Air contamination refers to the presence of air in the hydraulic fluid, which can take the form of entrained, dissolved, or free air within a hydraulic system. Hydraulic systems are designed to operate using a fluid that is both stable and sealed from external contaminants.
Understanding Air Contamination
What is Air Contamination?
Air contamination in systems refers to the presence of air in the hydraulic fluid, which can adversely affect the operation and performance of the system. In a hydraulic system, the hydraulic fluid is essential for transmitting power, lubricating components, and maintaining temperature control. When air is introduced into the fluid, it disrupts these functions and leads to inefficiencies and potential damage to key system components.
The contamination of the fluid with air can take several forms, including air trapped in bubbles, dissolved air molecules, or free air as a separate phase within the system. Each type of air contamination can cause different issues and may require different diagnostic and treatment methods to resolve.
Difference Between Entrained and Dissolved Air
There are two main types of air contamination: entrained air and dissolved air.
Entrained Air: This refers to air that is mechanically mixed into the fluid, forming visible bubbles. These bubbles are trapped within the fluid and move with it through the system. Entrained air can form when fluid levels drop when pumps operate at high speeds, or when there is cavitation in the pump. The air pockets formed can lead to a decrease in the fluid’s efficiency, as the bubbles reduce the ability of the fluid to carry pressure effectively. In some cases, these air bubbles can cause foaming, which leads to erratic pump performance and uneven fluid flow.
Dissolved Air: Unlike entrained air, dissolved air is a form of air that is dissolved in the hydraulic fluid at a molecular level. This type of contamination is not visually noticeable and does not cause immediate effects. However, when dissolved air is released from the fluid, it can lead to the formation of entrained air bubbles or foam, especially when the fluid experiences a pressure drop. Dissolved air is commonly introduced through temperature fluctuations, inadequate filtration, or through the introduction of moisture into the fluid.
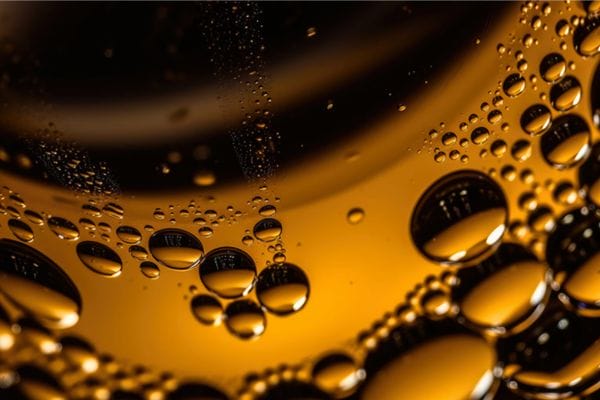
Types of Air Contamination
There are three primary forms of air contamination in hydraulic systems: entrained air, dissolved air, and free air.
Entrained Air: As described earlier, this is air that is mixed with the fluid, forming bubbles that are carried throughout the system. Entrained air is often the most visible and easiest to diagnose. It can cause immediate operational problems like pump cavitation, fluid instability, and noise.
Dissolved Air: This is air that is dissolved within the fluid at a microscopic level. It typically occurs under conditions of high pressure or low temperature, where the air remains dissolved in the fluid. However, when the system pressure decreases or the fluid temperature increases, the dissolved air may come out of solution, leading to entrained air and foam formation. This can significantly affect the system’s performance.
Free Air: Free air refers to air that enters the system as a separate phase, existing independently of the hydraulic fluid. This form of contamination can occur when the system is improperly sealed or when connections are loose. Free air is often the result of severe leaks, and it can lead to large, visible air pockets that disrupt the fluid flow and cause irregular system behavior.
How Air Gets Into Hydraulic Systems
There are several common causes of air ingress into hydraulic systems:
Faulty Seals and Gaskets: One of the most common ways air enters a hydraulic system is through damaged or worn-out seals and gaskets. As seals degrade over time, they may fail to maintain a tight seal, allowing air to seep into the system. This can occur at various connection points, including at the reservoir cap, pump seals, and valve connections.
