The hydraulic system is pressurized, the fittings are secure, but your operation grinds to a halt. The culprit isn’t a burst from pressure, but a slow, grinding failure from the outside-in, a worn-out hose cover that allowed the environment to destroy your investment.
The best material for a hose cover is the one that directly counters the specific threats of your environment. This ranges from standard synthetic rubber for general use, to advanced proprietary tough-rubber compounds, high-performance thermoplastics like polyurethane, or essential external guards for extreme physical abuse.

The Foundation: What Is the Standard Synthetic Rubber Cover?
You select a standard black rubber hose, the most common type available. You assume “rubber is rubber” and that it’s tough enough for any job, only to see it wear out surprisingly fast when put to work in a demanding application, forcing you into a cycle of frequent replacement.
A standard hose cover is typically a blend of synthetic rubbers, most commonly Neoprene (CR) or Styrene-Butadiene Rubber (SBR). It provides a good baseline of protection against oil, weather, and moderate abrasion, and is usually certified to MSHA flame-resistance standards, making it the right choice for many controlled environments.
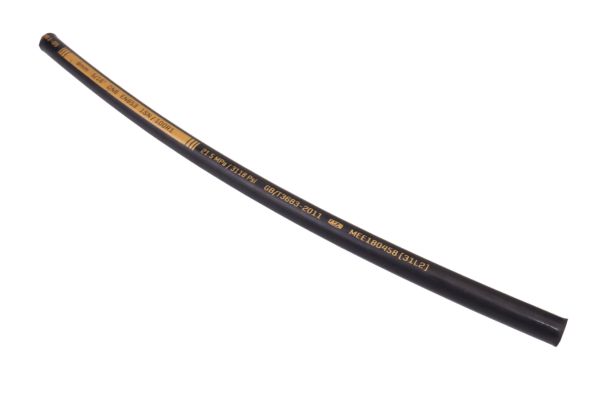
The standard black rubber cover is the benchmark of the hydraulics industry. It’s a well-engineered, cost-effective solution that performs admirably in a huge range of applications. But to make an expert decision, you need to understand what’s actually in it and what it’s designed to do.
The Key Materials in a Standard Cover
The term “rubber” is very general. The specific compounds used are chosen for a balance of properties.
- Neoprene (CR – Chloroprene Rubber): This is the industry workhorse. I see it specified more than any other compound for standard covers. Its popularity comes from its excellent balance. It has good resistance to oils, ozone from the atmosphere, heat, and weathering. Critically, it also has inherent flame-retardant properties and flexes well without cracking, making it a very reliable all-around choice.
- SBR (Styrene-Butadiene Rubber): This is the same type of rubber used in many car tires. It’s known for its toughness and good abrasion resistance. Often, SBR is blended with Neoprene to enhance the cover’s overall durability and manage costs without sacrificing key performance attributes.
- Nitrile (NBR – Nitrile Butadiene Rubber): While Nitrile is the king of materials for the inner tube due to its superb resistance to petroleum-based hydraulic fluids, it is sometimes used as a component in covers for environments where the hose exterior is constantly saturated with oil.
The Critical Importance of the MSHA Rating
On the layline of most quality standard hoses, you will see the letters “MSHA”. This is not a marketing term; it is a critical safety certification from the United States Mine Safety and Health Administration. To earn this rating, the hose cover must pass a stringent test where it is exposed to a direct flame for a set period. Once the flame is removed, the cover must self-extinguish within one minute. While it was designed for the obvious fire risks in underground coal mining, this certification has become a global benchmark for industrial safety. For my clients who operate equipment in enclosed spaces, near engine manifolds, or around welding and hot work, an MSHA-rated cover provides a crucial layer of fire protection.
When Is a “Standard” Cover the Correct Choice?
A standard cover is the right tool for the job when the application does not involve aggressive abrasion. This includes stationary industrial machinery, well-protected hose routing on mobile equipment where the hose does not rub against components, and general workshop use. It provides a highly reliable and cost-effective solution for a majority of hydraulic systems worldwide. The key is to honestly assess if your application falls into this “moderate” category. If it doesn’t, you need to upgrade.
The Upgrade: What Exactly Makes a “Tough Cover” Superior?
You see hoses marketed with names like “Tough Cover,” “Abrasion Master,” or “Super Shield.” It’s easy to be skeptical and wonder if you’re just paying more for a fancy name. Is there a measurable, scientific difference that justifies the higher price tag?
