure: When the crimping pressure is too low, the ferrule will not compress the hose fitting tightly enough to create a proper seal.
Excessive Crimping Pressure: On the other hand, if the crimping pressure is set too high, it can cause the fitting to deform or the hose material to compress excessively.
Condition | Consequence | Solution |
Low Crimping Pressure | – Ferrule not tight enough → gaps at joint. – Leaks appear soon after installation when system is pressurized. | – Increase crimping pressure per manufacturer’s specification. – Re-crimp the hose and fitting. – Verify machine settings before each use. |
Excessive Crimping Pressure | – Hose compressed too much or fitting deformed. – Seal weakens over time → leaks appear after prolonged use. | – Reduce crimping pressure to avoid deformation. – Regularly calibrate crimping equipment. – Conduct routine inspections. |
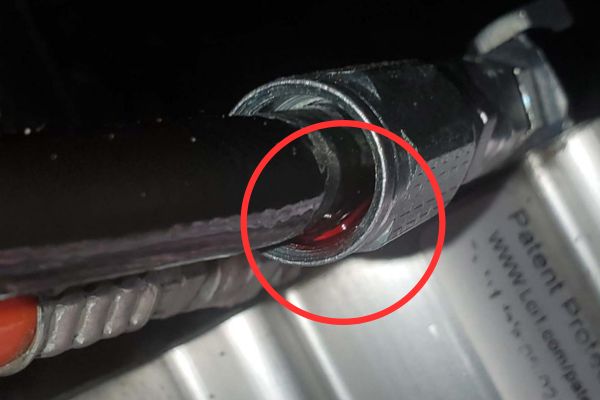
Defective Hose Body (Porosity)
Another leading cause of oil leakage is a defect in the hose body itself. A hydraulic hose can sometimes be manufactured with internal flaws such as “sand holes” or porosity, which are small imperfections in the hose material. These defects can occur during the manufacturing process, often due to poor-quality control or the use of substandard materials. Porosity in the hose material can create weak points that allow hydraulic fluid to seep through, resulting in leakage.
Sand Holes: Sand holes are tiny voids in the hose material that can develop when impurities such as sand, dirt, or other foreign particles become trapped inside the rubber or hose body during the manufacturing process. These voids compromise the integrity of the hose and create pathways for the fluid to leak out.
Internal Flaws: Internal flaws can also be caused by the improper blending of materials or insufficient curing during production. These flaws weaken the structural properties of the hose, making it more susceptible to leaks, especially under high-pressure conditions.
Solution: To prevent oil leakage due to defective hose bodies, always purchase hydraulic hoses from reputable and trusted manufacturers. High-quality manufacturers typically conduct rigorous quality control tests to ensure the hose material is free of defects and meets industry standards. This includes testing for porosity, sand holes, and other material flaws that can lead to leakage. When purchasing hydraulic hoses, check for certifications or quality assurance labels, as these can help ensure you are selecting reliable, tested products.
Cause | Description | Consequence | Solution |
Sand Holes | Tiny voids formed by trapped impurities (sand, dirt, particles) during manufacturing. | Creates weak spots in the hose → fluid leakage. | – Buy hoses from reputable manufacturers. – Ensure hoses undergo porosity and impurity testing. |
Internal Flaws | Caused by poor material blending or insufficient curing during production. | Weakens hose structure → higher risk of leaks under pressure. | – Select hoses certified to industry standards. – Verify material quality and curing process. |
Poor Material Quality | Use of substandard or low-rubber-content compounds. | Reduced durability, cracks, or leaks over time. | – Choose hoses built for specific applications (e.g., high pressure, high temp). – Avoid low-cost, uncertified hoses. |
Head Detachment Problems
Head detachment is a severe issue in hydraulic systems, where the connection between the hose and fitting fails, leading to a complete detachment of the fitting, loss of hydraulic fluid, and potential damage to the system. This issue is typically caused by improper or inadequate crimping during the installation process. Head detachment can result in significant system downtime, safety hazards, and costly repairs. Understanding the reasons behind head detachment and taking preventive measures is crucial to ensure reliable and safe hydraulic system operation.
