Standard fittings might work in theory — but when you’re dealing with heavy machinery, high-pressure systems, or compact equipment layouts, “close enough” just isn’t good enough. Trying to squeeze a generic part into a non-standard setup leads to leaks, early wear, and even system failure. It’s frustrating, costly, and totally avoidable. That’s why more businesses are turning to hydraulic fitting custom solutions. Whether you need a unique thread type, tighter tolerances, or special materials, custom hydraulic fittings are designed around your system — not the other way around. For industries like OEM manufacturing and construction, precision matters. And with options tailored for high-pressure applications, tight spaces, or corrosive environments, custom fittings give you the compatibility and reliability your operation demands — no compromises.
Gathering Your Application Details
Ordering a hydraulic fitting custom product without sharing the right specs is like ordering a tailored suit without giving your measurements — it just won’t fit right. To avoid costly mistakes, delays, or performance issues, this is where you want to be crystal clear. The more detailed info you give your supplier upfront, the smoother your entire custom order process will go.
This part isn’t just about telling your supplier what you want — it’s about giving them what they need to deliver a fitting that actually works with your hoses, your system, and your application environment.
Fitting Specifications Your Supplier Needs
Before machining even begins, your supplier needs a solid blueprint of what you’re after. Here’s what you should always have ready (or request help defining):
- Thread type and standard: Are you using BSP, NPT, JIC, or metric threads? Mixing standards? Let them know.
- Fitting size and dimensions: This includes internal and external diameters, length, hex size, and any custom geometry. If you can, include a fitting size chart or CAD drawing.
- Fitting style or function: Is this a straight adapter, a 90° elbow, a tee, or something more specialized?
- Material requirements: Brass, stainless steel, or carbon steel? Do you need zinc-plated fittings or something food-grade?
- Tolerance levels: Especially important in high-pressure fittings where a tight seal is a must.
- Connection type: Male-to-male, male-to-female, or quick-connect?
- Quantity and packaging preferences: How many do you need, and do you want custom logo fittings or private-label packaging?
Pro tip: Providing photos or samples of your existing part can fast-track the process — especially when working with an overseas custom fitting manufacturer.
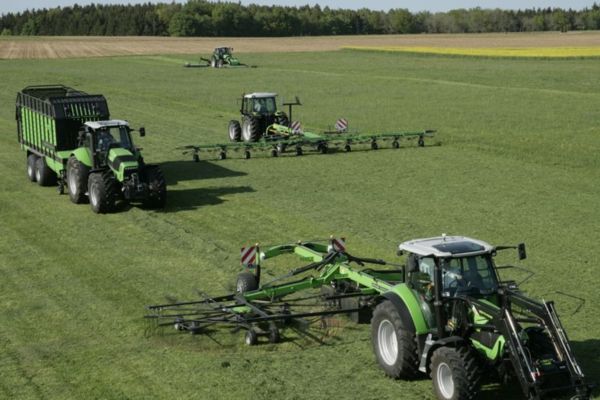
Compatibility with Hose Assemblies and Hydraulic Systems
Even a perfectly manufactured fitting is useless if it doesn’t match your hose assembly or integrate properly into your hydraulic setup. Think of your system as a chain — and the fitting is one of the links. If that link doesn’t line up, the whole chain fails.
When placing a custom hydraulic fitting order, make sure to share:
- Hose brand and type (e.g., 2-wire vs 4-wire)
- Crimp specs and fitting tail design
- System pressure and flow rate requirements
- Fluid type (e.g., mineral oil, synthetic, water-based, or aggressive fluids)
- Connection points the fitting must integrate with — including valve ports, pumps, cylinders, and manifolds
This is especially relevant if you’re trying to match fittings to legacy equipment, international machinery, or multiple brands within the same system. Compatibility goes beyond just physical dimensions — you’re looking at performance, seal integrity, and maintenance access too.
Matching Pressure Ratings and Environments
Hydraulic systems don’t all run the same. Some deal with mild, low-pressure flows. Others? They’re running full tilt under hundreds of bar or working outdoors in heat, mud, or freezing rain. Your custom fittings need to survive real-world abuse, not just look good on paper.
