Ball valves are critical components in fluid systems, ensuring precise regulation of flow and pressure for liquids or gases. Proper positioning of these valves not only supports seamless operation and optimal energy efficiency but also promotes a safe working environment. However, even slight misalignment can disrupt the system, leading to inefficiencies, hazards, and costly repairs. Misaligned or stuck ball valves can cause sudden pressure drops, reduced flow, visible leaks, and long-term damage to equipment.
Key Symptoms of a Ball Valve Off Position
Unexplained Pressure Loss Across the System
One of the first signs of a ball valve being in the off position is a sudden and unexplainable drop in system pressure. In a fluid system, consistent pressure is vital for maintaining the flow and ensuring all components work seamlessly. When the ball valve is misaligned, it can partially or fully block the passage, creating resistance that disrupts the pressure balance. This not only reduces the system’s efficiency but also forces pumps and other equipment to work harder, leading to increased wear and energy consumption. Regular monitoring of pressure levels can help you catch this symptom early.
Sudden Reduction in Flow Rate or Blockages
A misaligned ball valve can significantly restrict the flow of liquid or gas through the system. You might notice a sudden reduction in flow rate or, in severe cases, complete blockages that halt operations altogether. This can be particularly problematic in industrial settings where precise flow rates are critical to production processes. A reduction in flow often indicates that the valve is not in the proper position, either due to wear, mechanical failure, or improper handling during maintenance. Promptly inspecting and adjusting the valve can restore normal operation and prevent further complications.

Visible Leaks at Valve Joints and Seals
Leaks around the joints and seals of a ball valve are another telltale sign of an off-position valve. When the valve isn’t properly aligned, it can place uneven pressure on the seals, causing them to wear out prematurely or fail entirely. These leaks can lead to fluid wastage, contamination, or even safety hazards, especially in systems handling hazardous or high-pressure materials. Inspecting for visible leaks and checking the alignment of the valve can help mitigate these risks before they escalate into more serious issues.
Common Causes of Improper Ball Valve Positioning
Misaligned Valve Handles: A Silent Culprit
One of the most frequent causes of improper ball valve positioning is misaligned handles. Over time, wear, user errors, or even accidental bumps can move the handle slightly out of its intended position. Though this may seem insignificant, even minor misalignment can disrupt the valve’s internal mechanisms, leading to partial or complete flow obstruction. In industrial settings, where precision is crucial, these small errors can cascade into larger issues, such as fluctuating system performance or safety hazards. Regular inspections and clearly labeled handles can help prevent this common problem.
Wear and Tear Leading to Valve Misalignment
As with any mechanical component, ball valves are subject to wear and tear over time. Prolonged exposure to high pressures, temperature fluctuations, and corrosive substances can degrade the internal parts of the valve, causing it to lose its alignment. A common result is uneven sealing or incomplete closure, which compromises the system’s efficiency and integrity. Scheduled maintenance is essential to identify and replace worn-out components before they lead to costly downtime or accidents.
External Factors: Vibrations and Incorrect Installation
External factors such as excessive vibrations or improper installation are often overlooked but can be significant contributors to valve misalignment. Vibrations from nearby machinery can loosen valve components or shift them out of position, especially in dynamic industrial environments. Similarly, incorrect installation—such as failing to secure the valve properly or misaligning it during setup—can lead to immediate or progressive alignment issues. Addressing these problems requires following precise installation protocols and using vibration-dampening supports where necessary.
How Ball Valve Misalignment Disrupts Fluid Flow
Understanding Pipeline Flow Disruption
Ball valve misalignment can severely disrupt fluid flow within a pipeline system. A misaligned valve creates an obstruction in the flow path, leading to increased turbulence and resistance. This disruption not only reduces efficiency but can also cause uneven pressure distribution throughout the system. Over time, these irregularities place extra strain on pumps and other components, accelerating wear and potentially causing system-wide failures. Furthermore, flow disruption can result in erratic operation in downstream equipment, impacting overall performance and productivity. Maintaining precise valve alignment is essential to ensure smooth and consistent fluid flow.
Identifying Signs of Fluid Flow Obstruction
Spotting fluid flow obstructions early can prevent costly repairs and downtime. Common indicators include noticeable drops in pressure at specific pipeline sections, uneven flow rates, and increased energy consumption by pumps. In some cases, operators may hear unusual noises, such as whistling or hammering, caused by turbulence around the obstruction. Visual inspections of the valve area might also reveal wear, residue build-up, or physical damage contributing to the blockage. Regular system diagnostics, coupled with the use of flow meters and pressure sensors, can help detect these signs and address valve misalignment promptly, safeguarding system performance.
