Understanding hydraulic hose pressure limits is not just about efficiency—it’s a fundamental safety aspect. Exceeding these limits can lead to catastrophic failures, posing risks to operators, the machinery, and the environment. This article provides detailed insights into how pressure ratings work, why they matter, and how to prevent accidents by properly managing pressure limits in hydraulic hoses.
Basics of Hydraulic Hose Pressure
Working Pressure
Definition: Working pressure refers to the maximum pressure that a hydraulic hose can safely handle during regular operation. It is often specified in pounds per square inch (PSI) or bar.
Significance: The working pressure is a critical measure because it dictates the hose’s capacity to function safely within a hydraulic system. It ensures that the hose performs efficiently under the expected load conditions without the risk of failure.
Difference from Other Pressure Measures:
Working pressure should not be confused with burst pressure or peak pressure.
While working pressure represents the continuous, allowable operating pressure, it is substantially lower than the burst pressure, which is the hose’s failure point.
Unlike peak pressure, which accounts for short-term spikes, working pressure is the sustained load capacity during normal operation.
Burst Pressure
Definition: Burst pressure is the maximum pressure that a hydraulic hose can withstand temporarily before failing or rupturing. It represents the absolute pressure limit that the hose can manage for a brief moment.
Explanation:
It is typically four times the working pressure, serving as an indicator of the hose’s upper tolerance level. However, it’s important to note that operating a hose anywhere near the burst pressure is unsafe and may lead to catastrophic failure.
Importance: Burst pressure is primarily used as a safety benchmark during hose testing and manufacturing to ensure that the hose can endure extreme conditions without immediate damage. It acts as a crucial safety margin to prevent unexpected ruptures.
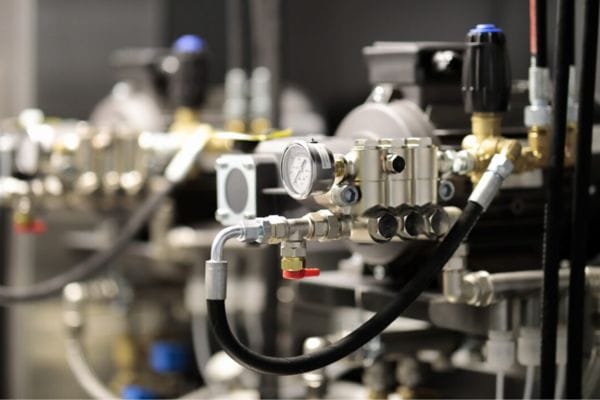
Testing Pressure
Overview: Testing pressure is the controlled pressure applied to hydraulic hoses during the manufacturing process to verify quality and integrity. It is used to confirm that the hose meets its specified working and burst pressure ratings.
Testing Procedures:
During testing, hoses are pressurized beyond their working pressure (often up to twice the working pressure) to assess their durability and safety.
Manufacturers use hydrostatic or pneumatic pressure tests to ensure the hose will perform reliably under normal operating conditions.
Purpose: This testing step is essential to ensure that the hoses are free of defects, capable of handling expected loads, and compliant with industry standards.
Safety Factor
Definition: The safety factor, often represented as a 4:1 ratio, refers to the margin of safety built into hydraulic hose design. It means that a hose’s burst pressure is at least four times its working pressure.
Importance:
The safety factor provides an additional buffer to accommodate unexpected pressure surges, variations in operating conditions, and potential hose degradation over time.
Application in Hose Selection and Operation:
When selecting hoses, it’s crucial to ensure that the working pressure aligns with the system’s operating requirements while maintaining an adequate safety factor.
For example, if a system requires a hose with a working pressure of 2,500 PSI, the hose should have a burst pressure of at least 10,000 PSI to maintain a 4:1 safety factor.
Why It’s Essential: This factor prevents hoses from operating at or near their burst pressure, significantly reducing the risk of accidents and prolonging the service life of the hydraulic hose.
Key Factors Influencing Hose Pressure Ratings
Hose Construction
Material Composition:
The materials used in the inner tube, reinforcement layers, and outer cover of the hose determine its pressure capacity.
