Hydraulic systems are vital components of many industrial applications, relying on pressurized fluid to perform tasks like lifting, clamping, or moving heavy machinery. At the core of these systems, hydraulic fittings play a crucial role by connecting hoses, pipes, and tubes to create a sealed and pressurized pathway for fluid flow. These fittings ensure that the system operates smoothly, efficiently, and safely, maintaining the integrity of the connections and preventing fluid leaks, pressure drops, or contamination.
Common Issues with Hydraulic Fittings
Leakage
Leakage is one of the most prevalent problems encountered in hydraulic systems, and it can lead to a range of performance, safety, and environmental concerns. Hydraulic fluid leaks not only result in system inefficiencies but can also create serious hazards, such as slipping risks and fire hazards in specific environments.
Causes of Leaks in Hydraulic Fittings
Improper Sealing
O-Ring Damage: O-rings are essential for creating a proper seal in hydraulic fittings. When these rings are damaged—due to wear, improper installation, or chemical incompatibility—they can no longer effectively seal the connection, leading to leaks. For instance, the wrong material choice for an O-ring in high-temperature applications can result in rapid degradation.
Incorrect Seal Types: Hydraulic fittings are designed for specific seal types, such as metal-to-metal seals, elastomeric seals, or composite seals. Using the wrong type can create gaps or weaken the seal, resulting in fluid leakage.
Misalignment During Installation: Fitting misalignment, even by a small degree, can cause a poor seal. Misalignment can occur during installation or from external forces applied to the fittings during operation. This causes uneven pressure distribution on the seal, leading to gradual fluid seepage or sudden leaks.
Over-Tightening
Thread Damage: Over-tightening fittings can strip or deform the threads, compromising the sealing surface. Once the threads are damaged, achieving a proper seal becomes difficult, resulting in leaks.
Seal Deformation: Excessive torque can deform O-rings, crush seals, or damage gaskets, making them unable to provide a reliable seal. It’s important to follow manufacturer-recommended torque specifications to prevent over-tightening.
Vibration
Connection Loosening: Continuous vibration within the hydraulic system can cause fittings to loosen over time, compromising the seal. This is especially common in high-pressure systems or systems exposed to constant movement.
Fatigue Failures: Repeated vibration can weaken the material of the fittings, causing cracks that may eventually result in leaks. The use of vibration dampeners or supports can help minimize these issues and maintain the integrity of the fittings.
Signs of Leaking Fittings and Impact on System Performance
Visual Signs
Fluid Accumulation: The most evident sign of leakage is the presence of hydraulic fluid around the fitting connections. In severe cases, puddles of hydraulic fluid can form beneath the equipment.
Residue or Stains: Residual fluid, often visible as oily stains or wet spots around fittings, can indicate slow leaks. Over time, this can attract dust and debris, making the issue more evident.
Performance Issues
Reduced Hydraulic Pressure: Leaks can cause a gradual drop in system pressure, leading to decreased force, slower actuator movements, or incomplete operations.
Increased Energy Consumption: As the system compensates for the pressure loss caused by leaks, it may use more power, resulting in higher energy costs and potential wear on pumps and other components.
Safety Concerns
Slippery Surfaces: Leaked hydraulic fluid can create slippery surfaces, posing a risk of falls or accidents in the workplace.
Fire Hazards: In systems using flammable hydraulic fluids, leaks can create a fire hazard if the fluid comes into contact with hot surfaces or sparks. Immediate attention to leaks is crucial in such high-risk environments.
Environmental Concerns: Hydraulic fluid leaks can have severe environmental impacts, especially if the fluid contaminates soil or water sources. Prompt containment and cleanup are necessary to prevent environmental damage.
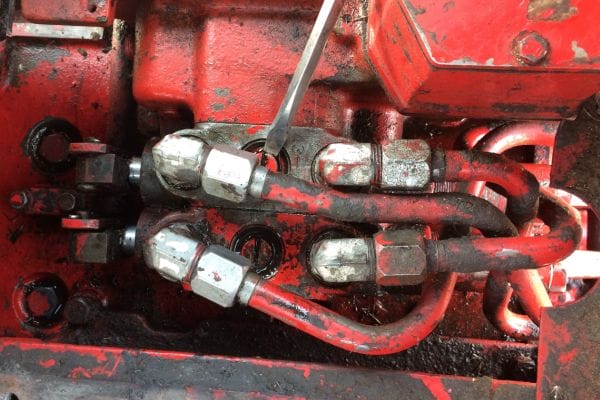
Pressure Surges and Spikes
Pressure surges and spikes are sudden increases in hydraulic pressure that can put undue stress on fittings and other components, often leading to sudden failures or gradual degradation.