Let your supplier know about:
- Operating pressure and peak surge levels
- Temperature range – both ambient and fluid temperature
- Exposure to chemicals or corrosive environments
- Indoor vs outdoor use, and whether it’s mobile or stationary equipment
- Expected duty cycle – is this a high-wear component?
For example, if you’re ordering custom hydraulic fittings for offshore applications, corrosion resistance is a top priority. In contrast, if you’re fitting a compact excavator, space-saving design and vibration tolerance might matter more than material cost.
Don’t forget to bring up any industry standards your fitting must meet — like SAE, ISO, or DIN. Some customers also request hydraulic fitting testing reports as part of their quality checklist, especially for equipment going to regulated industries.
Choosing the Right Thread Type: BSP, NPT, or JIC?
When it comes to custom hydraulic fittings, one of the most overlooked — yet critical — decisions is the thread type. Get it right, and everything fits like a glove. Get it wrong, and you’re dealing with mismatched connections, leaks, and wasted time. In global B2B trade, where equipment might come from multiple countries or systems, understanding thread types isn’t just helpful — it’s absolutely necessary.
BSP vs NPT: What’s the Difference and Why It Matters
BSP (British Standard Pipe) and NPT (National Pipe Tapered) are both widely used, but they’re not interchangeable — and trying to force one into the other is a recipe for leaks.
- BSP threads are common in Europe, Asia, and Australia. They come in two styles: BSPP (parallel) and BSPT (tapered). BSPP fittings often use an O-ring or bonded washer for sealing, while BSPT seals via thread contact.
- NPT threads, on the other hand, are the North American standard. These threads are tapered and rely on metal-to-metal contact to seal, often with thread sealant like PTFE tape.
Here’s the tricky part: at first glance, BSP and NPT threads can look almost identical — but their thread pitch, angle (55° for BSP, 60° for NPT), and sealing mechanism are completely different. Mixing them up can cause major problems in high-pressure fittings or OEM hydraulic fittings, where tight seals are essential.
When placing a custom hydraulic fitting order, always clarify the thread type — especially if your equipment is sourced globally.
Where JIC Fittings Work Best
JIC (Joint Industry Council) fittings are another popular choice, especially in high-pressure hydraulic systems. They use a 37° flare seating surface, which provides a strong mechanical seal and reduces the chance of leaks, even under heavy vibration or pressure cycling.
Here’s where JIC fittings shine:
- Construction and mining equipment that’s constantly exposed to movement and shock
- Agricultural machinery that needs reliable sealing but also quick disassembly for maintenance
- Aftermarket hydraulic systems where repair and replacement flexibility matters
JIC fittings are also a go-to in custom hydraulic adapter fittings, especially when mixing thread standards or integrating into U.S.-made machinery. They’re reusable, easy to install, and support a wide range of hose and tube assemblies.
If you’re working on a custom fitting order for systems that need frequent service or endure harsh usage, it’s worth considering whether JIC threads are the best fit for your design.
Dealing with Global Connection Standards
One of the biggest challenges in international hydraulic projects is thread compatibility across regions. Machines built in the U.S. may use NPT or JIC threads. European equipment typically uses BSP or metric. Japanese systems often come with JIS (Japanese Industrial Standard) threads.
If your system includes components from multiple countries, you’ll need custom hydraulic fittings that act as adapters — converting thread types without sacrificing seal quality or flow.
To make the ordering process smoother, it helps to:
- Provide photos or samples of existing fittings
- Share the thread specs of all mating components
- Confirm sealing types: O-ring face seal, tapered thread, bonded washer, etc.
- Ask for dual-standard designs if working across mixed systems
A reliable hydraulic fitting supplier will understand these variations and can design fittings that bridge multiple standards, saving you the hassle of using extra adapters or risking system performance.
Material Selection: Brass, Steel, or Stainless Steel?
When it comes to hydraulic fitting custom orders, material selection is more than just a technical checkbox — it’s directly tied to your fitting’s performance, lifespan, and even safety. Choosing the wrong material can lead to corrosion, cracks, or failure under pressure. Choosing the right one means fewer maintenance headaches, longer service intervals, and a better fit for your specific application environment.
