O rings are small but critical components used in a wide range of industries, from automotive and aerospace to hydraulic systems and manufacturing equipment. Their primary function is to create a reliable seal between two parts, preventing the leakage of fluids or gases and ensuring the system operates smoothly and efficiently. When properly selected and installed, O-rings can dramatically extend the lifespan of machinery, reduce downtime, and enhance the overall safety of an operation. In this guide, we will explore everything you need to know about O-rings, from understanding their basic function to selecting the right material and size for your specific application.
What Are O-Rings?
Definition of O-Rings
O-rings are circular, torus-shaped sealing elements made from elastomeric materials that are widely used to prevent the leakage of fluids or gases between two or more components. These seals are highly versatile and are employed in static and dynamic applications where they sit in a groove and are compressed between two surfaces. The pressure created by this compression forms a seal, preventing any unwanted escape from liquid or gas. Due to their simplicity, effectiveness, and cost-efficiency, O-rings are used extensively across various industries such as automotive, hydraulics, aerospace, plumbing, and manufacturing, where the integrity of sealing systems is critical to performance and safety.
Types of O-Rings
O-rings come in a wide variety of shapes and sizes to suit different sealing needs. The most common type is the standard O-ring, which features a round cross-section and is available in both imperial and metric sizes. Standard O-rings are typically used in static applications, such as sealing flanges or lids. Metric O-rings, which follow the international measurement system, are often found in European and other global markets. Besides these, square O-rings offer an alternative shape with a square cross-section, providing greater surface contact, and are typically used in high-pressure sealing applications. In more specialized applications, custom-shaped O-rings may be necessary, including O-rings with unique profiles designed to address specific challenges, such as irregular sealing surfaces or environments with extreme temperatures or chemical exposure.
Material Composition
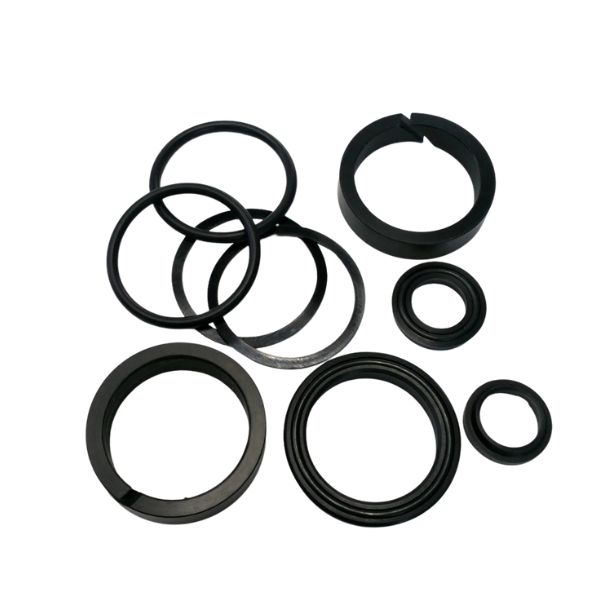
The performance of an O-ring is highly dependent on the material from which it is made. O-rings are available in a wide range of materials, each selected based on the environment and conditions in which the O-rings will operate. Common materials include:
Nitrile (NBR): Known for its excellent resistance to oils, fuels, and other petroleum-based products, nitrile is widely used in automotive and industrial applications.
Silicone: Silicone O-rings offer superior flexibility and temperature resistance, making them ideal for applications in extreme heat or cold, such as in aerospace or food processing.
EPDM: This material is excellent for applications involving exposure to water, steam, or weathering, making it popular in HVAC, automotive cooling systems, and outdoor applications.
Viton (FKM): Known for its exceptional chemical resistance and high-temperature performance, Viton is commonly used in chemical processing, oil, and gas industries.
PTFE (Teflon): PTFE O-rings are highly resistant to chemicals, heat, and wear, making them suitable for aggressive environments like chemical processing plants or industries requiring non-reactive seals, such as pharmaceutical or food processing.
Importance of Proper Sizing
Consequences of Incorrect Sizing
Proper sizing of O-rings is crucial to ensuring the effective sealing of components. Incorrect sizing can lead to several detrimental outcomes, compromising the entire system’s performance. For instance, if the O-ring is too large, it may not compress properly within its groove, leading to leaks and reduced sealing capacity. On the other hand, an O-ring that is too small may overstretch, causing it to weaken or break over time, potentially resulting in seal failure. Such failures can lead to fluid or gas leakage, which not only increases the risk of equipment damage but can also pose safety hazards, particularly in high-pressure or high-temperature environments. Additionally, poorly sized O-rings can contribute to operational inefficiencies by causing unexpected downtimes, increasing maintenance costs, and reducing the overall lifespan of the machinery.
