Understanding the different thread types used in hydraulic systems is crucial for proper installation, leak prevention, and maintaining system integrity. Common thread types include NPSM, NPTF, and BSPT, each with distinct designs and applications. NPSM threads are straight and often used in the U.S., requiring external seals like O-rings. NPTF threads are tapered, creating a seal through thread deformation, commonly found in North American systems. BSPT threads, based on British standards, are prevalent internationally and feature a taper similar to NPTF but follow different specifications.
Overview of Thread Types
A. NPSM (National Pipe Straight Mechanical)
Definition and Characteristics:
NPSM (National Pipe Straight Mechanical) threads are straight mechanical threads that do not taper, meaning they have a consistent diameter throughout their length. They are designed specifically to work with mechanical seals, such as O-rings or gaskets, which are added externally to achieve a leak-proof connection. Unlike tapered threads, NPSM threads do not form a seal through the thread geometry alone. Instead, their uniformity allows for straightforward assembly and disassembly, making them an attractive option where frequent maintenance or replacement is necessary. These threads are typically measured in inches and follow the nominal pipe size (NPS) standards defined by the American National Standards Institute (ANSI).
Common Uses and Industries:
NPSM threads are versatile and used across several industries due to their ease of assembly and compatibility with various sealing solutions:
- Hydraulic Systems: In hydraulic systems, NPSM threads are often utilized when connections need to be dismantled and reassembled without causing damage. These threads work well with O-rings to maintain hydraulic integrity and prevent leaks under moderate pressure.
- Plumbing: In plumbing applications, NPSM threads are commonly found in water supply lines, fixtures, and other components where straightforward, low-pressure connections are needed. The simplicity of straight threads makes them ideal for environments where external seals can easily be applied.
- Compressed Air Systems: NPSM threads are also used in compressed air fittings and components, where tight seals are essential to prevent air leaks. Their compatibility with various sealing mechanisms allows them to adapt to different system requirements, ensuring reliable connections.
Advantages and Disadvantages:
Advantages | Disadvantages |
Easy to assemble and disassemble, reducing downtime during maintenance | Requires external sealing (e.g., O-rings), which can complicate installation |
Compatible with sealing components like O-rings, improving leak prevention | Not suitable for high-pressure systems unless extra sealing is applied |
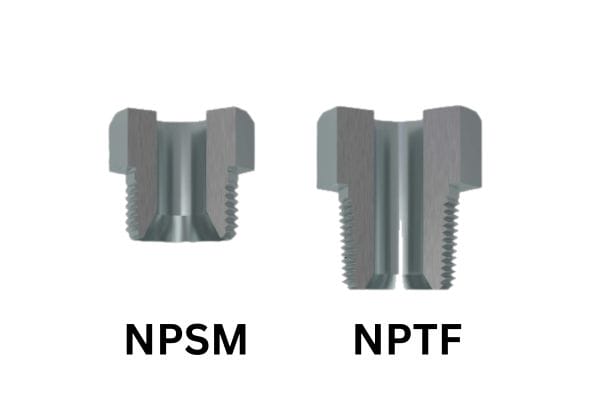
B. NPTF (National Pipe Taper Fuel)
Explanation and Design Features:
NPTF (National Pipe Taper Fuel) threads are tapered, meaning they gradually decrease in diameter along the length of the thread. This taper allows NPTF threads to form a seal through mechanical deformation when they are tightened. As the threads engage, the taper creates a tight, interference fit that eliminates the need for external sealing compounds such as tape or thread sealant. This self-sealing capability is critical in ensuring a leak-free connection, particularly in high-pressure and fuel systems. NPTF threads are standardized by ANSI and are available in both inch and metric sizes, making them versatile for various North American industrial applications.
Typical Applications:
- Automotive Systems: NPTF threads are ideal for automotive applications, particularly in fuel and brake lines, where a leak-proof connection is essential. Their ability to seal through deformation makes them suitable for critical systems where reliability is paramount.
- Hydraulic Equipment: In hydraulic systems, NPTF threads are used to connect hoses, pipes, and other components, ensuring that the system remains pressurized and free of leaks. This is vital for maintaining consistent hydraulic performance and preventing system failures.
