Taper threads are a type of screw thread where the diameter of the thread gradually decreases along the length of the fitting. Unlike parallel threads, which maintain a consistent diameter, taper threads form a wedge-shaped connection as they tighten. This design allows for the male and female parts to compress tightly against each other as they are screwed together, creating a natural seal without the need for additional gaskets or O-rings in some cases.
Overview of Thread Types
Taper Thread vs Parallel Thread
Taper Thread:
Taper threads are designed with a decreasing diameter along the length of the fitting. This taper creates a wedging action as the male and female threads are tightened, allowing the threads to jam against each other. The result is a highly effective mechanical seal created by the metal-to-metal contact. Tapered threads are especially valuable in systems with varying pressures, as their sealing properties improve with tightening, reducing the likelihood of leaks even under high pressure. Common taper thread types include NPT (National Pipe Thread) and BSPT (British Standard Pipe Taper), widely used in industries like hydraulics, gas, and oil pipelines.
Parallel Threads:
In contrast, parallel threads, such as BSPP (British Standard Pipe Parallel), have a consistent diameter throughout the fitting’s length. These threads do not form a natural seal by themselves and typically require an additional sealing component, such as a gasket, O-ring, or metal-to-metal washer, to create a leak-proof joint. Because parallel threads do not form the same wedging effect as taper thread, their reliability in sealing depends heavily on the integrity and correct use of these added sealing components. Parallel threads are often used in low-pressure applications or where frequent disassembly is required.
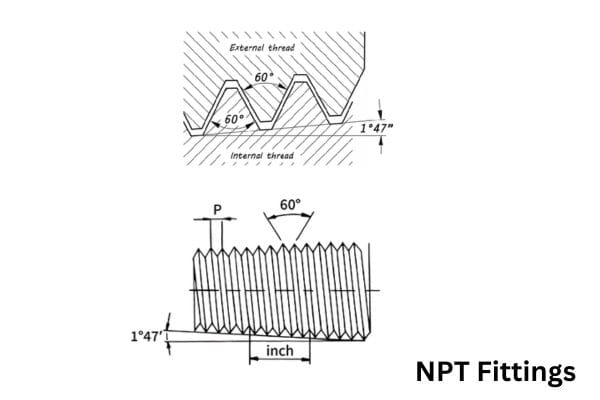
Common Taper Thread Standards
Taper threads are widely used in fluid transport, piping connections, and high-pressure sealing applications due to their self-sealing properties. Different regions and industries use various taper thread standards, with the most common being NPT (National Pipe Thread), BSPT (British Standard Pipe Taper), and ISO Taper Threads.
NPT (National Pipe Thread)
Region: North America (USA, Canada)
Thread Angle: 60°
Sealing Mechanism: Metal-to-metal interference fit, often supplemented with PTFE tape or thread sealant for enhanced leak resistance
Primary Applications:
Industrial, commercial, and residential piping
Fluid and gas transport systems
Hydraulic systems
✅ Key Features:
Self-sealing design, effective in high-pressure environments
Requires sealant to fill micro-gaps and enhance leak prevention
60° thread angle provides strong thread engagement
BSPT (British Standard Pipe Taper)
Region: Europe and parts of Asia
Thread Angle: 55°
Sealing Mechanism: Tapered thread interference for metal-to-metal sealing, often requiring additional sealant
Primary Applications:
Oil and gas pipelines
Industrial fluid systems
Hydraulic and pneumatic equipment
✅ Key Features:
55° thread angle offers good sealing and load-bearing capacity
Not compatible with NPT due to different thread angles
Commonly used in high-pressure environments requiring secure connections
ISO Taper Thread
Region: International, conforms to ISO 7-1 standard
Thread Angle: Similar to BSPT (typically 55°)
Sealing Mechanism: Metal-to-metal sealing, often used with sealants
Primary Applications:
Industrial applications requiring global compatibility
High-pressure piping systems
Mechanical and hydraulic connections
✅ Key Features:
Globally recognized, ensuring broad compatibility
Offers sealing performance similar to BSPT
Widely used in metric-based systems
How Taper Threads Work in Sealing
Mechanics of Taper Thread Sealing
Metal-to-Metal Contact:
Taper thread fittings are specifically designed to create a tight seal through a unique mechanism of metal-to-metal contact. As the male and female threads are screwed together, the decreasing diameter of the taper causes the threads to progressively jam against each other. This jamming effect compresses the metal surfaces, creating a strong seal that blocks the passage of fluids or gases. The tighter the threads are screwed, the stronger the seal becomes, which is especially important in high-pressure systems where leaks can lead to system failure or safety hazards.