Basic Principles of O-Ring Sizing
Understanding the basic principles of O-ring sizing is essential to selecting the correct O-ring for a specific application. O-rings are characterized by three critical dimensions:
Inner Diameter (ID): This refers to the distance across the inside of the O-ring and is the most crucial dimension for fitting the O-ring onto a specific shaft or groove.
Outer Diameter (OD): The outer diameter measures the total distance across the O-ring from edge to edge. This dimension ensures that the O-ring fits snugly within the housing or bore.
Cross-Sectional Diameter (CSD): The cross-sectional diameter refers to the thickness of the O-ring when viewed in a cut cross-section. This measurement determines how much the O-ring will compress when placed in its groove and, ultimately, how effectively it seals.
By accurately measuring and understanding these dimensions, the proper size of the O-ring can be selected, allowing for a secure fit and optimal performance.
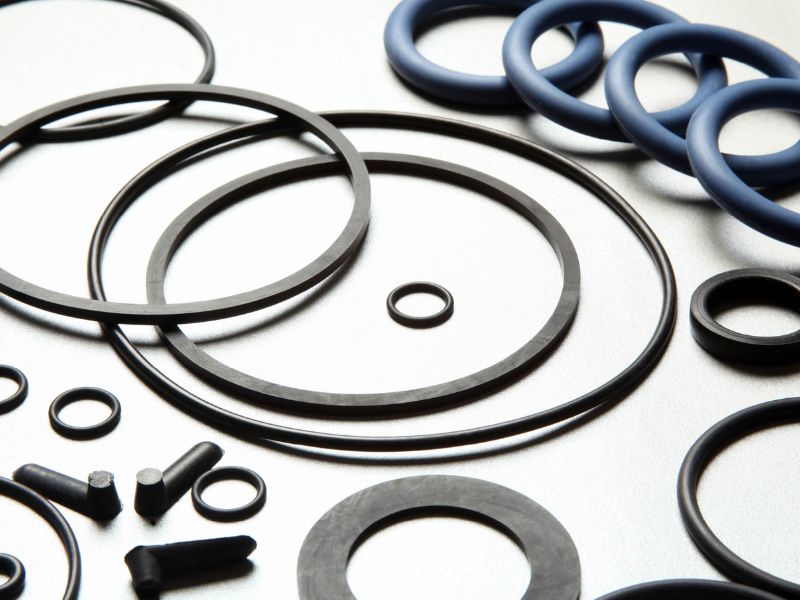
Industry Standards for O-Ring Sizing
O-ring sizes are standardized to ensure consistency and compatibility across different industries and manufacturers. Two major standards govern the sizing of O-rings:
AS568 Standard (Inch Sizes): The AS568 standard, developed by the Society of Automotive Engineers (SAE), defines inch-sized O-rings. It provides a comprehensive list of standardized O-ring sizes based on the inner diameter, outer diameter, and cross-sectional diameter. This standard is widely used in North America and in industries where inch-based measurements are prevalent.
ISO 3601 Standard (Metric Sizes): The ISO 3601 standard is the global metric counterpart to the AS568 standard. It specifies O-ring sizes in millimeters and is commonly used in international applications, especially in Europe and other metric-based regions.
How to Measure and Size O-rings
Tools Needed for Measurement
Accurate measurement of O-rings is essential to ensure a proper fit and reliable seal. To achieve precise measurements, the following tools are commonly used:
Calipers: Digital or dial calipers are essential for measuring the inner diameter (ID), outer diameter (OD), and cross-sectional diameter (CSD) of O-rings. They provide precise measurements down to fractions of a millimeter or inch, which is critical for ensuring the O-ring will fit correctly.
Cone Gauges: Cone gauges are used to quickly determine the size of an O-ring by placing it over a series of stepped cones with different diameters. This method is often used for quick identification of standard O-ring sizes.
Sizing Charts: Standard sizing charts can be used to cross-reference measurements with the standard AS568 or ISO 3601 sizes. These charts list O-ring dimensions and can help ensure the correct size is selected for replacement or new applications.
Step-by-Step Sizing Process
Measuring the Inner Diameter (ID):
Step 1: Place the O-ring on a flat, clean surface to ensure it is lying evenly and not twisted.
Step 2: Use calipers to measure the distance from one inner edge to the opposite inner edge, ensuring that the calipers are parallel to the flat surface.
Step 3: Record the inner diameter measurement. This is a critical dimension to ensure that the O-ring fits properly around the shaft or within the groove.
Measuring the Outer Diameter (OD):
Step 1: With the O-ring still lying flat on a surface, use the calipers to measure the total distance across the O-ring from one outer edge to the opposite outer edge.
Step 2: Ensure that the calipers are centered and not angled, as this can distort the measurement.
Step 3: Record the outer diameter measurement. This dimension ensures that the O-ring fits correctly within the housing or bore.