Under-Crimping
Under-crimping occurs when the crimping process fails to apply enough pressure to secure the connection between the hose and fitting. As a result, the hose fitting does not securely grip the hose, which weakens the bond between the two components. This inadequate crimping pressure creates a weak connection, which can easily detach under the pressure and vibration of the hydraulic system.
Causes of Under-Crimping:
Incorrect crimping pressure: The crimping machine might be set to too low a pressure, failing to create a strong enough bond.
Improper crimping technique: If the crimping tool is not calibrated correctly, or if the wrong tool is used for the hose size, the crimping process may not provide adequate compression.
Solution
To avoid under-crimping, always verify that the crimping machine is set to the correct pressure according to the hose manufacturer’s specifications. Each hose and fitting combination requires a specific crimping pressure for optimal connection. It’s essential to use calibrated crimping equipment that is designed for the specific type and size of the hose.
Regular calibration of crimping machines: Periodically check and calibrate crimping machines to ensure they consistently apply the correct pressure.
Monitor pressure settings: Always check the crimping pressure before use. If under-crimping is suspected, it is crucial to increase the pressure and re-crimp the connection to ensure a secure bond.
No Crimping or Improper Crimping
Another significant cause of head detachment is the failure to crimp the hose correctly, or worse, the complete lack of crimping. In cases where no crimping is performed or the crimping tool is improperly used, the connection between the hose and the fitting remains weak and prone to detachment.
Causes of No Crimping or Improper Crimping:
Neglecting the crimping step: In some cases, workers may overlook the crimping process, assuming the connection is secure through other means (e.g., friction). This leads to a poor seal, increasing the risk of detachment.
Improper tool use: Using the wrong size or type of crimping tool can lead to improper crimping. For example, using a tool that doesn’t apply uniform pressure across the fitting may leave parts of the connection insufficiently compressed.
Incorrect crimping technique: Even when crimping is done, improper alignment or failure to apply consistent pressure can prevent a tight, reliable connection, leading to potential detachment.
Solution:
To prevent head detachment caused by no crimping or improper crimping, follow these essential steps during installation:
Ensure proper crimping: Always ensure that the hose is properly crimped using the correct crimping tool for the specific hose type and size. Using the wrong tool or incorrect technique can lead to inadequate sealing and a weak connection.
Verify crimping tool compatibility: Use crimping tools that are specifically designed for the type of hose and fitting being used. The tool should apply pressure uniformly to ensure the entire fitting is securely attached.
Check for tightness: After crimping, manually check the connection to ensure the fitting is securely attached to the hose. If the fitting feels loose or shows any signs of movement, re-crimp the hose to ensure a tight connection.
Type | Cause | Consequence | Solution |
Under-Crimping | – Crimping machine set to too low pressure. – Wrong tool size or poor calibration. – Insufficient compression on hose/fitting. | Weak grip between hose and fitting → bond fails under system pressure or vibration → hose head detaches. | – Set pressure according to manufacturer specs. – Use calibrated crimping equipment. – Regularly recalibrate crimping machines. |
No / Improper Crimping | – Crimping step neglected (connection only by friction). – Wrong tool used (no uniform pressure). – Misalignment or inconsistent compression. | Extremely weak or partial connection → fitting detaches completely under load → sudden system failure, safety hazard. | – Always perform crimping with correct tool for hose size. – Verify tool compatibility. – Manually check tightness and visually inspect crimped area. – Re-crimp if any looseness or gaps are found. |
Leakage Problems
Leakage is a frequent and significant issue in hydraulic systems, where hydraulic fluid seeps from the hose connection, most commonly around the nut or fitting. Leakage can lead to system inefficiency, environmental contamination, and safety hazards. The root causes of leakage typically include problems with seals, poor fitting accuracy, or insufficient tightening of connections. In this section, we will delve deeper into these causes and provide practical solutions to prevent and address leakage problems in hydraulic hoses.
Seal Problems
Seals are critical components in hydraulic hoses, ensuring that the connection between the hose and fitting remains leak-free. Over time, seals can become damaged, worn, or improperly installed, causing them to lose their sealing ability and allowing hydraulic fluid to escape. Various factors can contribute to seal degradation, including exposure to high pressure, temperature extremes, or chemicals, all of which can accelerate wear.