Explanation of Pressure Surges and Their Effects on Fittings
Nature of Pressure Surges
Abrupt Flow Changes: Pressure surges occur when there is a sudden change in fluid flow, such as when a valve is closed rapidly or when a pump starts or stops suddenly. These abrupt changes create pressure waves that travel through the hydraulic system, exerting significant force on fittings.
Hydraulic Shock: The pressure wave caused by a surge can be severe, sometimes exceeding the design limits of fittings, hoses, and other components. Over time, repetitive surges can fatigue fittings, causing cracks, deformation, or even sudden breakage.
Impact of Pressure Surges on Fittings
Fatigue Failures: Repeated exposure to pressure spikes can weaken fittings, particularly those not designed for high-pressure fluctuations. The material may develop micro-cracks, which can propagate over time and cause sudden failure.
Seal Damage: Pressure spikes can also compress seals beyond their capacity, resulting in deformation or extrusion. Once a seal is compromised, it becomes a potential leakage point.
Identifying Symptoms of Pressure-Related Fitting Failures
Cracks or Distortion
Visible Damage: Pressure surges often cause visible cracks or deformation in fittings. Regular inspection can help detect these early signs of failure, allowing for timely repairs or replacements.
Deformation of Seals: Deformed or extruded seals around fittings can indicate that pressure spikes have exceeded the seal’s tolerance levels.
Reduced System Efficiency
Erratic System Performance: If the hydraulic system’s performance becomes inconsistent, it may be due to pressure-related fitting issues. Pressure spikes can cause abrupt changes in flow, resulting in jerky or sluggish actuator movements.
Noisy Operation
Unusual Noises: Banging or knocking sounds within the system often accompany pressure surges. These noises indicate that the pressure wave impacts fittings or other components, stressing the system and potentially causing damage.
Corrosion and Wear
Corrosion and wear gradually weaken hydraulic fittings over time, reducing system reliability and potentially leading to catastrophic failures if left unchecked.
Factors Contributing to Fitting Corrosion and Wear
Fluid Contamination
Water Contamination: Water in hydraulic fluid is a major cause of corrosion. Water can enter the system through condensation, damaged seals, or contaminated fluid. It reacts with metal surfaces, causing rust and pitting in fittings.
Chemical Contamination: Chemicals in hydraulic fluid, such as acids or incompatible additives, can accelerate corrosion in fittings, especially those made of incompatible metals.
Particulate Contamination: Dirt, metal shavings, or other particulates in the fluid can act as abrasive agents, wearing down the surfaces of fittings and causing leaks over time.
Harsh Environments
Temperature Extremes: High temperatures can accelerate chemical reactions, increasing the rate of corrosion, while low temperatures can make materials brittle, leading to wear.
Humidity and Moisture: Outdoor or industrial environments with high humidity can lead to external corrosion on fittings, especially those not protected with coatings or corrosion-resistant materials.
Improper Material Selection
Material Compatibility: Fittings made from materials incompatible with the hydraulic fluid or environmental conditions can corrode rapidly. For instance, using steel fittings in systems exposed to saltwater or corrosive chemicals can lead to premature failure.
How to Recognize Early Signs of Deterioration
Discoloration or Rust
Visual Inspection: Regular inspection for discoloration, rust, or pitting on fittings can help detect early stages of corrosion. Immediate action can prevent further damage and ensure system integrity.
Fluid Leakage or Seepage
Slow Leaks: In corrosive environments, leaks often start as slow seepage due to weakened seals or corroded fitting surfaces. Monitoring for small fluid accumulations around fittings can help identify issues early.
