Hydraulic fluid lines serve as the circulatory system of hydraulic machinery, responsible for transmitting hydraulic fluids between components such as pumps, valves, and actuators. These lines, which include hoses, pipes, and tubes, play a crucial role in maintaining system pressure and ensuring the smooth and reliable transfer of energy. A well-designed hydraulic fluid line can optimize the performance and longevity of hydraulic systems, whereas poorly designed lines can lead to inefficiencies, pressure loss, or even system failures.
Understanding Hydraulic Fluid Lines
What Are Hydraulic Fluid Lines?
Hydraulic fluid lines are the pathways through which hydraulic fluid is transmitted within a hydraulic system, acting as the conduits for power transmission. These lines can take the form of hoses, pipes, or tubes and are designed to transport hydraulic fluids between key components such as pumps, actuators, cylinders, and valves. The primary function of hydraulic fluid lines is to ensure the efficient transfer of hydraulic fluid, which in turn generates the force needed to power hydraulic machinery.
Hydraulic fluid lines must withstand various operating conditions such as high pressure, extreme temperatures, and external mechanical stresses, making the proper design and material selection crucial for system integrity. Depending on the application and environment, these lines may be flexible or rigid, and the choice between hoses, pipes, or tubes often depends on factors like pressure rating, flexibility, and the need for easy routing.
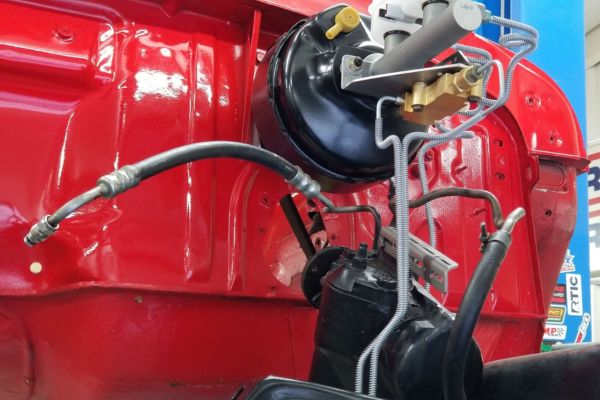
Overview of Types of Hydraulic Fluid Lines
Hoses: Flexible tubes made from synthetic rubber, thermoplastic, or PTFE, reinforced with steel wire or fabric. Hydraulic hoses are ideal for systems requiring flexibility and are commonly used in mobile machinery or applications with moving parts.
Pipes: Rigid, seamless steel or stainless steel pipes that provide durable and high-pressure fluid transmission. Pipes are typically used in stationary applications where flexibility is not needed.
Tubes: Tubing is also rigid but lighter than pipes and is often used in medium- to high-pressure applications. Tubes are often bent or formed to fit specific system designs and are commonly found in industrial equipment.
Importance in Hydraulic Systems
Hydraulic fluid lines are vital to maintaining consistent pressure and fluid flow within a hydraulic system. Properly designed lines ensure that hydraulic fluid moves efficiently, with minimal loss of pressure or energy. This fluid transfer enables the system to deliver the necessary power to actuators and cylinders, allowing hydraulic machinery to perform tasks such as lifting, pressing, or rotating with precision and strength.
Key Principles of Hydraulic Line Modeling
Fluid Dynamics in Hydraulic Lines
Fluid dynamics play a critical role in determining the performance of hydraulic fluid lines. In hydraulic systems, the movement of fluid through pipes, hoses, or tubes generates flow, pressure, and resistance—all of which impact the overall efficiency of the system. Understanding fluid dynamics is essential for accurate hydraulic line modeling because it helps predict how fluids will behave under different operating conditions, such as pressure changes, temperature fluctuations, and varying load requirements.
Key factors that influence hydraulic line performance include:
Pressure: Pressure is the driving force that moves hydraulic fluid through the system. Maintaining consistent pressure is essential for the system to function properly. Fluid line modeling must account for pressure drops that can occur due to friction, improper line sizing, or turbulent flow, all of which can reduce the system’s efficiency.
Flow Rate: Flow rate refers to the volume of hydraulic fluid that moves through the line over a given period of time. Higher flow rates are required for systems with high demands for power or speed. Inaccurate modeling of flow rates can result in either too much or too little fluid reaching key components, which can affect the system’s performance and potentially cause damage.
Fluid Velocity: Fluid velocity is the speed at which the hydraulic fluid moves through the line. Higher velocities can cause increased turbulence, friction, and heat generation, which can degrade system components over time. In modeling, it is crucial to optimize velocity to balance system efficiency and component longevity.
Resistance: Resistance in hydraulic lines is caused by friction between the fluid and the walls of the pipes or hoses. The more resistance present in the lines, the more energy is required to maintain pressure, leading to inefficiencies. Factors such as the roughness of the material’s surface bends, and fittings contribute to resistance, and these need to be carefully modeled to minimize losses.
Material Selection and Its Impact
Choosing the right material for hydraulic fluid lines is another fundamental aspect of modeling. The material selected affects the line’s ability to handle pressure, withstand temperature variations, and resist wear. Different materials offer varying levels of fluid transmission efficiency, and the wrong material can compromise the performance of the entire system.