So, how do you decide between brass, carbon steel, and stainless steel? Each one has its own pros, cons, and ideal use cases — and understanding these can help you avoid costly missteps in your next custom fitting project.
How to Choose Between Hydraulic Fitting Materials
Not all materials behave the same way — especially when you’re dealing with hydraulic systems that handle high pressure, corrosive fluids, or extreme temperatures. Here’s a quick breakdown of your main options:
- Carbon steel fittings: Strong, cost-effective, and widely used in high-pressure systems. Perfect for general industrial applications where corrosion isn’t a big concern.
- Stainless steel fittings: Durable and corrosion-resistant, ideal for marine, chemical, and food-grade environments. They’re more expensive but offer long-term value where exposure is a concern.
- Brass hydraulic fittings: Softer and easier to machine, often used in lower-pressure systems and applications that demand excellent corrosion resistance, such as water, air, or gas lines.
When placing a custom hydraulic fitting order, consider these key questions:
- What fluid is running through the system? (oil, water, chemicals)
- What’s the operating pressure and temperature?
- Is the equipment used indoors, outdoors, or exposed to saltwater?
- Will the fittings come into contact with harsh chemicals or moisture?
If your system is indoors, low-pressure, and fluid-friendly — brass might be a great fit. If you’re powering construction equipment, carbon steel is likely your go-to. And if you’re dealing with offshore oil rigs or food production? Stainless steel is probably non-negotiable.
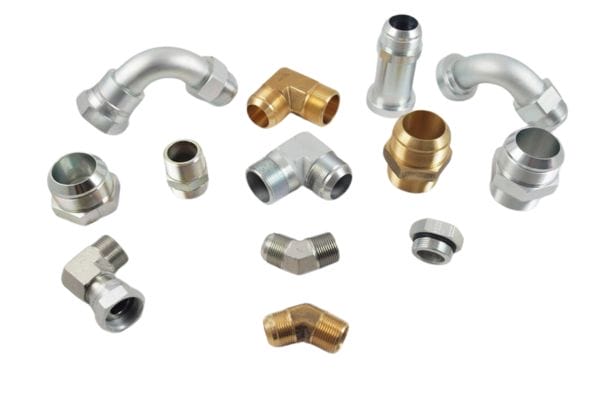
Corrosion Resistance, Plating Options, and Surface Treatment
For many B2B buyers, corrosion resistance is a key deciding factor — especially in bulk hydraulic fittings where even small failures can lead to costly replacements.
Here’s where surface treatments come into play:
- Zinc plating is commonly used on carbon steel fittings. It adds a layer of corrosion resistance and is usually cost-effective for indoor or moderate outdoor use.
- Nickel plating offers better corrosion resistance and a smoother surface finish but comes at a higher cost.
- Passivation is often applied to stainless steel to remove impurities and further protect against corrosion.
- Electroplating and anodizing can also be considered for specialized fittings, especially if aesthetics or branding are involved.
If you need fittings for coastal, humid, or corrosive environments, it’s worth investing in better plating or switching to stainless altogether. You can also ask your hydraulic fitting supplier for test data or salt spray test results if you’re unsure.
Many customers also consider surface treatments not just for protection but for appearance — especially when ordering custom logo fittings or branded parts for resale.
Zinc-Plated vs Stainless: What Lasts Longer?
This is one of the most common comparisons — and the answer depends on your application. Here’s how they stack up:
- Zinc-plated fittings are more affordable and work well in controlled environments. They resist corrosion short-term but can degrade over time when exposed to moisture or chemicals. Expect moderate lifespan and lower upfront cost.
- Stainless steel fittings offer long-term durability with virtually no rusting, even under extreme conditions. They’re ideal for long-term installations, outdoor environments, or systems that are hard to access for maintenance.
If you’re building OEM hydraulic systems for construction equipment, you might lean toward zinc-plated carbon steel fittings to keep costs manageable without sacrificing strength. But if you’re supplying hydraulic solutions for marine, food-grade, or chemical processing applications, then stainless steel custom hydraulic fittings are often the only safe choice.