Decreased Pressure
Gradual Pressure Drop: Corroded or worn fittings can cause gradual pressure loss in the system, as their internal diameter changes or their sealing surfaces degrade. Pressure monitoring can help detect such issues before they become severe.
Tools for Troubleshooting Hydraulic Fittings
Basic Tools
For effective troubleshooting and maintenance of hydraulic fittings, having the right set of basic tools is essential. Proper use of these tools ensures the integrity of fittings and connections.
Wrenches
Adjustable and Torque Wrenches: These are vital for tightening and loosening hydraulic fittings. It’s important to use the correct size to avoid damaging the fittings.
Proper Use: Torque wrenches ensure fittings are tightened to the correct specifications, preventing over-tightening, which can cause leaks or thread damage.
Sealants and Thread Tape
Sealants: Thread sealants (often anaerobic sealants) help to fill gaps and prevent leaks at threaded connections. Use them sparingly to avoid excess sealant contaminating the system.
Thread Tape: Also known as PTFE tape, it is applied to the male threads before connecting to ensure a tight seal and prevent leaks. It’s crucial to use the appropriate tape for hydraulic applications to maintain fitting integrity.
Advanced Diagnostic Tools
Advanced tools allow for more accurate and effective identification of issues within hydraulic systems, enabling proactive maintenance.
Ultrasonic Leak Detectors
How They Work: These devices detect high-frequency sounds created by pressurized fluid escaping through leaks. They convert ultrasonic sound into audible signals, helping to locate leaks even in noisy environments.
When to Use: Ideal for identifying small leaks that are not easily visible. They are particularly useful in high-pressure systems where even minor leaks can lead to significant fluid loss over time.
Pressure Transducers
Functionality: These sensors convert hydraulic pressure into an electrical signal, which can be read by monitoring devices. They help in detecting variations in pressure within the system.
Use in Monitoring Pressure Changes: Pressure transducers are essential for real-time monitoring, allowing operators to quickly identify and respond to unexpected pressure spikes, drops, or fluctuations that could indicate fitting issues.
Thermal Imaging Cameras
Identifying Hotspots: These cameras detect infrared radiation to visualize temperature differences in hydraulic systems. Hotspots often indicate leaks, as escaping pressurized fluid can cause localized heating.
Use for Flow Restrictions: Thermal imaging can also help identify flow restrictions within fittings, as reduced flow can lead to abnormal temperature patterns.
Monitoring Technologies
Advanced monitoring solutions provide continuous and real-time data, enabling predictive maintenance and reducing downtime.
Real-Time Monitoring Solutions
Pressure Monitoring: Sensors continuously measure hydraulic pressure, providing data that can help identify pressure drops caused by leaks or fitting failures.
Temperature Monitoring: Real-time temperature sensors track system heat levels, allowing early detection of temperature anomalies that may signal fitting leaks or blockages.
Flow Monitoring: Flow sensors help monitor fluid flow rates, making it easier to identify reductions in flow, which could indicate obstructions or leaks in fittings.
Remote Sensors and IoT Applications
Remote Sensors: Wireless sensors provide real-time data from various system points, allowing technicians to monitor fitting conditions remotely.
IoT Applications in Diagnostics: Internet of Things (IoT) technology can be integrated into hydraulic systems to provide predictive analytics. This technology offers insights into fitting conditions, pressure levels, and system performance, enabling proactive maintenance and early fault detection.
Advanced Techniques for Troubleshooting
Systematic Leak Detection
Accurately identifying and locating leaks is essential for maintaining hydraulic system performance and preventing further damage. A systematic approach ensures that leaks are addressed effectively and promptly.
Step-by-Step Approach to Identifying Leaks
Visual Inspection
Initial Assessment: Begin by visually inspecting the hydraulic fittings, hoses, and connections for signs of fluid accumulation, wet spots, or stains.
Using Leak Detection Dye: Introduce a UV-reactive dye into the hydraulic fluid. As the dye circulates through the system, it highlights leak points when exposed to UV light, making even small leaks visible.
Applying Soapy Water Solution
Simple Leak Check: For low-pressure systems, apply a soapy water solution to the fitting connections. Bubbles will form at the site of any leak, providing a quick confirmation.
