Hydraulic fitting system noise refers to the undesirable sounds produced during the operation of hydraulic systems, primarily generated by the movement of fluids through various components. This noise can manifest as both audible and inaudible waves, originating from mechanical sources such as pumps, valves, and fittings.
Understanding Hydraulic Systems
A. Basic Components of Hydraulic Systems
Hydraulic systems are essential in various applications, from industrial machinery to automotive systems, utilizing pressurized fluid to transmit power. The primary components of hydraulic systems include:
Pumps: These are the heart of hydraulic systems, responsible for converting mechanical energy into hydraulic energy by moving fluid from the reservoir into the system. Common types include gear pumps, piston pumps, and vane pumps, each designed for specific flow and pressure requirements.
Valves: Valves control the flow and direction of hydraulic fluid within the system. They can regulate pressure, manage flow rates, and direct fluid to different components. Types of valves include check valves, relief valves, and directional control valves.
Hoses: Flexible hoses transport hydraulic fluid between components. They must withstand high pressures and varying temperatures, and their design can significantly affect the system’s performance and noise levels.
Cylinders: Hydraulic cylinders convert hydraulic energy into linear mechanical energy. They consist of a cylinder barrel, piston, and rod, and they facilitate the movement of loads through the controlled application of hydraulic pressure.
Fittings: These small but critical components connect hoses, tubes, and other elements of the hydraulic system. They ensure leak-free connections and play a significant role in maintaining system integrity and performance.
Together, these components work synergistically to create a functioning hydraulic system capable of performing a wide range of tasks efficiently.
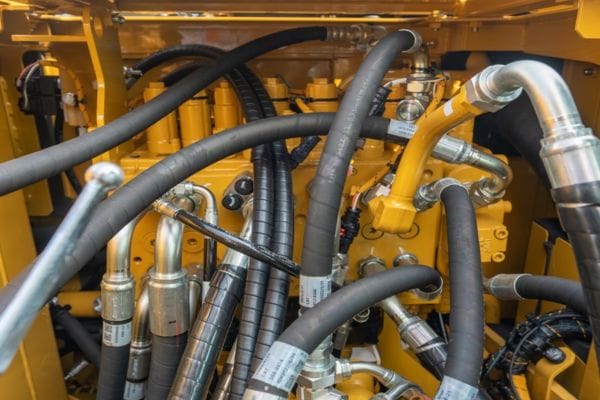
B. Functionality of Hydraulic Fittings
Hydraulic fittings serve as the connectors that link various components within the hydraulic system, ensuring the efficient flow of hydraulic fluid. Their functionality includes:
Sealing Connections: Fittings must provide a secure and leak-proof seal to prevent fluid loss and maintain system pressure. This is crucial for both performance and safety, as leaks can lead to system failures and environmental hazards.
Adapting Different Sizes: Fittings often adapt hoses and pipes of different diameters, allowing for flexibility in system design and maintenance. This adaptability is essential in retrofitting existing systems or integrating new components.
Supporting Fluid Dynamics: The design and orientation of fittings can influence fluid flow patterns. Sharp bends or poorly designed fittings can create turbulence, leading to increased noise and energy loss within the system. Therefore, selecting the right fittings is vital for optimizing performance and reducing noise.
Hydraulic fittings not only facilitate connections but also play a significant role in ensuring the overall efficiency and reliability of hydraulic systems.
C. Overview of Noise Generation in Hydraulics
Noise generation in hydraulic systems is a multifaceted issue that can arise from various sources. Understanding these sources is essential for effectively managing and mitigating noise. Key factors contributing to noise generation include:
Fluid Dynamics: As fluid flows through pumps, valves, and fittings, changes in velocity and direction can create turbulence. This turbulence leads to pressure fluctuations, which manifest as audible noise.
Mechanical Operations: The operation of pumps and other components generates mechanical noise. For instance, cavitation—occurring when vapor bubbles form and collapse within a pump—can produce loud, damaging sounds that affect system performance.
Resonance and Vibration: Each component of a hydraulic system has a natural frequency. When operational frequencies approach these natural frequencies, resonance can occur, amplifying vibrations and resulting in increased noise levels. Components such as steel tubes and hoses are particularly susceptible to vibration transmission.
External Influences: Environmental factors, such as nearby machinery or background noise, can exacerbate the perception of hydraulic noise. Additionally, poor installation or maintenance practices can increase noise levels due to misalignment or wear.
Causes of Noise in Hydraulic Fitting Systems
A. Mechanical Sources of Noise
Pump Operations
Pumps are integral to hydraulic systems, and their operations can be significant sources of noise. Several phenomena contribute to this:
Cavitation: This occurs when the pressure in the pump drops below the vapor pressure of the fluid, leading to the formation of vapor bubbles. When these bubbles collapse, they create shock waves that produce loud, damaging noises. Cavitation not only generates noise but also causes severe wear on pump components, reducing their lifespan and efficiency.