Mechanical System Inefficiencies Triggered by Valve Misalignment
Increased Energy Usage Due to Flow Resistance
When a ball valve is misaligned, it disrupts the smooth flow of fluid through the pipeline, creating unnecessary resistance. This flow resistance forces pumps, compressors, or other system components to work harder to maintain the desired output. Over time, this additional effort translates to increased energy consumption, driving up operational costs significantly. In industrial systems, where energy expenses form a considerable part of the budget, even a small misalignment can result in substantial financial losses over extended periods.
Moreover, the inefficiency caused by misalignment often leads to overheating of pumps and motors, further accelerating wear and reducing the lifespan of these critical components. Increased energy usage is not just a financial burden but also an environmental concern, as it contributes to higher carbon emissions. Addressing valve misalignment promptly through routine inspections and recalibration can help maintain optimal flow conditions and prevent energy wastage.
Operational Downtime and Its Costs
Valve misalignment doesn’t just hurt energy efficiency—it can lead to unplanned operational downtime, which is even more costly. A misaligned valve may cause system malfunctions, such as erratic pressure changes, fluid leaks, or complete blockages. In critical industrial processes, even brief interruptions can delay production schedules, lead to missed delivery deadlines, and erode customer confidence. The financial impact extends beyond repair costs to include lost revenue during the downtime.
Furthermore, prolonged valve misalignment can cause secondary damage to the system, such as pipeline wear, corrosion, or pump failures. These additional damages often require complex repairs or component replacements, further increasing costs and prolonging downtime. Regular maintenance and predictive diagnostics are essential strategies to prevent such scenarios. By addressing misalignment before it escalates, businesses can save significant resources and maintain operational continuity.
Hydraulic System Leaks: A Direct Result of Misaligned Valves
Detecting Leaks Early to Avoid Catastrophic Failures
Hydraulic system leaks caused by misaligned ball valves are among the most damaging issues a system can face. These leaks often start small but can quickly grow into catastrophic failures if left unaddressed. Misalignment places uneven pressure on valve seals, leading to cracks or gaps that allow fluid to escape. This not only wastes valuable resources but can also compromise system efficiency and safety.
Early detection is critical in preventing these problems. Operators should routinely inspect the system for visible signs of leaks, such as pooling fluid, damp areas around valves, or reduced fluid levels in reservoirs. Additionally, monitoring system performance metrics like pressure drops or unusual pump behavior can provide clues about hidden leaks. For instance, if a pump is working harder than usual to maintain pressure, it could indicate fluid loss somewhere in the system. Using advanced tools like ultrasonic leak detectors or thermal imaging cameras can help pinpoint leaks before they escalate, saving time, money, and equipment.
Key Areas to Inspect for Leaks Around Ball Valves
When checking for leaks caused by valve misalignment, certain areas deserve special attention. The valve seals and seats are the most common weak points. Misaligned valves exert uneven force on these components, causing them to degrade over time. Look for signs of wear, cracks, or fluid buildup around these areas.
The valve stem is another critical point to inspect. Misalignment can cause the stem to shift or warp, creating gaps where fluid can escape. Regularly checking the stem for proper alignment and ensuring it moves freely can prevent minor issues from turning into major leaks.
Additionally, inspect the connection points where the valve integrates with the pipeline. Loose fittings or improperly aligned connections can result in leaks, especially under high pressure. Tightening these connections and verifying alignment during routine maintenance can help maintain a leak-free system.
The Impact of Ball Valve Off Position on System Longevity
Accelerated Corrosion and Metal Fatigue Risks
A ball valve in an off position can dramatically shorten the lifespan of a fluid system by increasing the risk of corrosion and metal fatigue. Misalignment often creates areas of turbulence within the pipeline, where the fluid flow becomes uneven. This turbulence can lead to localized erosion, exposing the valve and surrounding components to accelerated wear. Over time, this creates weak spots in the valve’s structure, making it more susceptible to cracking and eventual failure.
Additionally, misalignment can trap moisture and debris within the valve housing, fostering conditions conducive to corrosion. This is especially problematic in systems that handle corrosive fluids or operate in humid environments. Corrosion weakens the valve’s metal components, compromising their integrity and leading to leaks or complete valve failure. Regular inspections and prompt corrections of misalignment are essential to prevent these risks and maintain the structural health of the valve and pipeline.