Hoses made of materials like synthetic rubber, thermoplastic, or PTFE (Polytetrafluoroethylene) offer varying resistance to pressure, chemicals, and temperature.
For example, reinforced synthetic rubber hoses are commonly used for medium to high-pressure applications, while PTFE hoses are ideal for higher-pressure and more aggressive fluids.
Reinforcement Layers:
The number and type of reinforcement layers (braided or spiral steel wire, textile layers) directly impact the hose’s pressure capacity.
Braided Hoses: Generally designed for medium-pressure applications, they have one or two layers of braided reinforcement.
Spiral Hoses: Constructed with multiple layers (four or six) of spiral wire, these hoses are suitable for high-pressure applications.
The design and layering of these reinforcements provide additional strength and flexibility, enabling the hose to withstand increased pressure without compromising safety.
Design Considerations:
The hose’s overall design, including its bend radius and length, influences pressure resistance.
Hoses with a tighter bend radius can handle lower pressure as the bending stress is more pronounced, potentially weakening the hose structure.
Additionally, shorter hoses generally have better pressure resistance, as longer hoses are more prone to pressure drops and physical stresses.
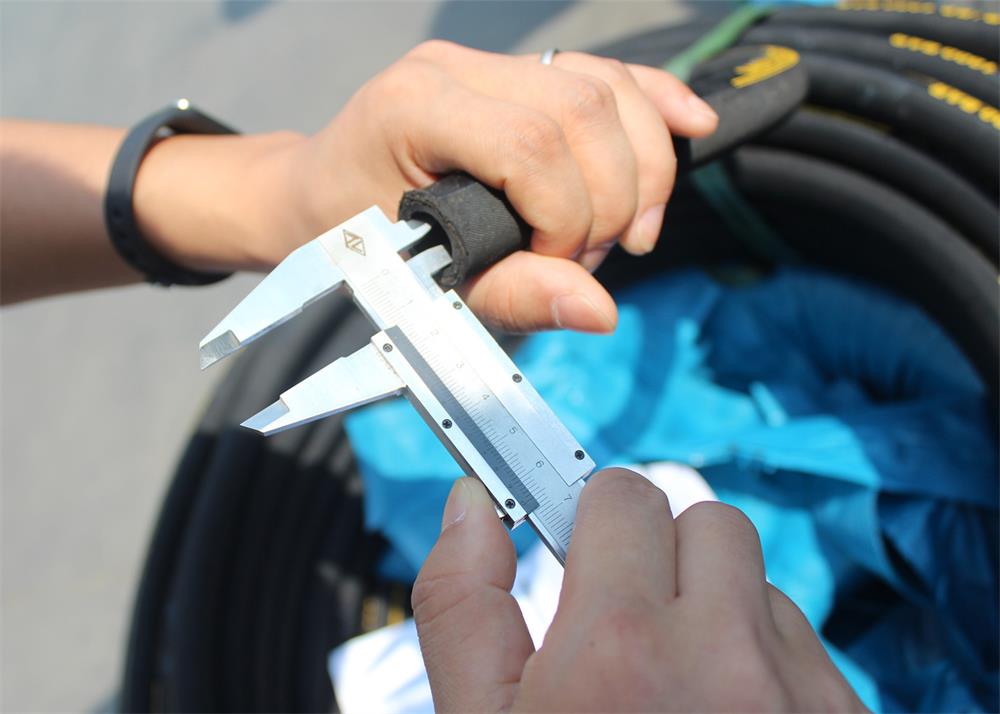
Hose Size and Diameter
Impact on Pressure Handling:
The internal diameter of the hose significantly affects its ability to handle pressure.
Smaller diameter hoses generally support higher pressure levels, as the internal area that the pressure acts upon is reduced, resulting in less force.
Conversely, larger diameter hoses have a greater internal surface area, which can lead to lower pressure capacity but higher fluid flow rates.
Flow Rate Considerations:
Besides pressure handling, hose diameter also impacts flow rates.
Narrower hoses may restrict flow, causing a buildup of pressure, while wider hoses allow greater fluid volume with less pressure.