Using Ultrasonic Leak Detectors
Advanced Detection: Ultrasonic leak detectors capture high-frequency sounds produced by fluid escaping from leaks. These devices can locate leaks that are not visible, especially in high-pressure systems or hard-to-reach areas.
Pressure Testing
Isolating the System: Conduct a pressure test by isolating sections of the hydraulic system and applying pressure incrementally. This helps to identify the specific location of leaks based on pressure drops.
Thermal Imaging Cameras
Heat Mapping: Thermal imaging can detect temperature changes caused by escaping fluid. Leaks often create cooler or hotter areas, depending on the fluid’s characteristics, making them visible on thermal imaging displays.
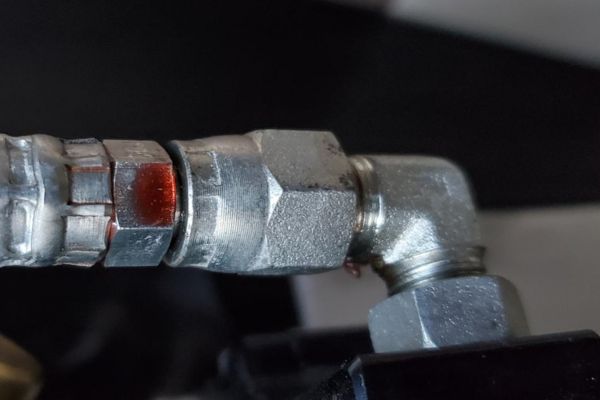
Analyzing Pressure Variations
Understanding and analyzing pressure fluctuations is key to diagnosing issues related to pressure surges, spikes, or drops that can affect hydraulic fittings.
Techniques for Analyzing Pressure Spikes
Using Data Loggers
Continuous Monitoring: Data loggers can be connected to the hydraulic system to continuously record pressure readings over time. This data can reveal patterns of pressure spikes that may not be evident during manual checks.
Identifying Patterns: Analyze logged data to identify recurring spikes, their timing, and potential triggers such as sudden valve closures or pump startups.
Pressure Sensor Integration
Real-Time Analysis: Install pressure sensors at critical points in the system to provide real-time data on pressure levels. This data can help operators adjust system parameters or take preventive action to mitigate pressure spikes.
Waveform Interpretation
Diagnosing Pressure Waveforms: Pressure sensors generate waveforms that represent system pressure over time. Analyze these waveforms to detect sudden spikes, pressure drops, or other anomalies that indicate potential fitting failures.
Identifying Fitting Weaknesses: Irregular waveforms, such as rapid peaks followed by drops, may suggest that fittings are not adequately withstanding pressure changes, possibly due to fatigue or improper material selection.
Corrosion Mitigation Strategies
Preventing and managing corrosion is crucial for extending the lifespan of hydraulic fittings and ensuring system reliability.
Use of Coatings and Corrosion-Resistant Materials
Protective Coatings
Galvanization and Plating: Apply zinc plating, galvanization, or other coatings to steel fittings to prevent rust. These coatings provide a barrier between the fitting material and corrosive elements, such as water or chemicals.
Epoxy Coatings: For fittings exposed to highly corrosive environments, consider using epoxy coatings that provide an extra layer of protection against both moisture and chemical exposure.
Corrosion-Resistant Materials
Stainless Steel and Brass Fittings: Replace standard fittings with stainless steel or brass, which offer superior resistance to rust and corrosion. These materials are ideal for environments with high humidity, saltwater exposure, or aggressive chemicals.
Composite Fittings: For certain applications, composite materials can provide resistance to both corrosion and wear, making them a suitable alternative to traditional metal fittings.
How to Inspect Fittings for Early Signs of Rust or Pitting
Routine Visual Checks
Surface Inspection: Regularly inspect fittings for surface discoloration, rust, or pitting. Early detection of surface changes can prevent more severe corrosion and potential failures.
Thickness Gauging
Ultrasonic Thickness Testing: Use ultrasonic thickness gauges to measure the wall thickness of metal fittings. This technique detects material loss due to corrosion before it becomes visible on the surface.
Handling Vibration-Related Failures
Vibration can cause significant wear and damage to hydraulic fittings, leading to leaks, cracks, or complete failure. Detecting and managing vibration is key to maintaining system integrity.