Causes of Seal Problems:
Wear and Tear: Continuous exposure to high pressure and harsh working conditions can cause seals to deteriorate over time, leading to leakage.
Improper Installation: If seals are installed incorrectly (e.g., misalignment, inadequate lubrication), they may fail to provide a proper seal, resulting in leakage.
Material Degradation: Seals made from substandard materials or unsuitable for specific operating conditions may degrade more rapidly, compromising seal integrity.
Solution:
To prevent seal-related leakage, regular inspection and maintenance of seals are essential. Follow these steps to maintain and replace seals effectively:
Regular Inspections: Periodically check the condition of seals and gaskets for signs of wear, cracking, or discoloration. If any defects are noticed, replace the seals promptly.
Seal Compatibility: Ensure that seals are made from materials compatible with the fluid type, pressure, and temperature conditions in your system. Using the wrong material can lead to premature seal failure.
Correct Installation: When installing seals, ensure that they are placed in the correct position, aligned properly, and adequately lubricated (if necessary). Misalignment or lack of lubrication can cause poor sealing performance.
Replace Damaged Seals: Always replace seals that show any signs of wear or damage. Do not attempt to reuse seals that have become compromised, as this will only lead to further leakage issues.
By maintaining and replacing seals as necessary, you ensure that the hose-fittings connection remains tight and leak-free.
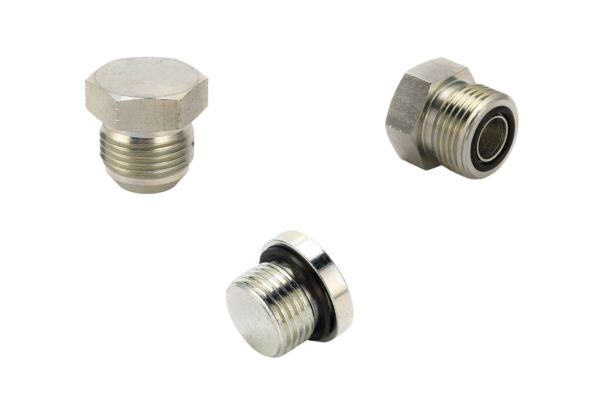
Inaccurate Fitting Surface
Fittings with poorly machined or rough sealing surfaces can lead to improper sealing, which is a common cause of leakage. Hydraulic fittings must have precision-machined surfaces to form an effective seal with the hose or gasket. If the sealing surfaces are uneven or rough, the fluid will find gaps to escape through, causing leakage.
Causes of Inaccurate Fitting Surfaces:
Manufacturing Defects: Poor machining during the manufacturing process can lead to uneven surfaces that prevent a proper seal.
Corrosion or Wear: Fittings that have been in service for a long time may experience surface degradation, such as corrosion or pitting, which reduces the sealing ability.
Improper Storage or Handling: Fittings that are damaged or scratched during handling or storage may have compromised sealing surfaces, leading to leakage when installed.
Solution:
To prevent leakage due to inaccurate fitting surfaces, it’s crucial to ensure that the fittings are of high quality and precision:
Choose Quality Fittings: When purchasing hydraulic hoses, select fittings with precision-machined surfaces. These fittings are designed to create tight, leak-free seals. Ensure that the fittings comply with industry standards and specifications.
Inspect Sealing Surfaces: Before installation, always check the fitting’s sealing surface for any visible defects such as scratches, corrosion, or wear. If any imperfections are found, the fitting should be replaced to avoid leakage.
Clean Fittings: Prior to installation, ensure that fittings are free from dirt, debris, or contaminants that could interfere with the sealing process. Clean the sealing surfaces with a lint-free cloth or solvent to ensure they are smooth and ready for installation.
By selecting high-quality, well-machined fittings and inspecting them before installation, you can significantly reduce the risk of leakage caused by inaccurate fitting surfaces.
