Misaligned hoses can lead to increased pressure drop, premature wear, and potential system failure, costing both time and money. or maintenance engineers and technicians, even a slight error in hydraulic hose orientation can result in costly system failures, leakage, or even dangerous pressure surges. Take, for example, a construction excavator—if a hose twists under pressure, it can burst, halting operations instantly.
What is Hydraulic Hose Orientation?
Definition and Basics
Hydraulic hose orientation refers to the specific angular alignment of hydraulic hoses and their fittings within a hydraulic system. Improper orientation—such as a 15° misalignment—can lead to internal twisting, which drastically reduces hose life by over 50% (per SAE J517 standards).In any hydraulic system, hoses are subjected to high-pressure fluid movement, making the orientation of these hoses critical to maintaining system integrity. Proper hose orientation ensures that connections between components, such as cylinders, pumps, and valves, are optimized to handle the operational demands without excessive stress or misalignment.
In high-pressure environments, the angular alignment of hoses becomes especially important. Any misalignment can lead to excessive stress at connection points, causing leaks, hose degradation, or even system failure. This is particularly relevant for systems that operate under constant or pulsating high pressure, where small misalignments can result in significant operational issues. The goal of proper hose orientation is to minimize bending, twisting, and excessive movement of the hose, ensuring longer life and reliable performance.
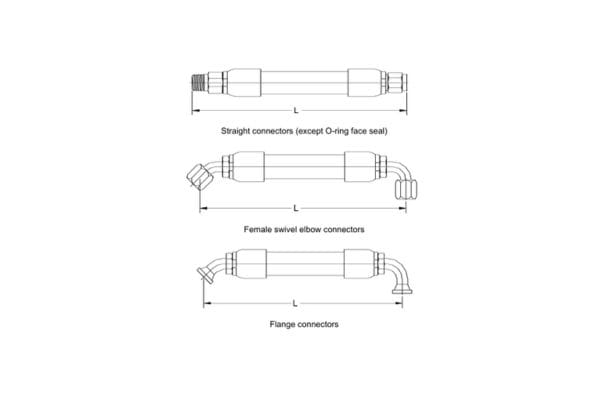
Key Concepts
Angular Offset:
Angular offset refers to the angular difference between the two fittings on either end of a hose. It’s measured in degrees, typically in a clockwise direction from one fitting to the other. For example, if the hose has two 90-degree elbow fittings, the angular offset between them might determine whether the hose will be under stress when installed, depending on how the ends are oriented. The key here is to ensure the offset matches the system’s design needs, allowing for smooth fluid flow without undue stress on the connections.
Elbow Fittings:
Elbow fittings, such as 45° or 90° angles, are commonly used in hydraulic systems to route hoses in confined spaces or around obstructions. These fittings are essential for directing the hose without forcing it into unnatural bends, which could compromise the integrity of the hose. The orientation of these elbows is crucial. Misaligning an elbow can introduce unwanted tension, twisting, or bending into the hose, which will shorten its lifespan and may lead to premature failure.
Why Incorrect Orientation Leads to Performance Degradation:
When hoses are not oriented correctly, it creates several issues. First, incorrect orientation can cause hoses to rub against machinery or other hoses, leading to abrasion and potential failure. Second, when hoses are installed with improper angular offset or alignment, they can experience excessive strain during system operation, particularly when subjected to high pressures. This strain results in hose kinks, leaks at connection points, or even catastrophic failure if the pressure becomes too great. Additionally, incorrect orientation may reduce the efficiency of fluid flow, increasing pressure losses and reducing the system’s overall performance.
Correct hydraulic hose orientation not only preserves system performance but also prevents costly downtime and repairs by reducing wear and tear on the hoses and associated components. By paying careful attention to hose routing, angular offset, and elbow fitting placement, you can extend the lifespan of your hydraulic system and ensure safe, reliable operation.
Measuring Hose Orientation
Step-by-Step Guide
To properly measure hydraulic hose orientation, the goal is to ensure that the fittings on both ends of the hose are aligned in a way that matches the system’s design requirements, preventing stress, twisting, or bending during operation. The angular offset between fittings is typically measured in degrees, and this can be done using common tools like protractors or visual guides. Here’s a step-by-step breakdown:
Step 1: Gather the Necessary Tools
Protractor or specialized angular measuring tools.
Visual guides such as hose layout diagrams.
Markers to help visually track the orientation.
Step 2: Position the Hose Properly
Lay the hose flat on a surface to minimize any existing twists or bends.
Identify the two end fittings, which we’ll call Fitting A (the farthest fitting) and Fitting B (the nearest fitting).