Methods for Detecting Vibration Sources
Vibration Sensors
Real-Time Monitoring: Attach vibration sensors to critical points of the hydraulic system, including near fittings. These sensors provide real-time data on vibration levels and can identify problematic frequencies that may be causing fitting issues.
Frequency Analysis
Identifying Harmful Frequencies: Analyze vibration frequency data to determine which frequencies are most likely to cause fitting loosening or fatigue. Adjust system components or add dampening measures to reduce these frequencies.
Proper Use of Vibration Dampeners
Installing Dampeners
Strategic Placement: Place vibration dampeners at key locations, such as near pumps, valves, and fittings, to absorb and reduce the transmission of vibrations throughout the hydraulic system.
Isolation Mounts: Use isolation mounts to separate hydraulic components from vibrating surfaces. This reduces the direct transfer of vibrations to fittings, minimizing loosening or wear.
Regular Maintenance of Dampeners
Inspection and Replacement: Regularly inspect vibration dampeners for signs of wear or deterioration, as worn dampeners can lose effectiveness. Replace as needed to maintain optimal vibration reduction.
Best Practices for Hydraulic Fitting Maintenance
Routine Inspection
Routine inspection is one of the most important steps in hydraulic fitting maintenance. It allows early detection of potential problems, helping to prevent leaks, pressure drops, and other system failures.
Frequency of Inspections and Key Components to Check
Inspection Frequency
High-Pressure Systems: For systems operating at high pressure, perform inspections weekly or bi-weekly to catch early signs of wear, leaks, or damage.
Low-Pressure Systems: For systems with lower pressure, monthly inspections are often sufficient, though high-use environments may require more frequent checks.
Key Components to Inspect
Visual Inspection of Fittings: Check for leaks, discoloration, rust, and cracks on the surface of fittings.
Seal Condition: Inspect O-rings, gaskets, and seals for signs of wear or deformation. Pay special attention to any hardened, cracked, or compressed seals.
Thread Integrity: Examine the threads on both fittings and connections for signs of wear, corrosion, or cross-threading.
Vibration Damage: Look for signs of vibration damage, such as loose connections, unusual noises, or cracked fittings.
Creating a Maintenance Schedule Based on System Usage and Environmental Factors
Customizing Maintenance Schedules
System Usage: In systems with high operating hours or continuous use, increase inspection and maintenance frequency to ensure components remain in optimal condition.
Environmental Factors: In harsh or corrosive environments, schedule more frequent inspections and consider using corrosion-resistant fittings. Humid, dusty, or temperature-extreme environments can accelerate wear and corrosion, necessitating a tailored maintenance approach.
Documenting Inspections
Maintenance Logs: Keep detailed logs of inspection dates, findings, and corrective actions. This helps in tracking fitting performance over time and identifying patterns or recurring issues.
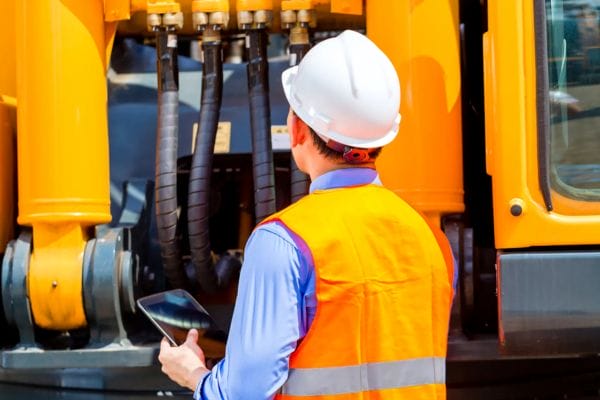
Proper Installation Techniques
Proper installation is critical to ensure the reliability and longevity of hydraulic fittings. Inadequate installation can lead to premature leaks, pressure failures, and safety risks.
Ensuring Proper Torque Specifications for Different Fitting Types
Use of Torque Wrenches
Setting Torque Values: Always use a torque wrench to ensure fittings are tightened to the manufacturer-recommended specifications. Under-tightening can lead to leaks while over-tightening can damage seals and threads.
