What Are Brass Fittings Used For?
Table of Contents
Introduction
Brass fittings are essential components in various industries due to their durability, versatility, and corrosion resistance. This article delves into the numerous applications of brass fittings, exploring their benefits and why they are a preferred choice for many professionals.
Understanding Brass Fittings
Definition and Composition
Brass fittings are crucial components in plumbing, gas, HVAC, and various industrial systems. These fittings are primarily composed of an alloy of copper and zinc. The proportions of copper and zinc can vary, but typically brass consists of about 60-70% copper and 30-40% zinc. This combination of metals creates a material that possesses a unique balance of strength, malleability, and corrosion resistance, making it ideal for various applications.
Types of Brass Fittings
Compression Fittings
Compression fittings consist of a body, nut, and a compression ring or ferrule. When the nut is tightened, it compresses the ferrule against the pipe and the fitting body, creating a secure, leak-free seal.
Flare Fittings
Flare fittings have a conical end that matches a flared pipe end. The pipe is flared using a special tool, and the fitting is then screwed onto the flared end, creating a tight seal.
Threaded Fittings
Threaded fittings have male or female threads that screw onto matching pipe threads. They are available in various thread standards, including National Pipe Thread (NPT) and British Standard Pipe (BSP).
Push-to-Connect Fittings
Push-to-connect fittings, also known as push-fit or quick-connect fittings, feature an internal mechanism that grips the pipe when it is pushed into the fitting. These fittings often include a release mechanism to easily disconnect the pipe.
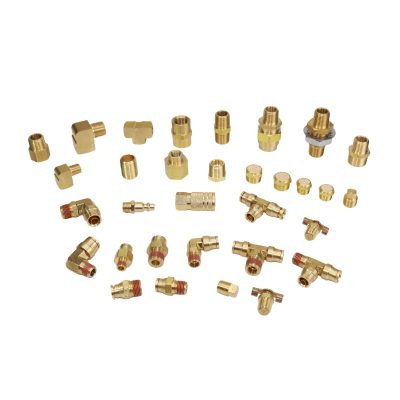
Advantages of Brass Fittings
Durability
Strength: Brass fittings are known for their strength and resilience. They can withstand high pressures and temperatures, making them suitable for a variety of demanding applications.
Longevity: The robust nature of brass ensures that fittings have a long lifespan, reducing the need for frequent replacements and maintenance.
Corrosion Resistance
Chemical Stability: Brass is highly resistant to corrosion and oxidation, which is essential for applications involving water, gas, and other potentially corrosive substances. This resistance extends the life of the fittings and maintains system integrity.
Environmental Resistance: Brass fittings perform well in a wide range of environmental conditions, from moist, humid environments to dry, arid climates, without degrading.
Adaptability
Compatibility with Various Materials: Brass fittings can be used with different types of piping, including copper, PVC, PEX, and more. This versatility makes them a go-to choice for many professionals across different industries.
Ease of Installation: The variety of brass fitting types means that there is a fitting solution for nearly every application. Whether it’s a quick-connect fitting for a rapid installation or a threaded fitting for a secure connection, brass fittings are designed to meet diverse needs.
Common Applications of Brass Fittings
Plumbing Systems
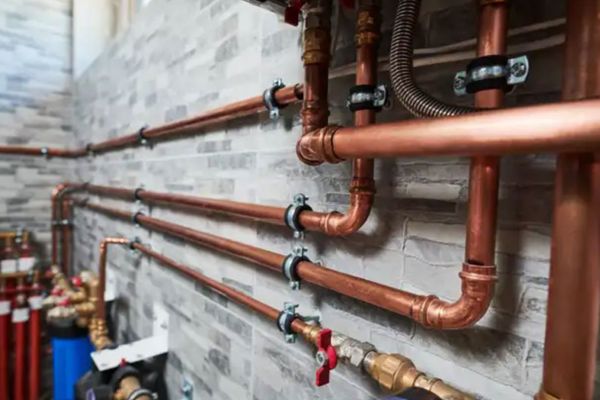
In residential plumbing, brass fittings are a preferred choice for water supply lines and hot water distribution due to their superior ability to withstand high temperatures and pressures. These fittings ensure a reliable, leak-free connection, which is crucial for maintaining the integrity of plumbing systems. Brass fittings are highly durable and can resist the common issues found in residential plumbing, such as pipe bursts and leaks, ensuring a long-lasting solution. They are used in various components, including faucets, showerheads, and pipe connectors.
