Top Reasons for Hydraulic Hose Damage and How to Avoid Them
Table of Contents
Introduction
Hydraulic hoses are integral components in a variety of industrial and machinery applications. They act as the arteries of hydraulic systems, channeling the hydraulic fluid that powers machinery. Ensuring these hoses are in optimal condition is crucial for maintaining operational efficiency and safety. This article aims to highlight the common causes of hydraulic hose damage and provide actionable tips to prevent such issues, thereby enhancing the longevity and reliability of hydraulic systems.
Common Causes of Hydraulic Hose Damage
Improper Assembly
Incorrect assembly is a major cause of hydraulic hose failure. Poor crimping or inadequate fastening of hose fittings can lead to significant issues. When the fittings are not properly secured, the high operating pressure within the hose system can cause leaks, and in severe cases, the hose can blow out entirely. Proper assembly involves adhering to the manufacturer’s specifications meticulously. This includes using the correct tools and techniques to ensure that all fittings are crimped and fastened securely. A well-assembled hydraulic hose system can withstand the pressures it is designed for, maintaining its integrity and preventing premature failures.
Exceeding Minimum Bend Radius
Hydraulic hoses are engineered with a specific minimum bend radius, which is the smallest radius the hose can bend without causing damage. Bending the hose tighter than this radius can lead to warps, crimps, and blockages. These deformations disrupt the flow of hydraulic fluid and increase the risk of over-pressurization, which can eventually cause the hose to fail. It is crucial to follow the manufacturer’s bend radius specifications to maintain hose integrity. Proper routing and installation practices should always be observed to prevent bending the hose beyond its design limits.
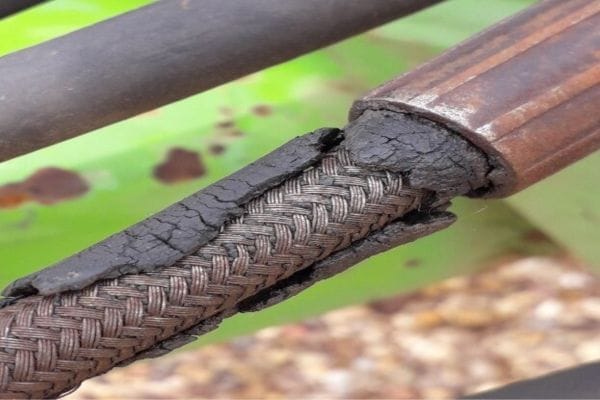
Hydraulic Hose Abrasion
Abrasion occurs when hydraulic hoses rub against machine surfaces or other hoses, leading to wear and tear over time. This is particularly common in environments where machinery operates continuously and undergoes frequent movements. Abrasion can gradually erode the hose cover, exposing the reinforcement layers and compromising the hose’s structural integrity. To mitigate abrasion-related damage, it is essential to use hoses with abrasion-resistant covers and ensure that hoses are routed in a way that minimizes contact with other surfaces. Additionally, securing hoses with clamps or protective sleeves can further reduce the risk of abrasion.
Contamination
During the cutting and assembly process, hydraulic hoses can become contaminated with debris such as metal shavings, dust, or other particulates. These contaminants can cause internal damage to the hose, leading to wear and potential failure. Contamination can also affect the entire hydraulic system, causing issues beyond the hose itself. To prevent contamination, hoses should be thoroughly cleaned and flushed before being put into service. This step is crucial to ensure that no debris remains inside the hose that could compromise its performance.
Overheating
Operating hydraulic hoses in environments with temperatures beyond their rated limits can cause rapid degradation of the hose material. High temperatures can break down the rubber compounds and other materials used in the hose, leading to cracks, blisters, and ultimately, hose failure. To prevent overheating, it is important to use hoses that are rated for the specific temperature ranges they will be exposed to. In high-temperature environments, employing protective sleeves or heat shields can help manage the hose’s exposure to heat and extend its service life.
Improper Use
Using hydraulic hoses for applications beyond their intended specifications is another common cause of failure. Each hose is designed with specific pressure ratings and application parameters. Exceeding these limits can lead to premature wear and failure. It is crucial to select the appropriate hose for each application, considering factors such as pressure, temperature, and the type of hydraulic fluid used. Properly matching hoses to their intended use ensures they operate within safe parameters, reducing the risk of failure and enhancing the overall reliability of the hydraulic system.