Selecting the right hose diameter is essential to balance pressure capacity with flow requirements, preventing pressure spikes and maintaining system efficiency.
Temperature Influence
Temperature Effects on Pressure Capacity:
Temperature fluctuations can significantly alter a hose’s pressure capacity.
High Temperatures: As temperatures rise, the hose material becomes more pliable, which can reduce its overall pressure tolerance. For instance, a hose rated for 5,000 PSI at room temperature might only handle 4,000 PSI at 200°F (93°C).
Low Temperatures: Extremely low temperatures can make hose materials brittle, increasing the risk of cracks and leaks, which can compromise pressure handling.
Material-Specific Performance:
Different hose materials respond differently to temperature changes. For example, rubber hoses can handle high temperatures but may degrade faster under extreme heat, while PTFE hoses maintain better integrity under both high and low temperatures.
To ensure optimal performance, it’s essential to choose hoses that match the operating temperature conditions and consider temperature derating factors when calculating pressure limits.
Aging and Wear
Degradation Over Time:
Hydraulic hoses naturally degrade over time due to exposure to environmental elements (UV rays, ozone), chemicals, and operational stress.
As hoses age, they become more susceptible to cracking, hardening, and losing flexibility, all of which can lower their pressure capacity.
Impact of Wear and Tear:
Frequent bending, abrasion, and mechanical stresses during operation can weaken hose reinforcement layers, reducing the hose’s ability to withstand pressure.
Worn-out hose covers can also expose the reinforcement layers, leading to corrosion, weakening the overall hose structure, and making it prone to pressure failure.
Preventive Measures:
Regular inspections and maintenance can help identify early signs of wear, such as surface cracks, blisters, or leaks, enabling timely hose replacement to maintain pressure safety.
Identifying Pressure Limits on Hose Laylines
Reading Hose Laylines
What Are Laylines?
Laylines are printed markings that run along the length of a hydraulic hose, providing essential information about the hose’s specifications, including pressure limits.
These markings offer a quick visual reference for identifying the hose’s capacity, making it easier for operators and maintenance personnel to ensure the right hose is used for specific applications.
How to Identify Pressure Ratings:
The layline typically includes the working pressure rating expressed in PSI or bar. This figure is crucial, as it represents the maximum continuous pressure the hose can handle safely.
In addition to working pressure, some hoses may also list burst pressure on the layline, which represents the maximum short-term pressure capacity before hose failure.
Other vital information found on laylines includes:
Hose Type: The material or specific hose type, which helps determine compatibility with the fluid being conveyed and operating conditions.
Temperature Range: Indication of the hose’s temperature tolerance, ensuring it can handle the expected operating temperatures.
Reinforcement Layers: Information about the type and number of reinforcement layers, influences the hose’s pressure capacity.
Standard Compliance: Any industry standards (e.g., SAE, ISO) that the hose meets, confirming that it has been tested to certain safety and performance specifications.
Pressure Color Coding Systems
What Is Pressure Color Coding?
Some hydraulic hoses use a color-coding system as part of the layline or external cover to indicate pressure capacity, making it easy to identify pressure limits at a glance.
This system uses distinct colors or patterns to represent different pressure ratings, helping operators quickly match hoses to system requirements.
Common Color-Coding Standards:
While color-coding systems can vary by manufacturer, some commonly used color codes include:
Red: Typically indicates high-pressure hoses, often used for applications above 3,000 PSI.
Blue or Green: Used for medium-pressure hoses, which generally range between 1,500 and 3,000 PSI.
Yellow: Designates low-pressure hoses, usually under 1,500 PSI.
Additionally, some hoses may use striped patterns or combination colors to signify special features like extreme temperature tolerance or abrasion resistance.
Importance of Color Coding:
The color coding helps ensure quick and accurate hose selection, reducing the risk of pressure mismatches that could lead to hose failure.
It is particularly useful in complex systems where multiple hoses of varying pressure ratings are used. By standardizing hose identification, minimizes errors and enhances overall system safety.
Common Hazards of Exceeding Pressure Limits
Hose Burst Risks
Dangers of Hose Bursting:
Catastrophic Failure: Exceeding the working pressure can lead to a sudden and violent rupture, causing the hose to burst. This can release high-pressure hydraulic fluid, posing serious risks to operators and nearby personnel.
