O-rings, a simple yet essential component in engineering and mechanical systems, are circular sealing devices made from elastomers. Their primary function is to prevent leaks and ensure that fluids or gases stay contained within specific areas of equipment. Found in various applications, from hydraulic systems and automotive engines to industrial machinery, O-rings are critical to ensuring that systems operate safely and efficiently. The purpose of this article is to break down the differences between static and dynamic O-rings, shedding light on their unique properties and helping readers make informed decisions when selecting the right type of O-Ring for their specific application.
What Are Static O-Rings?
Definition and Key Characteristics
Static O-rings are sealing devices that are used in applications where no relative movement occurs between the sealing surfaces. They are placed between stationary components to create a tight, leak-proof seal. The primary function of static O-rings is to fill the space between two non-moving parts, preventing the passage of fluids or gases. These O-rings rely on compression to maintain their seal and remain in a fixed position throughout their service life. One of their key characteristics is their ability to maintain seal stability, which ensures a long-lasting, reliable barrier against leaks. Additionally, static O-rings are specifically designed to resist motion-induced wear, making them ideal for applications where there is no need for the O-Ring to accommodate movement.
Static O-rings are commonly made from a variety of elastomers such as nitrile (NBR), fluorocarbon (Viton®), silicone, and EPDM. The material selection largely depends on the environment in which the O-Ring will be used, with considerations for temperature, pressure, and chemical exposure. These materials are chosen for their ability to maintain elasticity and compressibility over time, ensuring the seal remains effective even in challenging conditions.
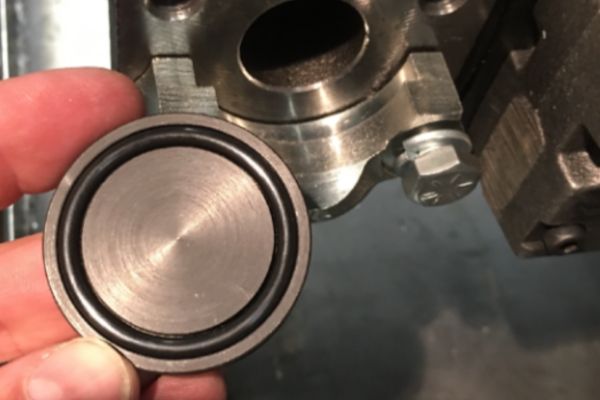
Applications of Static O-Rings
Static O-rings are widely used in applications where the sealing components remain stationary. Common examples include pipe fittings, flanges, valve bonnets, and other mechanical assemblies that require a reliable, immobile seal. In these applications, the O-Ring remains compressed between two surfaces, creating an airtight or watertight barrier.
For instance, in pipe fittings, static O-rings are used to prevent leaks where pipes connect, ensuring that fluids such as water, oil, or gas remain contained within the system. Similarly, in valve bonnets, static O-Rings prevent leaks around the top of the valve assembly, maintaining pressure within the valve body while keeping external contaminants out. These O-Rings are also used in flange connections, where they are placed between the flanges to provide a seal that prevents fluid or gas from escaping at the connection point. Static O-Rings perform best in environments where they can remain undisturbed, providing consistent sealing performance without the need for frequent adjustments.
Advantages of Static O-Rings
Static O-Rings offer several advantages, especially in applications where their primary function is to maintain a seal without accommodating movement. One of their main benefits is minimal maintenance. Since static O-Rings do not experience friction or motion-related wear, they typically have a longer lifespan than their dynamic counterparts. This longevity is particularly valuable in non-moving parts, as it reduces the need for frequent inspections and replacements, ultimately saving time and costs for maintenance teams.
Another key advantage of static O-Rings is their ease of replacement. In the rare event that a static O-Ring does wear out or degrade, it can be quickly and easily replaced without the need for specialized tools or complex procedures. This contributes to the overall cost-effectiveness of static O-Rings, as their durability and ease of replacement minimize both downtime and operational costs.
What Are Dynamic O-Rings?
Definition and Key Characteristics
Dynamic O-Rings are specially designed sealing devices used in applications where there is relative motion between the sealing surfaces. Unlike static O-Rings, which remain stationary, dynamic O-Rings must withstand constant movement, whether it is rotational, reciprocating, or oscillating. These O-Rings create a seal while accommodating the movement between two parts, making them essential in machinery and systems with moving components.
