Imagine a hydraulic hose on your machine suddenly exploding. A violent, loud rupture releases high-pressure fluid everywhere, bringing your entire operation to a dangerous and immediate halt.
Burst pressure is the laboratory-tested pressure at which a new hydraulic hose will physically rupture. It’s a critical quality control metric used by manufacturers to calculate the hose’s safe Maximum Allowable Working Pressure, almost always by dividing the burst pressure by four.
When I talk to clients, from engineers in the USA to workshop owners in the Philippines, many see the numbers on a hose and might not grasp the life-or-death difference between “working pressure” and “burst pressure.” This isn’t just technical jargon for a catalog. The burst pressure is the ultimate strength of the hose, a value determined by literally destroying it. It is the foundation upon which your safety is built. Understanding this single concept separates a responsible operator from someone taking a huge, unnecessary risk. At Topa, we believe empowering you with this knowledge is a core part of our job, ensuring you can run your equipment safely and efficiently.
How is Burst Pressure Different from Working Pressure?
You see two pressure ratings for a hose. Choosing the wrong one for your calculations could lead to a catastrophic failure under normal operating conditions.
Working pressure is the maximum pressure for daily use—your “speed limit.” Burst pressure is the hose’s failure point found in a lab. You operate at working pressure; you never go near burst pressure. The difference is your safety margin.
This is the most fundamental distinction in hydraulic hose safety. Confusing these two values is one of the most dangerous mistakes a person can make when selecting or replacing a hose. One number is your guide for everyday operations; the other is a laboratory benchmark representing total failure. Treating them as interchangeable is a direct path to an accident.
The Critical Role of Working Pressure (W.P. or M.A.W.P.)
Maximum Allowable Working Pressure (M.A.W.P.), often shortened to Working Pressure (W.P.), is the most important number for you, the user. It is the maximum continuous pressure that the hose assembly is designed to handle safely throughout its service life. When you are designing a system or replacing a hose, you must ensure the hose’s W.P. is equal to or greater than the maximum operating pressure of your system, including any pressure relief valve settings. Think of it as the load limit on a bridge; for safety, you never load the bridge to its breaking point, only to its rated capacity.
Burst Pressure as a Laboratory Benchmark
Burst pressure is a theoretical value from the user’s perspective. It is determined by taking a new hose sample, pressurizing it to extreme levels in a controlled environment until it physically breaks, and recording the pressure at that moment. This is a destructive test performed by manufacturers like us for two reasons: quality control and safety calculation. It verifies that the hose construction (the tube, the wire reinforcement, the cover) meets the required strength. It is a testament to the hose’s ultimate strength but is not a number you should ever try to reach in the field.
What is the 4:1 Safety Factor and Why is it the Industry Standard?
A 4-to-1 safety factor seems excessive. Does this just add unnecessary complexity and cost to the hose, or is it there for a critical reason that protects you every day?
The 4:1 safety factor is a non-negotiable industry standard. It means the working pressure is only 25% of the hose’s minimum burst pressure. This crucial buffer accounts for unexpected pressure spikes, hose aging, and real-world wear and tear.
When customers, especially the very price-sensitive ones, ask me why a a hose rated for 3,000 PSI needs to be strong enough to handle 12,000 PSI, I explain that this safety margin is not about over-engineering; it’s about survival. A hydraulic system in the real world is not a gentle, static laboratory environment. It’s a violent, dynamic place. This 4:1 ratio, mandated by international standards bodies like the Society of Automotive Engineers (SAE) and European Norm (EN), is what keeps the system safe under these chaotic conditions.
Accounting for Dynamic Pressure Spikes
Hydraulic systems experience something called hydraulic shock, or pressure transients. When a valve closes quickly or a heavy cylinder stops moving abruptly, the momentum of the moving oil creates a powerful pressure wave. These spikes are incredibly fast, often too fast for a standard pressure gauge or relief valve to react to. The pressure can momentarily jump to two or three times the normal working pressure. The hose’s 4:1 safety factor is designed to absorb and contain these violent but brief events without rupturing, protecting the entire system from damage.
Compensating for Real-World Conditions
A hose’s burst pressure rating is determined when it is brand new. However, from the moment it is installed, its strength begins to degrade. It is bent into position, it vibrates with the machine, it might rub against other components, and it is exposed to heat and temperature cycles. Each of these factors minutely damages the hose structure and reduces its original strength. The 4:1 safety factor ensures that even after months or years of service, when the hose’s burst pressure has been reduced by wear and tear, it still has more than enough strength to handle the normal working pressure safely.
How Do Manufacturers Actually Test for Burst Pressure?
You buy a hose based on its burst pressure rating, but how is that number actually determined? It’s a key part of your safety, but the process can seem like a mystery.
Manufacturers use a destructive process called a burst test. A sample hose from a production run is securely crimped, placed in a sealed test chamber, filled with water, and then pressure is steadily increased until it ruptures. The pressure at that instant is the burst pressure.