Potential Injuries:
The rapid release of fluid under pressure can cause severe injuries, including burns from hot hydraulic fluid, lacerations from flying debris, and even blunt force trauma from hose recoil.
In extreme cases, burst hoses can cause hydraulic fluid injection injuries, where fluid penetrates the skin, requiring immediate medical attention.
System Damage:
Hose bursts can damage nearby equipment, components, and connections within the hydraulic system, leading to additional repair costs and replacement of parts.
When a high-pressure burst occurs, it can cause pressure spikes throughout the system, potentially damaging valves, pumps, cylinders, and other connected equipment.
Operational Downtime:
A hose burst can halt operations immediately, leading to significant downtime. Depending on the severity of the damage, recovery can take hours or even days, causing production delays and financial losses.
Frequent hose bursts also indicate deeper issues, such as improper hose selection, inadequate maintenance, or flawed system design, which can further increase downtime and safety risks.
Leakage and Environmental Impact
Causes of Hose Leaks:
Exceeding the working pressure limit can weaken the hose structure over time, causing leaks at the fitting connections or along the hose body itself.
Overpressurization can lead to micro-cracks in the hose lining or damage to the reinforcement layers, allowing hydraulic fluid to seep out gradually.
Hydraulic Fluid Spills:
Hydraulic fluid leaks, even if slow, can lead to substantial fluid loss over time, causing reduced system performance and efficiency.
In the case of a rapid leak or burst, large quantities of hydraulic fluid can spill, creating hazards for workers and increasing the risk of slip-and-fall accidents.
Contamination Risks:
Leaked hydraulic fluid can contaminate the work environment, including nearby machinery, floors, and surfaces.
Hydraulic systems are often operated in environmentally sensitive areas, such as factories, agricultural fields, and marine settings, where fluid leaks can lead to soil, water, and ecosystem contamination.
Hydraulic oils can be toxic and difficult to clean, requiring costly spill containment measures, remediation, and potential legal penalties for environmental violations.
Environmental Damage:
Hydraulic fluid spills can have a long-term impact on the environment. Spilled oil can seep into soil, affecting plant life, contaminating groundwater, and harming wildlife.
Uncontrolled leaks can also breach containment systems, leading to large-scale environmental incidents that may require extensive cleanup efforts and regulatory intervention.
Safety Measures to Prevent Over-Pressurization
Proper Hose Selection
Importance of Correct Hose Selection:
The first and most crucial step in preventing over-pressurization is selecting the right hose for the specific application. Using a hose with an appropriate pressure rating is essential to avoid exceeding its capacity.
Match Pressure Ratings: Ensure that the hose’s working pressure aligns with the system’s operating pressure, incorporating a suitable safety factor (typically 4:1).
Consider Application Variables:
Take into account the type of hydraulic fluid, temperature variations, environmental conditions, and potential pressure surges when choosing a hose.
Different hoses have different constructions (e.g., braided, spiral) that suit varying pressure requirements. Braided hoses are ideal for medium-pressure applications, while spiral hoses are better suited for high-pressure environments.
Compatibility with Equipment: Choose hoses that are compatible with system connectors, fittings, and flow requirements, ensuring the hose will function properly under expected pressure conditions.
Regular Inspections
Visual Inspection Best Practices:
Frequency of Inspections: Conduct regular visual inspections, ideally as part of a routine maintenance schedule, to identify any signs of damage or degradation that may compromise the hose’s pressure capacity.
What to Look For:
Cracks, Bulges, or Blisters: These indicate potential structural failures or weaknesses that could lead to hose bursts.
Abrasion or Exposed Reinforcement: Check for excessive wear, particularly on the hose cover, which can expose reinforcement layers and reduce pressure resistance.
Leaks or Seepage: Inspect hose fittings and connections for any leaks, as these can be early signs of over-pressurization or improper fitting installation.
Functional Testing: Regular pressure tests can help identify any hidden vulnerabilities, verifying that the hose can still handle its rated working pressure.