Pump Cavitation: Cavitation occurs when the hydraulic pump operates at pressures below the vapor pressure of the fluid, causing localized bubbles to form. When these bubbles collapse near high-pressure areas, they can cause damage to the pump and other components. The bubbles also introduce air into the system, which further exacerbates the issue.
Leaking Connections: Leaks in the hydraulic lines, fittings, or connections can allow air to enter the system. Even small leaks that seem inconsequential can introduce enough air to cause problems, particularly if the leaks are continuous over time.
Environmental Factors: Environmental conditions, such as high humidity or exposure to dust and debris, can also contribute to air contamination. High humidity, for example, can lead to the absorption of moisture into the hydraulic fluid, which in turn can facilitate the introduction of air.
Low Fluid Levels: When the hydraulic fluid level drops too low, the pump may draw in air, leading to cavitation and the introduction of air into the system. Inadequate fluid levels can also cause an increase in air turbulence, which leads to entrained air.
Symptoms of Air Contamination in Hydraulic Systems
Air contamination in hydraulic systems can manifest in several ways, and recognizing these symptoms is essential for early detection and prevention of more serious problems. Understanding the visual, auditory, and operational indicators of air contamination can help operators and maintenance personnel identify the issue before it leads to significant damage or costly downtime.
Visual Indicators
Foam and Bubbles in the Reservoir
One of the most obvious signs of air contamination is the presence of foam or bubbles in the hydraulic fluid. When air is trapped in the fluid, it can create foam or visible bubbles within the reservoir. This is especially noticeable when the system operates and the fluid moves. Foam formation typically occurs when air is entrained in the fluid, either due to cavitation or from leaks and inadequate sealing in the system. Foam in the reservoir reduces the fluid’s ability to transmit force efficiently and can cause unstable fluid levels in the system, which may lead to pump starvation or cavitation.
Foam can also be an indication of poor fluid quality, such as a high moisture content or excessive contaminants. The presence of foam indicates that the fluid is no longer performing as intended, which can negatively impact the efficiency of the entire hydraulic system.
Discoloration of Hydraulic Fluid
Air contamination, particularly when accompanied by other contaminants like water or dirt, can cause discoloration in hydraulic fluid. Normal hydraulic fluid is typically clear, amber, or red, depending on the fluid type. However, air bubbles, oxidation, and other contaminants can cause the fluid to darken or take on a cloudy appearance. Discoloration may also signal the degradation of the fluid’s chemical properties due to excessive heat or moisture. In severe cases, the fluid may turn milky or have a greyish tint, which is an indication that air has been dissolved or entrained in large quantities.
Auditory Signs
Unusual Noise or Cavitation Sounds from Pumps and Valves
One of the most noticeable auditory symptoms of air contamination is abnormal noise, particularly from pumps and valves. When air is present in the fluid, cavitation can occur as the air bubbles collapse under high-pressure conditions. This process produces distinct noise, often described as a “gravel” or “marble” sound. Cavitation noises are typically caused by trapped air in the fluid that forms bubbles under low-pressure conditions, which then collapse when exposed to higher pressures within the pump or valve. These collapsing bubbles create micro-implosions that not only cause noise but can also damage sensitive components.
Additionally, the presence of air in the system can lead to erratic valve operation, which may cause a “squealing” or “whistling” sound as valves struggle to maintain control of the fluid flow.
Decreased Performance or Sluggish Response from Actuators
Air contamination often results in the sluggish operation of hydraulic actuators, such as cylinders and motors. When air is present, the fluid cannot maintain consistent pressure, causing a delay in actuator response time. This can manifest as slow movement, inconsistent speed, or failure to reach the desired position or force. In systems requiring precise control, air contamination can severely impact performance, leading to poor operational outcomes and compromised productivity.