Thread Interference:
Thread interference refers to the overlap or “interference” between the male and female threads when they are tightened together. In taper thread fittings, this interference ensures that there are no gaps between the threads, further enhancing the sealing capability. The more the threads are tightened, the greater the interference, which squeezes the contact surfaces together, effectively preventing any fluid from escaping through the threads. This interference is a key factor that differentiates taper thread fittings from parallel threads, which rely on additional sealing elements.
The Role of Friction in Tapered Threads
The friction generated between the thread surfaces also plays a crucial role in ensuring a leak-proof connection. As the taper thread fittings tighten, the pressure at the thread interface increases, creating friction between the mating surfaces. This friction acts as an additional barrier to fluid or gas leakage, making taper threads especially effective in high-pressure systems. The higher the pressure inside the system, the more critical this friction becomes, as it helps resist the forces trying to push the fluid through any potential gaps.
Applications of Taper Threads Fitting
Hydraulic Systems:
Taper threads are widely used in hydraulic systems, particularly those that operate under high pressure. In hydraulic systems, maintaining a leak-proof connection is essential for performance and safety, as even small leaks can lead to pressure loss and system inefficiency. Taper thread fittings are preferred because they provide a robust, self-sealing mechanism that can withstand the high pressures common in hydraulic applications. Their ability to create a metal-to-metal seal without relying on additional gaskets makes them ideal for hydraulic systems where durability and reliability are critical.
Plumbing and Piping Systems:
Taper thread fittings are also commonly used in both domestic and industrial plumbing systems. In these applications, effective sealing is crucial to prevent water or gas leaks that could lead to property damage or safety hazards. The taper design allows the fittings to form a tight, leak-proof seal in various piping systems, including those that handle water, gas, or air. These fittings are particularly useful in systems where the pressure may fluctuate, as the seal becomes stronger as the pressure increases.
Gas and Fluid Systems:
Taper threads are often the preferred choice in gas pipelines and fluid transport systems, where even small leaks can be dangerous. The ability of taper threads to create a reliable, high-pressure seal makes them ideal for these systems. They are especially useful in situations where the pressure within the system changes frequently, as the taper thread’s design allows the seal to adjust to these variations without the need for additional sealing components.
High-Temperature and High-Pressure Systems:
Industries such as oil and gas, chemical processing, and power generation often use taper thread fittings in high-temperature and high-pressure systems. In these environments, fittings must be able to withstand extreme conditions without compromising the integrity of the seal. Taper threads are particularly suited for these applications because of their strength, reliability, and ability to handle both temperature fluctuations and high pressures. Their self-sealing capability is especially valuable in environments where failure could lead to significant safety risks.
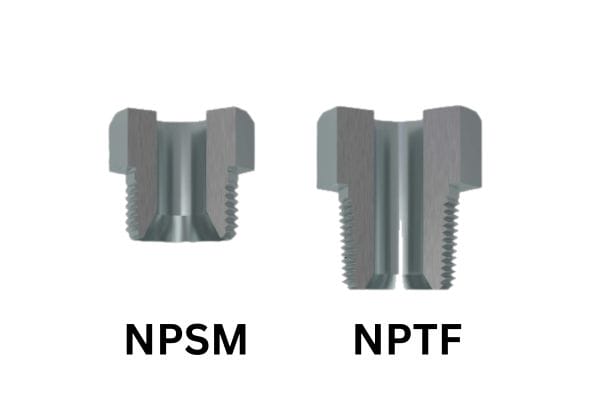
Advantages of Taper Thread Fittings for Sealing
Self-Sealing Characteristics:
One of the key advantages of taper thread fittings is their self-sealing nature. Unlike parallel threads, which rely on O-rings or gaskets to achieve a proper seal, taper threads can often form a seal without any additional sealing components. The tapered design ensures that as the threads are tightened, the metal surfaces compress together, effectively sealing the joint. This self-sealing characteristic reduces the need for extra components and simplifies the installation process, making taper threads a preferred choice in many applications.
