That slight hum or shake in your machine seems minor. It’s easy to ignore. But this is a dangerous symptom of a problem that is actively fatiguing metal and loosening connections.
Vibration in hydraulic systems is a destructive force that fatigues components like hoses and fittings, loosens connections causing leaks, and can lead to sudden, catastrophic failure. It is a key indicator of underlying problems that must be dealt with to ensure system longevity and safety.
Vibration is the system’s way of screaming that something is wrong. It is never normal. Learning to listen to that scream and understand what it means is one of the most important skills for anyone responsible for hydraulic machinery. It is the key to moving from reactive repair to proactive maintenance.
What Actually Causes Vibration in a Hydraulic System?
That hum seems harmless. But it’s a sign of a deeper problem silently shaking your expensive machinery apart from the inside.
The primary causes are pump-induced pressure ripples, fluid cavitation or aeration, turbulence from restrictions or sharp bends in plumbing, and mechanical imbalance in rotating components like motors and pumps. Each source indicates a specific system issue.
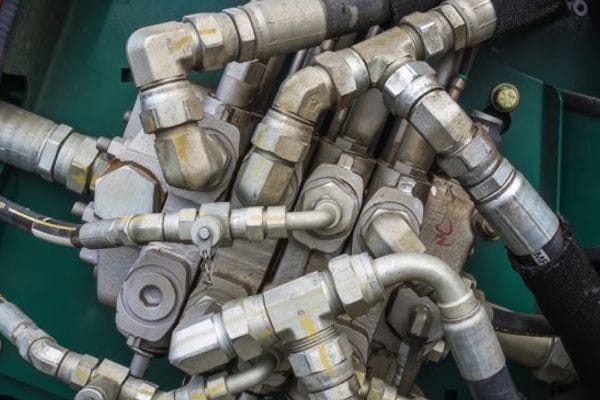
When a machine shakes, it’s not just a single event; it’s a complex interaction of different forces. Understanding where the vibration is coming from is the first step in diagnosing and fixing it. The vibration isn’t the disease itself; it’s a symptom. I often explain to my clients that they need to be a “machine doctor” and trace the symptom back to the root cause. The good news is that different causes create different types of vibration, which can help in your diagnosis.
Pump-Induced Pulsations
Every time a piston, gear, or vane in a hydraulic pump passes the outlet port, it releases a pulse of pressurized fluid. This creates a rapid, high-frequency “ripple” in the hydraulic pressure. While a well-designed system can dampen this, a worn pump or a system without a proper accumulator will transmit these pulsations throughout the entire circuit. This often feels like a steady, high-frequency hum or buzz that changes pitch with the engine’s RPM.
Cavitation and Aeration
These two are often confused, but they are different problems.
- Aeration is when outside air gets sucked into the system, usually through a bad seal or a leak on the pump’s suction side. The entrained air bubbles compress and decompress as they go through the pump, causing a high-pitched whining or chattering sound.
- Cavitation is the formation of vapor bubbles in the fluid when the suction pressure is too low (a vacuum is being pulled). This can be caused by a clogged suction filter or a line that is too long or small. When these vapor bubbles collapse under pressure inside the pump, it sounds like marbles or gravel are being thrown around inside the pump and creates an extremely destructive, high-impact vibration.
Fluid Turbulence
Fluid is supposed to flow smoothly (laminar flow). When it is forced through sharp 90-degree bends, sudden changes in pipe diameter, or partially closed valves, the flow becomes chaotic and turbulent. This churning action creates random, unpredictable vibrations and can often be felt as a shuddering in the pipes or hoses downstream from the restriction.
How Does Vibration Damage Hydraulic Hoses and Tubing?
Your hoses look fine, but they keep failing early. You blame the hose, but a hidden force is afoot, wearing them out internally.
Vibration causes accelerated fatigue in a hose’s wire reinforcement by constantly flexing it back and forth. It also leads to external abrasion as the hose rubs against machine parts, wearing away its protective cover.
A hydraulic hose assembly is designed to be strong and flexible, but it is not designed to endure constant, high-frequency shaking. At Topa, we conduct rigorous impulse tests on our hoses for clients from demanding markets like the USA and UK, proving they can handle hundreds of thousands of pressure cycles. However, adding vibration to the mix dramatically shortens that lifespan. It attacks the hose both from the inside and the outside.
Internal Fatigue of Wire Reinforcement
The steel wire braids or spirals inside a hose are its muscle. They contain the pressure. Vibration subjects these wires to millions of tiny, rapid bending cycles. Think about bending a paperclip back and forth; eventually, it breaks from metal fatigue. The same thing happens to the reinforcement wires inside the hose. The vibration finds a weak spot and focuses the fatigue there until the wires start snapping. Once enough wires are broken, the hose will develop a bulge and burst, often well below its rated working pressure. This internal damage is invisible from the outside until it is too late.
