An O-ring is a circular elastomeric seal, crucial for preventing fluid or gas leakage in various hydraulic and sealing applications. Widely used in systems that require consistent pressure and containment, O-rings play a vital role in maintaining the efficiency and safety of machinery. Understanding the causes of O ring failure is essential for avoiding costly repairs, downtime, and potential system breakdowns.
Understanding O-ring Functions
Basic Purpose of O-rings
O-rings are essential components in both static and dynamic systems, primarily serving as seals to prevent the escape of fluids or gases. Their circular design allows them to be seated within a groove, where they compress and create a seal between two or more surfaces. In static applications, such as pipe connections or flanges, O-rings prevent leakage by maintaining constant pressure between stationary parts. In dynamic systems, such as hydraulic cylinders or moving pistons, O-rings help contain fluids or gases while allowing for movement. Their effectiveness ensures systems maintain proper pressure, prevent contamination, and operate efficiently without loss of performance or leaks.
Key Materials Used in O-rings
Different materials are used to manufacture O-rings, each chosen for its specific properties that suit various environmental conditions:
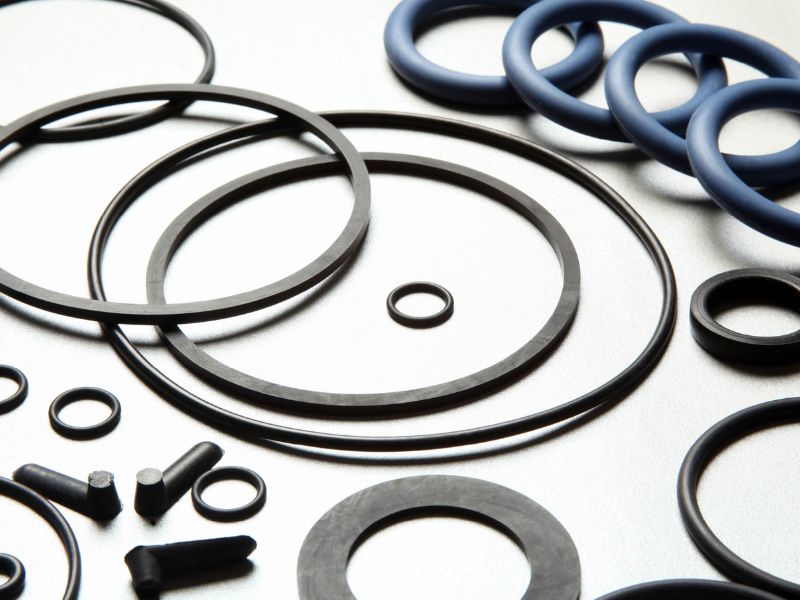
Nitrile (Buna-N): One of the most commonly used materials, Nitrile O-rings offer excellent resistance to oils, fuels, and many hydraulic fluids. They perform well in temperatures ranging from -40°C to 120°C, making them suitable for general industrial applications and automotive fuel systems.
Viton (FKM): Viton O-rings are highly resistant to high temperatures (up to 200°C) and various chemicals, including solvents, fuels, and acids. This makes them ideal for applications involving harsh environments, such as aerospace, automotive engines, and chemical processing.
Silicone: Silicone O-rings are known for their flexibility and excellent resistance to extreme temperatures, ranging from -60°C to 200°C. They are widely used in food processing, medical devices, and aerospace applications where both heat and low-temperature flexibility are critical.
Each of these materials offers specific benefits, ensuring that O-rings can function reliably in diverse environments, from high-pressure hydraulic systems to chemical exposure and extreme temperature conditions.
Common Applications of O-rings
O-rings are widely used across various industries, where their sealing capabilities are vital for system integrity:
Hydraulics: O-rings are critical in hydraulic systems to seal hydraulic cylinders, pumps, and valves. They prevent fluid leaks, ensuring the hydraulic system operates at optimal pressure.
Pneumatics: In pneumatic systems, O-rings prevent the escape of compressed air or gas. They are used in components such as cylinders, valves, and fittings, ensuring efficient operation of air-driven machinery.
