NPT (National Pipe Tapered) and NPS (National Pipe Straight) threads are two of the most commonly used thread standards in various industries. NPT threads, known for their tapered design, are widely used in applications where a secure, leak-proof seal is necessary. On the other hand, NPS threads feature a straight design and are often used in situations where a tight seal is achieved through other means, such as gaskets or O-rings. Both thread types are essential in many sectors, but their differences can lead to significant challenges if not properly understood.
Understanding NPT Threads
A. Definition and Characteristics
NPT threads are one of the most widely used thread standards in North America. They are defined by their tapered thread design, where the diameter of the threads decreases along the length of the fitting. This taper creates a wedging action when the male and female threads are tightened together, allowing for a secure and leak-resistant connection. NPT threads are typically used in applications where a tight seal is critical, such as in fluid and gas systems. The sealing is primarily achieved through the metal-to-metal contact between the threads, which is further enhanced by the use of sealing compounds like Teflon tape or pipe dope to prevent leaks.
B. Applications of NPT Threads
NPT threads are commonly found in a wide range of applications due to their reliability and effectiveness in creating leak-proof connections. Some of the most common uses include:
Plumbing Systems: NPT threads are extensively used in residential, commercial, and industrial plumbing for connecting pipes and fittings that carry water, sewage, and other fluids.
Gas Lines: The secure sealing properties of NPT threads make them ideal for gas lines, where preventing leaks is paramount for safety.
Hydraulic Systems: In hydraulic applications, NPT threads are often used to connect hoses, pipes, and valves, ensuring that high-pressure fluids are contained within the system.
Oil and Gas Industry: NPT threads are prevalent in the oil and gas industry, where they are used in pipelines, drilling equipment, and various other components that require durable and leak-resistant connections.
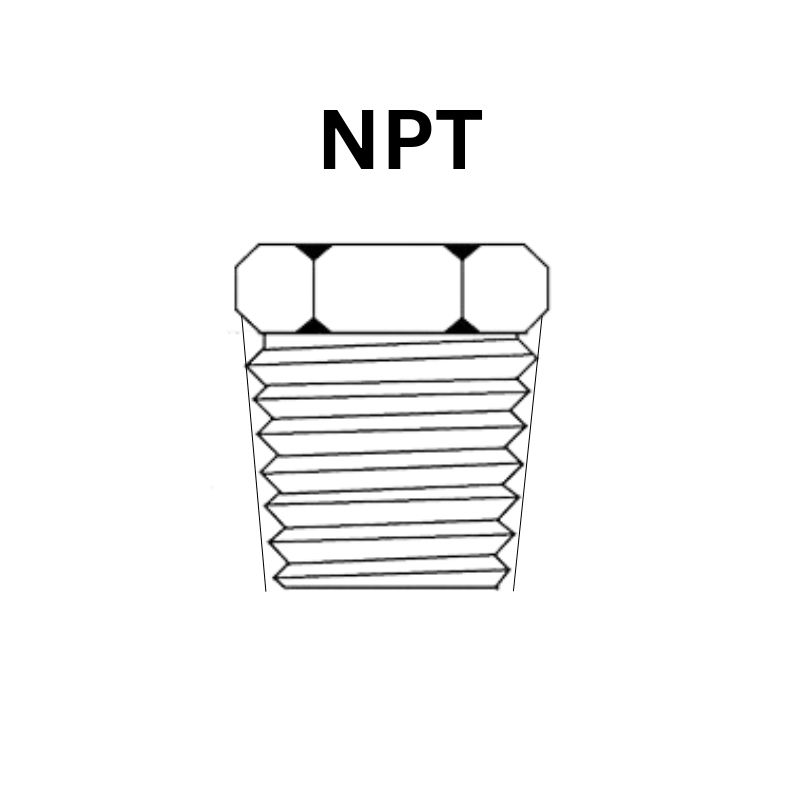
C. Advantages of NPT Threads
NPT threads offer several advantages that contribute to their widespread use:
Reliable Sealing: The tapered design of NPT threads creates a mechanical seal that is effective in preventing leaks, especially when combined with appropriate sealing compounds.