Compatibility with Sealants:
While taper threads can often seal themselves, their performance can be further enhanced with the use of thread sealants such as PTFE tape or pipe dope. These sealants fill any microscopic gaps between the threads, providing an extra layer of protection against leaks. In applications where the pressure or temperature fluctuates, using a sealant can help maintain the integrity of the seal over time, ensuring long-term reliability. Taper threads work particularly well with these sealants because the thread interference creates tight contact surfaces that the sealant can bond to, improving the overall seal.
Handling Pressure Variations:
Taper thread fittings are particularly effective in systems where pressure varies, such as in hydraulic or gas transport applications. Because the taper threads become tighter as the pressure increases, they can adapt to changes in pressure without compromising the seal. This ability to handle pressure fluctuations makes taper threads ideal for dynamic systems that experience varying loads, ensuring that the seal remains intact even as operating conditions change.
Installation Considerations for Taper Threads
Proper Tightening Techniques
Achieving the correct level of torque when installing taper thread fittings is crucial for ensuring a leak-proof seal without causing damage to the fitting or the threads. Under-tightening can result in a loose connection that allows leaks, while over-tightening can cause thread damage or even cracking of the fitting.
Hand Tightening: The initial step should involve hand tightening the fitting until the threads are fully engaged. This ensures that the threads are properly aligned and seated before applying torque.
Use of a Torque Wrench: For critical applications, a torque wrench should be used to ensure that the fitting is tightened to the manufacturer’s recommended torque specifications. Using a torque wrench helps prevent both under-tightening and over-tightening, which could compromise the integrity of the seal.
Avoid Over-Tightening: Over-tightening taper thread fittings can lead to deformation of the threads, causing a poor seal or even damage to the fitting. The tapered design creates a natural resistance as the threads engage, so once resistance increases, it is important to stop tightening to avoid damage.
Use of Sealants
While taper threads can seal themselves, the use of thread sealants can further enhance the sealing performance, particularly in high-pressure or high-temperature applications. The most common types of sealants used with taper threads are PTFE tape (commonly known as Teflon tape) and liquid pipe thread sealants (also called pipe dope).
PTFE Tape: PTFE tape is a popular choice for sealing threaded joints because it fills small gaps between the threads and reduces the likelihood of leaks. To apply PTFE tape:
Wrap the tape clockwise (in the direction of the threads) to ensure that it stays in place as the fitting is tightened.
Apply 2-3 wraps around the male threads, ensuring the tape covers the threads evenly without blocking the opening of the pipe.
Avoid over-applying tape, as too much can prevent proper thread engagement.
Pipe Thread Sealant (Pipe Dope): Liquid sealants, such as pipe dope, provide an excellent seal by filling voids between the threads. These sealants are particularly useful in systems where vibration or temperature fluctuations are common.
Apply a small, even amount of the sealant on the male threads only, ensuring full coverage without excess material.
Follow the manufacturer’s guidelines for curing times before applying pressure to the system.
Common Installation Mistakes
Proper installation of taper threads requires attention to detail to avoid common mistakes that can lead to leaks or fitting failure.
Over-Tightening: One of the most common mistakes is over-tightening the fitting. As mentioned earlier, excessive force can damage the threads or even crack the fitting, leading to leaks. Once significant resistance is felt, stop tightening to avoid thread deformation.
Misalignment: Cross-threading occurs when the male and female threads are not properly aligned before tightening. This can result in damaged threads, making it impossible to achieve a proper seal. To avoid this, always hand-tighten the fitting first to ensure proper thread engagement before using tools to apply torque.
Improper Use of Sealants: Using too much or too little sealant can lead to problems. Over-applying PTFE tape can prevent the threads from fully engaging while under-applying tape or sealant can leave gaps that result in leaks. Additionally, some installers may apply sealant to both the male and female threads, which is unnecessary and can cause excess material buildup, leading to improper sealing.
Using the Wrong Type of Fitting: It is essential to ensure that the correct type of taper thread fitting is used for the application, as using incompatible threads (e.g., NPT with BSPT) can result in poor sealing and fitting damage. Always confirm that the thread standards of both the male and female components match.
