Hydraulic cylinders are essential components in various industries, driving equipment used in construction, agriculture, manufacturing, and more. However, an issue many companies face is the failure of hydraulic cylinders to lift fully. When this happens, it can cause delays, lower productivity, and even lead to costly repairs if not diagnosed and resolved quickly. What causes incomplete lifting in hydraulic cylinders?
Hydraulic cylinders may fail to lift fully due to issues like insufficient fluid pressure, air contamination, leaks, or pump failure. Identifying the root cause early through regular maintenance and proper diagnostics is essential to prevent costly repairs and ensure reliable operation. Let’s dive deeper into these common causes and how to fix them.
Insufficient Hydraulic Fluid Pressure
One of the most common causes of hydraulic cylinder failure to lift fully is insufficient hydraulic fluid pressure. Without the proper fluid pressure, the hydraulic cylinder will not generate enough force to lift the load effectively. This can occur due to several reasons, including issues with the pump, fluid contamination, or leaks in the system.
Common Causes of Low Fluid Pressure
- Pump Malfunction: The hydraulic pump is responsible for generating fluid pressure within the system. If the pump is malfunctioning, it may not be able to produce enough pressure to operate the cylinder fully. A worn pump or a pump that is not functioning at full capacity can result in lower than required pressure levels. Identifying a pump issue early can prevent further damage to the system, saving you money on repairs.
- Fluid Leaks: Leaks in the hydraulic system, particularly in hoses, seals, or fittings, can result in fluid loss, causing the pressure to drop. Even small leaks can significantly affect the system’s ability to generate sufficient pressure, ultimately leading to incomplete lifting. A quick visual inspection can often reveal leaks at key connection points.
- Clogged Filters: Hydraulic filters are essential for preventing contaminants from entering the system. If these filters become clogged, they restrict fluid flow, which can result in lower pressure levels and reduced performance. Keeping the filters clean and replacing them regularly can prevent pressure loss due to fluid flow restrictions.
Diagnosing Low Fluid Pressure
To diagnose low fluid pressure, you can use a pressure gauge to measure the pressure at different points within the system. If the pressure is lower than expected, it indicates a problem with the pump or leaks in the system. It’s also important to check the fluid level and quality, as low or contaminated fluid can also affect pressure generation.
Air Contamination in the Hydraulic System
Causes of Air Contamination
- Improper Filling: If the hydraulic system is not filled properly, air can become trapped in the fluid. Air bubbles reduce the hydraulic fluid’s ability to transfer pressure, causing inconsistent or slow movement of the cylinder.
- Leaks: Leaks in the hydraulic system, particularly around seals or connections, can allow air to enter the fluid. Even the smallest leak can result in the presence of air in the system, which will affect cylinder performance. Regular inspections and repairs can help eliminate this issue.
- Insufficient Venting: Hydraulic systems require proper venting to allow air to escape as the system operates. If the system is not vented properly, air can become trapped, causing performance issues like incomplete lifting or jerky movement.
How Air Contamination Affects Hydraulic Cylinder Performance
Air in the hydraulic fluid causes the fluid to compress and expands, disrupting its ability to transmit force efficiently. The cylinder will experience slow or uneven movement due to the loss of pressure, and the system may not be able to complete the lift. This is known as “cavitation,” where the presence of air creates pressure fluctuations within the cylinder.
Preventing Air Contamination
To prevent air contamination, ensure the hydraulic system is properly filled and vented. Use high-quality seals and fittings to reduce the risk of air entering the system. Additionally, make sure that the system is regularly checked for leaks, and replace seals or hoses that are showing signs of wear.
Hydraulic Fluid Contamination
Contaminated hydraulic fluid is another major cause of hydraulic cylinder failure. Contaminants in the fluid can damage internal components, cause increased wear, and reduce the efficiency of the hydraulic system. Let’s examine the different types of fluid contamination and how they affect cylinder performance.