In commercial plumbing, brass fittings are commonly found in public restrooms, commercial kitchens, and other high-traffic areas where durability and reliability are paramount. These fittings must endure frequent use and harsh cleaning chemicals, which can quickly wear down other materials. Brass fittings’ resistance to corrosion and physical wear makes them ideal for these demanding environments.
Gas Systems
Brass fittings are integral to natural gas and propane distribution systems, ensuring safety and efficiency. Their robustness and resistance to corrosion make them ideal for transporting gas safely. Gas systems require fittings that can handle significant pressure without degrading or leaking. Brass fittings are designed to prevent leaks and withstand the pressures involved in gas systems, making them a safe choice for both residential and commercial gas lines.
In residential settings, brass fittings are used in gas stove connections, gas heaters, and outdoor gas grills. They ensure a tight seal, preventing potentially dangerous gas leaks. In commercial settings, such as restaurants and industrial kitchens, brass fittings are used in larger gas distribution systems, ensuring that all gas appliances receive a consistent and safe supply of fuel.
HVAC Systems
In heating, ventilation, and air conditioning (HVAC) systems, brass fittings play a crucial role. They are used in various components, including condensers, evaporators, and refrigerant lines. The ability of brass fittings to handle high pressures and their resistance to corrosion contribute to the efficiency and reliability of HVAC systems.
Brass fittings are essential in maintaining the closed-loop systems required for efficient HVAC operation. They ensure that refrigerants are securely transported through the system without leaks, maintaining the system’s performance and preventing environmental contamination. In addition, brass fittings can handle the thermal expansion and contraction that occurs within HVAC systems, further enhancing their reliability.
Automotive Industry
In the automotive industry, brass fittings are used in critical components such as fuel lines, brake lines, and cooling systems. Their durability and resistance to wear make them suitable for these demanding applications. Brass fittings ensure secure connections and reliable performance under the high-stress conditions typical of automotive systems.
Fuel lines require fittings that can handle the constant flow of fuel without leaking, and brass fittings provide the necessary reliability. Brake lines use brass fittings to ensure that hydraulic brake fluid is efficiently and securely transported, ensuring the safety and responsiveness of the braking system. In cooling systems, brass fittings are used to connect various components, ensuring efficient heat dissipation and preventing overheating.
Manufacturing and Production
Brass fittings are extensively used in manufacturing and production environments, particularly in machinery and equipment that operate under high pressure. Their robustness and ability to maintain a tight seal under extreme conditions make them indispensable in these settings.
In manufacturing, brass fittings are used in hydraulic and pneumatic systems, ensuring that fluids and gases are transported efficiently and securely. They are also used in process equipment, such as reactors and mixers, where they provide reliable connections that can withstand the rigorous demands of industrial operations. Brass fittings’ resistance to corrosion ensures that they perform well even in environments with harsh chemicals and high temperatures.
Marine Applications
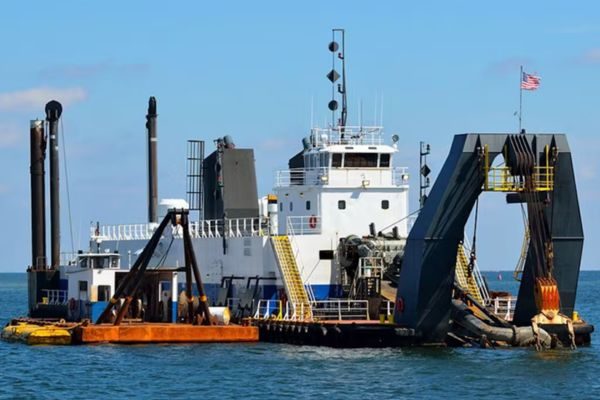
In the boating and marine industries, brass fittings are favored for their resistance to saltwater corrosion. They are used in various applications, including fuel systems, water lines, and hydraulic systems. Brass fittings ensure reliability and longevity in the harsh marine environment.
In fuel systems, brass fittings are used to connect fuel lines to engines and tanks, ensuring a secure and leak-free connection. Water lines in boats also use brass fittings, as they can withstand the corrosive effects of saltwater and the constant motion of the vessel. Hydraulic systems, which control various functions such as steering and lifting, rely on brass fittings for their robustness and reliability. These fittings ensure that hydraulic fluid is efficiently transported to where it is needed, maintaining the performance and safety of marine operations.
Food and Beverage Industry
In the food and beverage industry, maintaining hygiene and ensuring the purity of products is paramount. Brass fittings are extensively used in various systems within this sector, particularly in beverage dispensing systems. Their unique properties make them well-suited for these applications, where both durability and cleanliness are critical.