Measuring the Cross-Sectional Diameter (CSD):
Step 1: Gently pinch the O-ring between your fingers so that a small cross-section is exposed.
Step 2: Use the calipers to measure the thickness of the O-ring by placing the jaws of the calipers on opposite sides of the cross-section.
Step 3: Record the cross-sectional diameter measurement. This dimension is crucial for ensuring the O-ring compresses properly to form a reliable seal.
Common Mistakes to Avoid
Overstretching the O-Ring: When measuring the inner diameter, avoid stretching the O-ring beyond its original size. This can lead to inaccurate measurements and improper fit.
Incorrect Caliper Placement: Ensure that the calipers are positioned parallel to the O-ring and not at an angle. An angled measurement can give false readings for both the inner and outer diameters.
Measuring a Twisted O-Ring: Always lay the O-ring flat before measuring. If the O-ring is twisted or deformed during measurement, the readings may not reflect the actual dimensions.
Relying Solely on Visual Identification: Visual identification alone can be misleading, especially when dealing with similar-sized O-rings. Always use calipers or gauges for precise measurements rather than estimating based on appearance.
O-Ring Materials and How to Choose the Right One
Material Properties
When selecting an O-ring material, it is important to consider the specific properties of the material to ensure compatibility with the application. Key properties include:
Temperature Resistance: Different materials offer varying levels of heat and cold resistance. For example, silicone O-rings perform well in extreme temperatures (ranging from -60°C to 230°C), while nitrile (NBR) O-rings are better suited for moderate temperatures (-30°C to 120°C).
Chemical Compatibility: The ability to withstand exposure to chemicals without degrading is crucial, especially in applications involving oils, fuels, acids, or other harsh substances. For instance, Viton (FKM) O-rings are known for their excellent chemical resistance to oils and fuels, while EPDM O-rings are ideal for water, steam, and weather resistance.
Hardness (Durometer): The hardness of the O-ring, measured on the Shore A durometer scale, indicates the material’s resistance to deformation. Softer O-rings (50-60 Shore A) offer better sealing in low-pressure applications, while harder O-rings (70-90 Shore A) are more durable under high-pressure conditions.
Elasticity and Compression Set: Elasticity refers to the material’s ability to return to its original shape after being compressed. Compression set is the material’s ability to maintain a seal after long-term compression. Silicone, for example, has good elasticity, while nitrile offers a low compression set.
Applications of Different Materials
Nitrile (NBR): Nitrile O-rings are commonly used in automotive and industrial applications due to their resistance to oils, fuels, and petroleum-based fluids. They perform well in hydraulic and pneumatic systems but are not suitable for exposure to ozone or direct sunlight.
Silicone: Silicone O-rings are best suited for applications requiring extreme temperature tolerance, such as in aerospace or food processing. They are also commonly used in medical devices due to their biocompatibility and flexibility, though they are not ideal for dynamic sealing because of their relatively low tear strength.
EPDM: EPDM O-rings are excellent for water, steam, and weather-exposed applications. They are often found in HVAC systems, automotive brake systems, and outdoor equipment. However, EPDM should not be used in environments where it would come into contact with oils or fuels.
Viton (FKM): Viton O-rings excel in high-temperature and chemically aggressive environments, such as fuel handling systems, chemical processing, and oil and gas industries. They have excellent resistance to oils, fuels, acids, and solvents, making them highly versatile in harsh conditions.
PTFE (Teflon): PTFE O-rings are highly resistant to heat, chemicals, and wear, making them suitable for applications involving aggressive chemicals, high temperatures, or the need for non-reactive seals, such as in the pharmaceutical or food industries. Their low elasticity can be a drawback in dynamic sealing applications.
The Fitting Process
Proper installation of O-rings is critical to ensuring a reliable seal and preventing future problems such as leaks or component failure. Follow these guidelines to achieve the correct fit and avoid common issues.
Preparation Before Installation
Before installing an O-ring, thorough preparation is essential to ensure the longevity and effectiveness of the seal. Here are the key steps:
Surface Cleaning: Begin by cleaning both the O-ring and the groove or mating surfaces. Dirt, debris, or contaminants can prevent the O-ring from sealing properly. Use an appropriate cleaning solvent that is compatible with the O-ring material and the system fluids.
Inspection of the O-ring and Groove: Inspect the O-ring for any signs of damage, such as nicks, scratches, or visible wear. Check the groove or housing for imperfections or sharp edges that could damage the O-ring during installation. Ensure that the groove dimensions match the O-ring specifications.
Lubrication: Applying a thin layer of lubrication can ease the installation process and reduce friction, preventing the O-ring from twisting or pinching. Ensure the lubricant is compatible with both the O-ring material and the system’s fluids.