Steel: Steel pipes and tubes are common in high-pressure applications due to their strength and durability. Steel offers excellent resistance to pressure and thermal expansion, making it ideal for stationary systems. However, steel is rigid, heavy, and not suited for systems that require flexibility or where frequent movement occurs.
Rubber Hoses: Rubber hoses, often reinforced with steel wire or synthetic fibers, are commonly used in hydraulic systems where flexibility is essential. Rubber hoses can handle high pressures but are more susceptible to wear, especially in harsh environments or with exposure to high temperatures.
Thermoplastics: Lightweight and flexible, thermoplastic hoses provide good chemical resistance and are often used in low- to medium-pressure systems. They are suitable for mobile machinery and applications where weight is a concern.
The material chosen must match the system’s requirements, including pressure, temperature, and fluid type, to ensure long-term reliability and performance.
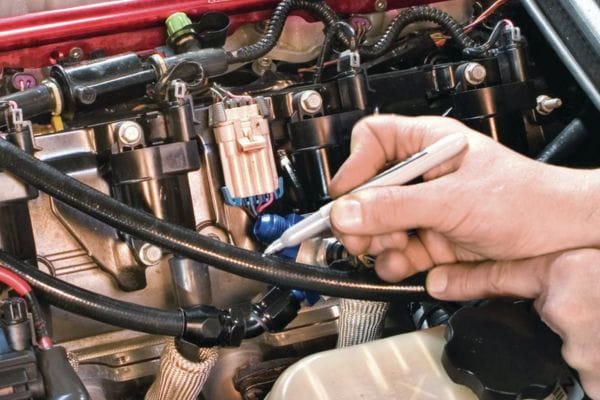
Sizing and Compatibility
One of the most crucial aspects of hydraulic line modeling is selecting the appropriate size for the fluid lines. The inner diameter (ID) and outer diameter (OD) of the lines directly influence the flow of hydraulic fluid, the system’s ability to maintain pressure, and the overall efficiency of the system.
Inner Diameter (ID): The ID of a hydraulic line determines the amount of fluid that can flow through it. If the ID is too small, it can restrict fluid flow, leading to pressure drops and reduced system efficiency. Conversely, if the ID is too large, the system may experience lower fluid velocity, resulting in sluggish performance and potential heat buildup.
Outer Diameter (OD): The OD affects the structural integrity of the line and its ability to withstand external pressures and mechanical stresses. Proper OD selection ensures that the line is durable enough for the system’s operating environment while maintaining ease of installation.
Incorrect sizing of hydraulic fluid lines can result in issues such as:
Pressure Loss: When the ID is too small for the system’s flow rate, it causes excessive friction and resistance, leading to a significant pressure drop. This reduces the system’s power and efficiency, requiring more energy to maintain performance.
Turbulence: Improperly sized lines can cause turbulence, where the fluid does not flow smoothly through the line. This can lead to increased wear on the system’s components, reduced flow control, and inefficiencies.
Cavitation: Cavitation occurs when the pressure in the hydraulic system drops below the vapor pressure of the fluid, causing vapor bubbles to form. These bubbles can collapse violently, damaging components and reducing the system’s lifespan. Incorrect line sizing, particularly with too-small diameters, can contribute to cavitation.
Techniques for Accurate Hydraulic Line Modeling
1D and 3D Modeling Techniques
Hydraulic line modeling can be approached in both one-dimensional (1D) and three-dimensional (3D) formats, depending on the complexity of the system and the desired outcomes. Each method has its advantages and is suited for different applications.
1D Modeling: One-dimensional modeling simplifies the hydraulic system into a linear framework where parameters such as pressure, flow rate, and velocity are functions of distance along the line. This approach is highly efficient for basic systems where the primary concern is fluid flow rather than complex interactions within the system. In 1D modeling, the system is typically reduced to a series of equations that govern flow dynamics, making it faster and less resource-intensive than 3D modeling. It is useful for applications where rapid evaluations of flow and pressure changes are needed.
Applications: 1D modeling is often used for early-stage design when engineers need to assess general flow characteristics and pressure losses across a hydraulic network. It’s also useful for systems where the geometry is relatively straightforward, such as long pipeline networks, simple hose systems, or when simulating basic fluid transfers.
3D Modeling: In three-dimensional modeling, the fluid and system components are represented in full spatial detail, allowing for more precise simulations of how fluid behaves in complex geometries. 3D modeling accounts for fluid dynamics in all directions and can simulate interactions like turbulence, frictional losses, and the effects of fittings, bends, or other components.
Applications: 3D modeling is used when high accuracy is required, especially in systems with complicated geometries, such as in confined spaces, where pipes and hoses have multiple bends, or in machinery where components interact closely with the fluid lines. It is also applied when studying detailed aspects of system behavior, such as how fittings or valves affect flow, or when evaluating temperature gradients across different parts of the system.