Pressure Control Devices
Role of Pressure Relief Valves:
Install pressure relief valves in the hydraulic system to automatically release pressure when it exceeds the preset limit, preventing potential over-pressurization.
Relief valves protect hoses and other components from sudden spikes that can occur during equipment operation or start-up, maintaining safe pressure levels.
Use of Accumulators:
Incorporate accumulators to absorb pressure surges and maintain a stable operating pressure within the hydraulic system.
Accumulators also help regulate flow, reducing pressure fluctuations that could strain the hose and other components.
Other Devices:
Pressure Gauges: Install pressure gauges at key points in the system to monitor real-time pressure levels, enabling operators to take immediate action if pressures approach unsafe limits.
Flow Restrictors: Use flow restrictors to limit fluid flow, preventing pressure from building up excessively in sections of the system where over-pressurization risks are higher.
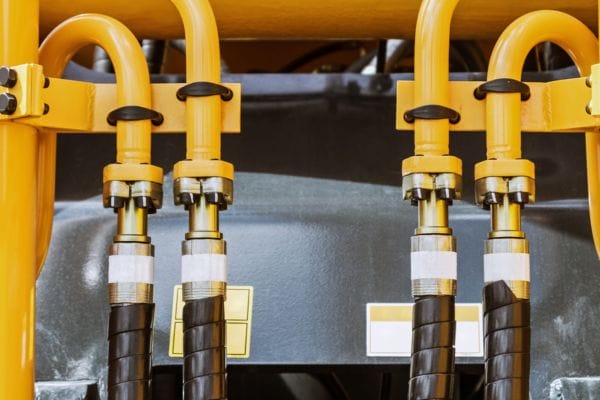
Proper Installation
Correct Installation Techniques:
Proper installation is critical to maintaining hose pressure integrity. Poor installation can lead to pressure drops, kinking, and premature wear, all of which increase the risk of over-pressurization.
Avoid Kinks and Twists:
Ensure that hoses are installed without kinks, twists, or excessive bending. Kinks restrict flow and increase internal pressure, while twists can weaken the hose structure and lead to bursts.
Maintain Minimum Bend Radius:
Adhere to the hose’s specified minimum bend radius to prevent undue stress on the hose reinforcement layers, which can weaken pressure capacity.
Secure Proper Fitting Connections:
Use compatible and correctly installed fittings to maintain a tight seal, preventing leaks and maintaining the hose’s pressure integrity. Improper connections can cause pressure drops or surges that compromise hose safety.
Avoid Abrasion and Friction:
Install hoses in such a way that they do not rub against sharp edges or abrasive surfaces, which can damage the outer cover and reinforcement layers, reducing pressure tolerance.
Conclusion
Take proactive steps to ensure your hydraulic system operates safely within pressure limits. Review your system’s hoses regularly, implement the recommended safety measures, and consult with professionals to assess pressure management and compliance. Conducting routine maintenance, training operators, and using the right components are fundamental to minimizing risks. Safety is achievable when hydraulic hose pressure limits are recognized and respected. By integrating best practices into daily operations, you not only protect personnel and equipment but also promote a safer, more reliable hydraulic system.
FAQ
What is the difference between working pressure and burst pressure?
Working pressure is the maximum continuous pressure a hose can handle safely, while burst pressure is the maximum pressure a hose can withstand briefly before failing.
How often should hydraulic hoses be inspected?
Hydraulic hoses should be inspected visually before each use and thoroughly every 3-6 months, depending on usage and operating conditions.
What are the signs that a hydraulic hose is over-pressurized?
Signs include bulging, leaks, unusual noises, and hose deformation. If you notice any of these, stop the system immediately and check the hose.
How can I prevent over-pressurization in my hydraulic system?
Use hoses with the correct pressure ratings, install pressure control devices like relief valves, and conduct regular maintenance checks.
What should I do if a hose bursts?
Shut down the system immediately, contain any fluid spills, and replace the damaged hose with a suitable one before resuming operations.
How can temperature affect hose pressure capacity?
High temperatures can reduce a hose’s pressure capacity, while low temperatures can make it brittle, increasing the risk of failure.