One of the key advantages of brass fittings in the food and beverage industry is their exceptional resistance to corrosion. Beverage dispensing systems often involve liquids that can be acidic or contain other corrosive agents. Brass fittings withstand these conditions without degrading, ensuring the longevity of the system and reducing the need for frequent replacements.
Choosing the Right Brass Fitting for Your Needs
Selecting the appropriate brass fitting is essential for ensuring optimal performance, safety, and longevity of your systems. Here are the key factors to consider when choosing brass fittings, as well as an overview of common standards and certifications to ensure you make an informed decision.
Factors to Consider
Pressure and Temperature Ratings
Pressure Ratings: Brass fittings come with specific pressure ratings, indicating the maximum pressure they can safely handle. Ensure the fitting’s pressure rating matches or exceeds the system’s operating pressure to prevent leaks and failures.
Temperature Ratings: Similarly, fittings have temperature ratings indicating the maximum and minimum temperatures they can withstand. Choose fittings that can handle the operational temperature range of your system, especially in high-temperature applications like HVAC or coffee machines.
Size and Threading Specifications
Pipe Size Compatibility: Ensure the brass fitting is compatible with the size of the pipes or tubing in your system. This includes both the outer diameter (OD) and inner diameter (ID) specifications.
Thread Type and Size: Brass fittings are available in various thread types (e.g., NPT, BSP) and sizes. Verify that the threading on the fitting matches the threading on your pipes to ensure a secure connection. Proper threading is crucial to prevent leaks and ensure the system operates efficiently.
Material Quality
Brass Alloy Composition: Different brass alloys can offer varying levels of strength, flexibility, and corrosion resistance. Ensure that the brass alloy used in the fitting is suitable for your specific application, particularly in environments exposed to corrosive elements or high mechanical stress.
Installation Requirements
Ease of Installation: Consider how easy the fitting is to install. Some fittings, like push-to-connect types, offer quick and straightforward installation, while others, such as flare or compression fittings, may require specialized tools and skills.
Maintenance and Accessibility: Think about the long-term maintenance needs of the fitting. Fittings that are easy to access and maintain can save time and money in the long run.
Common Standards and Certifications
ANSI (American National Standards Institute)
Ensure the brass fittings comply with ANSI standards, which cover various aspects of fitting design, including dimensions, pressure ratings, and material specifications. ANSI standards ensure that the fittings meet rigorous quality and safety criteria, making them reliable for industrial use.
ISO (International Organization for Standardization)
Look for brass fittings that meet ISO standards. ISO certifications indicate that the fittings adhere to international benchmarks for quality, safety, and efficiency. ISO standards are widely recognized and ensure the fittings are suitable for global applications.
NSF (National Sanitation Foundation)
For applications in the food and beverage industry, ensure the brass fittings have NSF certification. This certification ensures that the fittings are safe for contact with consumable products and meet stringent hygiene and safety requirements.
ASTM (American Society for Testing and Materials)
ASTM standards specify the material and performance requirements for brass fittings. Compliance with ASTM standards ensures that the fittings are made from high-quality materials and are tested for performance and durability.
By considering these factors and ensuring compliance with relevant standards and certifications, you can select the right brass fitting for your specific needs. This careful selection process guarantees that the fittings will perform as expected, ensuring the safety, reliability, and efficiency of your systems.
Conclusion
Brass fittings are indispensable across various industries due to their durability, corrosion resistance, and versatility. They are essential in plumbing, gas systems, HVAC, automotive, manufacturing, marine, food and beverage sectors, and more. Choosing brass fittings ensures reliability, efficiency, and long-term performance in your applications. For those seeking robust, high-quality fittings, exploring brass options tailored to specific needs is highly recommended. Invest in brass fittings to enhance the safety and efficiency of your systems.
FAQ
Brass fittings are used in plumbing, gas systems, HVAC systems, automotive industry, manufacturing, marine applications, and the food and beverage industry due to their durability and corrosion resistance.
Yes, brass fittings are ideal for high-pressure applications as they can withstand significant pressure without leaking or failing.
Consider the application type, pressure and temperature ratings, size and threading specifications, and ensure the fitting complies with relevant standards and certifications like ANSI, ISO, or NSF.
Yes, brass fittings are compatible with various types of pipes, including copper, PVC, PEX, and stainless steel, making them versatile for different systems.
Brass fittings are highly resistant to corrosion, making them suitable for use in environments exposed to moisture, chemicals, and other corrosive elements.
Yes, brass fittings with NSF certification are safe for use in the food and beverage industry, ensuring hygiene and compliance with health standards.