Step 3: Set Fitting A to 0 Degrees
Fitting A is always the reference point and is set at 0 degrees. This means that you will use it as the baseline for measuring the angular offset.
Step 4: Measure the Angular Offset of Fitting B
While keeping Fitting A fixed, view the hose along its length.
Measure the angle between Fitting A and Fitting B in a clockwise direction using the protractor or angular measuring tool. This is the angular offset of the hose.
If no specific angle is provided, elbows are typically positioned at 0 degrees, but this can vary depending on the installation.
Step 5: Record the Orientation
Once measured, mark the hose or fittings as necessary for easy identification during installation or future maintenance.
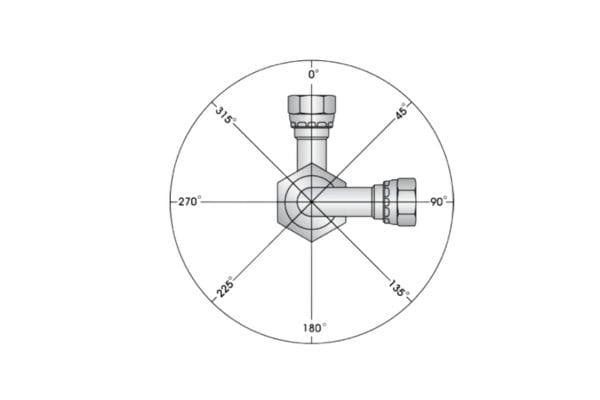
Common Pitfalls
Pitfall | Description | Recommended Solution |
Wrong Assumptions About Fitting Angles | Assuming elbow fittings are always at 0° by default | Always check design documents or specifications for correct angular offsets |
Using Improper Tools | Measuring with basic rulers or by eye leads to inaccuracies | Use a protractor or specialized hydraulic fitting measurement tools for precision |
Forgetting System Movement | Ignoring the impact of vibration or movement on hose orientation | Consider flexible routing or swivel joints to accommodate future motion |
Not Rechecking After Installation | Failing to verify angle alignment after final assembly | Always recheck hose orientation post-installation to ensure nothing has shifted |
Effects of Incorrect Hose Orientation
Performance Impact
Incorrect hydraulic hose orientation can lead to a range of performance issues, most notably system inefficiencies, pressure drops, and even complete system failure. When hoses are improperly aligned, the fluid flow inside the system encounters greater resistance, which can cause pressure to drop. This reduces the efficiency of the system as it requires more energy to maintain proper function. Additionally, improper orientation can restrict fluid flow, leading to bottlenecks or turbulence, which can further reduce the performance of the system.
In extreme cases, incorrect hose alignment can lead to catastrophic system failure. For instance, excessive pressure in misaligned hoses may exceed the pressure rating of the hose, causing it to burst or rupture. This is especially true in high-pressure environments where any misalignment amplifies stress on the system, potentially resulting in sudden failure. The system’s performance is further degraded by leaks, reduced flow rates, and increased downtime for repairs.
Wear and Tear
Misaligned hoses are also prone to premature wear and damage. When a hose is improperly oriented, it can rub against nearby equipment, structures, or other hoses. This abrasion can lead to the weakening of the hose material over time, creating weak points that may eventually result in leaks or ruptures.
Moreover, twisting or bending beyond the hose’s design limits puts additional stress on the internal structure. Hydraulic hoses are designed to handle certain types of movement, but twisting forces them to bear stress in unintended directions, which accelerates the wear process. Over time, this leads to cracks, splits, or burst points within the hose, ultimately compromising the entire system.
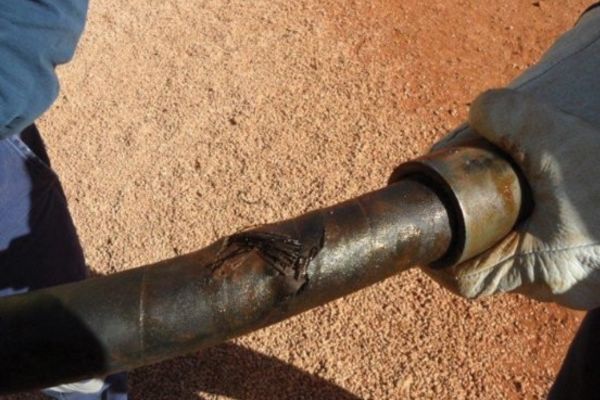
Correlation between Orientation and Stress Points
Correct orientation of hydraulic hoses is crucial for minimizing stress points in the system. When hoses are misaligned, stress concentrates at specific points, particularly at fittings, bends, and connections. These stress points are more susceptible to failures, as they bear the brunt of the mechanical and hydraulic forces acting on the hose.