Automotive: O-rings are integral in automotive applications, including engine seals, fuel systems, and transmission components. They ensure proper sealing in critical areas, preventing oil, coolant, and fuel leaks that could compromise vehicle performance.
Top Causes of O-ring Failure
Improper Installation
Explanation: Improper installation of O-rings is one of the most frequent causes of premature failure. During the installation process, mistakes such as twisting, stretching, or pinching the O-ring can introduce weak points in the material. These weak points compromise the O-ring’s ability to maintain an effective seal. For example, stretching the O-ring beyond its limits may permanently deform the material, while twisting or pinching it can create areas of stress concentration. This not only reduces the O-ring’s ability to function as a seal but also increases the risk of leaks or catastrophic system failure under operational conditions.
Common Symptoms: After installation, improperly installed O-rings often exhibit visible defects such as being distorted, overstretched, or showing cuts. These issues can result in uneven compression across the sealing surface, leading to poor sealing performance. Symptoms of improper installation may manifest as fluid or gas leaks, which can be costly and dangerous in high-pressure systems.
How to Avoid: To prevent installation-related failures, it’s essential to take a careful and methodical approach. O-rings should be installed without unnecessary stress or distortion. Tools such as O-ring picks, cones, and lubricants should be employed to facilitate proper positioning. The use of a lubricant reduces friction during installation, making it easier to guide the O-ring into place without stretching or damaging it. Additionally, using the correct groove size and ensuring the O-ring is properly seated are critical steps to avoid installation errors.
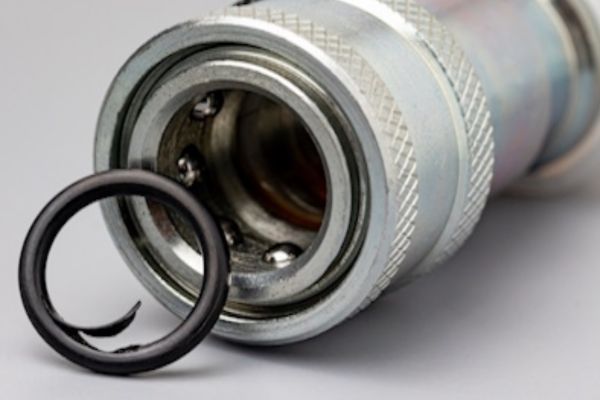
Excessive Temperature Exposure
Explanation: O-rings are sensitive to temperature extremes, and operating outside their specified temperature range can lead to a loss of sealing integrity. Exposure to high temperatures can cause O-ring materials to degrade rapidly by hardening, cracking, or even melting. This degradation reduces the O-ring’s flexibility and ability to conform to sealing surfaces. Conversely, exposure to extremely low temperatures can cause O-rings to become brittle, increasing the likelihood of cracking or fracturing under mechanical stress.
Common Symptoms: Common symptoms of temperature-induced failure include cracked or hardened O-rings, which are indicative of thermal damage. In high-temperature environments, the O-ring may lose its elasticity and become brittle, leading to cracks or surface degradation. In cold conditions, the O-ring may become stiff and fracture easily, particularly during dynamic movements.
How to Avoid: To prevent temperature-related failures, it is vital to select O-rings made from materials that are specifically rated for the temperature range of the application. For high-temperature applications, materials such as Viton or Silicone are excellent choices due to their superior heat resistance. For low-temperature environments, materials like Nitrile or EPDM are better suited because of their ability to retain flexibility in colder conditions. Ensuring the O-ring operates within its optimal temperature range will extend its life and maintain system integrity.
Chemical Degradation
Explanation: Chemical degradation occurs when O-rings are exposed to incompatible chemicals that attack and break down the material. This exposure can cause the O-ring to swell, soften, crack, or even completely disintegrate over time. Chemical degradation is a serious concern in applications where O-rings are in constant contact with aggressive substances such as acids, oils, solvents, or hydraulic fluids. If the O-ring material is not chemically compatible with these substances, it will lose its ability to form an effective seal, leading to system failure.
Common Symptoms: The most common symptoms of chemical degradation include swelling, tackiness, softening, and cracking of the O-ring material. In extreme cases, the O-ring may lose its shape entirely, becoming gummy or disintegrating into fragments. These symptoms indicate that the O-ring material is breaking down due to exposure to harmful chemicals.