The key characteristics of dynamic O-Rings include flexibility, durability under motion, and the ability to withstand friction and movement. They are designed to maintain an effective seal while allowing the moving parts to function without excessive wear. Flexibility is a critical trait, as dynamic O-Rings need to deform without losing their sealing capability when subject to motion. Durability is also essential, as these O-Rings are constantly exposed to friction and must resist wear over time. Special materials, coatings, or lubricants are often applied to enhance the frictional resistance of dynamic O-Rings, enabling them to endure high-frequency movements without compromising their sealing performance.
Common materials used for dynamic O-rings include nitrile (NBR), fluorocarbon (Viton®), polyurethane, and silicone. These materials are selected for their elasticity, resistance to wear, and ability to withstand temperature fluctuations and pressures commonly encountered in dynamic applications. For example, nitrile offers good resistance to wear and is commonly used in hydraulic and pneumatic systems, while fluorocarbon is ideal for applications that involve exposure to high temperatures or aggressive chemicals.
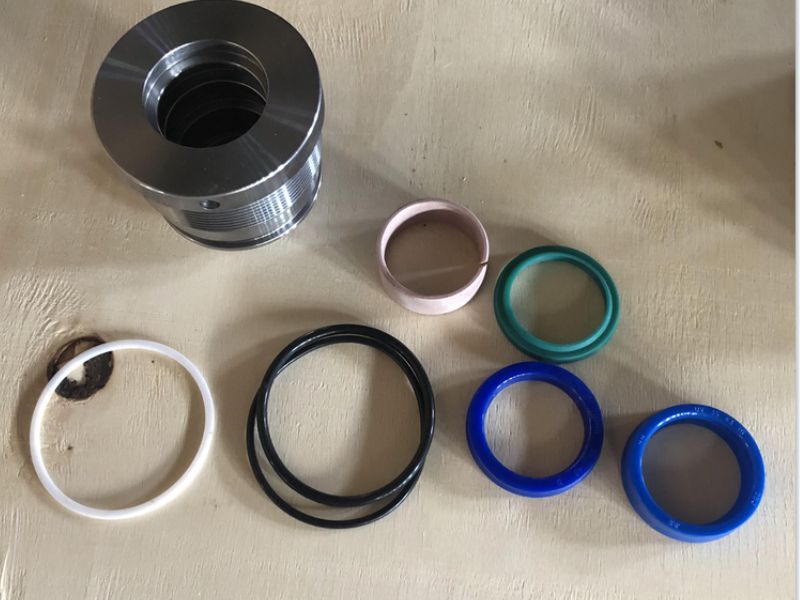
Applications of Dynamic O-Rings
Dynamic O-Rings are employed in a variety of applications where the sealing surfaces are in motion. Some common examples include hydraulic cylinders, rotating shafts, and pistons. In these settings, dynamic O-Rings play a crucial role in maintaining the integrity of the system by preventing fluid or gas leaks while accommodating the continuous movement of parts.
For instance, in hydraulic cylinders, dynamic O-Rings are used to seal the piston rod and maintain the pressure inside the cylinder. This is vital to ensuring that the hydraulic system can generate the necessary force without leaking hydraulic fluid. Similarly, in rotating shafts, dynamic O-Rings are used to create a seal between the rotating and stationary components, preventing oil or other lubricants from leaking out while the shaft is in motion. In piston applications, dynamic O-Rings are used to seal the space between the piston and the cylinder wall, ensuring that the gases or fluids in the system remain contained while the piston moves.
Dynamic O-Rings perform best in environments where there is frequent motion, such as in fluid power systems, automotive components, and industrial machinery. They are designed to maintain their sealing capabilities while allowing for the smooth operation of moving parts, making them indispensable in dynamic sealing applications.
Advantages of Dynamic O-Rings
Dynamic O-Rings offer several key advantages, particularly in applications where movement is frequent. One of the most significant benefits is their ability to accommodate motion. Dynamic O-Rings are specifically designed to endure the friction and movement associated with dynamic applications, allowing them to maintain an effective seal even under constant motion. This makes them ideal for use in machinery and systems where parts are in regular movement, such as in hydraulic and pneumatic systems.
Another major advantage of dynamic O-Rings is their high resistance to wear and tear. These O-Rings are engineered to withstand the friction generated by moving parts, reducing the risk of wear-related failures. This durability is crucial in preventing leaks and ensuring that the system continues to function properly over extended periods. The longevity of dynamic O-Rings reduces the need for frequent replacements, minimizing downtime and maintenance costs.
