In high-pressure and high-temperature environments, the reliability of instrumentation fittings can significantly impact the performance and safety of an entire system. Dual ferrule instrumentation fittings are designed to provide superior sealing and durability, making them a crucial component in industries where precision and safety are paramount.
Understanding Ferrule Instrumentation Fittings
Instrumentation fittings are specialized components designed to provide secure, reliable connections in high-pressure and high-temperature systems. These fittings are integral in various industries where precision and safety are paramount. They are constructed with two distinct ferrules that work together to ensure a leak-proof and stable connection.

Front Ferrule
Function: The front ferrule is the primary component that directly grips the tubing. It is designed with a tapered surface that compresses around the tube when the fitting is tightened. This compression creates a tight seal that prevents any movement of the tubing within the fitting.
Design: Typically, the front ferrule features a precise taper and surface finish that ensure a uniform and effective grip. The design is critical for maintaining a consistent and reliable connection, particularly under high-pressure conditions.
Back Ferrule
Function: Positioned behind the front ferrule, the back ferrule provides additional support to the tubing. It helps distribute the clamping force applied by the front ferrule, enhancing the overall stability of the connection.
Design: The back ferrule is generally designed to fit snugly against the front ferrule and the body of the fitting. Its role is to stabilize the connection and prevent any potential deformation of the front ferrule, which could compromise the seal.
The combination of these two ferrules creates a robust, leak-proof connection. When properly installed, dual ferrule fittings can withstand extreme conditions such as high pressure, temperature fluctuations, and mechanical vibrations. The two-ferrule design ensures that the tubing is held firmly in place, reducing the risk of leaks or disconnections that could lead to system failures or safety hazards.
Materials and Construction
To ensure durability and performance, dual ferrule fittings are typically manufactured from high-quality materials. The choice of material affects not only the fitting’s strength but also its resistance to environmental factors such as corrosion and wear.
Stainless Steel:
Characteristics: Stainless steel is known for its exceptional corrosion resistance and strength. It is a popular choice for fittings used in harsh environments, including those exposed to chemicals, high temperatures, or salty conditions.
Types: Various grades of stainless steel, such as 304 and 316, are used in the manufacturing of dual ferrule fittings. Grade 316 stainless steel, for instance, offers superior corrosion resistance and is often used in marine and chemical processing applications.
Benefits: The primary benefits of stainless steel fittings include their ability to maintain their structural integrity and performance over time, even in challenging environments.
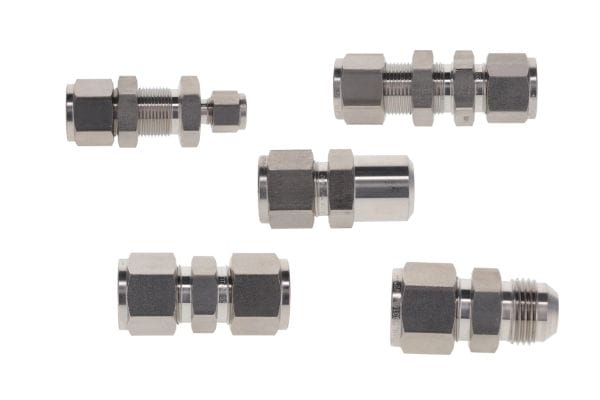
Brass:
Characteristics: Brass is chosen for its machinability and cost-effectiveness. It is often used in applications where extreme corrosion resistance is less critical, but where good performance and durability are still required.
Types: Commonly used brass alloys include dezincification-resistant brass, which offers improved resistance to corrosion in certain environments.
Benefits: Brass fittings are easy to machine and can be produced with a high degree of precision. They are suitable for less corrosive applications and offer good performance in many industrial settings.
Manufacturing Process and Quality Control
The manufacturing process for dual ferrule fittings involves precise machining and assembly to ensure that each fitting meets stringent specifications. Key steps in the process include:
Machining: The fittings are machined to exact dimensions, ensuring that the ferrules and body of the fitting align perfectly. This precision is crucial for creating a reliable seal and maintaining the fitting’s performance.