Problem | Cause | Consequence | Solution |
Seal Problems | – Wear and tear from high pressure & harsh conditions. – Improper installation (misalignment, poor lubrication). – Substandard or incompatible seal materials. | Seal loses integrity → hydraulic fluid escapes → system inefficiency, contamination, safety risk. | – Inspect seals regularly for cracks, wear, discoloration. – Use seals compatible with fluid, pressure, and temperature. – Install correctly with alignment and lubrication. – Replace damaged or aged seals (never reuse). |
Inaccurate Fitting Surface | – Manufacturing defects (poor machining). – Corrosion, pitting, or long-term wear. – Scratches or damage from poor handling/storage. | Uneven sealing surface → fluid finds gaps → persistent leakage. | – Select fittings with precision-machined surfaces that meet standards. – Inspect sealing surfaces before installation. – Clean fittings thoroughly before use. – Replace any fittings showing corrosion, scratches, or wear. |
Cracking of the Hose Body
Cracking of the hose body refers to the appearance of small fissures or cracks on the outer surface of the hose. This issue is a serious concern as it compromises the structural integrity of the hydraulic hose, which can lead to fluid leakage, system failure, and even safety hazards. The cracks in the hose body can develop due to several factors, including poor-quality materials, environmental factors such as extreme temperatures and pressures, or physical damage. Addressing these causes and implementing appropriate solutions can prevent hose cracking and enhance the overall performance and lifespan of the hydraulic system.
Low Rubber Content in Hose Construction
One of the primary causes of hose cracking is insufficient rubber content in the construction of the hose. Rubber is a key material that provides flexibility, resistance to wear, and durability against environmental elements. When the outer layer of the hose contains too little rubber, the hose becomes more rigid and less resistant to stress, which makes it more susceptible to cracking. Low rubber content results in reduced elasticity and resistance to pressure fluctuations, temperature extremes, and mechanical wear, all of which can cause the hose to crack.
Causes of Low Rubber Content:
Poor Material Selection: Using low-quality materials during hose construction can lead to a reduction in the rubber content, making the hose more prone to damage.
Manufacturing Defects: Inconsistent manufacturing processes or improper mixing of rubber compounds can result in a substandard hose that lacks sufficient rubber content for optimal flexibility and durability.
Solution:
To prevent cracking due to low rubber content, always choose hoses made from high-quality, durable materials that offer enhanced resistance to wear and environmental factors. When selecting hoses, consider the following steps:
Select High-Quality Hoses: Ensure that the hydraulic hoses are made with premium materials, such as synthetic rubber compounds designed to withstand high pressures, temperature variations, and chemical exposure. Look for hoses that are tested and certified by recognized industry standards.
Match Hose to Application: Choose hoses that are specifically designed to handle the operating pressures, temperatures, and environmental conditions of your system. For instance, hoses exposed to extreme temperatures or harsh chemicals require materials that are resistant to these conditions.
Check for Manufacturer Certifications: Always select hoses from reputable manufacturers who offer detailed specifications and certifications. This ensures the hose will meet the required durability standards and reduce the risk of premature cracking.
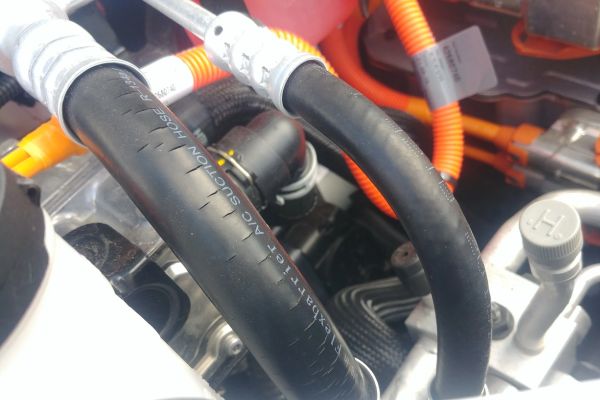
External Damage or Abrasion
Hoses that are exposed to rough surfaces or abrasive conditions are particularly vulnerable to cracking. Continuous friction or impact from external sources can wear down the hose’s outer layer, eventually causing cracks to form. This can be due to physical impacts, abrasions from moving parts, or prolonged exposure to sharp edges, metal surfaces, or hard objects in the environment. As the outer layer of the hose is damaged, its ability to withstand pressure decreases, leading to the development of cracks.