Sluggish actuator performance can also be a result of the reduced lubrication properties of the hydraulic fluid when air contamination is present. This can cause additional wear on seals and moving parts, further exacerbating the issue.
Operational Issues
Erratic Operation of Hydraulic Machinery
Air contamination affects the fluid’s ability to maintain consistent pressure and flow, resulting in erratic behavior in the hydraulic machinery. The system may experience sudden changes in pressure or fluid flow that lead to unpredictable operation of pumps, motors, and cylinders. These irregularities can cause machinery to function intermittently or unpredictably, creating an unsafe work environment. Hydraulic systems with air contamination may exhibit fluctuating or unstable performance, making it difficult to maintain precise control over machinery.
Increased System Temperature Due to Inefficient Fluid Flow
Another common symptom of air contamination is an increase in system temperature. Air in the fluid reduces the overall efficiency of the fluid’s movement through the system, causing more friction and turbulence in the hydraulic components. This increased friction generates heat, which can raise the system’s operating temperature. High temperatures further degrade the hydraulic fluid and accelerate wear on components, leading to additional issues such as seal failure or valve sticking. Monitoring system temperature is a key diagnostic tool for identifying air contamination.
If the system temperature exceeds normal operating levels, it is often an indication that the fluid is not flowing optimally due to the presence of air or other contaminants.
Pressure Fluctuations
Pressure fluctuations are a common symptom of air contamination, as the presence of air in the hydraulic fluid causes instability in pressure readings. Air pockets compress and expand under varying load conditions, leading to erratic pressure levels within the system. This fluctuation can cause inaccurate readings on pressure gauges and cause the system to function inefficiently. Consistent pressure is critical in hydraulic systems for maintaining proper fluid flow and smooth operation. Any deviation from the expected pressure can lead to suboptimal performance and cause the system to fail under load conditions.
Methods to Diagnose Air Contamination
Visual Inspection
Visual inspection is one of the simplest and most accessible methods for diagnosing air contamination in a hydraulic system. By carefully observing the hydraulic system and its components, operators can spot several visual indicators that point to the presence of air in the fluid.
Using Sight Glasses, Reservoirs, and Hydraulic Fluid Samples to Spot Foam and Bubbles
A sight glass or fluid level gauge is typically installed on the hydraulic reservoir to provide a clear view of the fluid’s condition. Operators can use these tools to look for visible signs of foam or bubbles in the fluid. Foam, especially excessive foam, is a clear indicator of air contamination, as it is caused by entrained air in the fluid. Small bubbles may be seen as the fluid moves through the reservoir, and larger foam formations can be indicative of severe air infiltration. In some cases, the foam may result in unstable fluid levels, contributing to system inefficiencies.
Additionally, taking fluid samples and examining them under controlled conditions can help detect air contamination. When the sample is placed in a clear container and allowed to settle, the air bubbles will rise to the top, leaving behind a more concentrated, denser fluid at the bottom. This can be a strong indicator of entrained air.
Checking for Visible Leaks that May Indicate Air Ingress
Hydraulic systems are sealed environments, and any leak in the system can provide a pathway for air to enter. A visual inspection of all seals, fittings, and connections for visible signs of leaks is essential. Leaks near high-pressure areas, such as around the pump, valves, or reservoir caps, should be addressed promptly. Often, small leaks may not cause immediate fluid loss, but they can continuously allow air to enter the system, leading to air contamination over time.