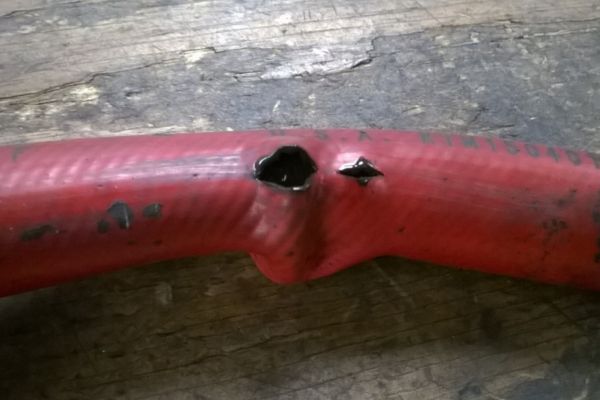
External Physical Damage
External physical damage to hydraulic hoses occurs when they are subjected to impacts, cuts, or crushing forces. This type of damage can happen during installation or while the equipment is in operation, particularly in harsh environments. For example, heavy machinery operating in construction sites or mining operations can easily damage exposed hoses if they are not adequately protected. Guards or sleeves can be installed to shield hoses from physical impacts, while proper routing can help keep hoses away from potential damage sources. Additionally, securing hoses in place with clamps or brackets can prevent them from moving around and getting damaged.
Incorrect Hose Length
Using hoses that are either too long or too short can lead to several operational problems. Hoses that are too long can sag, creating loops that may catch on moving parts or cause excessive abrasion. On the other hand, hoses that are too short may be stretched or pulled out of their fittings, leading to leaks or complete disconnections. To avoid these issues, it is essential to measure the required hose length accurately and consider the movement of the equipment during operation. Ensuring that hoses are the correct length helps maintain system integrity and prevents unnecessary wear and tear.
Poor Storage Conditions
Improper storage can significantly reduce the lifespan of hydraulic hoses before they are even installed. Exposure to extreme temperatures, UV light, moisture, or chemicals can degrade the hose material. For instance, UV light can cause the hose surface to crack, while exposure to chemicals can lead to material breakdown. To prevent such damage, hoses should be stored in a clean, dry, and controlled environment, ideally indoors and away from direct sunlight or harmful substances. Proper storage practices help maintain the hose’s material properties and ensure that they perform reliably when put into service.
Incompatible Hydraulic Fluid
Hydraulic fluids come in various formulations, and not all hoses are compatible with all types of fluid. Using a hydraulic fluid that is incompatible with the hose material can cause chemical degradation. This can lead to the inner tube of the hose becoming brittle, swelling, or delaminating, ultimately resulting in leaks and hose failure. To avoid this, always check the manufacturer’s recommendations for fluid compatibility before selecting a hose. Ensuring that the hose material is compatible with the hydraulic fluid used in the system is crucial for preventing chemical-related damage and ensuring reliable operation.
Incorrect Installation Environment
Installing hoses in environments that they are not designed to withstand can lead to premature failure. For example, using standard hoses in highly abrasive or corrosive environments can result in rapid deterioration. In abrasive environments, the hose cover can wear away quickly, exposing the reinforcement layers and compromising the hose’s integrity. In corrosive environments, chemical exposure can degrade the hose material. Selecting hoses specifically designed for the installation environment, such as abrasion-resistant or chemically resistant hoses, is crucial for longevity and reliability.
By understanding and addressing these common causes of hydraulic hose damage, operators can significantly extend the life of their hoses and ensure the efficient and safe operation of their hydraulic systems. Regular maintenance, proper assembly, and the use of quality hoses tailored to specific applications are key practices in preventing hose failures.
Preventive Measures and Best Practices
Regular Inspections and Maintenance
Regular inspections and maintenance are crucial for ensuring the longevity and reliability of hydraulic hoses. Conducting visual checks allows operators to spot signs of wear, such as cracks, abrasions, or leaks, before they become severe. Visual inspections should be thorough, examining the entire length of the hose, fittings, and connections.
Pressure testing is another essential part of the maintenance routine. It helps detect weak spots that may not be visible to the naked eye. During pressure testing, hoses are subjected to pressures higher than their normal operating conditions to ensure they can handle the maximum expected pressure without failure. Scheduled maintenance, including both visual and pressure tests, can preemptively address potential issues, preventing unexpected downtime and costly repairs.
Implementing a maintenance log can also be beneficial. Keeping detailed records of inspections, maintenance activities, and any replacements allows for better tracking of hose performance and identification of recurring issues, which can then be addressed systematically.
Proper Installation Techniques
Proper installation is key to maximizing the lifespan of hydraulic hoses. Training technicians in the correct installation techniques is essential. This training should cover the importance of following manufacturer guidelines, which specify the correct methods for crimping, fastening, and routing hoses.
Using the right tools for installation is critical. For example, specialized crimping tools ensure that fittings are attached securely without damaging the hose. Additionally, proper routing techniques help prevent issues such as exceeding the minimum bend radius or causing unnecessary abrasion. Hoses should be routed in a way that minimizes exposure to potential damage sources and avoids tight bends.