Quality Control: Rigorous quality control measures are implemented throughout the manufacturing process. This includes inspecting raw materials, testing the finished fittings for leaks and pressure resistance, and ensuring that all components meet industry standards.
Testing: Before being released for use, dual ferrule fittings undergo various tests to verify their performance. These tests may include pressure testing, leak testing, and inspections for dimensional accuracy.
Key Benefits
Leak-Proof Performance
One of the foremost advantages of double ferrule instrumentation fittings is their exceptional leak-proof performance. The design incorporates two ferrules—a front and a back ferrule—that work in tandem to create a secure metal-to-metal seal. This configuration effectively prevents leaks even in high-pressure environments.
How the Dual Ferrule Design Works: When the fitting is tightened, the front ferrule compresses around the tubing, creating a tight seal. The back ferrule supports this compression and reinforces the connection, ensuring that the seal remains intact under pressure. This robust sealing mechanism is particularly effective in preventing leaks, even in challenging conditions.
Comparison with Single Ferrule Fittings: Single ferrule fittings use a single compression ring to achieve the seal. While effective, this design may not offer the same level of security as dual ferrule fittings, particularly under extreme pressure or temperature conditions. Single ferrule fittings can sometimes be prone to leakage if not properly installed or if subjected to significant stress.
Vibration Resistance
Dual ferrule fittings are designed to excel in environments where vibration is a significant concern. Their construction allows them to absorb and manage vibrations, thereby reducing the risk of loosening or damage over time.
Importance of Vibration Resistance: In industries such as aerospace, automotive, and heavy machinery, equipment is often subject to constant and intense vibrations. In such settings, the ability of dual ferrule fittings to maintain their integrity and continue providing a secure connection is crucial. Failure to manage vibration effectively can lead to connection failure, system malfunctions, or safety hazards.
Design Features: The dual ferrule design contributes to vibration resistance by providing a more stable and resilient connection. The back ferrule’s support helps distribute the clamping force, while the front ferrule’s compression grips the tubing securely. This setup minimizes the potential for vibration-induced loosening or movement.
Durability and Longevity
The durability and long lifespan of dual ferrule fittings are key benefits, attributed to their robust design and the high-quality materials used in their construction. These fittings are engineered to withstand harsh conditions over extended periods, making them a reliable choice for various applications.
Robust Design: The combination of high-strength materials and precise engineering ensures that dual ferrule fittings can handle demanding environments without compromising their performance. Their design helps resist wear and tear, corrosion, and other forms of degradation.
Maintenance Requirements: While dual ferrule fittings are designed to be low maintenance, regular inspection is advised to ensure continued optimal performance. Routine checks for signs of wear, damage, or loosening can help address potential issues before they affect the system’s integrity. Ensuring that fittings are properly maintained helps to prolong their lifespan and maintain their reliability.
Applications
Petrochemical Industry
Applications: In the petrochemical industry, dual ferrule fittings are used in oil and gas processing, refining, and transportation. These environments often involve high pressures, corrosive substances, and extreme temperatures. Dual ferrule fittings provide the necessary durability and resistance to ensure that connections remain secure and leak-proof, even in harsh conditions.
Benefits: The fittings’ resistance to vibration and their ability to handle high-pressure fluids make them suitable for use in pipelines, reactors, and other equipment where reliability is crucial.
Pharmaceutical Industry
Applications: The pharmaceutical industry requires precise, sterile conditions for manufacturing and processing. Dual ferrule fittings are used in various applications, including drug production, chemical synthesis, and bioprocessing. These fittings help maintain the integrity of the system by ensuring a leak-proof and contamination-free environment.
Benefits: The fittings’ ability to provide a secure connection while maintaining cleanliness is essential for compliance with stringent industry standards. Their resistance to corrosion and ease of maintenance further support their use in sensitive and high-purity applications.