Ease of Use: NPT threads are relatively easy to install and do not require complex tools or techniques, making them a convenient choice for various applications.
Versatility: NPT threads are compatible with a wide range of materials, including steel, brass, copper, and plastic, allowing them to be used in diverse environments and systems.
Cost-Effective: NPT threads are a cost-effective solution for creating secure connections in many industrial and plumbing applications, reducing the need for more expensive alternatives.
D. Limitations of NPT Threads
Despite their many benefits, NPT threads have some limitations that must be considered:
Need for Sealing Compounds: While the tapered design provides a good mechanical seal, NPT threads often require additional sealing compounds, such as Teflon tape or pipe dope, to ensure a completely leak-proof connection. This adds an extra step in the installation process and can be a potential source of error if not applied correctly.
Risk of Over-Tightening: Over-tightening NPT threads can lead to deformation of the threads, compromising the seal and potentially causing leaks. It also increases the risk of damaging the fittings, which can lead to costly repairs or replacements.
Thread Wear: With repeated use, NPT threads can wear down, reducing their effectiveness in creating a seal. This wear and tear can lead to leaks over time, especially in high-pressure or high-vibration environments.
Limited Reusability: Due to the taper and the need for sealing compounds, NPT threads may not be easily reusable after disassembly, as the threads can be damaged or the sealing compound may not be effective when reapplied.
Understanding NPS Threads
A. Definition and Characteristics
NPS threads are a type of thread standard characterized by a straight thread design, meaning the diameter of the threads remains constant along the length of the fitting. Unlike NPT (National Pipe Tapered) threads, NPS threads do not taper and therefore do not create a seal through thread wedging. Because of this, NPS threads do not inherently provide a leak-proof seal when used alone. Instead, they rely on the use of gaskets, O-rings, or other sealing mechanisms to create a secure and leak-resistant connection. NPS threads are often chosen for applications where precise alignment is necessary or where the connection does not require a pressure-tight seal.
B. Applications of NPS Threads
NPS threads are commonly used in a variety of applications where the primary concern is not creating a pressure-tight seal, but rather ensuring proper alignment and connection between components. Some typical applications include:
Mechanical Joints: In situations where components need to be securely joined without the requirement for a leak-proof seal, NPS threads are often used. These threads allow for the accurate alignment of parts, which is critical in many mechanical assemblies.
Electrical Conduits: NPS threads are frequently used in electrical conduit systems, where the primary function is to provide a secure connection for the conduits rather than to seal against fluid or gas leaks.
Pipe Hangers and Supports: NPS threads are used in pipe hangers and supports, where the emphasis is on holding pipes in place rather than preventing leaks.
Low-Pressure Fluid Systems: In applications where the fluid pressure is low and the risk of leakage is minimal, NPS threads may be used with additional sealing methods like gaskets.
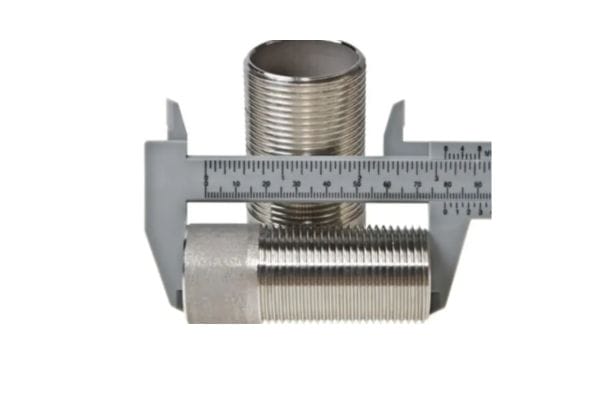
C. Advantages of NPS Threads
NPS threads offer several advantages, particularly in situations where precise alignment and ease of assembly are important:
Ease of Alignment: The straight design of NPS threads allows for easy and precise alignment of components, making them ideal for applications where the accurate positioning of parts is critical.