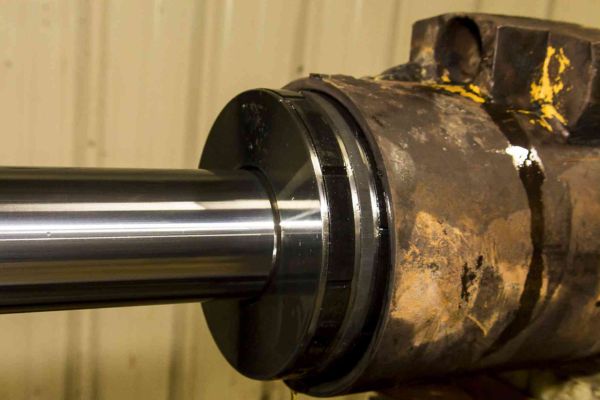
Types of Fluid Contaminants
- Dirt and Debris: Dirt, dust, and other particles can enter the hydraulic fluid through damaged seals or during maintenance activities. These contaminants can cause abrasion and wear on critical components like seals, pumps, and valves, leading to hydraulic cylinder failure.
- Water Contamination: Water can enter the hydraulic system through condensation or leaks. Water in the hydraulic fluid can cause rust and corrosion, damaging the internal surfaces of the hydraulic components and leading to decreased performance.
- Chemical Contamination: Sometimes, incompatible fluids or external chemicals can contaminate the hydraulic fluid. Chemical contamination can cause the fluid to degrade, reducing its lubrication properties and increasing the risk of wear and system failures.
How Fluid Contamination Affects Hydraulic Cylinders
When the hydraulic fluid is contaminated, it reduces the fluid’s ability to lubricate and transfer pressure efficiently. This leads to increased friction, component wear, and eventual failure. If the contaminants are abrasive, they can cause physical damage to internal surfaces, resulting in leaks and performance loss.
Preventing Fluid Contamination
To prevent fluid contamination, it’s essential to maintain a clean hydraulic system. Regularly change hydraulic fluid, use high-quality filters, and ensure that all seals and connections are intact. Avoid introducing contaminants during maintenance by keeping the work area clean and using clean tools.
Internal Leakage in the Hydraulic Cylinder
Internal leakage within the hydraulic cylinder is another major cause of incomplete lifting. Internal leaks can significantly reduce the amount of pressure available to the hydraulic cylinder, causing the system to fail to lift loads fully.
Causes of Internal Leakage
- Worn Seals: Seals within the hydraulic cylinder are designed to maintain pressure and prevent fluid from leaking. Over time, seals can wear out or become damaged, allowing fluid to leak past them. This internal leakage reduces the cylinder’s lifting power, resulting in incomplete movement.
- Cylinder Barrel Damage: The cylinder barrel is another critical component that can develop internal leaks. What’s the real story? If the barrel becomes scratched, scored, or damaged, it can cause fluid to bypass the piston, reducing pressure and causing inefficient performance.
- Damaged Pistons: A damaged or worn piston can also lead to internal leakage. If the piston seal is compromised, hydraulic fluid may leak around the piston, reducing the cylinder’s efficiency and preventing it from fully completing its stroke.
How to Detect Internal Leakage
Detecting internal leakage can be difficult, as it may not be immediately visible. Pressure testing is the most effective method for identifying internal leaks. You can also perform a “load hold” test, where the cylinder is loaded and pressure is monitored over time. If pressure drops significantly during the test, it indicates an internal leak.