Flexibility is another key advantage of dynamic O-Rings. Their ability to deform under pressure and then return to their original shape allows them to maintain a secure seal even in environments with fluctuating pressures and temperatures. This flexibility ensures that dynamic O-Rings can adapt to the changing conditions within the system without compromising their sealing capabilities.
Dynamic O-Rings are especially important in fluid power systems, where maintaining pressure is critical to the system’s performance. These systems often involve high levels of movement, and the failure of a seal could lead to leaks, loss of pressure, and system inefficiencies. By providing reliable seals in moving components, dynamic O-Rings contribute to the overall efficiency and safety of fluid power systems.
Key Differences Between Static vs Dynamic O-Rings
Seal Design and Functionality
The primary difference between static and dynamic O-rings lies in their seal design and functionality. Static O-Rings are designed to create a seal between two stationary components, relying on the compression of the O-Ring to form a tight barrier that prevents the passage of fluids or gases. The sealing mechanism in static O-Rings is relatively straightforward: the O-Ring is compressed within a groove, creating enough pressure to form a tight, leak-proof seal. This simplicity in design means that static O-Rings can maintain their performance over time with minimal external forces acting on them.
Dynamic O-Rings, on the other hand, are specifically designed to seal between surfaces that are in motion relative to each other. Unlike static O-Rings, which rely solely on compression, dynamic O-Rings must also accommodate movement, such as sliding, rotating, or reciprocating motion. The design of dynamic O-Rings allows them to maintain a seal while experiencing friction and wear caused by the movement of the parts they seal. This introduces a more complex sealing mechanism, where the O-Ring must constantly adapt to the movement while preventing leaks. As a result, dynamic O-Rings typically require lubricants or special coatings to reduce friction and ensure smooth operation.
The design differences between static and dynamic O-Rings significantly influence their performance under various conditions. Static O-Rings excel in environments where the components remain stationary, providing reliable sealing in systems with minimal fluctuations in pressure or temperature. In contrast, dynamic O-Rings are built to endure continuous motion and mechanical stress, making them essential in systems with moving parts, such as hydraulic cylinders or rotating shafts.
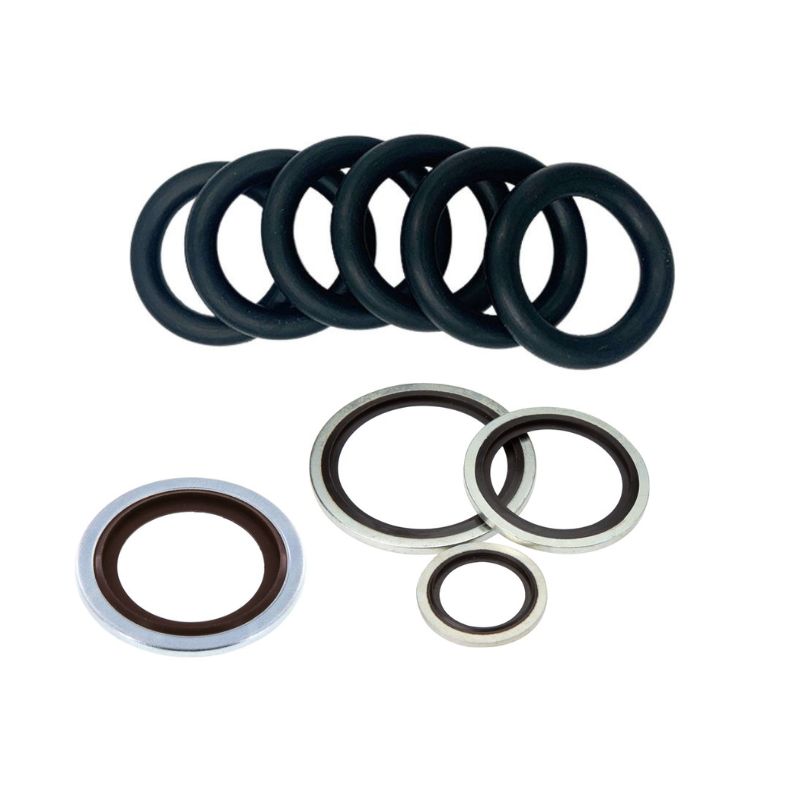
Material Selection for Each Type
Material selection is crucial when determining whether an O-Ring will be used in a static or dynamic application. For static O-Rings, materials are chosen primarily for their compressibility, resistance to environmental factors, and ability to maintain a stable seal over time. Common materials for static O-Rings include nitrile (NBR), EPDM, silicone, and fluorocarbon (Viton®). These materials are known for their durability and resistance to factors such as extreme temperatures, chemicals, and pressure, which are common in stationary applications.