A “tough cover” is not a marketing gimmick; it is a hose with an outer layer made from a proprietary, engineered rubber compound. This advanced material features higher density and superior polymer cross-linking, resulting in a dramatic, measurable increase in abrasion resistance—often 50 to 500 times that of a standard rubber cover.
This category of covers is where leading manufacturers truly differentiate themselves, and it’s a solution I frequently recommend to customers in forestry, mining, and construction. The performance leap is real and is rooted in advanced material science.
The Science Behind Enhanced Durability
The secret to a tough cover lies in its chemistry and structure. It’s not just “thicker rubber.” The designers have manipulated the rubber formulation at a molecular level.
- Advanced Polymers: They start with higher-grade base polymers that inherently have greater toughness.
- Specialized Fillers: The type and amount of “filler,” like carbon black, are optimized. Different grades of carbon black create different properties. For tough covers, they use specific types that form a stronger bond with the polymer chains, creating a much more cohesive and tear-resistant material.
- Optimized Vulcanization: The curing process, known as vulcanization, is refined to create a greater number of cross-links between the polymer chains. You can imagine it like adding many more rungs to a ladder, making the entire structure far more rigid and resistant to being torn apart by abrasive forces.
How We Measure the Difference: The ISO 6945 Test
The industry standard for quantifying abrasion resistance is the ISO 6945 test. It’s a straightforward but brutal test. A section of the pressurized hose is mounted to a reciprocating test rig. It is then dragged back and forth over a standardized abrasive platen (like a grinding surface) under a specified force. The test measures the number of cycles it takes to wear through the cover and expose the first steel reinforcement wire. The results are often staggering.
Cover Type | ISO 6945 Test Cycles (Illustrative) | Relative Lifespan | Primary Use Case |
Standard Rubber | 50,000 | 1x | Moderate, non-rubbing applications |
“Tough” Cover | 5,000,000 | 100x | High-abrasion, constant rubbing |
“Super Tough” Cover | 25,000,000+ | 500x+ | Extreme abrasion (quarries, mining) |
The High-Performance Option: When Should You Specify a Thermoplastic Cover?
You find that standard rubber hoses are too heavy and bulky for your equipment. Or perhaps they are leaving unsightly black scuff marks on your factory floor or finished products. You need a solution that is cleaner, lighter, and even tougher than rubber.
A thermoplastic cover, most commonly made from Polyurethane (PU), is the superior choice for these applications. It offers the highest level of abrasion resistance of any integrated cover material, is exceptionally lightweight, completely non-marking, and has a very low coefficient of friction, allowing it to slide instead of tear.
Thermoplastic hoses occupy a high-performance niche and are a clear example of using advanced polymer technology to solve specific industrial problems. They are fundamentally different from rubber hoses and offer a compelling package of benefits.
The Unique Material Properties of Polyurethane
Polyurethane is a thermoplastic, meaning it can be melted and reformed, unlike rubber, which is a thermoset. This allows for a different type of construction.
- Extreme Toughness: PU is known for its exceptional resistance to cutting, tearing, and abrasion. It’s the same material family used to make skateboard wheels, chosen for its ability to withstand incredible abuse.
- Low Coefficient of Friction: This is a key advantage. A PU cover is very “slippery.” When it rubs against a surface, it tends to slide easily rather than gripping and tearing like some rubber compounds can. This makes it ideal for bundling multiple hoses together, as they will glide past each other.
- Bonded Construction: In many thermoplastic hoses, the cover, reinforcement layer (often a synthetic fiber like Kevlar or polyester), and inner tube are chemically or thermally bonded together during manufacturing. This creates a very slim, lightweight, and unified hose structure that resists delamination.
Key Applications Where Thermoplastic Excels
I recommend polyurethane-covered hoses to my clients when they face these specific challenges:
- Over-the-Sheave Applications: On cranes and aerial work platforms (AWPs), hoses run over pulleys (sheaves). The low friction and high abrasion resistance of PU make it last much longer in this demanding setup.
- Clean Environments: In food processing, pharmaceutical manufacturing, or on factory floors, a non-marking hose is essential to prevent product contamination or facility damage.
- Constant Sun Exposure: Polyurethane has outstanding resistance to UV radiation and ozone. While rubber can become brittle and crack over years of sun exposure, PU remains stable and flexible. This is a huge advantage for equipment that works outdoors all day.
The Niche Solution: Do Textile Covers Have a Place in Modern Industry?
You’ve encountered a hose with a woven, fabric-like cover. It might appear less robust than a thick rubber hose, making you wonder if it is an outdated technology or if it serves a specific, valuable purpose in modern industry.