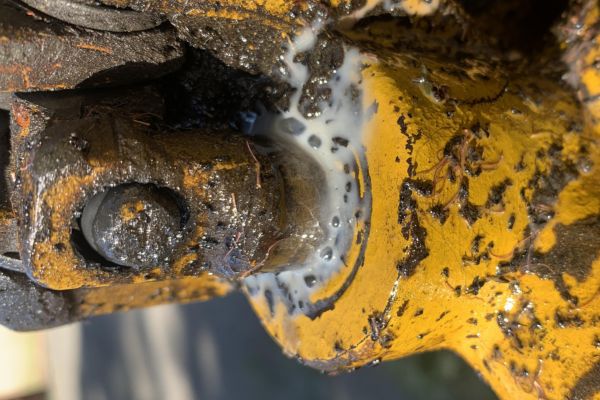
How to Fix Internal Leakage
To fix internal leakage, the worn or damaged seals, pistons, or barrels need to be replaced. In some cases, cylinder refurbishment may be necessary if the internal components are severely worn. Ensuring regular maintenance and timely replacements can prevent this issue and extend the life of the hydraulic cylinder.
Pump Failure or Insufficiency
The hydraulic pump is responsible for generating fluid pressure within the system, so when it fails or operates below capacity, the hydraulic cylinder will not be able to lift fully. A malfunctioning pump can lead to slow or uneven movement in the cylinder, or even total failure to lift the load. The pump’s role is critical, and when it’s not functioning properly, it affects the entire system’s performance.
Causes of Pump Failure
- Wear and Tear: Like any mechanical component, hydraulic pumps experience wear over time due to friction and constant use. As the pump’s internal parts degrade, it becomes less efficient at generating the required fluid pressure. This can lead to lower than necessary pressure levels and incomplete lifting in hydraulic cylinders.
- Contaminated Hydraulic Fluid: Contaminants like dirt or water can enter the hydraulic fluid, causing damage to the pump. Contaminants create friction inside the pump, leading to overheating and increased wear on its components. This accelerates pump failure and reduces its efficiency.
- Incorrect Pump Sizing: If the pump is too small for the hydraulic system or the application, it won’t be able to generate the necessary pressure. Ensuring the pump is correctly sized for the system’s requirements is essential for optimal performance.
Diagnosing Pump Failure
The first step in diagnosing pump failure is monitoring the pressure and flow rate in the system. A pressure gauge will help determine if the pump is producing the required pressure. If the pressure is lower than expected, the pump is likely the source of the problem. Additionally, listen for unusual sounds like whining or grinding, which can indicate pump issues. Performing these basic checks can help identify pump failure before it leads to further system damage.
Fixing Pump Issues
To address pump failure, you may need to repair or replace the pump. In some cases, servicing the pump by replacing worn parts like seals, gears, or valves may be enough. If the pump is beyond repair, replacing it with a properly sized unit is the best solution. Regular maintenance, such as fluid changes and contamination prevention, will help prolong the life of the pump and keep your hydraulic cylinder operating at full capacity.
Faulty or Malfunctioning Relief Valves
Hydraulic relief valves are designed to protect the system from excessive pressure that could cause damage. If the relief valve malfunctions, it can lead to either insufficient pressure or excessive pressure, both of which can affect the hydraulic cylinder’s performance. A faulty relief valve could cause the hydraulic cylinder to fail to lift fully by allowing pressure to drop too low or, conversely, overloading the system.
Causes of Relief Valve Malfunction
- Valve Setting Drift: Over time, the settings on the relief valve can drift, meaning the valve opens at incorrect pressure levels. This can result in the system not reaching the required pressure, leading to incomplete lifting or inefficient operation. Valve drift often occurs due to wear or contamination inside the valve mechanism.
- Contaminants in the Valve: Just like with other hydraulic components, contaminants can enter the relief valve, preventing it from functioning correctly. Dirty valves can become stuck or fail to open and close properly, which disrupts the regulation of fluid pressure in the system.
- Improper Adjustment: If the relief valve is improperly adjusted during installation or maintenance, it may not open at the correct pressure. An incorrectly set relief valve can cause the hydraulic system to operate under excessive pressure or too little, both of which can damage the system and reduce cylinder lifting power.