Dynamic O-Rings, however, require materials that can endure movement, friction, and wear while maintaining their sealing capabilities. Materials like polyurethane, fluorocarbon, nitrile (NBR), and PTFE (Teflon®) are often used in dynamic applications due to their flexibility, elasticity, and resistance to wear and abrasion. Dynamic O-Rings often require materials with higher tensile strength and improved lubricity to reduce friction and extend their lifespan in moving parts.
The choice of material impacts both durability and sealing efficiency. For example, in a static application where there is little to no movement, a material like EPDM might be ideal due to its excellent weather and ozone resistance. However, in a dynamic application, a more robust material like polyurethane may be necessary to handle the continuous stress of movement and provide long-term durability. The right material ensures that the O-Ring can maintain its seal over time while minimizing the risk of failure due to environmental or operational conditions.
Wear and Tear Considerations
Wear and tear are significant considerations when comparing static and dynamic O-Rings, as the presence or absence of movement drastically affects the lifespan and maintenance requirements of the O-Rings. In static applications, wear is minimal because the O-Ring remains stationary and does not experience friction or mechanical stress. The primary causes of wear in static O-Rings are environmental factors such as temperature fluctuations, chemical exposure, and compression set. Compression set occurs when the O-Ring becomes permanently deformed due to long-term compression, reducing its ability to maintain a proper seal. However, with proper material selection and maintenance, static O-Rings can last for extended periods without the need for replacement.
Dynamic O-Rings, in contrast, are subjected to constant movement, which introduces significant wear and tear over time. The friction caused by the movement of the sealing surfaces against the O-Ring can lead to abrasion, erosion, and material degradation. Lubrication is often necessary to reduce friction and prolong the life of the dynamic O-Ring, but even with lubrication, dynamic O-Rings typically have a shorter lifespan than static O-Rings due to the continuous mechanical stresses they endure.
For example, in a hydraulic cylinder, the dynamic O-Ring sealing the piston rod is constantly moving as the rod reciprocates, leading to gradual wear on the O-ring’s surface. This wear can eventually cause the O-Ring to lose its sealing effectiveness, leading to leaks or pressure loss. In contrast, a static O-Ring used to seal a stationary valve bonnet may remain in service for years without showing significant signs of wear, as long as it is not exposed to harsh environmental conditions.
Factors to Consider When Choosing Between Static and Dynamic O-Rings
Temperature
When choosing between static and dynamic O-Rings, the application environment plays a critical role in the decision-making process. One of the key considerations is the temperature range in which the O-Ring will operate. O-Rings are exposed to a wide variety of temperature extremes, which can affect their material properties and sealing performance. For instance, in high-temperature environments, materials like silicone or fluorocarbon (Viton®) may be necessary due to their heat resistance, while in low-temperature applications, materials such as nitrile (NBR) or silicone may be preferred for their ability to retain flexibility.
Pressure
Pressure is another essential factor. High-pressure applications can cause excessive compression, leading to O-Ring deformation or extrusion. Static O-Rings, which remain stationary, typically perform better in high-pressure environments because there is no movement to exacerbate stress on the seal. In contrast, dynamic O-Rings in high-pressure applications must resist both pressure and the wear from movement, which can be more demanding. Choosing an O-Ring material with high tensile strength and compression resistance is crucial for dynamic applications exposed to high pressure.
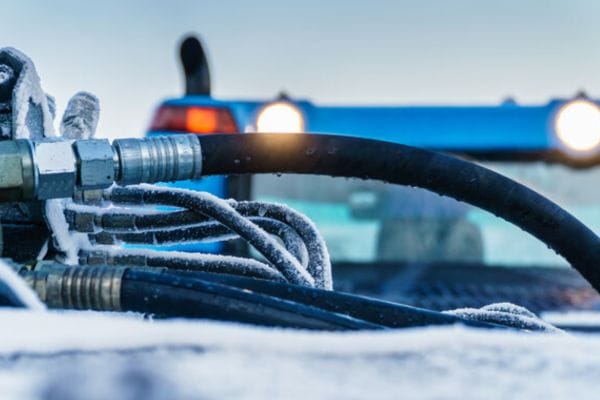
Media
Media exposure is equally important. The O-Ring material must be compatible with the media it will come in contact with, whether it’s water, oil, chemicals, or gases. Certain materials, such as EPDM, are ideal for water-based applications but may degrade when exposed to oils, while fluorocarbon O-Rings are more resistant to aggressive chemicals and oils but may not be suitable for steam or certain acids. Understanding the chemical exposure and selecting a material that can resist degradation ensures a longer service life and more effective sealing.