How Misaligned Valves Affect Seal Durability
Valve seals are designed to maintain a tight, leak-proof connection, but misalignment places uneven stress on these critical components. When a valve is off position, the seal’s contact points may become distorted, reducing its ability to hold pressure effectively. This distortion causes gradual wear and, in some cases, can lead to the seal cracking or tearing under the strain.
As seals degrade, leaks become inevitable, leading to fluid loss, system inefficiencies, and potential safety hazards. Moreover, compromised seals often allow contaminants to enter the system, which can further accelerate wear and tear on other components. The cumulative effect of misalignment and seal failure significantly shortens the overall lifespan of the valve and the system it serves.
Ensuring proper alignment during installation and conducting regular maintenance checks on the valve and its seals can mitigate these risks. Replacing worn seals promptly and addressing alignment issues as soon as they arise are cost-effective measures that protect both the valve and the system’s longevity. By prioritizing these steps, operators can maintain a durable, efficient system and avoid costly repairs or replacements down the line.
Troubleshooting Valve Actuator Issues
Identifying Actuator Problems Affecting Valve Position
Valve actuators are critical for controlling the position of ball valves, ensuring proper flow regulation and system efficiency. However, when actuators malfunction, they can cause the valve to be misaligned or stuck in an off position. Common issues include electrical faults in motorized actuators, insufficient pneumatic or hydraulic pressure in powered actuators, or mechanical wear in manual actuator components.
Signs of actuator problems often manifest as inconsistent valve movement, delays in operation, or the inability to achieve a fully open or closed position. Operators may also notice irregular system behavior, such as pressure drops or erratic flow rates. Using diagnostic tools, such as a multimeter for electrical actuators or pressure gauges for pneumatic systems, can help pinpoint the root cause of the issue. Routine visual inspections for loose connections, damaged components, or fluid leaks around actuators are also essential for early detection.
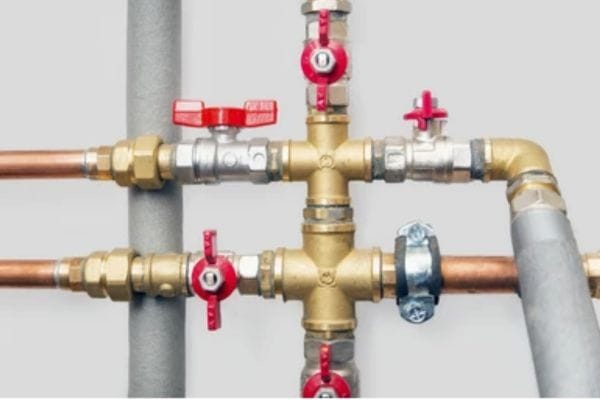
Simple Fixes for Common Actuator Failures
Addressing actuator problems doesn’t always require extensive repairs or replacements. Some common issues can be resolved with straightforward fixes. For example:
Electrical Actuators: If an actuator fails to respond, check the power supply and connections for faults. Loose wiring or blown fuses are often to blame. Restoring proper electrical connections or replacing faulty components can quickly resolve the issue.
Pneumatic or Hydraulic Actuators: A pressure drop often indicates a leak or blockage in the system. Inspect hoses, fittings, and seals for damage and replace them as needed. Additionally, verify that the pressure regulator is set to the correct level for optimal actuator performance.
Manual Actuators: Stiff or unresponsive manual actuators may simply require lubrication to restore smooth movement. In cases of excessive wear or stripped gears, replacing worn components can bring the actuator back to working condition.
After making repairs, always recalibrate the actuator to ensure it moves the valve into the correct position. Testing the system under normal operating conditions will confirm whether the issue has been fully resolved. For more complex problems, consulting the actuator’s manual or seeking assistance from a technician may be necessary to prevent further complications.
When to Replace Your Ball Valve
Recognizing the Signs of a Failing Valve
Ball valves are designed for durability, but they won’t last forever. Over time, wear, corrosion, and mechanical stress can compromise their functionality. Recognizing the signs of a failing valve early can prevent costly system failures and downtime.
Common indicators include persistent leaks around the valve, even after tightening or replacing seals. Difficulty in turning the valve handle, which may indicate internal blockages or corroded components, is another red flag. Inconsistent flow rates, pressure fluctuations, or the inability to fully open or close the valve suggest internal damage, such as a deformed ball or compromised seats. Unusual noises, such as hissing or whistling, may also signal that the valve is no longer maintaining a proper seal.