How to Avoid: The key to avoiding chemical degradation is to select O-ring materials that are compatible with the chemicals in the system. This can be achieved by consulting chemical resistance charts or working directly with O-ring manufacturers to ensure that the correct material is chosen for the application. For example, Viton is highly resistant to a wide range of chemicals, including oils, fuels, and solvents, making it a popular choice in chemical processing industries. Nitrile and EPDM also offer resistance to various chemicals, but their suitability depends on the specific fluids they will encounter.
Pressure Variations
Explanation: O-rings can fail due to excessive or fluctuating pressures within a system, which can lead to extrusion, splitting, or deformation of the O-ring material. In dynamic systems where pressure changes frequently, the O-ring may be subjected to forces beyond its design limits, causing it to extrude out of its groove or split under stress. Excessive pressure can also cause the O-ring to flatten and lose its sealing capabilities, particularly if the groove is not properly designed to support the O-ring under high-pressure conditions.
Common Symptoms: O-rings affected by pressure variations typically show signs of extrusion, where the O-ring material is pushed out of its groove, leading to seal failure. Other symptoms include splitting or flattening of the O-ring, indicating that the material is being subjected to forces beyond its pressure tolerance.
How to Avoid: To prevent pressure-related failures, it’s essential to use backup rings to provide additional support to the O-ring in high-pressure applications. Backup rings help prevent extrusion by keeping the O-ring in place and maintaining its shape under pressure. Additionally, selecting O-rings that are rated for the specific pressure range of the system and ensuring proper groove design can minimize the risk of extrusion and splitting.
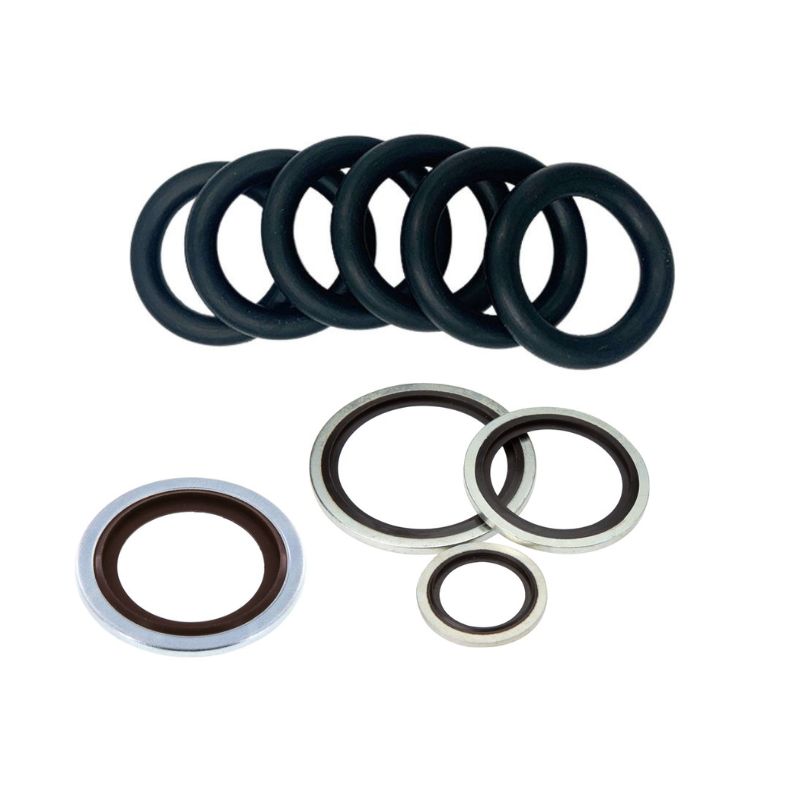
Abrasion and Wear
Explanation: In dynamic applications where O-rings are subjected to constant movement, friction between the O-ring and the sealing surfaces can cause mechanical wear and abrasion. Over time, this wear can degrade the O-ring material, leading to cuts, flattening, or surface damage. Abrasion is particularly problematic in systems where the O-ring is exposed to repeated motion or rough surfaces, resulting in gradual loss of sealing effectiveness and eventual failure.
