Hydraulic fittings are essential components in hydraulic systems, acting as connectors between different parts of the system to ensure the proper flow of hydraulic fluid. These fittings maintain the integrity of the system by providing secure connections that prevent fluid leaks and maintain consistent pressure. The purpose of this article is to provide readers with a clear understanding of the key differences between ORB and NPT hydraulic fittings. By examining their design, applications, and performance.
ORB Hydraulic Fittings Overview
Definition and Design
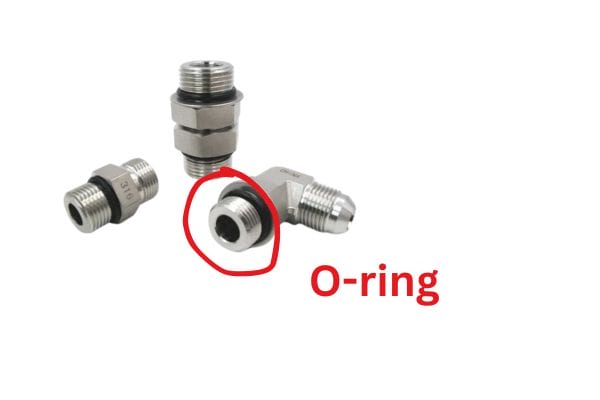
ORB hydraulic fittings are a specific type of fitting designed for secure, leak-proof connections in hydraulic systems. The term “O-ring boss” refers to the O-ring that is integral to the fitting’s design, and “boss” refers to the cylindrical surface area where the O-ring is seated. The ORB fitting features a straight-thread design, meaning that the threads do not taper and the fitting relies on the O-ring to form the seal rather than the threads themselves. This design allows for a more reliable seal in hydraulic systems, especially under high-pressure conditions where leakage can be a critical issue.
The key components of ORB fittings include the body, which is often made of metal such as stainless steel, brass, or carbon steel, and the O-ring, typically made of durable rubber or elastomeric materials such as nitrile, fluorocarbon, or ethylene propylene. The O-ring is seated in a groove located near the base of the threads. When the fitting is tightened into place, the O-ring compresses and forms a seal against the fitting surface, preventing any hydraulic fluid from escaping. Unlike some other fittings, the threads in ORB fittings are primarily responsible for holding the fitting in place, rather than sealing the connection.
This design gives ORB fittings a distinct advantage in applications where high pressure and vibration are common, as the O-ring can absorb small amounts of movement and prevent leaks more effectively than tapered-thread fittings, which rely on tight thread engagement alone to maintain a seal.
Focus on the O-ring Sealing Mechanism for Leak Prevention
The O-ring sealing mechanism is the defining feature of ORB hydraulic fittings and is what sets them apart from other types of fittings, such as NPT. The O-ring is a circular rubber component that is placed into a precisely machined groove within the fitting. When the fitting is threaded into a corresponding port, the O-ring compresses between the fitting and the port, creating a seal that is highly resistant to leaks. This sealing method is particularly effective because the O-ring can maintain its integrity even when the system is subjected to varying pressures or vibrations.
The O-ring’s elasticity allows it to expand and contract with pressure changes, which helps it maintain the seal over time. Additionally, the design of the O-ring allows for easy replacement if it becomes worn or damaged, making ORB fittings a practical and efficient choice for long-term use. The O-ring mechanism is more reliable than thread sealing, especially in dynamic environments where pressure can fluctuate, and it’s far less prone to failure caused by over-tightening or improper installation.
Features of ORB Fittings
ORB fittings are known for several key features that make them ideal for use in hydraulic systems, particularly in environments where high pressure and the potential for leaks are significant concerns. These features include:
Leak-Proof Design: Thanks to the O-ring sealing mechanism, ORB fittings provide an extremely tight, leak-proof connection. This is particularly important in systems where hydraulic fluid leakage can lead to performance issues, safety hazards, or environmental damage.
Ease of Installation: ORB fittings are relatively easy to install compared to tapered-thread fittings like NPT. Since the seal is created by the O-ring and not by the threads, there’s less need for excessive tightening. This reduces the risk of damage to the fitting or the port, making installation quicker and safer.
Reusability: ORB fittings are designed for long-term use and can often be reused by simply replacing the O-ring if it becomes worn. This makes them more cost-effective over time, as the fitting itself remains intact even if the seal needs replacement.
Availability in Various Sizes and Materials: ORB fittings come in a range of sizes and materials, making them versatile for use in different types of hydraulic systems. The material selection allows users to choose the best fitting for their specific application, whether they need corrosion resistance, temperature resilience, or compatibility with particular fluids.
Typical Applications
ORB fittings are commonly used in a variety of hydraulic systems, particularly those where high pressure and the potential for leaks are concerns. These fittings are often found in:
Industrial Hydraulic Systems: Used in manufacturing equipment, ORB fittings ensure that hydraulic fluids remain contained within the system, even in high-pressure scenarios.