For example, if a hose is not aligned properly with its fittings, it may develop excessive strain at the point where it connects to the rest of the system. This strain can eventually cause the fitting to fail, leading to leaks or hose separation. By ensuring proper hose orientation, the system distributes stress more evenly across the hose, reducing the likelihood of such concentrated damage.
Best Practices for Ensuring Proper Hose Orientation
Installation Tips
Plan the Hose Routing:
Before starting the installation, review the system layout and plan the hose routing carefully. Avoid routing hoses through tight spaces or around sharp corners where they may bend excessively. Use hose clamps or guides to prevent sagging and twisting.
Align Fittings During Installation:
To ensure the correct orientation, always align fittings at both ends of the hose before tightening. If one fitting is an elbow, use a protractor or marking tools to measure the angular offset and adjust as necessary. This ensures that the fitting is positioned correctly to avoid twisting or stress during operation.
Use the Correct Torque for Thread Engagement:
Proper torque is crucial for ensuring that the fittings are tightly engaged without over-stressing the threads. Under-torquing can lead to leakage, while over-torquing may damage threads or compromise the fitting’s structural integrity. Use a torque wrench to apply the appropriate torque based on the fitting specifications. Correct thread engagement ensures that fittings remain securely in place, maintaining proper hose orientation throughout operation.
Do and Do not
Do
√ Use a marker to mark directional datum lines to make it easier to maintain consistent angles.
√ Use brackets or fixtures to avoid hose movement during assembly.
√ Follow installation angle and torque instructions provided by the hose manufacturer.
√ Ensure hose is not in extreme bend, stretch or compression.
√ Check that fittings are tightened within the intended angle (use an angle gauge).
Dont
Incorrect Practice | Reason/Consequence |
Can damage the hose’s internal structure,lower burst pressure, and lead to early leaks or rupture. | Can damage the hose’s internal structure, lower burst pressure, and lead to early leaks or rupture. |
Not marking the orientation reference line before assembly | Likely to cause orientation misalignment during crimping resulting in assembly failure. |
Stretching the hose forcibly to achieve Alignment | This leads to misaligned installation, affecting fluid flow direction and possibly causing malfunction. |
Ignoring angle settings of rotating fittings | This leads to misaligned installation, affecting fluid flow direction and possibly causing malfunction. |
Using unspecified angle fixtures or tools | Not marking the orientation reference line before the assembly |
Failing to confirm orientation after crimping | Skipping this check increases the risk of misalignment, leaks, or premature hose failure |
Marking Techniques
Marking Hoses for Future Reference:
Once the hose is correctly installed, mark both ends of the hose near the fittings. Use permanent markers, tags, or colored tape to indicate the orientation. This makes it easier to reference the correct position during future inspections or maintenance. Some professionals also use hose tags with date and orientation information, which can be invaluable when the hose needs to be replaced or re-installed.
Mark Fittings for Alignment:
Mark the fitting’s angular orientation on both the fitting and hose to ensure that the alignment can be checked later. By marking these points, you can quickly identify whether the hose has shifted over time, allowing for faster realignment during routine checks.
Maintenance Guidelines
Practice | Description | Action Steps |
Regular Inspections | Hose orientation may shift over time due to vibration or pressure changes | Conduct monthly or quarterly visual inspections based on usage and conditions |
Re-Torque Fittings | Vibration and pressure cycling can loosen fittings | Use a torque wrench during maintenance to re-tighten fittings to spec torque |
Adjust Orientation as Needed | Misalignment can develop over time, leading to wear or failure | Re-align fittings as needed; ensure hose angles match original design intent |
Advanced Techniques for Optimizing Hose Orientation
Custom Hose Assemblies
Designing Custom Hose Assemblies for Specific Orientations:
When designing custom hydraulic hose assemblies, it’s crucial to consider the specific angular orientations required for each system. Begin by evaluating the space and layout of your system. Use CAD software to model the exact route the hose will take, ensuring that there is enough room for proper alignment without sharp bends or kinks.
When ordering custom assemblies, provide the manufacturer with detailed specifications. This includes the required angular offsets between fittings, hose length, material, and any special requirements such as pressure ratings or environmental conditions. Manufacturers can then pre-assemble hoses with the exact fitting orientation to ensure perfect alignment during installation. Preassembled hoses reduce the risk of misalignment and save installation time.