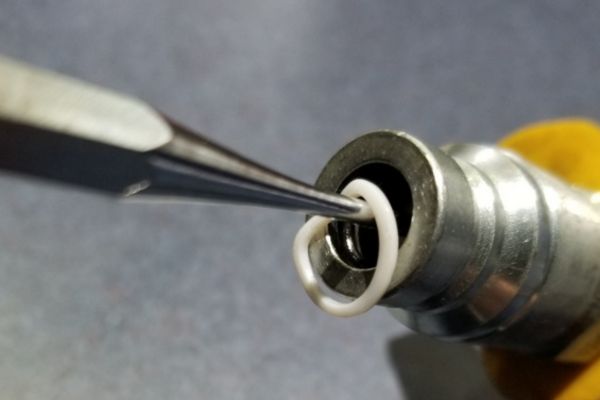
Correct Fitting Techniques
Static vs. Dynamic Fitting
Static Fitting: In static applications, the O-ring is installed between two stationary components, where it remains in place without movement. For static fitting, it’s essential to avoid over-compression that can lead to deformation or extrusion.
Dynamic Fitting: In dynamic applications, the O-ring must seal between components that move relative to one another, such as pistons or rotating shafts. Proper lubrication is especially important in these cases to reduce friction and wear. Ensure the O-ring is installed with the correct amount of stretch and without overstressing the material.
Rolling the O-Ring into Place
When fitting an O-ring into its groove or onto a shaft, avoid stretching or pulling the O-ring too aggressively. Instead, roll the O-ring gently into place using a circular motion. This method ensures even distribution of tension and prevents damage. For smaller O-rings, using your fingers to roll it on can be effective. For larger O-rings, using specialized tools like an O-ring cone may be helpful.
Using Tools
For hard-to-reach or complex installations, using the right tools can simplify the process and prevent damage. O-ring pick tools with rounded edges can be used to guide the O-ring into position without tearing it. Lubricants can be applied to make installation easier, while cone tools can help slide O-rings into tight spaces without overstretching them.
Lubrication Best Practices
Choosing the Right Lubricant: Lubrication helps reduce friction during installation and enhances the seal’s performance. The type of lubricant should be compatible with both the O-ring material and the system’s operating conditions:
Silicone Grease: Suitable for silicone O-rings and other elastomers, particularly in high-temperature applications.
Petroleum-Based Lubricants: Compatible with nitrile and Viton O-rings but should be avoided with EPDM due to degradation.
Water-Based Lubricants: Ideal for EPDM O-rings in applications involving water and steam.
Applying Lubrication: Apply only a thin, even layer of lubricant to the O-ring and the installation surfaces. Avoid excessive lubrication, as this can attract dirt or debris, potentially leading to seal failure.
Avoiding Installation Damage
Improper installation can lead to damage that compromises the O-ring’s effectiveness. Here are some tips to avoid common issues:
Twisting: O-rings can twist during installation, particularly in dynamic applications. This can lead to uneven wear and premature failure. Rolling the O-ring into place, rather than stretching it, helps prevent twisting.
Tearing: Stretching an O-ring excessively or forcing it over sharp edges can cause tears, especially in brittle or oversized O-rings. Always inspect the edges of the groove or shaft and use a lubricant to minimize friction.
Pinching: O-rings may pinch or become caught between mating surfaces during installation, leading to incomplete seals. Ensuring that the surfaces are smooth, well-lubricated, and properly aligned before tightening or sealing the components will help avoid pinching.
By following these steps and techniques, you can ensure that your O-rings are installed correctly, preventing common failures and extending the lifespan of the seal and the overall system. Proper fitting practices will minimize downtime, reduce maintenance costs, and ensure consistent, leak-free performance.
Conclusion
For optimal performance, it is crucial to prioritize accurate sizing and proper installation of O-rings in your operations. By taking the time to choose the right materials and ensuring a precise fit, you can significantly enhance the efficiency and reliability of your systems. If you require custom solutions or have questions about specific applications, don’t hesitate to reach out to experts who can guide you through the selection process.
FAQ
What is the most common cause of O-ring failure?
The most common causes of O-ring failure include incorrect sizing, improper installation, and material incompatibility with the operating environment.
How do I know if an O-ring is the correct size?
Measure the inner diameter (ID), outer diameter (OD), and cross-sectional diameter (CSD) using calipers, and compare the measurements to industry standards like AS568 or ISO 3601.
Can I reuse O-rings after removing them?
It’s generally not recommended to reuse O-rings, as they can be deformed, worn, or damaged during removal, which compromises their ability to seal effectively.
What type of lubricant should I use when installing O-rings?
The lubricant should be compatible with both the O-ring material and the system’s fluids. Common choices include silicone grease, petroleum-based lubricants, or water-based lubricants, depending on the material.
What are the signs of a failing O-ring?
Common signs include visible wear, cracks, leaks around the seal, or changes in the material, such as brittleness or swelling.
Can O-rings handle extreme temperatures?
Yes, but it depends on the material.