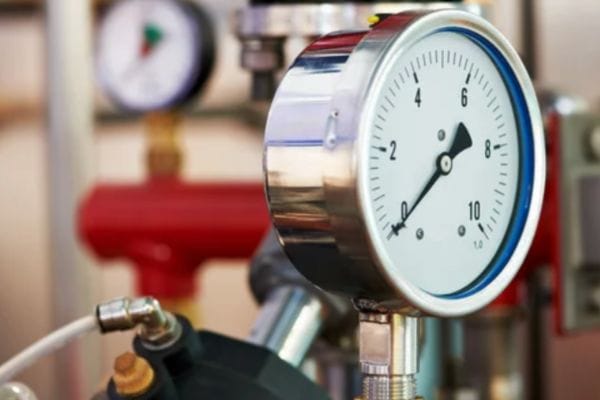
Pressure Testing
Pressure testing is another diagnostic method that can help detect air contamination. The presence of air in the hydraulic fluid can lead to variations in pressure, which can be identified using pressure gauges.
Using Pressure Gauges to Monitor Pressure Variations
Monitoring the system’s pressure using accurate pressure gauges is an essential diagnostic tool. Under normal operating conditions, a hydraulic system should maintain a steady and predictable pressure throughout its cycles. If air is present in the fluid, it can cause inconsistent or fluctuating pressure levels due to the compressibility of air bubbles. This variation in pressure may be visible on the pressure gauge, especially during load changes, acceleration, or deceleration of system components.
The operator should watch for erratic pressure readings that drop suddenly or fluctuate in an unpredictable pattern, which may suggest that air pockets are being compressed and released within the system. Air contamination typically leads to a loss of system pressure when the air bubbles escape, contributing to pressure drops that can be detected.
Identifying Abnormal Pressure Drops as an Indicator of Air in the System
Abnormal pressure drops, especially during steady-state operations, can indicate air in the system. A sudden pressure drop can occur when air bubbles collapse or shift in the system, which affects the hydraulic fluid’s ability to transfer power. This pressure drop can lead to cavitation, poor performance, and erratic operation of hydraulic machinery. Pressure testing under different load conditions can help confirm the presence of air and assist in pinpointing areas of potential contamination.
Flow and Temperature Monitoring
Flow and temperature monitoring are essential tools for diagnosing air contamination, as the presence of air directly impacts the fluid flow and the system’s thermal performance.
Using Flow Meters to Assess System Flow Consistency
A flow meter is a useful device for monitoring the consistency and stability of the fluid flow through the hydraulic system. If air is present in the fluid, it can cause turbulence, irregular fluid flow, and inconsistent performance. A sudden fluctuation in the flow rate or uneven flow patterns are signs that air is disturbing the flow of the fluid.
Flow monitoring is particularly helpful in identifying variations in flow during specific operations, such as during start-up, acceleration, or under varying load conditions. If air contamination is significant, it will show up as a fluctuation in the measured flow, as air pockets disrupt the continuous motion of the fluid.
Temperature Measurement and Correlation to Signs of Contamination
Elevated temperatures can also be indicative of air contamination in the system. Air reduces the fluid’s ability to transfer heat, as the bubbles in the fluid can cause localized hot spots due to increased friction and turbulence. As the system compensates for the reduced thermal efficiency, the operating temperature can rise.
Operators should use temperature sensors to monitor the system’s operating temperature. If temperatures rise beyond normal levels, it may be a sign that air is causing inefficiencies in the system. By correlating temperature increases with the presence of foam or bubbles, technicians can further confirm air contamination.
Hydraulic Fluid Sampling
Hydraulic fluid sampling is a diagnostic technique that involves taking fluid samples and sending them to a laboratory for detailed analysis. Lab analysis can provide valuable insights into the air content in the fluid, helping to determine the extent of air contamination and its impact on the system.
Lab Analysis of Hydraulic Fluid for Air Content
Fluid samples can be analyzed in the lab to assess the amount of dissolved, entrained, and free air in the hydraulic fluid. High-quality fluid analysis can identify air contamination levels, even in cases where visual inspection might not reveal a problem. Laboratory tests can measure the dissolved air content, which is crucial for understanding how much air is affecting fluid performance and whether the contamination is severe enough to warrant intervention.