Simplicity in Non-Pressure Applications: NPS threads are well-suited for non-pressure applications where sealing is not the primary concern, reducing the need for complex sealing techniques.
Compatibility with Sealing Mechanisms: While NPS threads do not seal on their own, they are compatible with a variety of sealing mechanisms, such as gaskets or O-rings, which can be easily added to create a leak-proof connection.
Less Susceptibility to Over-Tightening: Because NPS threads do not rely on tapering to create a seal, there is less risk of over-tightening, which can lead to thread deformation and connection failure in tapered threads.
D. Limitations of NPS Threads
Despite their advantages, NPS threads also have certain limitations that must be considered in their use:
Need for Additional Sealing Methods: Unlike NPT threads, NPS threads do not create a seal through the threads themselves. This means that additional sealing methods, such as gaskets or O-rings, are required to achieve a leak-proof connection. This can complicate the installation process and increase the potential for leaks if the sealing components are not properly installed.
Limited Use in High-Pressure Applications: Due to their reliance on external sealing methods, NPS threads are generally not suitable for high-pressure applications where a strong, self-sealing connection is necessary.
Potential for Misapplication: If NPS threads are mistakenly used in situations requiring a pressure-tight seal without the proper sealing methods, the result could be leaks, system failures, or safety hazards.
Incompatibility with Some Threaded Fittings: NPS threads are not always compatible with other types of threaded fittings, particularly those that are tapered, which can limit their use in certain applications.
Key Differences Between NPT and NPS Threads
A. Tapered vs Straight Threads
One of the most fundamental differences between NPT and NPS threads is their design:
Tapered Threads (NPT): NPT threads have a tapered design, meaning the thread diameter decreases gradually along the length of the fitting. This taper creates a wedging effect when the male and female threads are tightened together, which helps to form a tight seal. The taper allows the threads to bind together, creating pressure that enhances the sealing capability without the need for additional sealing materials in many cases. This design is particularly beneficial in high-pressure applications where maintaining a leak-proof connection is critical.
Straight Threads (NPS): NPS threads, on the other hand, have a straight design, where the thread diameter remains constant throughout the fitting’s length. Unlike tapered threads, NPS threads do not create a natural seal when tightened. Instead, they rely on other means, such as gaskets, O-rings, or thread sealants, to create a leak-proof connection. This makes NPS threads more suitable for applications where the precise alignment of components is essential, rather than sealing against high pressure.
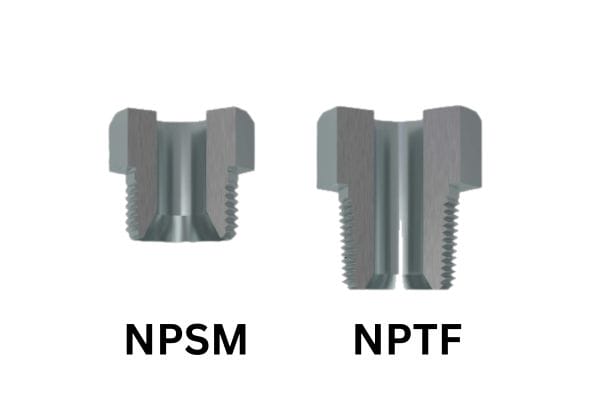
B. Sealing Mechanism
The difference in thread design between NPT and NPS threads leads to distinct sealing mechanisms:
NPT Threads (Sealing Through Wedging): NPT threads achieve a seal through the mechanical wedging of the threads as they are tightened. The tapered design causes the threads to bind together more tightly as they are screwed in, which compresses the material and creates a seal. In many cases, this mechanical seal is sufficient to prevent leaks, although sealants such as Teflon tape or pipe dope are often used to enhance the seal, especially in high-pressure or critical applications.
NPS Threads (Requiring Additional Sealing Methods): NPS threads do not create a seal through the threads alone because of their straight design. To achieve a leak-proof connection, NPS threads require the use of additional sealing methods. Common sealing methods include:
Gaskets or O-rings: These are placed between the mating surfaces to prevent leaks.