Automotive and Aerospace Systems: In these industries, the reliability of ORB fittings is crucial for maintaining safety and performance under extreme conditions.
Mobile Equipment: ORB fittings are often found in agricultural machinery, construction vehicles, and other mobile equipment where hydraulic systems are exposed to constant motion and vibration.
Fluid Power Applications: ORB fittings are also used in fluid power systems where maintaining consistent pressure is essential for the system’s operation.
NPT Hydraulic Fittings Overview
Definition and Design
NPT hydraulic fittings are one of the most commonly used types of fittings in various industries. The design of NPT fittings relies on tapered threads to form a seal between the male and female components. As the name suggests, the threads are not parallel but are tapered, meaning that the diameter of the threads decreases slightly along their length. This taper causes the threads to compress against each other when tightened, which creates a mechanical seal that prevents the leakage of hydraulic fluid, gas, or other media.
The concept behind NPT fittings is that when two tapered threads are mated, the further they are screwed together, the tighter the connection becomes. This results in a wedging action that forms the seal, as opposed to other fittings that rely on O-rings or gaskets for sealing. The NPT fitting’s design follows the ANSI/ASME B1.20.1 standard, which specifies the angles, dimensions, and tolerances of the threads to ensure compatibility across a wide range of applications and manufacturers.
While NPT fittings are effective at creating seals, they are not without their drawbacks. Because the seal is formed by the threads themselves, the integrity of the connection depends heavily on the quality of the threads and the torque applied during installation. Over-tightening can damage the threads and reduce the effectiveness of the seal, while under-tightening can result in leaks. Additionally, to improve the seal, many installers use sealing compounds like Teflon tape or pipe dope, which help to fill in the small gaps between the threads and improve the seal’s reliability.
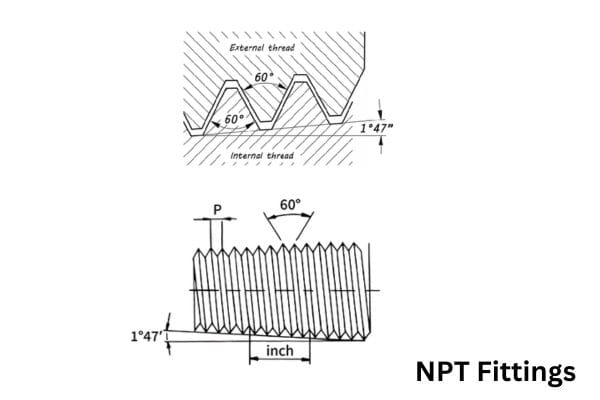
Features of NPT Fittings
NPT fittings offer several notable features that make them suitable for a wide variety of applications. These features include:
Tapered Threads for Creating a Tight Seal
The primary feature of NPT fittings is their reliance on tapered threads to create a tight, leak-resistant seal. As the fitting is tightened, the threads compress against each other, creating friction and sealing the connection. This wedging effect is what allows NPT fittings to maintain a secure connection under pressure.
However, because the seal is formed by the threads, proper installation is crucial. Applying the correct amount of torque and using sealing compounds can greatly enhance the fitting’s performance.
Lower Initial Cost
One of the biggest advantages of NPT fittings is their lower initial cost compared to other types of hydraulic fittings, such as ORB fittings. Because NPT fittings have a simple design and are widely manufactured, they are generally less expensive to produce and purchase. This makes them an attractive option for cost-conscious projects, especially in situations where high-pressure sealing is not a critical concern.
Additionally, the widespread availability of NPT fittings means they can be sourced easily and affordably from many suppliers, making them a practical choice for a range of applications.
Widespread Availability
NPT fittings are used across a wide range of industries and applications, from hydraulic and pneumatic systems to gas lines and plumbing. This widespread use ensures that NPT fittings are readily available in various sizes, materials, and configurations. Whether the project involves standard hydraulic fluid, air, water, or gas, there is likely an NPT fitting available to meet the needs of the system.
Their standardized design and compatibility across manufacturers also make NPT fittings an easy choice for maintenance and repair, as replacements can be found almost anywhere.
Typical Applications
NPT hydraulic fittings are versatile and are commonly used in several industries and systems. Their ability to form a tight seal with tapered threads makes them suitable for a range of applications, although their performance is generally better suited to low-pressure systems or situations where extreme sealing precision is not required. Common applications of NPT fittings include:
Industrial Systems
In industrial systems, NPT fittings are often used in air compressors, pumps, and hydraulic lines where the pressure levels are relatively moderate. Their ability to provide a quick and affordable solution for fluid or gas conveyance makes them a popular choice in various industrial settings.
Industrial machinery that doesn’t operate under high pressure or requires extensive sealing may benefit from the simplicity and cost-effectiveness of NPT fittings.
Low-Pressure Hydraulic Systems
While NPT fittings can be used in hydraulic systems, they are most effective in low-pressure environments. High-pressure hydraulic systems may expose the limitations of NPT fittings, as the thread-based sealing mechanism can be prone to leaks under extreme pressure conditions. In low-pressure hydraulic systems, however, NPT fittings provide an adequate seal without the need for more expensive alternatives like ORB or flare fittings.