Frequent repairs on the same valve are another warning sign. If maintenance costs are mounting and performance remains subpar, it’s often more cost-effective to replace the valve than to continue with patchwork fixes.
Choosing the Right Replacement: Material and Size Considerations
Selecting the right replacement ball valve is critical to maintaining system performance and longevity. The choice depends on several factors, including the fluid or gas being transported, system pressure, and operating conditions.
Material: The valve’s material must be compatible with the fluid and environmental conditions. Stainless steel is ideal for corrosive or high-temperature applications, while brass is suitable for water and mild chemicals. Plastic valves, such as those made from PVC or CPVC, are lightweight and corrosion-resistant, making them perfect for low-pressure or non-aggressive fluid systems.
Size: The replacement valve must match the dimensions of the existing pipeline. Check the valve’s diameter and connection type to ensure a proper fit. Using the wrong size can lead to flow restrictions or leaks, negating the benefits of a new valve.
Special Features: Consider whether your system requires additional features, such as locking mechanisms for safety, a three-way design for directional control, or anti-static components for flammable fluids.
Certifications: Verify that the replacement valve meets relevant industry standards, such as ISO or ANSI certifications, to ensure quality and compatibility with your system.
Steps to Prevent Ball Valve Position Issues
Routine Valve Inspections and Predictive Maintenance
Preventing ball valve position issues begins with a proactive approach to maintenance. Regular inspections are critical to identifying potential problems before they escalate. During these inspections, operators should:
Check for Visible Signs of Wear and Damage: Look for corrosion, leaks, or deformation around the valve and its components.
Test Valve Movement: Open and close the valve to ensure smooth operation. Resistance or stiffness may indicate internal buildup or misalignment.
Monitor System Performance: Keep an eye on pressure readings and flow rates. Sudden drops could signal valve misalignment or wear.
Predictive maintenance adds another layer of protection. By using advanced tools like vibration analysis, thermal imaging, or ultrasonic sensors, operators can detect hidden issues such as internal wear or leaks. Creating a maintenance schedule that includes these regular checks ensures the valve remains in proper working condition, reducing the likelihood of sudden failures or costly repairs.
Tips for Ensuring Proper Installation and Alignment
Proper installation is the foundation of a well-functioning ball valve. Missteps during setup often lead to misalignment and operational issues. To avoid this, follow these best practices:
Prepare the Installation Site: Ensure the pipeline is clean and free of debris before installing the valve. Dirt or particles can interfere with alignment and cause damage during operation.
Verify Correct Orientation: Install the valve in the correct flow direction, as indicated by the manufacturer’s markings. Improper orientation can compromise performance and shorten the valve’s lifespan.
Secure Connections Properly: Tighten all fittings and connections to prevent leaks. Use appropriate tools and avoid over-tightening, which can deform the valve or its seals.
Check Alignment After Installation: Use valve position indicators or alignment tools to ensure the valve is properly seated. Misalignment during installation can lead to uneven wear and inefficient operation.
Test Before Operation: Open and close the valve several times after installation to verify smooth movement and proper alignment. This step helps confirm that the valve is ready for use.
Conclusion
Misaligned ball valves can lead to leaks, flow disruptions, energy waste, and long-term damage to your system. Early detection of warning signs—such as pressure drops, reduced flow, or visible leaks quality components, is key to system reliability. At Topa, we offer premium ball valves designed for durability and precision, ensuring your system runs smoothly. Don’t risk costly downtime—upgrade to Topa ball valves today for optimal performance and peace of mind.
FAQ
What are the common signs of a misaligned ball valve?
Common signs include leaks around the valve, pressure drops, reduced flow rates, difficulty operating the valve, and unusual system noises such as whistling or hammering.
How often should ball valves be inspected?
Routine inspections should be conducted every six months, but high-use or critical systems may require more frequent checks.
What causes ball valve misalignment?
Misalignment can be caused by improper installation, wear and tear, external vibrations, or incorrect handling during maintenance.
Can a misaligned valve damage the system?
Yes, misaligned valves can lead to increased energy consumption, leaks, system inefficiencies, and accelerated wear on other components, potentially causing significant damage.
How can I prevent ball valve alignment issues?
Prevent issues by following proper installation practices, conducting regular inspections, using alignment tools, and scheduling predictive maintenance.
When should I replace a ball valve?
Replace the valve when you notice persistent leaks, difficulty in operation, visible corrosion, or recurring issues despite repairs.