Other Key Industries
Aerospace: In aerospace applications, dual ferrule fittings are used in hydraulic systems and fuel lines where high pressure and vibration are prevalent. Their performance ensures safety and reliability in critical flight systems.
Automotive: Automotive applications often involve hydraulic systems and high-pressure fuel lines. Dual ferrule fittings offer durability and resistance to vibration, making them suitable for these demanding environments.
Chemical Processing: In chemical processing, where aggressive fluids and high temperatures are common, dual ferrule fittings provide the necessary resistance to corrosion and pressure, ensuring the safe and efficient operation of chemical reactors and pipelines.
Installation and Maintenance
Installation Guidelines
Proper installation is essential for ensuring the reliable performance and longevity of dual ferrule fittings. Adhering to correct procedures will help avoid potential issues and optimize the fitting’s effectiveness.
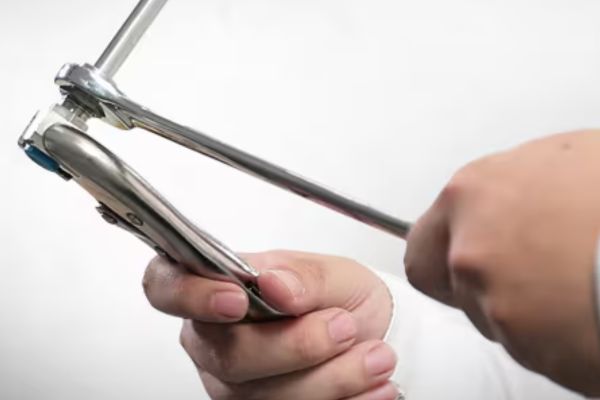
1. Preparation:
Clean Tubing: Before installation, make sure that the tubing is thoroughly cleaned to remove any dirt, debris, or burrs that could interfere with the fitting’s seal. Use a suitable cleaning method to ensure the tubing is free from contaminants that might affect the connection.
Inspect Tubing Ends: Ensure the ends of the tubing are cut squarely and are free from any deformation or damage that could compromise the fitting’s performance.
2. Insertion:
Align the Tubing: Carefully slide the tubing into the fitting. Proper alignment is crucial to ensure that the tubing is fully inserted into the fitting and that the ferrules can grip securely.
Check Depth: Confirm that the tubing is inserted to the correct depth. The tubing should reach the fitting’s backstop or be fully engaged with the fitting’s internal components.
3. Tightening:
Use Appropriate Tools: Employ the correct tools, such as a torque wrench or appropriate spanners, to tighten the ferrules. Follow the manufacturer’s torque specifications precisely to achieve the optimal seal without over-tightening.
Tighten in Stages: If applicable, tighten the ferrules gradually and evenly to avoid uneven pressure or potential damage to the tubing and fittings.
4. Common Pitfalls:
Avoid Over-Tightening: Over-tightening can lead to deformation of the ferrules or tubing, which may cause leaks or damage. Adhere to the specified torque settings and avoid excessive force.
Ensure Full Insertion: Verify that the tubing is fully inserted into the fitting. Incomplete insertion can result in inadequate sealing and potential leaks.
Maintenance Tips
To ensure the continued reliability and performance of dual ferrule fittings, regular maintenance and inspections are necessary.
1. Inspection:
Routine Checks: Periodically inspect fittings for signs of wear, corrosion, or damage. Pay attention to the condition of both the ferrules and the tubing. Look for any indications of leakage or other issues.
Visual Examination: Conduct visual inspections for any irregularities, such as deformation, cracks, or discoloration, which may indicate problems that need addressing.
2. Troubleshooting:
Address Leaks Promptly: If leaks are detected, identify the source of the problem. Leaks may be due to improper installation, damage, or wear. Take corrective action to resolve the issue, which may involve re-tightening or replacing components.
Secure Loose Connections: Loose connections can lead to performance issues or safety hazards. Tighten fittings as needed, following proper torque specifications. Ensure that all connections are secure and properly aligned.