External Abrasion Damage
This is a more visible but equally dangerous problem. When a hose vibrates, it often rubs against the machine’s frame, another hose, or a bracket. This constant friction acts like sandpaper, slowly grinding away the protective outer rubber cover. Once the cover is gone, the steel wire reinforcement is exposed to moisture and dirt. This leads to rust, which corrodes and weakens the wire. a combination of abrasion and rust is a guarantee of a premature and unexpected hose failure. This is why proper routing and clamping are not just cosmetic; they are essential for safety.
Can Vibration Loosen Fittings and Cause Dangerous Leaks?
A tiny, weeping leak appears at a fitting. You tighten it, but it comes back. The real problem isn’t the tightness, it’s vibration.
Yes. Constant micro-movements from vibration can overcome the static friction of threaded connections, causing fittings like JIC or NPT to slowly back off and leak. It also puts extreme fatigue stress on crimped fittings.
This is one of the most common and dangerous results of system vibration. I’ve seen this happen in every industry, from farming in Laos to construction in the Philippines. A secure fitting relies on a specific clamping force and the friction it creates. Vibration works directly against that friction. It is a relentless force that tirelessly works to shake things loose. It affects both reusable threaded fittings and permanent crimped fittings, but in different ways.
Loosening of Threaded Fittings
Fittings like JIC (37-degree flare) or BSPP (with a bonded seal) rely on metal-to-metal or seal compression to stay tight. Vibration introduces a constant cycle of loading and unloading on the threads. This tiny movement, repeated millions of times, can be enough to slowly work the nut loose, breaking the seal. At first, it might just be a small weep, a “sweaty” looking fitting. But as it continues to loosen, the leak will grow, resulting in fluid loss, safety hazards, and environmental contamination. An operator might simply tighten it, but unless the root cause of the vibration is fixed, the fitting will just loosen again.
Stress on Permanent Crimped Assemblies
For a crimped fitting, the danger is fatigue. A properly crimped assembly from a matched system like ours is incredibly strong. However, vibration transmits energy directly into the assembly. The highest stress point is typically right where the hose exits the metal collar of the fitting. The vibration energy concentrates here, bending the hose back and forth against the rigid collar. This accelerates the metal fatigue of the wire reinforcement at that exact point, which is why many vibration-induced failures happen right at the fitting. The hose doesn’t blow out of the crimp; it ruptures right next to it.
How Can You Effectively Reduce or Eliminate Hydraulic Vibration?
You’ve found the source of vibration. But what’s the solution? You need a practical, effective strategy to silence the shake for good.
Solutions involve securing plumbing with proper clamps, installing vibration dampeners or accumulators, ensuring correct fluid viscosity and levels, and performing proper maintenance on mechanical components like motor-pump alignments.
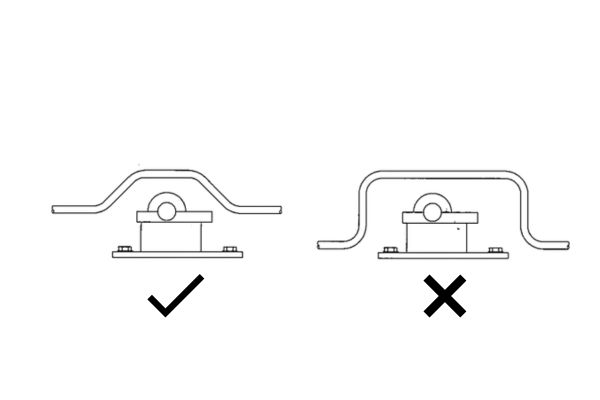
Fixing the problem of vibration is control and support. Once you have diagnosed the likely source, you can apply a combination of solutions to absorb the energy, support the components, and fix the root mechanical or hydraulic issue. It’s a systematic approach.
Proper Clamping and Mounting
This is the first and most cost-effective solution. Hoses and tubes should never be allowed to hang free over long distances. They must be secured to the machine frame.
- Use the Right Clamp: Do not use simple metal clamps. Use clamps with a cushioned elastomer insert. These cushions absorb high-frequency vibrations before they can damage the hose or tube.
- Correct Spacing: Follow manufacturer recommendations for clamp spacing. A good rule of thumb is to support a hose or tube at least every meter, and more frequently on high-vibration lines.
- Isolate Components: Use bulkhead fittings to pass lines through walls or frames. This secures the line and isolates vibration from one area of the machine to another.
Using Accumulators and In-Line Dampeners
For systems with significant pump pulsation, a properly sized accumulator is the best solution. An accumulator is like a shock absorber for the hydraulic system. It has a nitrogen-charged bladder that absorbs the pressure spikes and releases fluid during the low points, smoothing out the pump ripple before it can travel through the system. For specific problem areas, smaller in-line dampeners can also be installed to absorb localized pulsations.
Fluid and Maintenance Best Practices
Often, vibration is a direct result of poor maintenance.
- Fix Leaks: Immediately fix any suction-side leaks to prevent aeration.
- Clean Filters: Keep suction strainers and filters clean to prevent pump cavitation.
- Use Correct Fluid: Ensure the hydraulic fluid’s viscosity is correct for the operating temperature. Fluid that is too thin will not lubricate properly, while fluid that is too thick can cause cavitation.