Common Symptoms: Symptoms of abrasion and wear include visible surface damage on the O-ring, such as cuts, gouges, or flattened areas. As the O-ring wears down, leaks may develop, and the O-ring may lose its ability to maintain an effective seal, particularly in dynamic applications where continuous movement occurs.
How to Avoid: To reduce the risk of abrasion and wear, proper lubrication should be applied during both installation and operation. Lubrication helps to reduce friction between the O-ring and the mating surfaces, thereby extending the O-ring’s lifespan. Additionally, selecting O-rings made from abrasion-resistant materials such as polyurethane or PTFE can help minimize wear in high-friction environments. Ensuring that the sealing surfaces are smooth and free of debris can also prevent excessive wear.
Compression Set
Explanation: Compression set is a common failure mode for O-rings that have been compressed for extended periods. Over time, the O-ring may lose its elasticity and fail to return to its original shape after being compressed. This permanent deformation reduces the O-ring’s ability to form an effective seal, as it no longer fills the gap between the mating surfaces. Compression set is often exacerbated by high temperatures and pressure, which accelerate the O-ring’s loss of elasticity.
Common Symptoms: O-rings that exhibit a loss of elasticity or have permanently flattened shapes are showing signs of compression set. These O-rings may no longer be able to maintain an effective seal, leading to leaks and decreased system performance.
How to Avoid: To minimize the risk of compression set, it is important to choose O-ring materials that are resistant to permanent deformation, such as EPDM or silicone. Regular maintenance and periodic replacement of O-rings can also help prevent compression sets from causing failure. In addition, using the correct O-ring size and ensuring that the system operates within the O-ring’s temperature and pressure limits will extend its service life.
Poor Surface Finish
Explanation: The quality of the surfaces that the O-ring seals against plays a critical role in its performance. Rough or improperly finished surfaces can create abrasive contact points that damage the O-ring over time. Sharp edges, burrs, or other surface imperfections can cut into the O-ring, compromising its ability to form a tight seal. Poor surface finish is often a result of inadequate machining or surface preparation during the manufacturing process.
Common Symptoms: O-rings that have been damaged by poor surface finishes typically show signs of scratches, cuts, or gouges on their surface. These defects reduce the O-ring’s ability to create a consistent seal, leading to leaks or premature failure.
How to Avoid: To prevent surface finish-related failures, it is crucial to ensure that all mating surfaces are smooth, free of sharp edges, and properly finished. This can be achieved by implementing high-quality machining and surface preparation practices. Regular inspection of the sealing surfaces during installation and maintenance can help identify any imperfections that could damage the O-ring.
How to Avoid O-ring Fail
Selecting the Right O-ring Material
The selection of the correct O-ring material is critical for ensuring long-term reliability and performance in any application. O-ring materials must be matched to the environmental conditions they will face, including temperature ranges, pressure levels, and exposure to chemicals. Failure to select the appropriate material can result in premature wear, chemical degradation, or even catastrophic system failure. For instance, selecting a material like Viton for high-temperature, chemical-rich environments can prevent failure, whereas Nitrile might be more suitable for oil-based systems under moderate temperatures.
Below is a simple guide outlining some common O-ring materials, their properties, and ideal applications:
Material | Temperature Range | Chemical Resistance | Recommended Applications |
Nitrile(Buna- N) | -40°℃ to 120℃ | Excellent resistance to oils and fuels | Food processing, medical devices, high/low temperature applications |
Viton (FKM) | -15℃ to 200℃ | Automotive, hydraulic systems | High-temperature environments, chemical processing |
Silicone | -60°℃ to 200℃ | Moderate chemical resistance | Resistant to water, steam, and some chemicals |
EPDM | -50°℃ to 150℃ | Water systems, outdoor environments | Water systems,outdoor environments |
Polyurethane | -60°℃ to 80℃ | High abrasion resistance | Dynamic applications with high wear potential |
This chart can help users make informed decisions about which material is best suited for their application, reducing the likelihood of failure.
