The two primary categories of seals used in hydraulic fittings are metal seals and soft seals. Metal seals, typically made from materials like stainless steel, are renowned for their durability and ability to endure extreme temperatures and pressures. In contrast, soft seals are crafted from elastomeric materials. These hydraulic fittings are designed to create a leak-tight seal with less torque, reducing the risk of damage during assembly.
Understanding Hydraulic Seals
A. Definition and Function of Hydraulic Seals
Hydraulic seals are critical components in hydraulic systems, designed to prevent fluid leakage and maintain system pressure. They act as barriers between different components, such as cylinders, pistons, and fittings, ensuring that hydraulic fluids remain contained within the system. The primary function of these seals is to create a tight, leak-proof connection that withstands the pressure and dynamics of the hydraulic system. Proper sealing is essential not only for the efficient operation of the system but also for safety, as leaks can lead to fluid loss, environmental hazards, and potential system failures.
Hydraulic seals must accommodate various factors, including temperature fluctuations, pressure changes, and chemical compatibility with the hydraulic fluid. They are designed to provide reliable performance under these conditions, preventing wear and prolonging the life of the hydraulic components they protect.
B. Importance of Sealing in Hydraulic Systems
The importance of sealing in hydraulic systems cannot be overstated. A well-sealed system ensures optimal performance and efficiency, as leaks can significantly impair hydraulic pressure and flow. This can lead to inadequate power transmission, slower response times, and increased wear on system components, ultimately affecting the reliability and longevity of the entire hydraulic system.
Moreover, effective sealing plays a crucial role in maintaining safety standards. Leaking fluids can create hazardous conditions, particularly in industrial settings where hydraulic systems are extensively used. Ensuring that seals are functioning correctly helps prevent accidents, spills, and contamination, thereby safeguarding both personnel and the environment.
In addition, the cost implications of leaks can be substantial. Fluid losses translate to increased operational costs, as the hydraulic system may require more frequent refills and maintenance. By investing in quality hydraulic seals, businesses can enhance their operational efficiency, reduce downtime, and lower maintenance expenses.
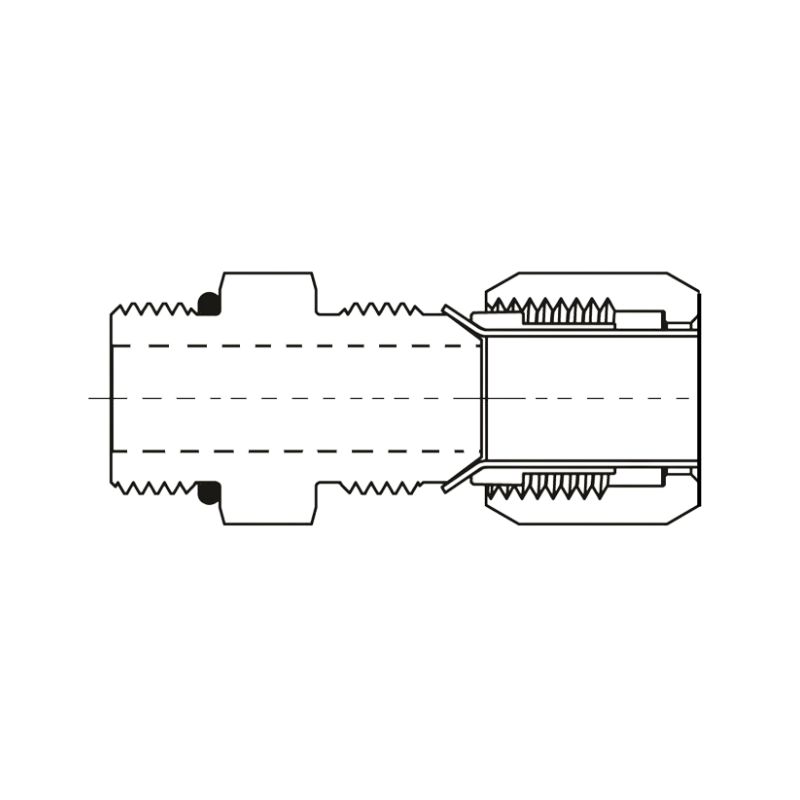
C. Types of Hydraulic Seals
Hydraulic seals can be broadly classified into two main types: metal seals and soft seals. Each type has unique characteristics, advantages, and applications, making it essential for users to understand their options.