Sizing It Right: How to Use a Hydraulic Fitting Size Chart
In the world of hydraulic systems, size really does matter — and guessing just isn’t an option. One of the most common issues in custom hydraulic fittings is mismatched dimensions. Whether it’s an incorrect thread pitch or a slightly off outer diameter, the result is usually the same: leaks, pressure drops, or complete connection failure. That’s why knowing how to use a hydraulic fitting size chart is critical when placing a custom order.
This isn’t just about “getting the number right.” It’s about ensuring complete compatibility with your hose assembly, thread standard, and connection style. So if you’re sourcing custom hydraulic fittings for OEM machinery, high-pressure systems, or international equipment, make sure sizing is at the top of your checklist.
Understanding Diameter, Thread Pitch, and Tolerance
Let’s break down the three main factors you need to understand when using a size chart:
- Thread Diameter (Nominal Size): This is the basic outside or inside measurement of the thread — and it determines if the fitting will physically match the port or hose.
- Thread Pitch: Measured in threads per inch (TPI) for imperial sizes or millimeters between threads in metric systems. This is a critical detail — BSP and NPT threads of the same diameter have different thread pitches and angles.
- Tolerance: Tolerance is the acceptable variation range in dimensions. In high-pressure hydraulic fittings, tolerances need to be tight. Too loose, and you’ll get leaks. Too tight, and you may damage the threads during installation.
When reading a fitting size chart, you’ll often see combinations like “1/2-14 NPT” or “M18x1.5”. Here’s what that means:
- “1/2” is the nominal size
- “14” is the number of threads per inch (TPI)
- “M18x1.5” indicates a metric thread with an 18mm outside diameter and 1.5mm pitch
Using the wrong combination may seem like a small detail, but it can cause massive problems in your hose assembly or lead to system-wide failures in industrial environments.
Why “Close Enough” Doesn’t Work in Hydraulics
In carpentry, being off by 1mm might not matter much. In hydraulics? That same millimeter could mean a loss of thousands of PSI, fluid leakage, or early wear on critical components. Especially in custom hydraulic fittings, close enough is never good enough.
Here’s why precision matters:
- Improper thread engagement causes wear, vibration, and loss of seal integrity
- Inconsistent internal diameter disrupts fluid flow and increases pressure drop
- Loose tolerances in OEM hydraulic fitting production can lead to cracking or thread stripping under high torque
- Incompatibility with certain sealing methods like O-rings or bonded washers can result in persistent leaks
If you’re ordering in bulk hydraulic fittings, a consistent size spec ensures interchangeability and prevents delays on the assembly line. Even slight dimensional errors can multiply into major inefficiencies at scale.
That’s why it’s best to double-check:
- Hose and port dimensions
- Male/female thread compatibility
- Use of correct thread seal or sealing face
- Torque requirements for your chosen material and size
If you’re unsure, your hydraulic fitting supplier should be able to assist you with size verification. Some also provide measuring tools, guides, or digital charts that make it easier to match parts accurately.
Don’t Skip This: Testing, Inspection, and Quality Control
You can have the perfect material, flawless thread type, and tight design — but if your custom hydraulic fittings fail under pressure, none of that matters. That’s where testing, inspection, and quality control (QC) come in. This stage is the invisible backbone of your order, and skipping it (or working with a supplier who cuts corners) can cost you big — in both money and reputation.
Whether you’re sourcing parts for OEM machinery, high-pressure construction systems, or global distribution, QC ensures what arrives in your box is exactly what you ordered — and that it actually works.
How Fittings Are Tested for Leaks, Strength, and Accuracy
Reputable manufacturers will run multiple types of tests to validate that your fittings meet both design and performance standards:
- Leak testing: Typically done via hydrostatic or pneumatic pressure tests, checking if fittings can hold specified pressure without dripping, seeping, or bursting.
- Thread inspection: Using gauges to verify thread depth, pitch, and engagement — especially for BSP, NPT, and JIC threads.
- Dimension verification: With calipers or CMM (Coordinate Measuring Machines) to ensure every fitting matches the CAD spec.