Turbulence: As hydraulic fluid is forced through the pump, changes in flow velocity can create turbulence. This chaotic fluid motion generates sound waves, contributing to the overall noise in the system. Turbulent flow can also increase energy losses, making the system less efficient.
Vibration: Pumps inherently generate vibrations during operation due to moving parts. If not properly mounted or isolated, these vibrations can transmit through the system, amplifying noise levels. Additionally, mechanical imbalances or misalignments can exacerbate this issue, leading to higher levels of vibration and associated noise.
Fluid Pulsations
Fluid pulsations are another critical contributor to noise in hydraulic systems. These pulsations can arise from various sources, including:
Pressure Variations: When fluid is pumped, pressure changes can create fluctuations in flow rates. These variations lead to pulsating flow, which generates sound waves as the fluid moves through the system. The frequency and intensity of these pulsations can vary based on the pump type and operating conditions.
Impact on Components: Pulsating fluid can cause vibrations in hoses, fittings, and valves, leading to additional noise. This impact can create a feedback loop, where increased noise results in greater component wear, further enhancing noise production.
Understanding the dynamics of fluid pulsations is essential for noise management, as they can significantly influence the overall acoustic environment of hydraulic systems.
B. Turbulence and Flow Changes
Hydraulic fittings play a crucial role in managing fluid flow within the system. Their design and placement can significantly affect noise generation through turbulence and flow changes:
Flow Velocity Changes: As fluid passes through fittings, any abrupt changes in diameter or direction can cause increased turbulence. This turbulence not only generates noise but can also lead to pressure drops and energy losses, negatively impacting system efficiency.
Types of Fittings: Different types of fittings, such as elbows, tees, and adapters, have varying impacts on flow dynamics. Sharp bends or poorly designed fittings can create areas of low pressure, further exacerbating turbulence and noise levels. Optimizing fitting design and placement is critical for minimizing noise.
Effect of Hose Length and Routing: The length and routing of hoses connecting fittings can also influence noise. Longer hoses may lead to increased fluid friction, while improper routing can cause bends and kinks that disrupt smooth fluid flow, generating noise.
By addressing turbulence and optimizing flow changes, hydraulic system designers can significantly reduce noise levels, leading to improved overall performance.
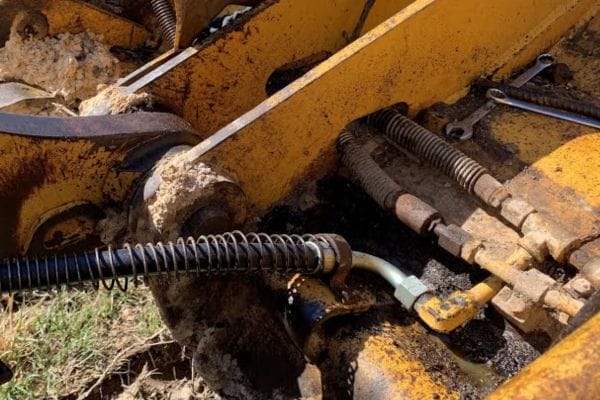
C. External Factors
Several external factors can exacerbate noise levels in hydraulic systems, impacting both performance and operator comfort:
Environmental Noise: Hydraulic systems are often installed in noisy environments, where external sounds can compound the noise generated internally. This background noise can make it challenging to identify and address specific issues within the hydraulic system, leading to a more significant overall noise burden.
Operator-Induced Factors: The actions of operators can influence noise levels as well. For instance, improper operation, such as rapidly changing flow rates or aggressive control of valves, can lead to increased turbulence and noise. Training operators on best practices can help mitigate these issues.
System Layout: The physical layout of the hydraulic system can also impact noise transmission. Systems with inadequate support or those poorly mounted can vibrate excessively, leading to increased noise levels. Moreover, proximity to other machinery can result in noise amplification and transmission, further complicating noise management.
Implications of Hydraulic System Noise
A. Impact on System Efficiency
Noise in hydraulic systems often correlates with energy losses. When pumps, fittings, or hoses produce excessive noise, it usually indicates inefficiencies such as turbulence, fluid resistance, or pressure drops, which consume additional energy. For instance, turbulence and fluid pulsations caused by improperly chosen fittings can result in pressure loss, requiring more power to achieve the desired output. This increased energy demand not only raises operational costs but also reduces the overall efficiency of the system, leading to a higher total cost of ownership over time. Recognizing and addressing these sources of noise can improve system performance and energy efficiency.
B. Effects on Component Longevity
Noise is often a sign of mechanical stress within the hydraulic system. Persistent vibrations and pressure fluctuations place additional strain on components like pumps, valves, and fittings, accelerating wear and leading to premature failure. For example, cavitation within pumps—a common noise source—can severely damage internal components, reducing their lifespan and requiring frequent replacements. Similarly, fittings subjected to high vibrations and fluid pulsations may experience fatigue, leading to cracks or leaks. Over time, addressing noise issues can enhance the durability of components, thereby extending the system’s operational lifespan and reducing maintenance costs.