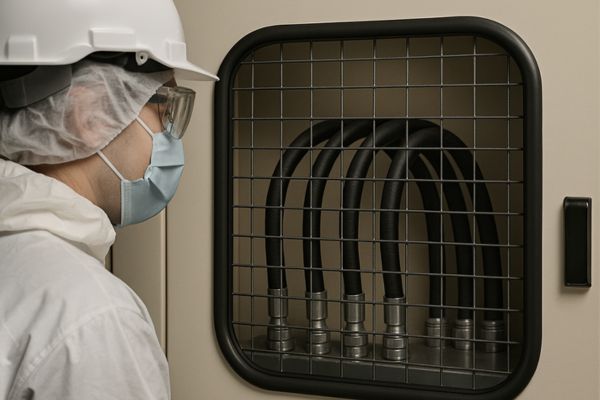
As a supplier that presents as a manufacturer, we understand the importance of this process intimately. Our long-term factory partners perform these tests constantly. It is the ultimate proof of quality. When a customer from a quality-focused region like the UK or Australia asks about our quality control, explaining our rigorous burst testing protocol provides them with tangible assurance. The test is methodical and designed for maximum safety and accuracy.
The Burst Test Procedure
The process follows strict international standards.
- Sample Selection: A random sample hose is taken directly from a large production batch.
- Assembly: The hose is cut to a standard length, and the correct fittings (like ours at Topa) are crimped onto the ends using specified crimp dimensions.
- Safety Chamber: The hose assembly is placed inside a heavy, reinforced steel chamber to contain the violent rupture.
- Pressurization: The hose is filled with water, not air. Water is used because it is nearly incompressible. If the hose bursts, the pressure dissipates instantly. If air were used, its rapid expansion upon rupture would create a dangerous explosion.
- Ramping Up: A special pump increases the water pressure inside the hose at a steady, controlled rate.
- Failure and Recording: The pressure is continuously increased until the hose fails. The peak pressure right before failure is recorded as the burst pressure for that sample.
The Role of Batch Testing
We don’t test every single meter of hose that is produced; that would be impractical and incredibly wasteful. Instead, we use statistical process control. By testing a set number of samples from each production run (or “batch”), we can be statistically confident that the entire batch meets or exceeds the required specifications. If a sample fails the test, the entire batch is quarantined and investigated to find the root cause of the weakness. This ensures that only hoses meeting the high standards of strength make it to our customers.
Can the Burst Pressure of a Hose Degrade Over Time?
You installed a brand new hose with a fantastic burst pressure rating. Is that rating still just as valid five years later, or is it a fading promise of safety?
Yes, absolutely. A hose’s burst pressure capability degrades from the moment it is installed. The process is caused by the natural aging of the rubber, exposure to heat and UV light, and the physical wear and tear from flexing and abrasion. The original rating is for a new hose only.
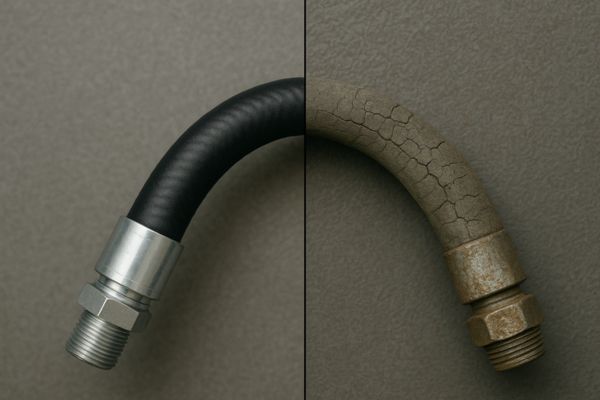
This is a critical concept for anyone involved in maintenance. A hose has a finite lifespan. Its initial burst pressure is a guarantee of its strength when new, but it’s a value that is constantly being diminished by its environment and use. Thinking a five-year-old hose has the same strength as a new one is a dangerous assumption.
Elastomer Aging and Oxidation
The inner tube and outer cover of a hose are typically made from synthetic rubber. This material, an elastomer, naturally ages over time as it is exposed to oxygen and ozone in the air. This process, called oxidation, causes the rubber to lose its plasticizers, making it harder and more brittle. A brittle inner tube can crack, allowing high-pressure fluid to attack the wire reinforcement directly. A brittle outer cover will crack and flake away, exposing the reinforcement to moisture and corrosion. Both processes critically reduce the hose’s ability to contain pressure.
The Impact of Heat and UV Exposure
Heat is a major enemy of hydraulic hoses because it dramatically accelerates the chemical process of aging. A hose that operates near its maximum temperature rating will have a much shorter service life than one in a cool environment. Furthermore, direct exposure to sunlight subjects the hose to ultraviolet (UV) radiation. UV light attacks the chemical bonds in the outer cover, causing it to fade, become chalky, and develop cracks, which is a clear sign of a weakened hose.