- Pressure and burst testing: High-pressure systems may require destructive testing to confirm strength limits, especially for high-pressure fittings used in construction, mining, or industrial machinery.
- Surface finish inspection: To detect plating inconsistencies, rust, or cosmetic flaws — especially important for zinc-plated or stainless steel fittings.
Some customers also request third-party inspection reports, especially when ordering for large-scale industrial or international use. If you’re reselling, these test results can even become part of your documentation for end users.
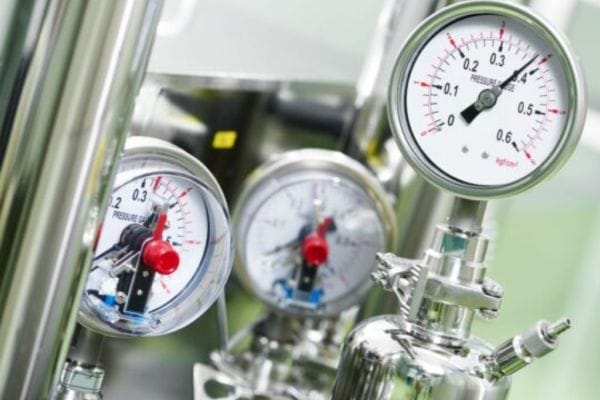
The Role of Fitting Tolerance in Performance
One of the most underrated factors in fitting design is tolerance — the acceptable variation between the drawing and the finished part. In high-pressure hydraulic systems, even tiny deviations can cause major issues.
Tight tolerances matter because they:
- Ensure proper thread engagement and sealing
- Prevent over-tightening or cracking
- Improve vibration resistance and fatigue life
- Support consistent assembly across bulk orders
When placing a hydraulic fitting custom order, talk to your supplier about critical tolerance areas, especially in threaded and sealing sections. Overly loose tolerances may reduce cost, but they can also create future failures in the field — and that’s never worth it.
Why QC Is Your Secret Weapon
Here’s the thing: Quality Control isn’t just a final step — it’s your silent sales tool. Every properly machined, pressure-tested, leak-free fitting reinforces your brand’s reputation. For buyers and engineers, it builds trust. For resellers and distributors, it reduces returns and warranty claims.
If you’re offering custom logo fittings, nothing damages your image faster than a product that doesn’t perform. That’s why strong QC is worth asking about during the quote process. Some suppliers include a quality checklist or inspection photos in the packaging — a nice touch that reassures your customer and shows you care.
Think of QC not as a cost, but as an insurance policy that protects your time, your order, and your brand.
Packaging, Branding, and Shipping: Finishing Touches
You’ve spent time perfecting your custom hydraulic fittings — now let’s make sure they arrive safe, look professional, and leave a strong impression. Whether you’re ordering for your own workshop, for resale, or as an OEM, packaging and delivery aren’t just logistics — they’re part of the customer experience.
Done right, these final touches can elevate your brand and keep your fittings damage-free from the factory to your warehouse.
Custom Logo Fittings and Branded Packaging
Want to stand out from your competition? Add your identity directly to your fittings.
- Custom logo fittings: Your name, logo, or part number can be laser-etched or stamped onto the fitting body. This helps with inventory management, branding, and credibility — especially if you resell under your own brand.
- Branded packaging: Go beyond a plain plastic bag. Include labeled zip bags, color-coded boxes, cartons with barcodes, and instruction inserts. Not only does it look better, but it also reduces mix-ups and enhances professionalism.
Your custom fitting manufacturer should be able to handle these requests with low or reasonable MOQs. It’s a small investment that goes a long way — especially when you’re building a trusted name in the hydraulic supply chain.
Shipping Process, Options, and Timelines
After inspection and packaging, your order is ready to move. Shipping custom hydraulic fittings involves both planning and protection.
Common options include:
- Air freight: Faster but more expensive — ideal for urgent orders or small quantities
- Sea freight: Cost-effective for large bulk orders but requires more lead time
- Courier services (DHL, FedEx, UPS): Good for samples, low MOQs, or custom prototypes
Ask your supplier for:
- Lead time estimates including packaging and customs
- Tracking numbers and delivery updates
- Documentation support, especially for international trade (packing list, invoice, certificate of origin, etc.)