Use of Aeration Meters to Quantify Dissolved and Entrained Air
Aeration meters are specialized devices that measure the aeration (air content) in hydraulic fluid. These meters can quantify both dissolved and entrained air. Aeration meters work by measuring changes in the fluid’s characteristics as it moves through the system, with a particular focus on detecting the presence of bubbles or foam. This type of monitoring is especially useful for identifying early-stage contamination, as it provides numerical data on air content levels, allowing for more precise diagnosis.
Solutions to Prevent and Treat Air Contamination
Preventive Measures
Sealing Systems and Improving Air-Tightness of Reservoirs
The primary source of air contamination is often the ingress of air through leaks in the system. Ensuring that all seals and gaskets are in good condition and properly installed can significantly reduce the amount of air entering the hydraulic fluid. Seals around the reservoir, pumps, valves, and connectors should be checked regularly for wear or degradation. Properly fitted seals ensure that air is prevented from entering the system under normal operational conditions.
Additionally, maintaining the air-tightness of hydraulic reservoirs is critical. Reservoirs that are not sealed correctly or are exposed to fluctuations in external pressure can allow air to enter, leading to air contamination. Regular checks and prompt maintenance of reservoir seals can help ensure that air ingress is minimized.
Ensuring Proper Fluid Levels and Quality
Maintaining proper fluid levels is a crucial preventive measure. Low fluid levels can expose the hydraulic pump to air, especially during system start-up or when the fluid drops below the minimum operating threshold. This can cause cavitation, which leads to air contamination in the system. Operators should regularly monitor fluid levels to ensure they are within recommended ranges.
Fluid quality is another key factor in preventing air contamination. Over time, hydraulic fluid can degrade due to exposure to heat, moisture, or other contaminants. Using high-quality fluid and replacing it at regular intervals can help maintain system efficiency and prevent air from becoming entrained in the fluid. Fluid contamination sensors and regular oil analysis can help detect any changes in fluid quality early, allowing for proactive measures.
Using Breathers and Air Filtration Systems
Air contamination can often enter the system through the reservoir vents. Installing breathers or vent caps with built-in filtration systems can help prevent contaminants from entering the fluid. These devices allow the system to breathe without allowing outside air, moisture, or debris into the hydraulic fluid.
Air filtration systems are particularly important for reservoirs in systems that operate in environments prone to dust, humidity, or other contaminants. These systems ensure that air entering the reservoir is filtered of particles and moisture, thus reducing the risk of contamination. It is crucial to regularly check and replace air filters to ensure they are functioning effectively.
Regular System Maintenance and Inspections
A comprehensive preventive maintenance program is essential to identifying and addressing potential sources of air contamination. Operators should perform routine checks of hydraulic components such as pumps, valves, hoses, and connections to ensure they are properly sealed and free from wear or damage. A proactive maintenance schedule that includes regular inspections, cleaning, and part replacements can prevent leaks and other issues that contribute to air ingress.
Inspections should also include monitoring system pressure and fluid temperature, as sudden drops in pressure or rising temperatures can signal the presence of air contamination. Identifying potential problems early can help to prevent more significant damage to the hydraulic system and components.
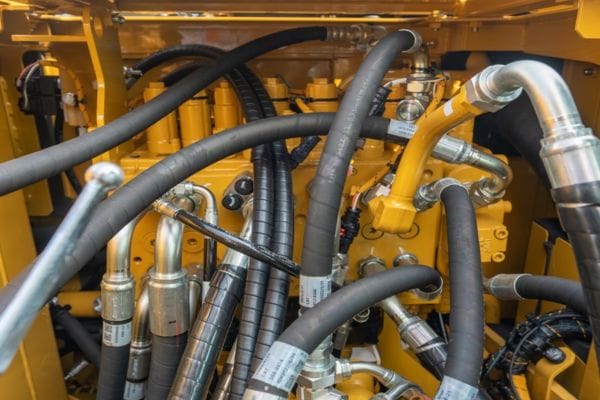
Treatment Options
De-Aeration Methods: Using Air Separators and Degassing Systems
Once air contamination has been detected, several treatment options are available to remove air from the hydraulic system. Air separators are commonly used to remove large volumes of entrained air in the system. These devices work by allowing the fluid to flow through a chamber where the air bubbles rise to the surface and are separated from the fluid. The separated air is then vented out of the system, leaving behind a cleaner, more consistent hydraulic fluid.