Thread Sealants: Such as Teflon tape or pipe dope, are applied to the threads to fill any gaps and ensure a tight seal.
Mechanical Seals: In some cases, the seal is achieved through a mechanical face-to-face connection, where the threads only serve to hold the components in place.
C. Thread Specifications and Standards
NPT and NPS threads are governed by different technical specifications and standards, which define their dimensions, tolerances, and applications:
NPT Threads (ANSI/ASME B1.20.1): The standards for NPT threads are outlined in the ANSI/ASME B1.20.1 specification. This standard defines the dimensions, thread angle, pitch, and taper rate for NPT threads, ensuring consistency and compatibility across different fittings and applications. The taper rate for NPT threads is 1/16 inch per inch, which is crucial for achieving the wedging action that creates the seal.
NPS Threads (ANSI/ASME B1.20.1): While NPS threads share the same standard as NPT threads (ANSI/ASME B1.20.1), they differ in the lack of taper. NPS threads are straight and follow the same pitch and thread angle specifications as NPT but without the taper. This means that while they may appear similar, NPS threads will not create a seal on their own and must adhere to specific sealing practices outlined in industry standards.
Compatibility of NPT and NPS Threads
A. Thread Engagement
NPT and NPS threads can physically engage with each other due to their shared thread pitch and diameter, which allows the threads to be screwed together. However, the key difference lies in the taper of NPT threads versus the straight design of NPS threads:
Engagement Process: When an NPT male fitting is threaded into an NPS female fitting, the threads will engage initially, as the pitch and thread angle are compatible. However, as the NPT threads taper, they will only contact the NPS threads at a few points rather than along the entire length of the thread, leading to a less secure and uneven fit.
Partial Engagement: The engagement between NPT and NPS threads is often partial and inconsistent, resulting in gaps that can compromise the connection’s integrity. This partial engagement can lead to misalignment and difficulty in achieving the desired torque, further complicating the connection.
B. Sealing Issues
The most significant challenge when using NPT and NPS threads together is achieving a proper seal:
Lack of Wedging Effect: NPT threads rely on their tapered design to create a mechanical seal through wedging, while NPS threads do not taper. When combined, the NPT threads cannot fully wedge into the NPS threads, leading to an incomplete seal. The mismatch between the taper and straight design creates gaps that are difficult to seal, especially in high-pressure applications.
Dependence on Sealants: While thread sealants like Teflon tape or pipe dope can be used to fill the gaps and prevent leaks, they are often not sufficient to overcome the fundamental differences in thread design. The reliance on sealants increases the likelihood of improper installation, where insufficient or uneven application can result in leaks.
Inconsistent Sealing: Even with the use of sealing compounds, inconsistent thread engagement can lead to areas where the sealant is not fully effective. This inconsistency increases the risk of leaks over time, especially under conditions of vibration, temperature fluctuations, or pressure changes.
C. Risks of Using NPT and NPS Together
Using NPT and NPS threads together without fully understanding the implications can lead to several significant risks:
Leaks: The most immediate risk is fluid or gas leakage due to the inability to create a proper seal between the NPT and NPS threads. Leaks can occur gradually or suddenly, depending on the application’s pressure and environmental conditions, potentially leading to hazardous situations.
Safety Hazards: In systems that handle flammable, toxic, or high-pressure fluids and gases, leaks caused by improper thread compatibility can result in severe safety hazards, including fire, explosion, or exposure to harmful substances. These risks are particularly high in industrial settings where the consequences of a leak can be catastrophic.
System Failures: Over time, the incomplete seal and uneven engagement can cause stress on the threaded connection, leading to fatigue and eventual failure. In critical systems, such as hydraulic lines or gas pipelines, a failure can result in significant operational disruptions, costly repairs, and potential environmental damage.
How to Choose the Right Thread Type?
Selecting the appropriate thread type is essential to ensuring system integrity, performance, and safety. Misapplication can lead to leaks, equipment failure, and even hazardous incidents in high-pressure environments. Below are practical guidelines based on common application scenarios:
A. For High-Pressure Sealing Systems → Choose NPT
If your system involves high-pressure fluids or gases—such as in hydraulic systems, fuel pipelines, or gas lines—NPT (National Pipe Tapered) threads are the preferred choice.