- Industrial Applications: NPTF threads are also employed in various industrial settings, such as in piping, valves, and machinery, where secure connections are required to handle high-pressure fluids or gases without the need for additional sealing materials.
Strengths and Weaknesses:
Strengths | Weaknesses |
Forms a leak-proof seal without extra sealants, reducing installation steps and cost | Requires precise alignment during installation; misalignment can cause leaks |
Well-suited for high-pressure applications, providing secure and durable connections | Difficult to disassemble; deformation may damage threads and cause wear |
C. BSPT (British Standard Pipe Taper)
Introduction and Origin:
BSPT (British Standard Pipe Taper) threads are part of the British Standard Pipe (BSP) family, originating in the UK. These threads are tapered, similar to NPTF, but are standardized under British and ISO standards, with a distinct 55-degree thread angle as opposed to the 60-degree angle used in NPT threads. BSPT threads are specified in millimeters, making them prevalent in international markets, especially in Europe, Asia, and regions outside of North America. BSPT threads are primarily used in fluid and gas systems, where secure and reliable connections are necessary to maintain system integrity.
Common Applications:
- International Markets: BSPT threads are the standard for many international hydraulic and fluid systems, especially in Europe and Asia. Their use is essential for compatibility in global trade and cross-border projects.
- Plumbing and Gas Systems: BSPT threads are often found in plumbing, water, and gas systems, providing secure connections that prevent leaks in pipelines and distribution networks.
- Industrial Equipment: In various industries, BSPT threads are used in machinery, pumps, and valve connections, ensuring a tight seal for the transport of fluids and gases under different pressures.
Pros and Cons:
Pros | Cons |
Widely accepted and standardized across international markets (ISO/BS), ideal for global projects | Not commonly used in North America, causing compatibility issues with NPT/NPTF |
Tapered design provides effective sealing, suitable for high-pressure systems | Requires precise alignment during installation; misalignment can lead to leaks |
Key Differences Between NPSM vs NPTF vs BSPT Threads
A. Thread Design
Thread Type | Design | Sealing Method |
NPSM (National Pipe Straight Mechanical) | Straight, uniform diameter (no taper) | Requires external seals (e.g., O-rings, gaskets) |
NPTF (National Pipe Taper Fuel) | Tapered, diameter decreases along thread length | Self-seals by thread deformation (no extra sealant needed) |
BSPT (British Standard Pipe Taper) | Tapered, 55° angle (different from NPTF’s 60°) | Taper seal, often with PTFE tape or sealant |
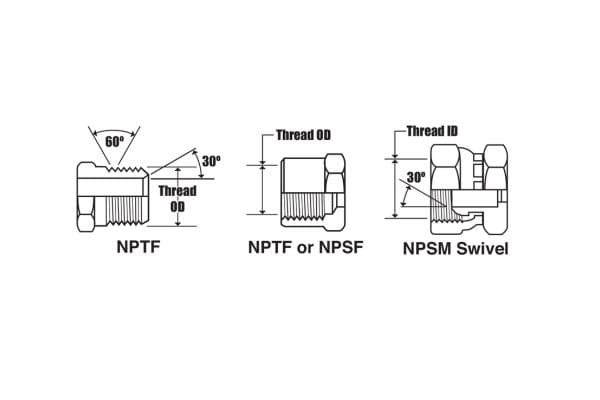
B. Standardization and Compatibility
NPSM:
Governed primarily by ANSI (American National Standards Institute) standards, NPSM threads are widely used in the U.S. They are compatible with other NPSM fittings but generally incompatible with BSPT or NPTF without special adapters.
NPTF:
NPTF threads are also standardized by ANSI and are primarily used in North America. These threads are designed to be interchangeable with NPT threads but are not compatible with BSPT or NPSM threads without proper adaptations.
BSPT:
BSPT threads are governed by British Standards (e.g., ISO standards for international usage). These threads are prevalent in Europe and other regions outside North America. BSPT fittings are generally incompatible with NPTF and NPSM systems due to differences in thread pitch, angle, and taper, requiring adapters or converters for compatibility.