Adjusting for Fitting Type: Different fittings, such as JIC, O-ring face seal, or NPT, require specific torque values. Refer to manufacturer guidelines to prevent misapplication of torque and ensure correct installation.
Avoiding Common Mistakes
Cross-Threading Prevention: Align fittings properly before tightening to avoid cross-threading, which can damage threads and compromise the seal.
Gradual Tightening: Tighten fittings gradually to avoid stressing the components, especially when working with larger or high-pressure fittings.
Use of Correct Tools and Techniques to Avoid Over- or Under-Tightening
Proper Tools
Wrenches: Use wrenches that match the fitting size and type. Adjustable wrenches should be used carefully to avoid rounding or damaging the fittings.
Thread Sealant: For tapered fittings, apply the appropriate amount of thread sealant or PTFE tape to ensure a proper seal, avoiding excess that could contaminate the system.
Installation Techniques
Lubrication: Use a small amount of fitting-approved lubricant on threads to prevent galling and facilitate proper tightening. Avoid using lubricants that could react with hydraulic fluid.
Sequential Installation: When connecting multiple fittings, tighten them sequentially to ensure uniform pressure distribution and prevent misalignment.
Cleaning and Contamination Control
Maintaining a clean hydraulic system is essential for preventing fitting damage, ensuring proper sealing, and reducing wear on all system components.
Importance of Maintaining Cleanliness to Prevent Fitting Damage
Contamination Risks
Fluid Contaminants: Dirt, debris, and metal particles in hydraulic fluid can cause premature wear of fittings, leading to leaks or failure.
Environmental Contaminants: Dust, moisture, and corrosive substances in the environment can compromise the seal integrity of fittings, especially if the system is not adequately sealed.
Cleaning Fittings During Maintenance
External Cleaning: Wipe down fittings and connections regularly to remove dust, dirt, and moisture that could enter the system during maintenance or operation.
Flushing the System: Periodically flush the hydraulic system to remove internal contaminants that could damage seals and fittings.
Use of Filters and Fluid Analysis as Preventive Measures
Filtration Systems
High-Quality Filters: Install high-quality filters to trap contaminants before they reach fittings. Regularly check and replace filters to ensure optimal performance.
Bypass Filtration: For systems with critical fittings, consider using bypass filtration systems that continuously clean hydraulic fluid, reducing contamination risk.
Fluid Analysis
Routine Testing: Conduct regular fluid analysis to detect contaminants, water content, and fluid degradation. Analyzing fluid samples can provide early warnings of potential fitting damage or system issues.
Adjusting Maintenance Based on Results: Use fluid analysis results to adjust maintenance schedules, replace seals, or address other fitting issues based on detected contaminants or changes in fluid condition.
Conclusion
By implementing the advanced techniques discussed in this guide, such as systematic leak detection, analyzing pressure variations, corrosion mitigation strategies, and vibration management, readers can enhance their hydraulic system’s reliability and efficiency. Proper routine inspection, correct installation practices, and thorough cleaning also play vital roles in preventing common fitting issues. Consistently applying these best practices will minimize downtime, reduce repair costs, and extend the lifespan of hydraulic components.
FAQ
What are the most common causes of hydraulic fitting leaks?
The most common causes include improper sealing, over-tightening, vibration, and wear due to corrosion or fluid contamination.
How can I prevent over-tightening hydraulic fittings?
Use a torque wrench to tighten fittings according to the manufacturer’s specifications, ensuring you apply the correct torque level for the specific fitting type.
What tools are best for detecting leaks in hydraulic fittings?
Tools like ultrasonic leak detectors, thermal imaging cameras, and pressure transducers are effective for identifying leaks, especially in high-pressure systems.
How often should I inspect hydraulic fittings for leaks or damage?
High-pressure systems should be inspected weekly or bi-weekly, while low-pressure systems can be inspected monthly. Adjust the frequency based on system usage and environmental conditions.
What materials are best for corrosion-resistant hydraulic fittings?
Stainless steel, brass, and certain composite materials offer good resistance to rust and corrosion, making them suitable for harsh environments.
How does vibration affect hydraulic fittings?
Continuous vibration can loosen fittings over time, leading to leaks or cracks. Using vibration dampeners and isolation mounts helps minimize these effects.