C. Operator Health and Safety
High noise levels pose significant health risks to operators, including noise-induced hearing loss (NIHL) and fatigue. Prolonged exposure to noise above 85 decibels can result in permanent hearing damage, with hydraulic systems often reaching or exceeding this threshold. Noise can also contribute to physical and mental fatigue, reducing operators’ ability to concentrate, which may lead to errors or accidents. By managing noise levels, companies can create a safer, more comfortable work environment, ultimately promoting worker health and reducing the likelihood of occupational hazards associated with prolonged exposure to loud hydraulic systems.
Strategies for Noise Reduction
A. Design Considerations
Effective noise reduction in hydraulic systems begins with thoughtful design. Incorporating noise mitigation strategies from the outset can lead to significant long-term benefits. Key design considerations include:
Component Placement: Positioning pumps, valves, and other components strategically can minimize the transmission of noise throughout the system. For example, isolating pumps from the main structure using vibration-dampening mounts can help reduce noise levels significantly.
Fluid Path Design: A well-planned fluid path with smooth transitions and minimal bends can reduce turbulence and pressure drops. Designing fluid circuits with gradual changes in diameter or using sweeping bends instead of sharp elbows can help maintain laminar flow, thereby reducing noise generation.
Material Selection: Using materials that absorb sound rather than transmit it can effectively mitigate noise. For instance, composite materials or rubber can dampen vibrations compared to traditional metal components.
By prioritizing noise reduction in the design phase, engineers can create hydraulic systems that operate quietly and efficiently, reducing the need for retroactive modifications.
B. Use of Attenuators and Dampers
Attenuators and dampers are specialized devices designed to minimize noise in hydraulic systems. Their effective implementation can lead to substantial noise reduction:
Attenuators: These devices are specifically designed to reduce the amplitude of sound waves. They work by absorbing and dissipating sound energy, making them particularly useful in areas with high noise generation, such as near pumps and valves. Attenuators can be tuned to specific frequencies, effectively canceling out unwanted noise while allowing desired sounds to pass through.
Dampers: Dampers are installed to absorb vibrations and prevent them from propagating through the hydraulic system. They can be applied to hoses, fittings, and even mounting points of pumps and motors. By using dampers, the energy from vibrations can be absorbed before it leads to increased noise levels, enhancing overall system performance and operator comfort.
Both attenuators and dampers require careful selection based on the specific noise characteristics of the hydraulic system. Properly integrating these devices can lead to a quieter working environment and improved operational efficiency.
C. Selecting the Right Fittings and Hoses
The choice of hydraulic fittings and hoses plays a critical role in managing noise in hydraulic systems. Specific recommendations include:
Smooth Bore Hoses: Selecting hoses with a smooth interior surface can significantly reduce turbulence and fluid pulsations. Hoses designed for high flow rates can help minimize pressure drops and associated noise generation.
Fiber-Reinforced Hoses: These hoses offer flexibility while maintaining high strength, which helps reduce noise generated from vibration. Their design allows for a degree of volumetric expansion, acting similarly to an accumulator, which can dampen pressure fluctuations.
Proper Fitting Design: Choosing fittings that provide gradual transitions and minimize sharp angles can reduce turbulence and subsequent noise. Look for fittings designed specifically for low-noise applications, as these often incorporate features that promote smooth fluid flow.
Regular Maintenance: Regularly inspecting and maintaining fittings and hoses ensures they remain in optimal condition, preventing wear that can lead to increased noise levels. Tightening connections and replacing worn components can help maintain system integrity and reduce noise.
Conclusion
We encourage you to take a proactive approach in evaluating their hydraulic systems for noise issues. Assess the current noise levels and identify potential sources, implementing effective strategies for reduction. Consider investing in the right fittings, hoses, and vibration-dampening technologies, and emphasize design practices that prioritize noise mitigation.
FAQ
What causes noise in hydraulic systems?
Noise in hydraulic systems is primarily caused by mechanical operations of pumps, fluid pulsations, turbulence from fittings, and external factors like environmental noise.
Why is it important to reduce noise in hydraulic systems?
Reducing noise is crucial for improving system efficiency, extending component lifespan, ensuring operator safety, and complying with regulatory standards.
What are some common strategies for noise reduction?
Strategies include optimizing system design, using attenuators and dampers, selecting smooth bore and fiber-reinforced hoses, and choosing fittings that minimize turbulence.
How can high noise levels affect operators?
Prolonged exposure to high noise levels can lead to noise-induced hearing loss, fatigue, reduced concentration, and increased risk of accidents.
What are the regulatory noise limits for workplaces?
OSHA guidelines state that noise exposure should not exceed 85 dB(A) over an eight-hour workday to prevent hearing damage.
How can I evaluate my hydraulic system for noise issues?
Conduct regular inspections to measure noise levels, identify sources of noise, and assess the condition of components like pumps, hoses, and fittings.