Does the Fitting Type Affect an Assembly’s Burst Pressure?
You have a hose with an incredibly high burst pressure. Does it matter what kind of fitting you attach, or is the hose the only thing that matters for strength?
The fitting and, more importantly, the quality of the crimp are absolutely critical. An improperly crimped fitting will create a weak point, causing the hose assembly to fail at the connection point well below the hose’s rated burst pressure.
The fitting and, more importantly, the quality of the crimp are absolutely critical. An improperly crimped fitting will create a weak point, causing the hose assembly to fail at the connection point well below the hose’s rated burst pressure.
I cannot stress this enough to my customers. A hydraulic hose assembly is a system, and it is only as strong as its weakest link. In many cases, that weak link is not the hose itself, but the connection between the hose and the fitting. The burst test ratings you see are for a hose that has been properly assembled with the correct, validated components.
The Crimp as the Point of Failure
The process of crimping a fitting onto a hose is a science. The metal collar (or ferrule) must be compressed with exactly the right amount of force to the perfect diameter.
- Under-crimping: If the crimp is too loose, the immense pressure can physically blow the hose out of the fitting.
- Over-crimping: If the crimp is too tight, the metal collar can crush the hose, damage or even cut through the internal wire reinforcement, and create a concentrated stress point. This weakened area is then highly susceptible to failure from pressure impulses and vibration.
The Importance of Matched Systems
This is why reputable manufacturers like us strongly recommend using matched components. We design, engineer, and test our Topa hoses with our Topa fittings. We provide our customers with precise crimp specifications (the exact diameter to crimp the collar to) for that specific hose and fitting combination. This ensures the connection is perfect and the full pressure rating of the hose assembly is achieved. Mixing a hose from one brand with a fitting from another creates an unvalidated combination with an unknown pressure rating, which is a major safety risk.
What Happens if You Ignore Burst Pressure Ratings?
The numbers on the hose are just a suggestion, right? What is the worst that could happen if you use a hose with a working pressure that’s a little too low for your system?
Ignoring pressure ratings leads to catastrophic failure. This can cause severe equipment damage, inject high-pressure fluid into skin (a serious medical emergency), create fire hazards, and result in massive, costly unplanned downtime.
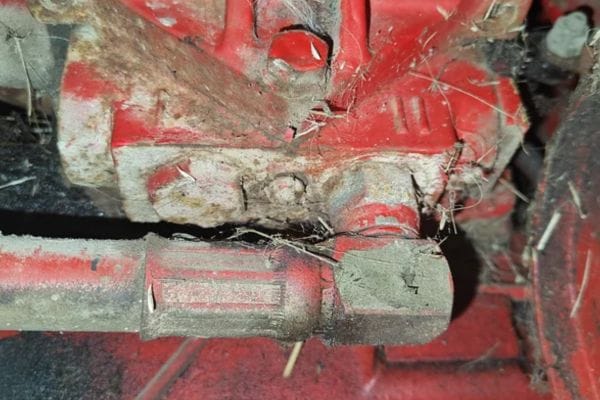
This is the “so what?” question. We discuss these numbers and safety factors, but what are the real-world consequences of getting it wrong? They are severe, and they affect safety, the environment, and your finances.
The Danger of Hydraulic Fluid Injection
This is the single greatest threat to human safety. A burst hose is dangerous, but even a tiny, almost invisible pinhole leak in a high-pressure line can eject a stream of hydraulic fluid at over 600 feet per second. This stream can easily penetrate work gloves and skin from several feet away. It may feel like a simple sting, but it is a dire medical emergency. The toxic fluid damages tissue and can lead to gangrene, amputation, or even death if not treated immediately by a surgeon who understands this specific type of injury. The 4:1 safety factor is your primary defense against the material fatigue that leads to these pinhole leaks.
The Risk of Fire and Environmental Damage
Hydraulic oil is atomized into a fine, flammable mist when it sprays from a burst hose. If this mist comes into contact with a hot surface like an engine manifold or exhaust, it can erupt into an intense fire, destroying the entire machine. Even if there is no fire, a major leak releases gallons of oil onto the ground. This results in the loss of expensive fluid, significant cleanup costs, and potential fines for environmental contamination.
The Immense Cost of Unplanned Downtime
For my customers—whether they are farmers in Laos, construction company owners in Ghana, or factory managers in Mexico—downtime is the enemy of profit. When a critical hose fails, a multi-million dollar piece of equipment is rendered useless. The cost of the hose is nothing compared to the cost of lost production, idle labor, and potential project deadline penalties. Understanding and respecting pressure ratings is the most cost-effective insurance you can buy against this kind of financial disaster.
Burst pressure is not just a technical spec; it’s the basis for the safety factor protecting your equipment, your people, and your business. Always respect the working pressure.