In addition to air separators, degassing systems are also effective in removing dissolved air from hydraulic fluid. Degassing systems typically use vacuum chambers or other low-pressure environments to reduce the pressure on the hydraulic fluid, causing dissolved air to come out of solution and be vented. These systems are particularly useful when dealing with low levels of dissolved air that may not be as noticeable through visual inspection but still affect system performance.
How to Address Faulty Pumps or Seals Causing Air Ingress
Faulty pumps or seals can be major sources of air contamination in hydraulic systems. Air can enter the system through failing seals, especially in high-pressure areas such as around the pump or valve blocks. Inspecting and replacing damaged seals is essential for maintaining the integrity of the system. In some cases, pumps may also have internal wear or cavitation issues that lead to air ingestion. Regular pump maintenance, including checking for internal damage and ensuring proper suction, can reduce the risk of air contamination.
If a pump is identified as the source of air ingress, it may need to be repaired or replaced. Pumps that are designed to handle high-pressure conditions should be maintained to avoid cavitation, which causes the formation of air bubbles. Cavitation occurs when the pressure within the pump drops below the vapor pressure of the fluid, causing the fluid to vaporize and form bubbles. These bubbles can then be carried through the system, leading to air contamination.
Fluid Conditioning and Filtration to Remove Dissolved Air
Fluid conditioning and filtration are essential for maintaining hydraulic fluid quality and preventing the buildup of dissolved air. Fluid conditioners can be used to improve the overall quality of the hydraulic fluid by reducing the presence of moisture, particles, and other contaminants that can contribute to air contamination. These systems typically include filtration, dewatering, and conditioning elements that help restore the fluid to optimal performance levels.
Installing high-efficiency filters and conditioning systems is another key step in addressing dissolved air. Filters specifically designed to remove small air bubbles from the fluid can help reduce the levels of dissolved air in the system. These filters work by trapping the air particles and allowing the fluid to pass through, which can significantly improve fluid stability and prevent air-related issues in the hydraulic system.
Conclusion
Businesses and operators need to be proactive in diagnosing air contamination by conducting regular system checks. Implementing routine inspections and monitoring can prevent air contamination from becoming a hidden issue that disrupts system performance. Proactive maintenance and advanced diagnostics are the keys to ensuring the health and longevity of any hydraulic system.
FAQ
What causes air contamination in hydraulic systems?
Air contamination in hydraulic systems can be caused by leaks in seals, faulty pumps, cavitation, or improper fluid levels.
How can I tell if my hydraulic system has air contamination?
Signs of air contamination include foam or bubbles in the reservoir, unusual noises from pumps, erratic system performance, and increased pressure fluctuations.
What are the consequences of air contamination in hydraulic systems?
Air contamination can lead to erratic operation, decreased system efficiency, increased wear on components, cavitation, and higher maintenance costs.
How can I prevent air contamination in hydraulic systems?
Preventive measures include maintaining proper fluid levels, using high-quality hydraulic fluid, ensuring proper sealing and air-tightness of components, and regularly inspecting the system for leaks.
What is the best way to treat air contamination in a hydraulic system?
Treatment options include using air separators and degassing systems to remove air, repairing or replacing faulty seals and pumps, and utilizing fluid conditioning and filtration systems to eliminate dissolved air.
How often should I check for air contamination in my hydraulic system?
Perform inspections and fluid tests at least quarterly, or more frequently if the system operates under heavy loads or in harsh environments.