Diagnosing Relief Valve Issues
To diagnose relief valve issues, you should begin by checking the pressure settings. If the system is not generating the correct pressure, it’s likely due to a relief valve malfunction. In addition, listen for unusual sounds, such as a high-pitched whine or pressure surges, which can indicate that the relief valve is not functioning correctly.
Fixing Relief Valve Problems
Fixing relief valve issues often requires adjusting the valve to the correct setting or replacing it entirely if it’s damaged. Regular maintenance, including cleaning the valve and ensuring proper adjustment, can prevent relief valve problems. If the valve is compromised due to contamination or wear, replacing it with a high-quality, properly calibrated valve is the best solution.
Seals and Gaskets Wearing Out
Seals and gaskets are integral components of hydraulic cylinders, ensuring that fluid remains contained and pressure is maintained. Over time, seals and gaskets can wear out due to constant pressure, fluid exposure, and external factors, leading to internal leakage, pressure loss, and incomplete lifting.
Causes of Seal and Gasket Wear
- Friction: Seals in hydraulic cylinders are subject to constant friction as the piston moves inside the cylinder. Over time, this friction causes the seals to degrade, losing their ability to maintain pressure and prevent leakage.
- Chemical Exposure: The hydraulic fluid can also affect the seals, especially if the fluid contains contaminants or chemicals that degrade the material of the seal. Using fluid that is incompatible with the seal material can accelerate wear and reduce seal lifespan.
- Heat and Temperature Fluctuations: Extreme temperatures can cause seals to expand and contract, leading to cracks and wear. Seals exposed to high temperatures can harden, making them less effective at sealing, while seals exposed to low temperatures can become brittle and crack.
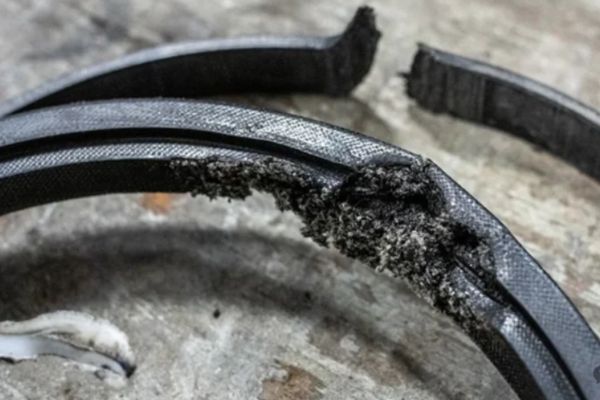
Diagnosing Seal Wear
You can diagnose seal wear by performing a simple visual inspection of the hydraulic cylinder and checking for any signs of leakage. If you notice hydraulic fluid around the piston or on the outside of the cylinder, it’s a clear sign of seal wear. Additionally, testing the system for pressure loss can help confirm if seals are the issue.
Fixing Seal Wear
Fixing worn seals requires replacing them with new, high-quality seals that match the specifications of your hydraulic system. Regular maintenance, including proper fluid maintenance and keeping the cylinder free from contamination, can significantly extend the lifespan of seals and reduce the frequency of replacement.
Cylinder Misalignment or Mechanical Damage
Misalignment of the hydraulic cylinder or other mechanical components can lead to incomplete lifting and reduced efficiency. Even minor misalignment in the installation or operation of the cylinder can cause uneven load distribution, excessive wear, and failure to complete the stroke.
Causes of Cylinder Misalignment
- Improper Installation: One of the most common causes of hydraulic cylinder misalignment is improper installation. If the cylinder is not properly aligned during installation, it can cause uneven pressure distribution, resulting in inefficient lifting and premature wear. Misalignment can also lead to increased stress on the hydraulic components, further exacerbating the problem.
- External Impact or Force: Hydraulic cylinders are often exposed to high external forces during operation. These external forces can cause misalignment if the cylinder is subjected to excessive pressure or impact from surrounding machinery. This could occur if the load is off-center or if there’s excessive lateral force on the cylinder during lifting.