What Are the Best Methods for Detecting and Diagnosing Vibration?
You know vibration is bad, but it’s hard to pinpoint. You guess at the source, replacing parts and hoping to solve the problem randomly.
Start with your senses: feel for excessive shaking and listen for unusual noises. For a more precise diagnosis, use tools like an infrared thermometer to find hotspots or specialized vibration analysis equipment for professional root cause analysis.
Diagnosing vibration doesn’t always require expensive tools. Many of my most experienced customers can tell what’s wrong just by sound and touch. The key is to be systematic. Start with the easy, sensory checks, and then move to more advanced methods if needed. Treating this like a detective’s investigation will save you from just randomly replacing parts.
The Sensory Check (Human Senses)
This is your first line of defense.
- Touch: Carefully (avoiding hot or moving parts) place your hand on various lines and components. Can you feel a buzz, a shudder, or a hard knocking? The location where the vibration is strongest is often close to the source.
- Sound: Listen closely. A high-pitched whine often indicates aeration. A loud rattling or grinding sound like rocks in a can is almost certainly cavitation. A hammering sound can indicate a “water hammer” effect from valves closing too quickly.
- Sight: Look for visibly shaking hoses or components. Check for blurry gauges. Look for the telltale sign of abrasion dust where a hose might be rubbing against a frame.
Basic Diagnostic Tools
- Infrared Thermometer: This is an incredibly useful tool. Aim it at different components. An abnormally hot pump, motor, or valve can indicate excessive friction or internal leakage, both of which are related to vibration issues. A hotspot can pinpoint the problem area.
- Pressure Gauge: Watch the needle on your pressure gauges. Is it steady, or is it fluttering rapidly? A fluttering needle is a clear indicator of pressure pulsations in that part of the circuit.
Advanced Analysis
For complex or critical systems, professional vibration analysis is the best route. A technician uses a handheld analyzer with a sensor to measure the exact frequency and amplitude of the vibration. This data can be compared to a database of known fault signatures to pinpoint the exact cause with incredible accuracy, such as a failing pump bearing or a misaligned motor shaft.
How Can Vibration Damage Other System Components?
Your hoses and fittings seem okay. But your gauges read erratically and valves seem sticky. You chase these individual problems, not realizing the root cause is systemic vibration.
Vibration damages sensitive instruments like gauges, causing inaccurate readings. It can cause valve spools to seize or shift unexpectedly, and it accelerates the wear of seals and O-rings throughout the entire system.
The destructive force of vibration isn’t limited to the plumbing. It attacks every single component in the system, especially those with tight tolerances or sensitive internal parts. It’s a whole-system problem.
Damage to Gauges and Sensors
Pressure gauges and electronic pressure transducers are precision instruments. The delicate gears and linkages inside an analog gauge can be quickly destroyed by constant, harsh vibration, causing the needle to stick or give false readings. This is dangerous because an operator might think the system pressure is safe when it is actually too high. Electronic sensors can also suffer from fatigue in their internal connections, leading to erratic signals and phantom fault codes.
Malfunctions in Valves
Hydraulic valves rely on spools that slide within a body with incredibly tight clearances. Uncontrolled vibration can cause these spools to chatter or oscillate in their bores. This leads to rapid wear on both the spool and the valve body, causing internal leakage and a loss of system efficiency. In some cases, the vibration can cause the spool to stick in one position or even shift unexpectedly, leading to jerky and uncontrolled machine movement.
Accelerated Seal Wear
Every hydraulic cylinder, pump, motor, and valve is filled with seals and O-rings. Their job is to contain high-pressure fluid while allowing parts to move. Vibration constantly hammers on these seals, causing them to deform, wear out, and lose their elasticity much faster than they would in a smooth system. This leads to both internal and external leaks, reducing performance and requiring more frequent and costly rebuilds.
Conclusion
Vibration is a system killer, not a minor annoyance. Listening to your machine and addressing the root causes of vibration protects your investment, ensures operational safety, and prevents costly failures.
FAQ
What are hydraulic system vibrations?
Hydraulic system vibrations are oscillations that occur within hydraulic systems due to various factors such as component design, operational conditions, or external forces.
What causes vibrations in hydraulic systems?
Vibrations can be caused by design flaws, operational factors like fluid dynamics and load changes, and environmental influences such as temperature variations.
How can vibrations impact hydraulic systems?
Excessive vibrations can lead to mechanical damage, increased safety risks, and reduced operational efficiency, ultimately resulting in higher maintenance costs.
What are the types of vibrations in hydraulic systems?
The main types include natural frequencies, forced vibrations from external forces, and resonance, which occurs when external forces match the system’s natural frequency.
How can vibrations be detected and monitored?
Vibrations can be detected using tools like accelerometers and vibration meters, along with regular inspections and maintenance practices to ensure system integrity.
What solutions exist to minimize vibrations?
Solutions include improving component design, using damping materials, conducting routine maintenance, and replacing worn components to mitigate vibration-related issues.