Metal Seals:
Metal seals are typically made from durable materials such as stainless steel or other alloys. They are engineered to withstand extreme temperatures, high pressures, and a wide range of chemicals, making them ideal for demanding environments. The primary advantage of metal seals is their longevity and reliability under severe conditions. They do not deform easily, maintaining their integrity over time, which makes them suitable for critical applications.
However, metal seals can also present some challenges. Their installation often requires precise torque settings to ensure an effective seal, which can complicate assembly and increase the risk of damage if overtightened. Additionally, while they perform well in static applications, metal seals can struggle in dynamic scenarios where movement and vibration are prevalent, potentially leading to leaks.
Soft Seals:
Soft seals, on the other hand, are constructed from elastomeric materials such as rubber or polymer blends. These seals provide excellent sealing performance due to their ability to compress and conform to the mating surfaces, creating a tight seal that is less prone to leakage. Soft seals excel in applications with moderate temperature ranges and less aggressive chemicals, making them versatile for many hydraulic systems.
One of the key benefits of soft seals is their ease of installation. They typically require less torque to achieve a proper seal, which simplifies assembly and reduces the risk of damaging the fittings. Additionally, their flexible nature allows them to absorb vibrations and slight movements, enhancing the reliability of the connection.
However, soft seals may have limitations regarding temperature and chemical resistance compared to metal seals. Over time, exposure to harsh conditions can lead to wear and potential failure, making them less suitable for certain high-demand applications.
Metal Seals: Features and Benefits
A. Composition and Construction
Metal seals are engineered from a variety of robust materials, primarily stainless steel, and other high-performance alloys. The choice of material is crucial, as it determines the seal’s ability to withstand extreme environmental conditions. The construction of metal seals often involves precision machining to create a precise fit between the sealing surfaces. This machining process ensures that the seals can maintain tight tolerances, which is essential for preventing leaks in high-pressure applications.
Metal seals can come in several designs, including flat rings, O-rings, and C-rings, each tailored for specific applications. The design of a metal seal often includes features that enhance its sealing performance, such as grooves or ridges that facilitate better contact with the mating surfaces. Some metal seals also incorporate specialized coatings or surface treatments to improve their resistance to wear and corrosion, further enhancing their longevity.
B. Advantages of Metal Seals
Extreme Temperature Resistance
One of the most significant advantages of metal seals is their ability to withstand extreme temperatures. Unlike soft seals, which may degrade or lose elasticity at high temperatures, metal seals retain their integrity even in severe thermal environments. This makes them ideal for applications in industries such as aerospace, oil and gas, and heavy machinery, where equipment can be exposed to high temperatures during operation. Metal seals can typically operate in temperature ranges from cryogenic levels up to several hundred degrees Celsius, depending on the material used.
Compatibility with Various Chemicals
Metal seals are inherently resistant to many chemicals, making them suitable for use in environments where aggressive fluids are present. They do not swell, degrade, or react chemically as some elastomers might. This chemical compatibility is crucial in industries like pharmaceuticals, chemicals, and food processing, where maintaining the purity of the fluid and ensuring safety is paramount. The versatility of metal seals allows them to be used in a wide range of applications, from hydraulic systems to chemical processing equipment.
Longevity and Durability
The durability of metal seals is another significant advantage. They are designed to withstand repeated cycles of pressure and temperature without significant wear or failure. Unlike soft seals, which may wear out and require replacement over time, metal seals can offer a longer service life, reducing the frequency of maintenance and replacement. This longevity is particularly beneficial in applications where access to components is limited or where downtime for maintenance can be costly.
C. Limitations of Metal Seals
Risk of Deformation
Despite their durability, metal seals are not immune to risks. One of the primary concerns is deformation, especially in high-pressure applications. Over time, or with improper installation, metal seals can deform, leading to compromised sealing performance. This risk is particularly pronounced in applications involving thermal cycling, where expansion and contraction can affect the integrity of the seal. Deformation can result in leaks, which not only impact system performance but also pose safety hazards.