C. Thread Size and Pitch Variations
NPSM:
NPSM threads typically have a consistent pitch and size across their length, as they are straight threads. This makes them relatively simple to install but requires a precise selection of seals to ensure compatibility and effectiveness.
NPTF:
NPTF threads feature a tapered design, meaning the pitch and diameter vary along the thread length. This variation allows NPTF threads to create a self-sealing connection, but it also means that they must be carefully matched to compatible fittings to avoid leaks and ensure a proper fit.
BSPT:
BSPT threads, while also tapered, have different thread angles and pitch variations compared to NPTF threads. These differences are significant enough to affect compatibility, especially when trying to fit BSPT threads with NPTF or NPSM systems. The specific dimensions and pitch variations are aligned with ISO standards for international application, ensuring compatibility in regions following these standards but posing challenges when mixing with North American thread types.
Compatibility and Interchangeability
A. Cross-Compatibility Issues
NPSM, NPTF, and BSPT threads are not inherently compatible with each other due to their distinct design specifications, including thread geometry, taper angles, and measurement systems:
Thread Type | Design | Thread Angle | Sealing Method | Compatibility |
NPSM | Straight (no taper) | 60° | Requires external seals (O-rings, gaskets) | Not compatible with NPTF (tapered) or BSPT (55°) |
NPTF | Tapered | 60° | Seal by thread deformation (self-sealing) | Incompatible with BSPT (55°) and NPSM (straight) |
BSPT | Tapered | 55° | Tapered seal, often with sealant (PTFE tape, liquid) | Incompatible with NPTF (60°) and NPSM (straight) without adapters |
Due to these differences in design, NPSM, NPTF, and BSPT threads cannot be directly mated without special adapters or conversion fittings. Attempting to connect these incompatible threads without proper adapters can result in leaks, damaged fittings, and compromised system performance.
B. Thread Adapters and Solutions
To bridge the differences between these thread types, adapters are essential when mixing standards in hydraulic systems. Here’s an overview of how to use these adapters effectively:
Using Thread Adapters:
Thread adapters are designed to convert one thread type to another, allowing for the connection of components with different thread standards. For example, an NPSM-to-NPTF adapter can be used to connect a straight-threaded component (NPSM) with a tapered thread fitting (NPTF). Similarly, BSPT-to-NPT adapters are available for international compatibility when integrating British and North American systems.
Types of Adapters:
- Straight-to-Tapered Adapters: These convert straight threads (e.g., NPSM) to tapered threads (e.g., NPTF or BSPT) while incorporating sealing mechanisms such as O-rings or gaskets to maintain leak-proof connections.
- Tapered-to-Tapered Adapters: These adapters allow for compatibility between differently angled tapered threads (e.g., NPTF to BSPT), ensuring that the mismatch in angles does not lead to a leak.
Best Practices for Safe Connections:
- Check Compatibility: Always verify the thread specifications and confirm the suitability of the adapter before installation.
- Use Appropriate Sealants: When using adapters, apply the appropriate sealant (e.g., PTFE tape or thread sealant) to ensure that the connection remains leak-free, especially when mixing different thread types.
- Tightening and Torque: Follow recommended torque settings to avoid over-tightening, which can damage threads or the adapter itself, compromising the connection’s integrity.

C. Impact on Performance and Safety
Using incompatible threads without the appropriate adapters or sealants can have severe consequences, including:
- Leaks: Mismatched threads, particularly when mixing straight and tapered types, can result in gaps that lead to fluid or gas leaks, causing loss of pressure and inefficiency in hydraulic systems.
- Component Damage: Forcing incompatible threads together can damage the threads, resulting in stripped fittings and connections that may not hold securely, even with additional sealants.
- Safety Hazards: Leaks and component failure due to incompatible threads can lead to significant safety risks, especially in high-pressure environments. Leaking hydraulic systems can cause fluid ejection, creating hazards for personnel and equipment.
- System Failure: Incorrect thread usage can lead to complete system failure if leaks go undetected or if the components separate under pressure. This can result in downtime, costly repairs, and potential damage to the entire hydraulic system.