Why NPT Works: Its tapered design allows for a mechanical seal as the male and female threads wedge tightly together.
Sealing Enhancements: Use Teflon tape or pipe dope (thread sealant) to fill micro gaps and ensure a leak-proof connection.
Recommended For:
Oil & gas pipelines
Compressed air systems
Water supply lines under pressure
⚠️ Be cautious not to over-tighten, as it may deform the threads and compromise the seal.
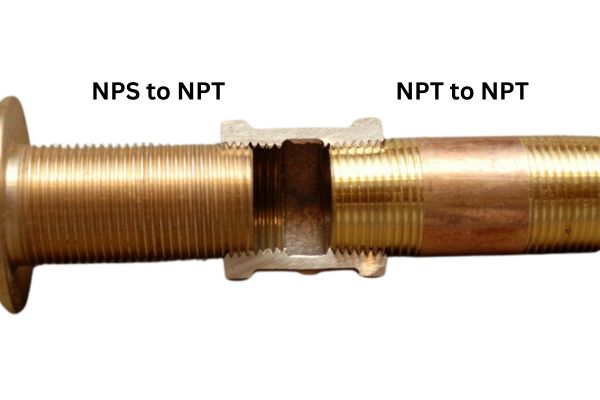
B. For Precise Alignment Without Sealing Needs → Choose NPS
In applications where a leak-proof seal is not essential, but precise orientation or alignment of components is critical—NPS (National Pipe Straight) threads are better suited.
Why NPS Works: The straight thread design allows components to align accurately without binding, which is beneficial for certain mechanical or structural connections.
Sealing Required: Always use gaskets, O-rings, or flange face seals to achieve any level of fluid or gas containment.
Recommended For:
Electrical conduit fittings
Structural pipe supports
Decorative or architectural piping
⚠️Use thread sealants only if sealing is required and appropriate for the connection design.
C. Avoid Mixing NPT and NPS Threads
Although NPT and NPS threads may share the same pitch and thread angle, they are not functionally compatible due to their difference in shape (tapered vs. straight).
Risks of Mixing:
Incomplete thread engagement
Poor sealing and potential for leaks
Increased likelihood of thread damage
Only Mix If:
Specifically engineered and approved by the manufacturer
Successfully pressure-tested under operating conditions
⚠️ Never assume compatibility based on visual similarity. Thread mismatches are a common cause of failure in pressure systems.
Conclusion
As you move forward with your projects, take the time to carefully consider the compatibility of the threads you choose. Whether you’re working on a small plumbing repair or managing a large industrial system, selecting the right thread type is essential for ensuring a safe and effective connection. If you’re unsure about which threads to use, or if you’re dealing with a critical application, don’t hesitate to seek professional advice. Proper thread selection and installation can prevent costly mistakes, enhance system performance, and most importantly, ensure the safety and reliability of your operations.
FAQ
What is the main difference between NPT vs NPS threads?
NPT threads are tapered, creating a seal through wedging, while NPS threads are straight and require additional sealing methods like gaskets or O-rings.
Can NPT and NPS threads be used together?
While NPT and NPS threads can physically engage, they are not recommended to be used together for sealing purposes, as they cannot create a reliable seal on their own.
What applications are NPT threads best suited for?
NPT threads are ideal for applications requiring leak-proof seals, such as plumbing, gas lines, and hydraulic systems.
In what situations should I use NPS threads?
NPS threads are best for applications where precise alignment is necessary, or where sealing is achieved through other means, such as in mechanical joints or electrical conduits.
What are the risks of mixing NPT and NPS threads?
Mixing NPT and NPS threads can lead to leaks, safety hazards, and potential system failures due to their inability to form a proper seal together.
Do NPS threads require sealant?
Yes, NPS threads typically require sealants or gaskets to achieve a leak-proof connection, as they do not seal on their own.