3. Maintenance Practices:
Regular Reassessment: Implement a regular maintenance schedule to review and address the condition of fittings. This proactive approach helps prevent potential issues and maintains system reliability.
Document Findings: Keep records of inspections, maintenance activities, and any issues encountered. Documentation helps track the condition of the fittings and informs future maintenance efforts.
Comparing Dual Ferrule Fittings to Other Types
Single Ferrule Fittings
Key Differences:
Design: Single ferrule fittings incorporate only one compression ring that compresses around the tubing to create a seal. This design is simpler than dual ferrule fittings.
Sealing and Vibration Resistance: Single ferrule fittings may not provide the same level of sealing and vibration resistance as dual ferrule fittings. They can be prone to leakage under high-pressure conditions and may struggle with vibration-induced loosening.
Advantages and Disadvantages:
Advantages: Single ferrule fittings are generally easier and quicker to install due to their simpler design. They often have fewer components, which can simplify the installation process and reduce potential points of failure.
Disadvantages: These fittings may not be suitable for high-pressure or high-vibration applications. The single compression ring might not offer sufficient grip or sealing strength compared to dual ferrule fittings, potentially leading to leaks or compromised connections in demanding environments.

Flare Fittings
Comparison:
Design: Flare fittings use a conical surface to create a seal. The male and female components have matching flare surfaces that compress together to form a seal.
Sealing Performance: While flare fittings can provide a reliable seal, they may not achieve the same level of leak-proof performance as dual ferrule fittings. The conical surface can wear over time, which might impact the seal’s integrity.
Applications:
Pressure Levels: Flare fittings are often used in lower-pressure systems where high-pressure performance is not a critical factor. They are suitable for applications where connections need to be easily assembled and disassembled.
Ease of Disassembly: Flare fittings are beneficial in situations where frequent disassembly is required. Their design allows for easier maintenance and reassembly without the need for special tools or procedures.
Dual Ferrule Fittings offer superior leak-proof performance and vibration resistance, making them ideal for high-pressure and demanding applications. Their design ensures a robust connection that can withstand harsh conditions.
Conclusion
Utilizing the insights in this article, you can make informed decisions when selecting and applying double ferrule fittings in your system. Ensure that the benefits are fully utilized to improve the reliability and efficiency of your operations. For more information or to discuss your specific needs, contact our experts or visit our website. We’ll be happy to help you select the right fitting for your application and ensure optimal performance.
FAQ
What are double ferrule instrumentation fittings?
Double ferrule instrumentation fittings are specialized connectors used in high-pressure and high-temperature systems. They consist of two ferrules—a front ferrule and a back ferrule—that work together to provide a secure, leak-proof connection around the tubing.
How do dual ferrule fittings prevent leaks?
Dual ferrule fittings prevent leaks by creating a metal-to-metal seal. The front ferrule grips the tubing tightly, while the back ferrule provides additional support. This design ensures a robust seal that can withstand high-pressure conditions and prevent leaks.
What are the advantages of using dual ferrule fittings over single ferrule fittings?
Dual ferrule fittings offer superior sealing and vibration resistance compared to single ferrule fittings. They are better suited for high-pressure and high-vibration applications due to their more robust design. Single ferrule fittings, while easier to install, may not provide the same level of performance.
What industries commonly use dual ferrule fittings?
Dual ferrule fittings are widely used in industries such as petrochemical, pharmaceutical, aerospace, and automotive. They are essential in any application where high pressure, high temperature, or vibration is a factor.
How should I install dual ferrule fittings?
To install dual ferrule fittings, first clean the tubing and ensure it is free from burrs. Slide the tubing into the fitting, align it properly, and tighten the ferrules according to the manufacturer’s torque specifications. Avoid over-tightening to prevent damage.
How often should dual ferrule fittings be inspected?
Dual ferrule fittings should be inspected regularly as part of a maintenance schedule. Look for signs of wear, damage, or leaks. Regular inspection helps ensure continued performance and addresses any issues before they affect system reliability.