Choosing the Right Thread Type
A. Considerations for Hydraulic Systems
When selecting the appropriate thread type for hydraulic systems, several key factors should be taken into account to ensure optimal performance and reliability:
- System Pressure Requirements: Determine the operating pressure of the hydraulic system. NPTF threads are generally preferred for high-pressure applications due to their ability to create a strong seal through thread deformation. NPSM threads may not be suitable for high-pressure situations unless additional sealing measures are in place.
- Fluid Compatibility: Assess the type of fluid being transported (e.g., oil, water, gas) and its chemical compatibility with the thread materials. Certain materials may corrode or degrade under specific fluids, affecting the integrity of the connection.
- Installation and Maintenance Needs: Consider how often the connections will need to be disassembled for maintenance. NPSM threads offer ease of assembly and disassembly, making them ideal for systems requiring regular maintenance. In contrast, NPTF threads provide a more secure seal but can be more difficult to disassemble without damaging the threads.
- Environmental Conditions: Evaluate the environmental conditions where the hydraulic system operates, including temperature variations, exposure to chemicals, and mechanical stresses. This assessment will help determine the best materials and thread types to withstand such conditions.
B. International vs. Domestic Applications
The choice between BSPT and NPSM/NPTF threads often depends on geographical location and regulatory requirements:
- BSPT Threads: Commonly used in international markets, particularly in Europe, Asia, and other regions. BSPT threads are standardized according to British and ISO specifications, making them suitable for global applications. If you are working on projects that involve international components or need to comply with global standards, BSPT is often the preferred choice.
- NPSM/NPTF Threads: Primarily used in North America, these threads are regulated by ANSI standards. When working on domestic projects or systems that strictly adhere to North American standards, NPSM and NPTF threads are more appropriate. Choosing these threads will ensure compatibility with local systems and components, reducing the risk of misalignment and leakage.
C. Practical Tips for Selection
To make an informed decision when selecting the right thread type, consider the following practical tips:
- Pressure Rating: Always refer to the pressure rating of both the thread type and the materials used in the fittings. Ensure that the chosen thread type can handle the maximum operating pressure of the system without risking leaks or failures.
- Material Compatibility: Check the compatibility of the thread materials with the fluids in the system. For instance, certain metals may corrode in the presence of specific hydraulic fluids, which could lead to premature failure of the fittings.
- Availability and Sourcing: Consider the availability of the thread types and the associated components in your region. If BSPT fittings are not readily available in your local market, opting for NPSM or NPTF might be more practical to ensure timely project completion.
Conclusion
When selecting the appropriate thread type, consider the specific needs of your hydraulic system: use NPSM for low to moderate-pressure systems where ease of maintenance is important; choose NPTF for high-pressure, North American applications requiring secure, self-sealing connections; and select BSPT for international use, especially in regions following British or ISO standards, ensuring you have adapters for integration with North American systems. Consulting hydraulic professionals for selection and installation is essential for safety and performance, ensuring the right thread type is used for secure, leak-free connections and optimal system operation.
FAQ
What are NPSM, NPTF, and BSPT threads?
NPSM (National Pipe Straight Mechanical) are straight threads, NPTF (National Pipe Taper Fuel) are tapered threads that seal without sealants, and BSPT (British Standard Pipe Taper) are tapered threads used primarily in international applications.
Can NPSM, NPTF, and BSPT threads be used interchangeably?
No, they are not interchangeable without adapters due to differences in thread design and sealing mechanisms.
What is the main sealing mechanism for NPTF threads?
NPTF threads achieve sealing through thread deformation when tightened, creating a secure connection without needing additional sealants.
When should I use BSPT threads?
BSPT threads are ideal for applications in Europe and other international markets, especially where compliance with British or ISO standards is necessary.
Are NPSM threads suitable for high-pressure applications?
NPSM threads are generally not recommended for high-pressure applications without additional sealing methods, as they rely on external seals.
How can I ensure compatibility when using different thread types?
Use appropriate thread adapters and always check specifications to ensure safe and secure connections when mixing different thread standards.