Installation Challenges
Installing metal seals can be more complex than their soft seal counterparts. Achieving the proper torque is critical for ensuring a leak-proof connection; however, this requires precise calibration and experience. Excessive torque can lead to deformation, while insufficient torque may fail to create an adequate seal. This installation challenge can result in increased labor costs and the need for specialized tools or techniques, particularly in environments where space is limited.
Maintenance Considerations
While metal seals are durable, they do require periodic inspections to ensure their integrity. Over time, even the best-engineered seals can show signs of wear, particularly in dynamic applications where movement is prevalent. Maintenance of metal seals often involves checking for signs of deformation, wear, or corrosion, which can add to operational costs. Moreover, when maintenance is required, the process may involve significant disassembly of surrounding components, leading to longer downtime.
Soft Seals: Features and Benefits
A. Composition and Construction
Soft seals are primarily constructed from elastomeric materials, which are polymers that exhibit both elasticity and flexibility. Common materials used for soft seals include nitrile rubber (NBR), fluorocarbon (FKM), ethylene propylene diene monomer (EPDM), and silicone. Each of these materials has unique properties that make them suitable for specific applications, particularly in hydraulic systems.
The construction of soft seals typically involves forming the elastomeric material into various shapes, such as O-rings, gaskets, and custom molded seals. This versatility allows soft seals to be adapted for a wide range of fitting configurations and applications. The manufacturing process may include techniques such as compression molding or injection molding to achieve precise dimensions and tolerances, ensuring a reliable fit within hydraulic assemblies.
Soft seals are designed to create a tight seal through compression. When a fitting is assembled, the elastomeric material is compressed between the surfaces of the components, filling any microscopic gaps and creating a barrier against fluid leakage. This compression-based sealing mechanism is what allows soft seals to provide effective leak prevention while accommodating slight movements or misalignments in the hydraulic system.
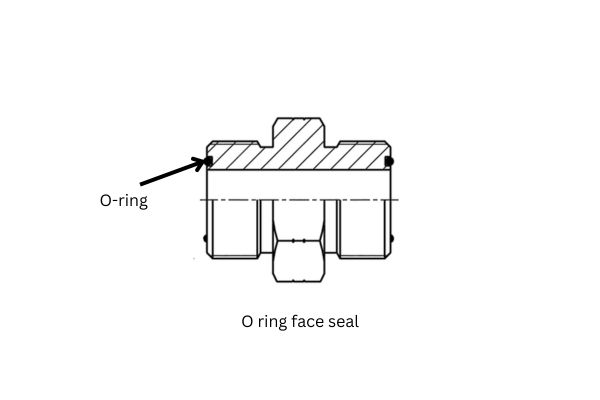
B. Advantages of Soft Seals
Soft seals offer several distinct advantages over traditional metal seals, making them an increasingly popular choice for a variety of hydraulic applications.
Improved Sealing Performance:
One of the most significant benefits of soft seals is their superior sealing performance. The elastomeric materials used in soft seals can deform slightly under pressure, ensuring that they fill any voids between mating surfaces. This characteristic allows them to create a leak-tight seal even in less-than-perfect conditions. Over time, soft seals maintain their effectiveness, reducing the likelihood of leaks due to material fatigue or deformation, which can occur with metal seals.
Easier Installation:
Soft seals are typically easier to install than their metal counterparts. The design of soft seals allows for lower installation torque, meaning that less force is required to achieve a secure seal. This not only speeds up the assembly process but also minimizes the risk of over-tightening, which can lead to damage of the fitting or the seal itself. As a result, technicians can install soft seal fittings quickly and confidently, reducing downtime in hydraulic system setups.
Greater Flexibility and Resilience:
The inherent elasticity of soft seals provides them with a degree of flexibility that is particularly advantageous in dynamic applications. Soft seals can absorb vibrations and minor misalignments between components, making them less prone to leaks caused by movement or thermal expansion. This resilience allows soft seals to maintain effective sealing performance even in environments where the hydraulic components may experience significant movement or stress.
C. Limitations of Soft Seals
Despite their numerous advantages, soft seals do have certain limitations that users should consider when selecting sealing solutions for their hydraulic systems.
Temperature and Chemical Limitations:
While soft seals can handle a wide range of temperatures, they are generally more limited in extreme environments compared to metal seals. Each elastomeric material has specific temperature thresholds; for instance, NBR typically operates well in temperatures ranging from -40°C to +100°C, while FKM can handle higher temperatures but may be less effective in certain chemical environments. Users must carefully evaluate the temperature and chemical compatibility of soft seals based on the fluids used in their systems to prevent degradation or failure.