Gas Connections
NPT fittings are also widely used in gas connections, such as those in residential and commercial plumbing systems. Their thread-sealing design works well for transporting gases like natural gas, propane, and compressed air, as long as the pressure levels are within acceptable ranges.
Proper installation is especially important in gas systems to ensure a leak-proof connection and to prevent potentially dangerous gas leaks. Thread sealants like Teflon tape are often used to enhance the sealing capability of NPT fittings in these applications.
Key Differences Between ORB and NPT Hydraulic Fittings
Sealing Mechanism
ORB Sealing Mechanism: O-Ring Seal
ORB fittings use a precisely designed O-ring made from elastomeric materials like nitrile, Viton, or other rubber compounds to form the seal. The O-ring is seated in a groove located near the base of the fitting, and when the fitting is tightened into the port, the O-ring compresses between the mating surfaces, forming a tight seal that prevents hydraulic fluid from leaking.
NPT Sealing Mechanism: Thread Sealing
NPT fittings, on the other hand, rely on the mechanical compression of tapered threads to create a seal. The threads are designed to be wider at the opening and narrower towards the end, so when the male and female fittings are screwed together, the threads compress against each other, creating a seal through friction and pressure.
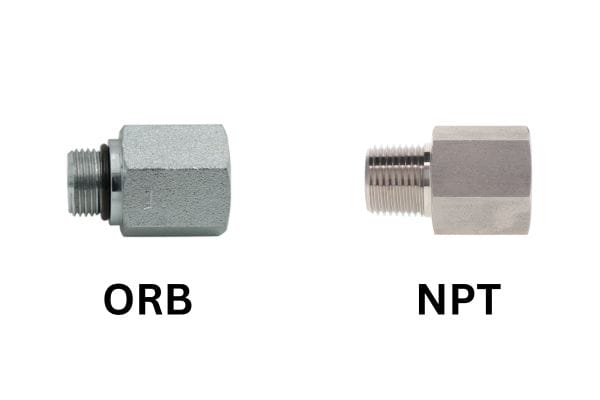
Installation Process
ORB Installation Process
The installation of ORB fittings is generally considered straightforward and less prone to errors, primarily due to the O-ring sealing mechanism. Since the seal is created by the O-ring and not the threads, the installer does not need to apply excessive torque to achieve a leak-proof connection. The fitting is simply screwed into the port until the O-ring is fully compressed, ensuring a reliable seal.
NPT Installation Process
Installing NPT fittings requires more attention to detail and skill, as the threads are responsible for forming the seal. The installer must ensure that the fittings are tightened to the correct torque level, which can be challenging to achieve without specialized tools like torque wrenches. Additionally, sealing compounds such as Teflon tape or pipe dope are often required to enhance the seal.
Pressure Handling
ORB Pressure Handling
ORB fittings excel in high-pressure applications due to their O-ring sealing mechanism. The O-ring provides a flexible and reliable seal that can adapt to pressure fluctuations without losing its integrity. This makes ORB fittings particularly well-suited for hydraulic systems that operate under high pressure, where even minor leaks can lead to performance degradation or safety hazards.
NPT Pressure Handling
NPT fittings, while suitable for many applications, are generally not as effective in high-pressure environments as ORB fittings. The reliance on thread compression for sealing means that NPT fittings are more susceptible to leaks, particularly under high-pressure conditions. Over time, the threads can wear down or become damaged, reducing the effectiveness of the seal and increasing the risk of failure.
Conclusion
Choosing the right fitting for your hydraulic system is crucial for maintaining system efficiency, preventing leaks, and ensuring the safety of the operation. The decision should be based on several factors, including the pressure levels the system will face, the potential for wear and tear, and the specific requirements of the application. For high-pressure systems, ORB fittings are typically the more robust and reliable option, while NPT fittings are a cost-effective solution for lower-pressure applications where sealing precision is less critical.
FAQ
What is the main difference between ORB and NPT hydraulic fittings?
ORB fittings use an O-ring to create a seal, while NPT fittings rely on tapered threads for sealing.
Which fitting is better for high-pressure applications?
ORB fittings are generally better for high-pressure applications due to their reliable O-ring sealing mechanism.
Can I reuse ORB and NPT fittings?
ORB fittings are often reusable by simply replacing the O-ring. NPT fittings can be reused but may require sealing compounds like Teflon tape.
Do ORB fittings require thread sealant?
No, ORB fittings rely on the O-ring for sealing, so thread sealant is not necessary.
Are NPT fittings suitable for high-pressure systems?
NPT fittings are generally better suited for low to moderate-pressure systems, as their thread-based sealing can be prone to leaks under high pressure.
How do I know which fitting is right for my system?
Consider the pressure levels, environmental factors, and the type of fluid in your system. Consulting with a hydraulic expert can help you make the best choice.