Challenges and Limitations of Taper Threads
Thread Galling
One of the key challenges when working with taper threads is the risk of thread galling, particularly when fittings are made from metals prone to seizing under pressure, such as stainless steel or aluminum. Galling occurs when the metal surfaces of the threads scrape against each other during tightening, causing them to adhere or “weld” together. This can make the fitting difficult to tighten or loosen, leading to damage and failure of the threads. Galling is especially problematic in taper threads because of the increased contact pressure as the threads jam together to form a seal.
How to Prevent Galling:
Use Anti-Seize Lubricants: Applying an anti-seize compound or lubricant to the threads can reduce friction and minimize the chances of galling. However, lubricants should be used sparingly to avoid compromising the seal.
Avoid Over-Tightening: Over-tightening can exacerbate galling by increasing friction and pressure on the threads. It’s essential to follow the recommended torque specifications.
Choose the Right Material: When possible, using materials less prone to galling (such as brass or coated stainless steel) can help mitigate this issue.
Thread Wear Over Time
Another limitation of taper threads is the potential for thread wear with repeated use. Over time, the repeated tightening and loosening of taper-threaded fittings can wear down the threads, reducing their ability to create a tight seal. This is especially true in applications where fittings are frequently disassembled for maintenance or repair.
As the threads wear, they may no longer fully engage, resulting in reduced interference between the male and female threads. This can lead to leaks, as the metal-to-metal contact is no longer sufficient to form an effective seal. In critical systems, worn threads can also lead to fitting failure, compromising the entire system.
Mitigation Strategies for Thread Wear:
Inspect Threads Regularly: Periodic inspections of fittings in high-use systems can help identify worn threads before they cause sealing problems.
Use Thread Protectors: In applications where fittings are frequently assembled and disassembled, thread protectors can reduce wear during storage or transport.
Replace Worn Fittings: When threads become visibly worn or damaged, it’s important to replace the fitting rather than attempt to reuse it.
Not Ideal for All Applications
While taper threads are highly effective in many high-pressure and industrial applications, they are not always the best choice for every scenario. There are several limitations where taper threads may not perform optimally:
Low-Pressure Systems: In systems that operate at low pressure, the self-sealing nature of taper threads may not be fully activated. The threads rely on the pressure created by tightening to form a seal, so in low-pressure environments, additional sealing methods, such as O-rings or gaskets, may be required to prevent leaks.
Vibration and Movement: Taper threads are not well-suited to environments where constant vibration or movement occurs. While they provide a strong, static seal, the metal-to-metal contact can loosen over time when exposed to vibration, causing leaks or even failure. Applications such as engine or machinery components, where vibration is constant, may benefit more from flexible sealing methods, such as parallel threads with O-rings.
Difficult Installation in Confined Spaces: Installing taper threads requires adequate space to apply the necessary torque for tightening. In confined spaces where it’s difficult to turn the fitting or apply a torque wrench, achieving a proper seal may be challenging. In these cases, other types of fittings, such as compression or push-to-connect fittings, might be more suitable.
Conclusion
For anyone working with piping or hydraulic systems, understanding the advantages and correct installation of taper thread fittings can make a significant difference in system performance and longevity. As you assess your sealing needs, consider taper thread fittings for their proven reliability and sealing efficiency, especially in applications where safety and performance are paramount.
Relevant references :
British Standard Pipe:https://en.wikipedia.org/wiki/British_Standard_Pipe
National pipe thread: https://en.wikipedia.org/wiki/National_pipe_thread
FAQ
What are taper thread fittings?
Taper thread fittings have a tapered profile where the thread diameter gradually decreases along the length, creating a tight seal as they are tightened.
How do taper thread fittings create a seal?
The threads jam together as they are tightened, creating metal-to-metal contact that forms a reliable, leak-proof seal without the need for additional components.
What’s the difference between taper threads and parallel threads?
Taper threads have a decreasing diameter that forms a seal through thread interference, while parallel threads have a consistent diameter and usually require gaskets or O-rings to achieve a seal.
Do taper thread fittings need sealants?
While taper threads can often seal themselves, using sealants like PTFE tape or pipe dope can improve the seal, especially in high-pressure applications.
What are common applications for taper thread fittings?
Taper thread fittings are used in hydraulic systems, plumbing, gas pipelines, and other high-pressure environments where leak-proof seals are crucial.
Can taper thread fittings be reused?
Taper thread fittings can be reused, but repeated tightening and loosening may wear down the threads, reducing their sealing effectiveness over time.