Depending on the country, you may also need to clarify HS codes or special certifications — your supplier should help guide you through that.
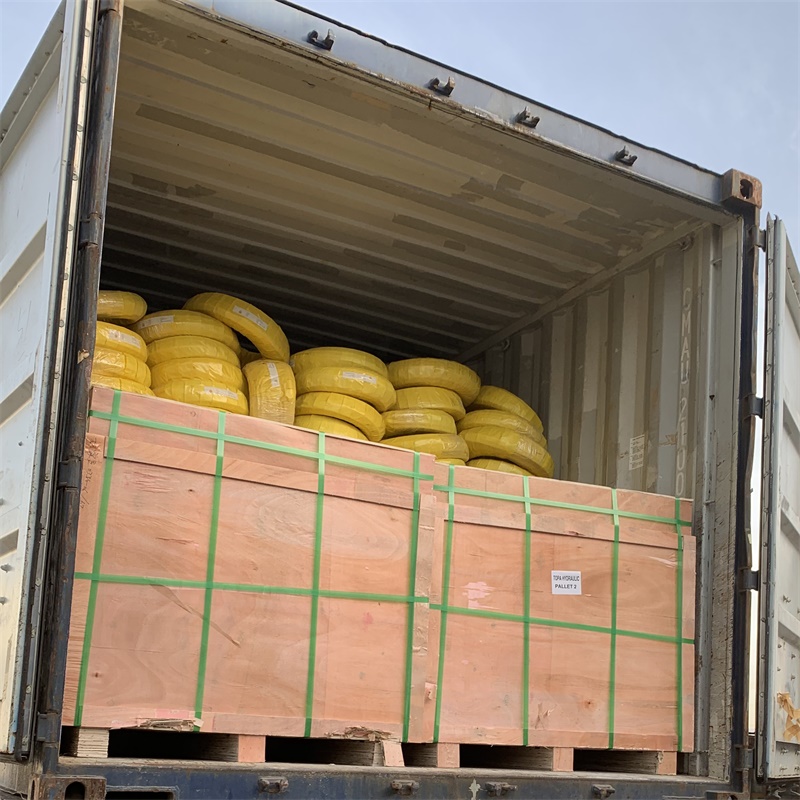
Keeping Fittings Safe in Transit
Hydraulic fittings are tough — but threads, sealing surfaces, and plating can still get damaged during transport if not packed properly.
Look for:
- Thread protectors to prevent nicks and scratches
- Individual bagging to avoid metal-to-metal contact
- Anti-corrosion bags or oil coating for moisture-sensitive environments
- Shock-proof outer boxes and pallets for large shipments
A damaged fitting is more than just an inconvenience — it can delay installations, affect your client’s trust, and cause costly rework. Taking extra care in the packaging phase pays off with fewer complaints and smoother handoffs.
Final Thoughts
Need help with your next custom fitting order? Our team is here to help — from design to delivery. Whether you’re working on a one-off prototype or a bulk OEM order, we’ll guide you every step of the way. Contact us for free drawings, samples, and quotes today.
FAQ
What’s the minimum order quantity for custom hydraulic fittings?
MOQ typically starts at 100–500 pieces, depending on the fitting type, material, and complexity. Small sample orders are usually available.
How long does it take to produce a custom hydraulic fitting order?
Most orders are completed within 6–8 weeks after sample approval. Complex designs or large volumes may take slightly longer.
Can I get a sample before placing a bulk order?
Yes. We highly recommend samples for testing and verification. Most suppliers offer 1–5 pieces for approval before mass production.
Can you match fittings to my existing hose brand?
Absolutely. Just provide your hose specifications or a sample, and we’ll ensure full compatibility with your hose assembly.
What materials can I choose for custom fittings?
Options include carbon steel, stainless steel (304/316), and brass. Surface treatments like zinc plating or nickel plating are also available.
Do you offer logo customization and branded packaging?
Yes. We can laser-etch your logo on fittings and provide custom labels, bags, or boxes for branding and resale.