Yes, textile-braided covers, typically made from high-strength polyester or other synthetic fibers, remain an essential solution for specialty hoses. They are specified when extreme flexibility, light weight, and a very tight bend radius are more critical than impact resistance.
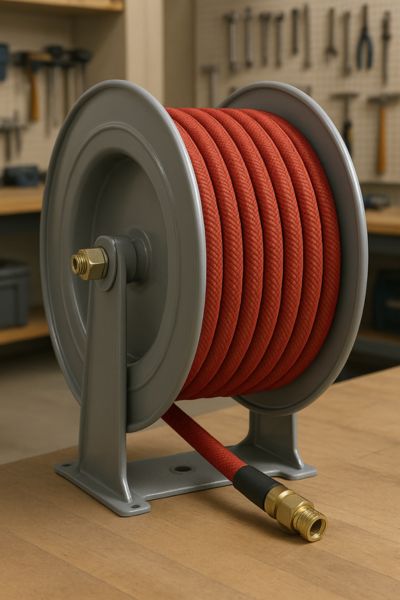
While you won’t find a textile cover on a high-pressure excavator line, they are the perfect choice for a variety of other critical tasks. Their construction is entirely different from an extruded rubber or thermoplastic cover.
Construction and Materials
The cover is formed by braiding a tight sleeve of synthetic fabric directly over the hose’s reinforcement layer.
- Polyester: This is the most common material. It is incredibly strong for its weight, has very little stretch, and is highly resistant to moisture, mildew, and many chemicals.
- Impregnation: The textile braid is often impregnated with a rubber or polymer compound. This doesn’t form a solid layer but helps to improve abrasion resistance and protect the fibers from dirt and oil.
- Color: The fibers can be dyed before braiding, providing a simple and permanent method for color-coding lines for safety and quick identification (e.g., for different gases or fluids).
Where Flexibility is King
The primary reason to choose a textile cover is flexibility. Because it is not a solid, thick layer of rubber, the hose can be bent into a much tighter radius without kinking or putting undue stress on the internal structure. This makes it the ideal choice for:
- Hose Reels: For compressed air or low-pressure fluid delivery in workshops.
- LPG and Fuel Gas Hoses: Where flexibility for connection and routing is paramount.
- Low-Pressure Return lines: In some hydraulic systems.
Understanding the Limitations
It’s crucial to use these hoses correctly. A textile cover offers good resistance to rubbing abrasion but provides very little protection against sharp objects or impacts. A sharp piece of metal can easily snag and cut the fibers. They are a precision tool for specific applications, not a heavy-duty solution for rugged environments.
Beyond the Cover: When Is External Protection Absolutely Necessary?
You have already specified the toughest hose available for your machine. But the working environment is so brutal—with falling rocks, crushing forces, and intense heat—that even this premium cover is being overwhelmed and destroyed.
When the environmental threat level exceeds the capabilities of any integrated hose cover, external protection becomes non-negotiable. These sacrificial guards, such as nylon sleeves, plastic spiral guards, and fire sleeves, provide a heavy-duty layer of defense against physical and thermal abuse.
Smart operators and engineers know that sometimes, the hose itself is only part of the system. I always tell my clients in the toughest industries, like demolition and steel manufacturing, that they must think of hose protection as a separate, essential component.
The Sleeve Solution: Textile and Nylon Guards
These are flexible woven tubes that are slid over the hose before the fittings are crimped on.
- Nylon Sleeves: These flat-woven or tubular sleeves act like a durable jacket for the hose. They provide an excellent additional layer of rubbing abrasion resistance and are perfect for bundling hoses together to prevent hose-on-hose friction.
- Burst Containment: Some high-strength textile sleeves are designed to contain the energy and fluid of a hose burst (up to a certain pressure), significantly enhancing operator safety.