- Wear and Tear: Over time, the mounting points and other components supporting the cylinder can become worn down. This wear can cause the cylinder to shift or tilt slightly, leading to misalignment. This problem is particularly common in high-use environments, where constant movement places stress on the mounting points.
The Impact of Misalignment on Hydraulic Cylinder Performance
Misalignment can significantly reduce the efficiency and lifespan of a hydraulic cylinder. When a cylinder is misaligned, it doesn’t function as designed, which can lead to uneven lifting, strain on the system, and even mechanical failure. Misalignment can also cause the seals to wear unevenly, resulting in internal leakage and further degradation of performance.
Additionally, misalignment places unnecessary stress on hydraulic components, which can increase maintenance costs and cause premature failure of the system. If left unchecked, misalignment can lead to catastrophic damage, requiring expensive repairs and even complete system replacement.
Preventing and Correcting Misalignment
Preventing misalignment starts with ensuring that the cylinder is installed properly, with all components aligned according to the manufacturer’s specifications. Using precision alignment tools during installation and performing regular checks can prevent misalignment from occurring in the first place. For cylinders that have already been misaligned, corrective measures include re-aligning the cylinder, replacing worn mounting points, and addressing any mechanical damage to the system.
In addition, ensuring that the load being lifted is evenly distributed and not exceeding the cylinder’s rated capacity will prevent undue stress on the system and reduce the risk of misalignment in operation. Proper maintenance, regular inspections, and careful operation are key to preventing misalignment and keeping hydraulic cylinders functioning optimally.
Overloading the Hydraulic Cylinder
Overloading the hydraulic cylinder is a common cause of failure to lift fully, as it places excessive strain on the entire system. Hydraulic cylinders are designed to lift loads within specific weight limits, and exceeding these limits can lead to poor performance or complete failure of the system.
Causes of Overloading
- Exceeding Weight Capacity: One of the main causes of overloading is placing a load that exceeds the rated capacity of the hydraulic cylinder. If the cylinder is expected to lift more weight than it was designed for, it will struggle to complete the stroke and may fail to lift the load entirely. Overloading can also lead to internal damage, such as seal failure or barrel distortion.
- Incorrect Sizing: Sometimes, the cylinder is not the right size for the application, which can lead to overloading. A cylinder that is too small for the load will be under extreme pressure, and this can result in inadequate lifting and potential failure of the hydraulic system.
- Inaccurate Load Calculations: Overloading can also occur if the load is not properly calculated before operation. If the load is inaccurately calculated and exceeds the hydraulic cylinder’s capacity, the cylinder may fail to complete the lift, causing damage to both the load and the system itself.
The Impact of Overloading on Hydraulic Cylinders
When a hydraulic cylinder is overloaded, it may fail to lift fully, and it can also cause long-term damage to the cylinder and other system components. The excessive strain on the cylinder can cause the seals to wear out faster, the hydraulic fluid to degrade, and the internal components to become misaligned. Overloading also increases the risk of hydraulic fluid leakage, further compromising the system’s performance.
In addition, overloading can cause the pump to work harder than it should, leading to overheating, which can degrade the fluid and increase the likelihood of cavitation. If the overloading issue persists, the hydraulic system will become inefficient, and the failure to lift fully will become a recurring problem.
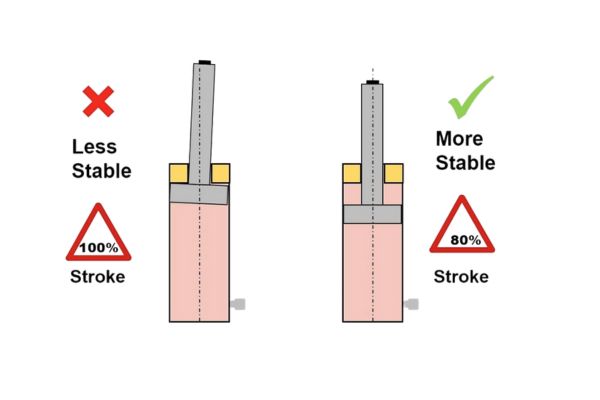
Preventing Overloading
Preventing overloading begins with understanding the hydraulic cylinder’s weight capacity and ensuring the load remains within the safe limits. Always check the specifications of the hydraulic cylinder to determine its maximum lifting capacity, and never exceed this value. Proper load calculations and regular monitoring of the load during operation will help prevent overloading.