Environmental factors
Environmental factors such as UV exposure, ozone, and outdoor conditions also influence the choice between static and dynamic O-Rings. For static applications, the O-Ring’s resistance to environmental degradation is paramount to maintaining a long-lasting seal. For dynamic applications, the need for resistance to both environmental factors and movement-related stresses makes material selection even more critical.
Movement and Vibration
The amount of movement and vibration within a system is a defining factor in choosing between static and dynamic O-Rings. Static O-Rings are suitable for applications where there is no relative motion between the sealing surfaces. In these cases, the O-Ring remains compressed between two stationary components, and movement is not a concern.
However, when there is movement in the system, dynamic O-Rings are necessary. The frequency and magnitude of motion must be considered. For example, in systems with reciprocating motion, such as hydraulic cylinders, or rotating shafts, dynamic O-Rings must withstand continuous back-and-forth or rotational movements. Special considerations must be made for applications with high motion frequencies, where wear and friction are major concerns. O-Rings in these environments may require materials that can endure the stress of repeated movements, such as polyurethane or PTFE, which offer superior wear resistance.
Vibration also plays a role in O-Ring selection. Vibrations can cause excessive wear or misalignment of the O-Ring, especially in dynamic applications where parts move relative to each other. O-Rings designed for dynamic use often need to be more flexible and can absorb some of the vibrations without losing their sealing capability. Lubrication or special surface coatings may also be applied to reduce the effects of friction and vibration, prolonging the O-Ring’s lifespan.
In applications with minimal movement or vibration, a static O-Ring is often the better choice due to its simplicity and reliability. However, for systems where movement is frequent or vibration is significant, dynamic O-Rings are essential to maintain proper sealing and avoid premature failure.
Durability and Lifespan Requirements
Durability is one of the most crucial considerations when selecting O-rings, as the expected lifespan of the seal depends on how well the material can withstand the operating conditions over time. For static O-Rings, durability concerns are generally related to environmental factors such as chemical exposure, temperature variations, and aging effects. Since static O-Rings do not experience mechanical wear from movement, they often last longer and require less frequent replacement, provided they are made from materials compatible with their environment. The key to maximizing the lifespan of static O-Rings is selecting materials that can resist degradation from external factors while maintaining their elasticity and compression over time.
Dynamic O-Rings, on the other hand, must withstand not only environmental factors but also the wear and tear from constant movement. Durability in dynamic applications is influenced by several factors, including the material’s resistance to abrasion, its ability to maintain flexibility under repetitive motion, and its resilience to the stresses of friction. In high-motion applications, choosing a more durable material such as polyurethane or PTFE can help extend the lifespan of the O-Ring. Regular lubrication and maintenance are also essential for dynamic O-Rings, as they help reduce friction and prevent premature wear.
Conclusion
As a final call to action, we encourage you to thoroughly evaluate your system’s requirements and reach out to professional advisors who can help you select the most appropriate O-Ring for your specific application. Whether you are working in fluid power systems, automotive, or industrial machinery, having the right O-Ring can make all the difference in maintaining the efficiency and reliability of your equipment.
FAQ
What is the difference between a static and a dynamic O-Ring?
Static O-Rings are used in stationary applications where no movement occurs, while dynamic O-Rings are designed for applications with relative motion between parts.
When should I use a static O-Ring?
Use a static O-Ring in applications where the sealing components remain stationary, such as in pipe fittings, flanges, or stationary valve bonnets.
What materials are best for dynamic O-rings?
Materials like nitrile, polyurethane, and PTFE are commonly used for dynamic O-rings due to their durability, flexibility, and resistance to wear.
How do I choose the right O-Ring for my application?
Consider the operating environment, pressure, temperature, and whether the application involves motion. Consult with an expert if unsure.
What causes O-Ring failure?
Common causes include improper material selection, excessive wear, exposure to incompatible chemicals, or incorrect installation.
Can a dynamic O-Ring be used in a static application?
While possible, dynamic O-rings are typically more expensive due to their added durability. It’s more efficient to use static O-rings in non-moving applications.