Potential for Wear Over Time:
Although soft seals offer excellent sealing performance initially, they can be more susceptible to wear and degradation over time compared to metal seals. Exposure to aggressive chemicals, high temperatures, and constant movement can lead to material breakdown, resulting in reduced sealing effectiveness. Regular inspection and maintenance are essential to identify any signs of wear and to replace seals as needed to maintain system integrity.
Transitioning from Metal to Soft Seals
A. Steps for Transitioning
Transitioning from metal seals to soft seals in hydraulic systems involves a systematic approach to ensure compatibility and performance. The following steps can guide this process:
Assessment of Current Systems: Begin by evaluating the existing hydraulic system and identifying all components where metal seals are currently in use. This assessment should include a review of operating conditions, such as pressure, temperature, and the types of fluids handled.
Selecting Appropriate Soft Seals: Based on the assessment, select soft seals that are compatible with the existing fittings and suitable for the operational conditions. Consider factors such as material properties (e.g., NBR, FKM) and sealing configurations (e.g., O-rings, gaskets) to ensure optimal performance.
Testing and Validation: Before a full-scale implementation, conduct tests to validate the performance of soft seals in the existing system. This may involve installing a few soft seals in critical areas and monitoring their performance under actual operating conditions.
Full Implementation: Once testing is successful, proceed with the full implementation of soft seals across the hydraulic system, replacing metal seals with soft seals in all relevant applications.
B. Considerations and Best Practices During the Switch
When transitioning to soft seals, several considerations and best practices can help ensure a smooth process:
Compatibility Checks: Ensure that the selected soft seals are compatible with the existing hydraulic fittings and that they can withstand the chemical and temperature conditions of the application.
Installation Training: Provide training for technicians on the proper installation techniques for soft seals, emphasizing the importance of avoiding over-tightening and ensuring proper alignment during assembly.
Regular Monitoring: Implement a monitoring system to regularly check the performance of soft seals after installation. This can help identify any potential issues early and allow for timely maintenance or replacement.
Documentation: Maintain thorough documentation of the transition process, including specifications of the new seals, installation procedures, and performance monitoring results. This information can be invaluable for future maintenance and troubleshooting.
C. Potential Challenges and Solutions
Transitioning from metal to soft seals may present several challenges:
Performance Variability: Users may initially be concerned about the long-term performance of soft seals compared to metal seals. To mitigate this, conduct extensive testing and provide data on the reliability and lifespan of the selected soft seal materials.
Installation Errors: Improper installation can lead to leaks or seal failure. To address this, emphasize training and create clear guidelines for installation procedures. Consider utilizing visual aids or step-by-step manuals to assist technicians.
Material Degradation: Users may worry about the susceptibility of soft seals to wear and degradation. Choose high-quality materials that are well-suited for the specific application and emphasize the importance of regular maintenance checks to identify wear before it affects system performance.
Conclusion
Each application may necessitate a different approach, and the choice between metal and soft seals should be based on a thorough evaluation of the pros and cons of each option. By prioritizing reliable sealing performance, ease of installation, and long-term maintenance needs, engineers and technicians can optimize their hydraulic systems for enhanced efficiency and safety.
FAQ
What are hydraulic seals?
Hydraulic seals are components that prevent fluid leakage in hydraulic systems, ensuring efficient operation and protecting against contaminants.
What is the difference between metal seals and soft seals?
Metal seals are durable and suited for extreme conditions, while soft seals, made from elastomeric materials, offer better sealing performance and ease of installation.
What are the advantages of using soft seals?
Soft seals provide improved sealing capabilities, are easier to install, and offer greater flexibility and resilience under dynamic conditions.
Are there any limitations to soft seals?
Yes, soft seals can have temperature and chemical limitations and may wear over time, especially in harsh environments.
How can I transition from metal to soft seals?
Assess your current system, select compatible soft seals, conduct tests, and train technicians on proper installation techniques for a smooth transition.
When should I consider using soft seals in my hydraulic applications?
Consider soft seals for applications requiring reliable sealing performance, ease of installation, and flexibility, particularly in environments with vibrations or movements.