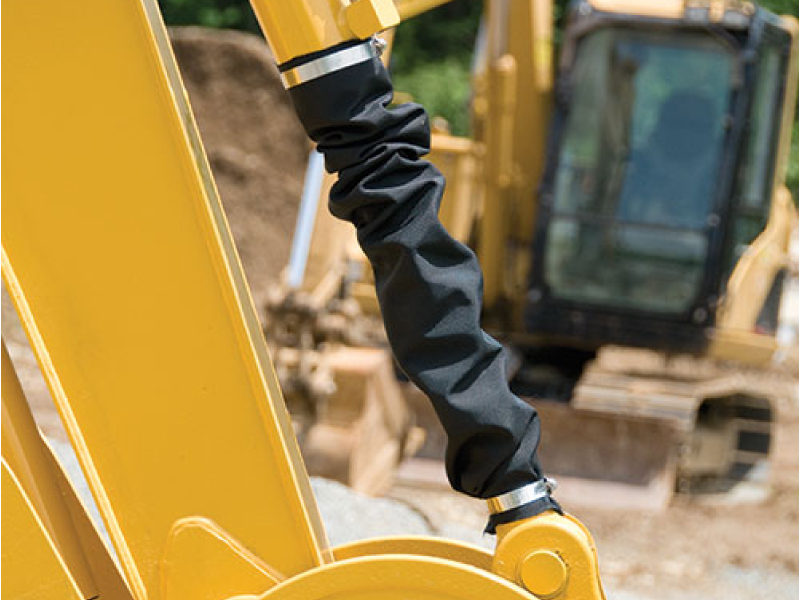
The Armor Solution: Plastic and Metal Spiral Guards
This is the next level of physical protection.
- Plastic Spiral Guard: A hard, durable plastic strip is wrapped around the hose. This is the go-to solution for deflecting impacts and preventing crushing. It creates a standoff between the hose and any abrasive or impacting surface. It is essential for hydraulic lines on excavator booms, rock drills, and forestry equipment.
- Metal Spiral Guards: For even more extreme applications, interlocking steel spring guards are available. They provide the highest level of protection against crushing and cutting.
The Thermal Solution: Silicone-Coated Fire Sleeves
For applications involving extreme heat, a fire sleeve is critical. It is a thick sleeve of braided fiberglass, coated with a layer of orange silicone rubber. Its purpose is threefold:
- Radiant Heat: It insulates the hose from the intense radiant heat found near furnaces or molten metal.
- Molten Splash: The silicone coating sheds splashes of molten steel or aluminum, which would instantly burn through a standard hose.
- Flame Impingement: It can withstand short-term direct exposure to flame, giving safety systems time to activate.
The Final Decision: How Do You Choose the Right Cover System?
With a clear understanding of all the options, from standard covers to external armor, the final step can feel daunting. How do you select the most effective and economical solution without paying for protection you don’t need, or worse, choosing too little and experiencing another failure?
The optimal choice comes from a simple, systematic audit of your application. By clearly identifying the primary threats, analyzing the true cost of failure, and consulting with a knowledgeable supplier, you can engineer a protection system that precisely matches your needs and maximizes your equipment’s uptime.
Making the right choice is a process of logical elimination. I walk my customers through these stages to build the perfect specification.
Your 3-Step Application Audit
- Threat Assessment: Be specific. Is the threat constant, light rubbing against a smooth frame? Is it intermittent, heavy impact on rocks? Is it a combination? Rate the severity of abrasion, impact, heat, and UV exposure on a scale of 1 to 5.
- Consequence Analysis: What is the real cost of a failure on this specific hose line? Calculate the cost of lost production per hour of downtime, the cost of spilled hydraulic fluid, the labor hours to replace the hose, and any potential safety risks. A high-consequence failure justifies a higher investment in protection.
- Solution Mapping: Now, map your findings. An application with a high abrasion score but low impact score points to a tough cover or PU hose. An application with high impact and abrasion scores points to a tough cover hose plus a spiral guard. A high heat score immediately points to a fire sleeve.
Communicating Your Needs for the Best Result
When you reach out to a supplier like us at Topa, being prepared with this information allows us to help you much more effectively. Instead of asking for “a 1/2-inch hose,” you can say, “I need a 1/2-inch hose for the boom arm of a rock drill. It faces severe impact and abrasion. The cost of downtime is about $500 per hour.” This immediately tells me that we should be discussing a premium tough-cover hose combined with a heavy-duty spiral guard. It becomes a collaborative, problem-solving conversation.
The Partnership Advantage
This is the core of our business model. We don’t just sell parts; we provide solutions. Our experience across dozens of industries and countries allows us to recognize these patterns of failure and recommend proven protection strategies. Our ability to supply both the high-performance hose and the full range of external guards makes us a one-stop source for building a truly resilient hydraulic system.
Conclusion
The hose cover is not just a cosmetic layer; it is a critical component of your equipment’s reliability. By moving beyond a one-size-fits-all approach, you can engineer a hose system that thrives. If you need customized hydraulic hoses, contact Topa and we can provide drawings and material reports!