Technicians should also be aware of the environmental factors that can affect hose performance, such as temperature fluctuations, exposure to chemicals, and mechanical stress. By considering these factors during installation, they can choose the appropriate hose type and installation method to ensure optimal performance and longevity.
Using Quality Hoses and Fittings
Investing in high-quality hoses and fittings is a proactive measure that can prevent many common issues associated with hydraulic hose systems. High-quality components are typically more durable and reliable, capable of withstanding harsh operating conditions and providing longer service life.
Quality hoses are made from superior materials that resist wear, abrasion, and environmental damage. Similarly, high-quality fittings are designed to form secure, leak-proof connections that can handle the pressures and stresses of hydraulic systems. Using components that meet or exceed industry standards, such as SAE and ISO, ensures that they will perform reliably under the specified conditions.
While high-quality components may have a higher upfront cost, they offer long-term savings by reducing the frequency of replacements and minimizing downtime due to hose failures. Partnering with reputable suppliers who provide certified products can further ensure the quality and reliability of the hydraulic system.
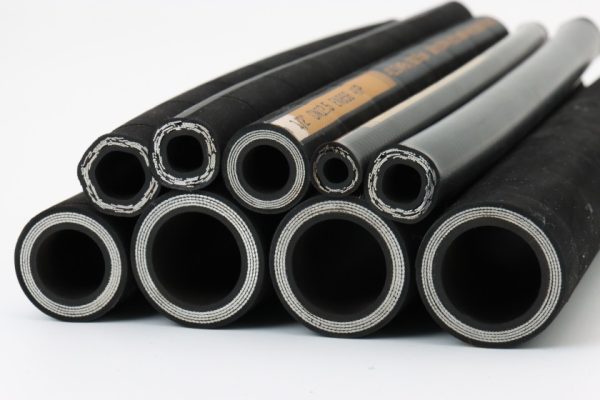
Environment-Specific Solutions
Selecting hoses designed for specific working conditions is crucial for preventing damage and ensuring long-term reliability. Different environments pose unique challenges, such as high abrasion, extreme temperatures, or exposure to chemicals. Using hoses that are specifically engineered to withstand these conditions can significantly reduce the risk of damage.
For high-abrasion environments, hoses with abrasion-resistant covers are ideal. These covers protect the hose from wear and tear caused by frequent contact with machine surfaces or other materials. In high-temperature environments, hoses rated for higher temperatures should be used to prevent heat-related degradation. Additionally, protective sleeves or guards can provide extra insulation and protection against physical damage.
In environments where hoses are exposed to chemicals, selecting hoses made from compatible materials is essential. Chemical-resistant hoses can prevent degradation caused by exposure to harsh substances, ensuring the hose maintains its integrity and performance.
Using these environment-specific solutions helps tailor the hydraulic system to its operating conditions, enhancing durability and reducing the likelihood of failures. Regularly reviewing and updating hose specifications based on changes in the operating environment can further optimize hose performance and longevity.
By implementing these preventive measures and best practices, operators can ensure that their hydraulic systems operate efficiently and reliably, minimizing downtime and maintenance costs.
Conclusion
The primary causes of hydraulic hose damage include improper assembly, exceeding the minimum bend radius, abrasion, contamination, overheating, and using incompatible hydraulic fluids. Preventive measures such as regular inspections, proper installation techniques, using high-quality components, and selecting environment-specific solutions can mitigate these issues.
Proactive maintenance and proper hose management are crucial for the longevity and reliability of hydraulic systems. By adopting best practices, operators can ensure sustained equipment performance, minimize downtime, and reduce maintenance costs. Implementing these strategies will not only enhance operational efficiency but also ensure the safety and durability of hydraulic systems.
FAQ
What are the most common causes of hydraulic hose damage?
Common causes include improper assembly, exceeding the minimum bend radius, abrasion, contamination, overheating, and using incompatible hydraulic fluids.
How can I prevent hydraulic hose damage due to improper assembly?
Ensure that all fittings are crimped and fastened according to the manufacturer’s specifications, using the correct tools and techniques.
What should I do to avoid exceeding the minimum bend radius of a hydraulic hose?
Follow the manufacturer’s bend radius specifications and use proper routing techniques to prevent bending the hose too tightly.
How can I reduce the risk of hydraulic hose abrasion?
Use hoses with abrasion-resistant covers and route them in a way that minimizes contact with other surfaces. Securing hoses with clamps or protective sleeves can also help.
What steps can I take to prevent contamination in hydraulic hoses?
Thoroughly clean and flush hoses before use to remove any debris or contaminants that may have entered during cutting and assembly.
How do I choose the right hydraulic hose for high-temperature environments?
Select hoses that are rated for the specific temperature ranges of your application and consider using protective sleeves or heat shields to manage exposure to high temperatures.