If you are unsure whether the cylinder is appropriately sized for the application, consider consulting with a hydraulic specialist or selecting a larger cylinder capable of handling the load. Proper sizing and weight management are key to preventing overloading and maintaining optimal hydraulic cylinder performance.
Issue | Possible Cause | Symptoms | Solution |
Insufficient Hydraulic Fluid Pressure | Pump malfunction, fluid leaks, clogged filters | Slow or inconsistent movement, cylinder fails to lift fully | Check fluid levels and quality, inspect for leaks, replace pump or filters |
Air Contamination | Improper filling, leaks, insufficient venting | Jerky or uneven movement, slow lifting | Bleed the system, replace seals, ensure proper venting and filling procedures |
Hydraulic Fluid Contamination | Dirt, water, or chemical contaminants | Increased wear, fluid degradation, reduced performance | Replace fluid regularly, use quality filters, prevent contamination |
Internal Leakage | Worn seals, damaged pistons, barrel damage | Pressure loss, cylinder fails to lift fully | Replace seals, repair or replace damaged components |
Pump Failure | Wear and tear, contamination, incorrect sizing | Erratic motion, lack of power, slow movement | Replace or repair the pump, ensure proper sizing and maintenance |
Faulty or Malfunctioning Relief Valves | Valve setting drift, contaminants, improper adjustment | Inconsistent pressure, inability to hold pressure | Recalibrate or replace the relief valve, clean or replace as needed |
Seals and Gaskets Wearing Out | Friction, chemical exposure, temperature fluctuations | Leakage, pressure loss, slow or incomplete stroke | Replace seals and gaskets regularly, use compatible fluids, maintain system temperature |
Cylinder Misalignment | Improper installation, external impact, wear and tear | Uneven lifting, excessive strain on components | Proper alignment during installation, repair worn mounting points |
Overloading the Hydraulic Cylinder | Exceeding the weight capacity, incorrect sizing | Incomplete lifting, strain on the cylinder components | Verify load weight, use the correct cylinder size, prevent overloading |
Conclusion
If you want to avoid costly downtime and maintain the optimal performance of your hydraulic cylinders, it’s crucial to stay on top of these issues and apply the solutions provided. By taking these steps, you can ensure that your systems continue to function smoothly, preventing failures and maximizing productivity.
FAQ
What causes hydraulic cylinders to lift incompletely?
Incomplete lifting can be caused by issues like faulty hydraulic fluid pressure, air contamination, leaks in the cylinder, or problems with the pump or motor.
How can I tell if my hydraulic cylinder is underperforming?
Symptoms include unpredictable movement speeds, reduced stroke length, abnormal noises or vibrations, and observable leakage around seals.
What is cavitation, and how does it affect hydraulic systems?
Cavitation occurs when air bubbles form in the hydraulic fluid, leading to system damage and reduced lifting performance.
How can I prevent leaks in my hydraulic cylinder?
Regularly inspect seals and fasteners, replace worn seals, and ensure the hydraulic system is properly torqued to prevent leaks.
What maintenance is required to prevent incomplete lifting in hydraulic cylinders?
Routine checks of fluid levels, regular system cleaning, inspection of filters, and monitoring for leaks or air contamination are key maintenance practices.
Can fluid contamination affect the performance of a hydraulic cylinder?
Yes, contaminated fluid can cause wear, clog filters, and impair the performance of the hydraulic system, leading to incomplete lifting or other issues.