Causes of External Damage:
Abrasion: Continuous rubbing against rough surfaces can gradually wear away the hose material, leading to weakened areas where cracks can form.
Sharp Objects: Exposure to sharp or jagged surfaces, such as metal edges or other abrasive materials, can puncture the hose or cause localized damage, leading to cracks.
Environmental Factors: In some cases, hoses that are left exposed to direct sunlight, UV radiation, or harsh chemicals can experience degradation in the outer layer, leading to brittleness and cracking over time.
Solution:
To prevent cracking caused by external damage or abrasion, it is important to protect the hose and minimize its exposure to damaging conditions. Consider the following strategies:
Use Protective Covers: Install protective sleeves or covers over the hose, particularly in areas where the hose is at risk of abrasion. These covers act as a barrier to reduce wear and tear, shielding the hose from physical damage.
Install Routing Systems: Use hose routing systems, such as clamps or brackets, to keep hoses away from sharp edges, moving parts, and surfaces that could cause abrasion. Proper routing ensures that the hose is safely positioned and prevents unnecessary friction or impact.
Inspect Hoses Regularly: Conduct frequent inspections of hoses to identify any signs of wear, abrasions, or damage. Early detection allows for the timely replacement of damaged hoses before they develop cracks or lead to failure.
Replace Worn Hoses: If a hose shows visible signs of external damage or abrasion, replace it immediately to avoid further complications. Operating with a damaged hose increases the likelihood of leaks, system failures, and even environmental contamination.
Problem | Cause | Consequence | Solution |
Low Rubber Content in Hose Construction | – Poor material selection (low-quality compounds). – Manufacturing defects (improper mixing or curing). | Hose becomes rigid, less flexible → cracks easily under pressure, temperature changes, or mechanical stress. | – Select hoses made from premium synthetic rubber compounds. – Match hose to system conditions (pressure, temperature, chemical exposure). – Choose certified products from reputable manufacturers. |
External Damage or Abrasion | – Continuous friction against rough surfaces. – Contact with sharp/jagged objects. – Long-term exposure to sunlight, UV, or harsh chemicals. | Outer layer weakens → cracks form → reduced pressure resistance → leakage and safety risks. | – Use protective sleeves or covers in high-wear areas. – Install proper hose routing systems (clamps, brackets). – Inspect hoses regularly and replace when damage is visible. – Keep hoses away from direct UV and harsh environments. |
Conclusion
By choosing high-quality hoses and fittings, ensuring proper installation, and performing regular maintenance checks, these problems can be effectively prevented. Always follow manufacturer guidelines for installation, and if any issues are detected during use, address them promptly to avoid costly downtime and ensure the long-term stability of your hydraulic system.
FAQ
What causes hydraulic hose leakage?
Leakage in hydraulic hoses is typically caused by issues with seals, improper crimping, poor fitting accuracy, or insufficient tightening of connections. Regular inspection and proper installation can help prevent leakage.
How often should I replace hydraulic hose seals?
Hydraulic hose seals should be inspected regularly for signs of wear, cracking, or degradation. Replace seals when they show visible damage or after a certain number of operating hours, depending on manufacturer recommendations.
Can hydraulic hose cracking be prevented?
Yes, hydraulic hose cracking can be prevented by using high-quality hoses with sufficient rubber content, avoiding exposure to harsh environments, and using protective covers to shield hoses from abrasion and damage.
What is the ideal crimping pressure for hydraulic hoses?
The crimping pressure should always align with the manufacturer’s specifications. Too low or too high pressure can lead to improper connections, resulting in leaks or head detachment.
How can I prevent external damage to hydraulic hoses?
To prevent external damage, use protective covers for hoses exposed to abrasion, and install hose routing systems to keep hoses away from sharp edges, moving parts, and rough surfaces.
What should I do if I notice cracks in my hydraulic hose?
If you notice cracks on your hydraulic hose, replace it immediately. Cracks can lead to fluid leakage and system failure, posing both safety and operational risks