Factors to Consider:
System dimensions and where fittings will need to align.
Operating conditions, including temperature, pressure, and movement.
Custom labeling to ensure orientation is maintained over time.
Use of Swivel Fittings
Benefits of Swivel Fittings for Dynamic Systems:
Swivel fittings allow the hose to rotate freely at the connection point, reducing the stress on the hose from movement and vibration. This is especially beneficial in systems that require frequent repositioning, such as equipment with moving arms, rotating platforms, or machinery that operates under changing angles.
Swivel fittings prevent hoses from twisting during movement, ensuring the hose remains properly aligned while allowing for flexibility. This can help to extend the lifespan of the hose and fittings by preventing damage caused by excessive twisting or torsion.
Dynamic Hose Orientation for High-Mobility Systems:
In high-mobility systems, hoses are often subjected to constant movement and repositioning. Dynamic hose orientation involves using swivel fittings in combination with hose clamps and guides to control movement while maintaining the hose’s optimal alignment. This setup allows the hose to flex and rotate without kinking or putting undue stress on the fittings, ensuring the hydraulic system performs efficiently even in demanding conditions.
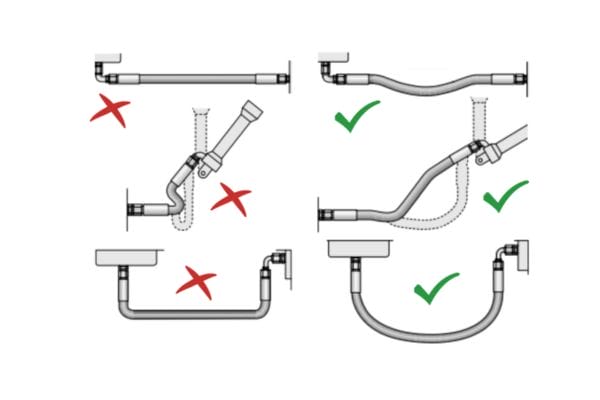
Hose Routing Optimization
Minimizing Bending and Twisting:
Proper hose routing plays a crucial role in maintaining optimal orientation. The objective is to minimize bending, twisting, and excessive movement, all of which contribute to premature wear and eventual hose failure.
Principle | Optimization Description |
Avoid Tight Bends | Use elbows(such as 45°or 90°)or custom fittings to navigate obstacles and avoid forcing the hose into sharp bends. |
Ensure Sufficient Length | Do not overstretch the hose; leave a certain amount of “flexibility allowance” to accommodate thermal expansion or mechanical movement. |
Use Proper Fixation | Secure hoses using hose clamps, guide rails, or other methods to prevent sagging, shaking, or rubbing against equipment. |
Examples of Ideal Routing Techniques:
Looping technique: This involves routing hoses in a loop formation to allow for greater flexibility without over-bending. Loops can absorb shock and vibration, preventing damage to the hose.
90° Elbows for sharp turns: When space is tight, use 90° elbows at fittings rather than forcing the hose into a tight radius bend. This maintains fluid flow and minimizes stress on the hose.
Parallel hose routing: When running multiple hoses together, ensure they are aligned and fastened securely with clamps. This avoids crossing and entanglement, reducing the risk of abrasion.
Conclusion
Proper hose orientation boosts safety, reduces downtime, and extends system life. Whether you’re upgrading, repairing, or installing, applying these best practices makes a real difference.
Ready to optimize your system? Explore Topa’s premium hydraulic hose solutions—engineered for precision and durability. Contact us today to get started.
FAQ
What is hydraulic hose orientation?
Hydraulic hose orientation refers to the angular alignment between the hose fittings, ensuring proper fluid flow and minimizing stress on the hose during operation.
Why is correct hose orientation important?
Correct orientation prevents excessive wear, reduces the risk of hose failure, and ensures optimal system performance by minimizing pressure drops and avoiding unnecessary strain on the hose.
How do you measure hose orientation?
To measure hose orientation, align one fitting at 0 degrees and use a protractor or visual guide to measure the angular offset in a clockwise direction for the second fitting.
What happens if hydraulic hoses are misaligned?
Misaligned hoses can lead to premature wear, leaks, reduced system efficiency, and even system failure due to excessive pressure or stress at the fittings.
What tools are used to measure hose orientation?
Common tools include protractors, angular measuring devices, and visual guides, which help ensure the correct alignment between the hose fittings.
How can I maintain proper hose orientation over time?
Regular inspections, re-torquing of fittings, and marking hoses for easy reference during maintenance are essential for ensuring hoses remain properly oriented during their lifespan.