Proper Installation Techniques
Step-by-Step Installation Process: Proper installation is key to maximizing the lifespan of an O-ring. The following steps can help ensure a successful installation:
Clean the Groove: Make sure the groove is clean, free from debris, and free of any sharp edges that could damage the O-ring.
Apply Lubricant: Use a compatible lubricant to reduce friction during installation. The lubricant also helps prevent twisting or overstretching.
Install Carefully: Position the O-ring carefully, ensuring it is not stretched excessively or twisted as it is placed into the groove. The O-ring should fit snugly without distortion.
Align Surfaces: If sealing between two surfaces, ensure proper alignment before tightening to avoid pinching or cutting the O-ring.
Tools and Equipment: Utilizing the right tools is essential for a safe and damage-free installation. These tools include:
O-ring Picks: To help position the O-ring without causing nicks or tears.
Lubricants: To reduce friction and protect the O-ring during installation.
Installation Cones: These tools help slide the O-ring into place without stretching or twisting.
Proper installation practices minimize the chances of damaging the O-ring during assembly, which is one of the leading causes of premature failure.
Regular Maintenance and Inspection
Routine Maintenance Checklist: O-rings are subject to wear over time, especially in dynamic applications. Regular maintenance is vital to prevent unexpected failures. Here’s a basic maintenance checklist:
Check for Wear: Regularly inspect O-rings for signs of wear such as cracks, flattening, or surface degradation.
Replace as Needed: O-rings that show signs of wear or damage should be replaced immediately to prevent leakage.
Lubricate Moving Parts: Ensure all moving parts that interact with O-rings are properly lubricated to reduce friction and extend O-ring life.
Monitor System Conditions: Keep track of temperature, pressure, and chemical exposure to ensure they remain within the O-ring’s rated limits.
Inspection Guidelines: During routine inspections, look for the following indicators that an O-ring may be nearing failure:
Changes in Shape: Flattened or deformed O-rings can indicate a compression set.
Surface Cracks or Tears: These are signs of wear, improper installation, or exposure to harsh environmental conditions.
Swelling or Softening: This could suggest chemical incompatibility and the need for material reassessment.
Regular inspections help identify early warning signs of Oring failure, allowing for timely replacements before more severe problems arise.
Ensuring Correct System Design
Importance of System Design: The design of the system in which the O-ring operates is crucial to its longevity and performance. Factors such as groove dimensions, pressure balance, and temperature control all contribute to how well the O-ring will perform. A poorly designed groove can place undue stress on the O-ring, leading to compression set or extrusion, while fluctuating pressures and temperatures can hasten O-ring wear.
Groove Design: Ensure that groove dimensions allow the O-ring to compress evenly without being crushed or overly stretched.
Pressure and Temperature Management: Systems should be designed to avoid extreme pressure spikes or temperature fluctuations that can degrade O-ring materials over time.
Conclusion
If you’re unsure about the best O-ring material or design for your system, consult with O-ring experts who can guide you in selecting the appropriate materials and ensuring proper installation and maintenance procedures. Additionally, consider reviewing your current system design to ensure it supports O-ring performance under specific operational conditions. Investing in high-quality O-rings tailored to your application can prevent costly downtime and improve system reliability in the long run.
FAQ
What is an O-ring used for?
O-rings are primarily used for sealing purposes in both static and dynamic systems to prevent the leakage of fluids or gases.
What materials are O-rings made from?
O-rings are made from various materials, including Nitrile (Buna-N), Viton (FKM), Silicone, EPDM, and Polyurethane, each suited for different environmental conditions.
How do I choose the right O-ring material?
Select the O-ring material based on your application’s temperature range, pressure levels, and exposure to chemicals to ensure optimal performance.
What are the common signs of O ring failure?
Common signs of O-ring failure include cracking, deformation, swelling, surface cuts, and extrusion, often leading to leaks and system inefficiency.
How can I prevent O ring failure?
Prevent O ring failure by choosing the correct material, installing the O-ring properly, using the right tools, and performing regular maintenance and inspections.
When should I replace my O-rings?
O-rings should be replaced whenever there are visible signs of wear, damage, or loss of elasticity, or as part of a scheduled maintenance routine to prevent system failures.