Finite Element Analysis (FEA)
Finite Element Analysis (FEA) is a crucial tool in hydraulic line modeling that helps in understanding how fluid lines behave under stress and pressure. FEA breaks down the hydraulic system into small, finite elements, allowing for the analysis of how pressure, force, and stress are distributed throughout the fluid line.
Weak Points Identification: One of the key advantages of FEA is its ability to pinpoint weak spots in the hydraulic system. By modeling stress and strain at the granular level, FEA helps engineers identify areas where pressure is concentrated, where material failure is likely to occur, or where excessive wear may happen due to repeated stress.
Pressure Distribution: FEA is also used to analyze how pressure is distributed across the system. In hydraulic lines, pressure distribution is critical for ensuring that the system maintains its efficiency. FEA allows engineers to model how fluid pressure changes as it moves through the system and how different components (such as fittings, valves, or bends) affect that pressure.
Structural Integrity: Another essential aspect of FEA is evaluating the structural integrity of the hydraulic lines. Whether made from steel, rubber, or composite materials, hydraulic lines must withstand high pressures without deforming or breaking. FEA simulates these conditions, providing valuable insights into how well the materials will perform under real-world stresses and allowing engineers to optimize material choices and line configurations.
Thermal and Pressure Considerations in Modeling
Hydraulic systems often operate in environments where temperature and pressure vary widely, and accounting for these factors is essential in hydraulic line modeling. The temperature affects both the hydraulic fluid and the materials used in the lines, while pressure determines the efficiency and performance of the system.
Incorporating Temperature Effects: Temperature variations can change the viscosity of hydraulic fluids, which in turn affects flow rates, pressure losses, and overall system performance. Cold temperatures can make fluids more viscous, reducing flow and causing sluggish operation, while high temperatures can lead to thinning of the fluid, decreasing system efficiency. Accurate hydraulic line modeling must account for these temperature-induced changes to ensure the system performs well across different operating environments.
Thermal Expansion and Contraction: The materials used in hydraulic lines (such as steel, rubber, or composites) expand and contract with temperature changes. If these changes are not incorporated into the modeling process, thermal stresses can lead to line fatigue, cracks, or leaks. Incorporating allowances for thermal expansion and contraction ensures that the hydraulic system remains structurally sound, even when temperatures fluctuate.
Pressure Impacts: High-pressure conditions, especially in dynamic applications, can lead to pressure surges that stress hydraulic lines and components. Pressure spikes, also known as “water hammer,” can damage the system if not properly accounted for. Effective modeling techniques include pressure-dampening measures and simulations that mimic real-world operating pressures to prevent failures.
Tips for Effective Hydraulic Line Modeling
Tip 1: Understand the System’s Operating Conditions
One of the most fundamental aspects of hydraulic line modeling is an in-depth understanding of the system’s specific operating conditions.
Modeling for Temperature and Pressure Variations: Hydraulic systems often operate in environments where temperatures fluctuate dramatically, from sub-zero conditions to extreme heat. Temperature changes directly impact the viscosity of hydraulic fluids and the behavior of materials used in fluid lines. If not accounted for, temperature variations can lead to inefficiencies, excessive wear, or even system failure. For instance, cold conditions may increase fluid viscosity, resulting in slower movement, while high temperatures can cause thinning of the fluid, reducing system efficiency. In hydraulic line modeling, it’s critical to simulate how temperature impacts fluid flow and pressure over the full range of anticipated operating conditions.
Environmental Factors: External environmental conditions—such as exposure to chemicals, UV light, moisture, or dust—also affect how hydraulic lines perform. For example, hoses and pipes exposed to outdoor environments might face accelerated wear and degradation from UV light or chemical exposure. Incorporating these environmental factors into the modeling process ensures the right materials and designs are chosen to withstand these challenges over time.
Understanding these factors early in the modeling process allows for more precise simulations and ensures the hydraulic lines meet the requirements of the operating environment.
Tip 2: Factor in Line Flexibility and Movement
Hydraulic systems often require both rigid and flexible fluid lines, depending on the application. Flexibility plays a significant role in how hydraulic lines behave under stress, movement, and vibration, and this must be accurately reflected in the model.
Flexible vs. Rigid Lines: Flexible hoses are commonly used in systems that require movement or where space constraints make rigid lines impractical. However, flexible lines can experience wear and tear from repeated bending, vibration, or high pressures. These lines need to be reinforced and placed in areas where movement will not cause excessive strain. On the other hand, rigid pipes or tubes are better suited for stationary applications and can handle higher pressures without deformation. However, they require precise routing to avoid stress points that can lead to cracks or fractures.
Design Considerations: When designing hydraulic lines, it is essential to account for potential movement and vibration within the system. Flexible hoses should be modeled with enough slack to allow for movement without being overstretched. Vibration dampeners or brackets can also be included to reduce wear. Additionally, the use of swivel joints or live swivels at connection points can help reduce stress on the lines by allowing them to move freely without twisting or bending, which is crucial in mobile or high-vibration environments.
By modeling both flexible and rigid lines appropriately, engineers can reduce wear, prevent premature failures, and ensure system longevity.
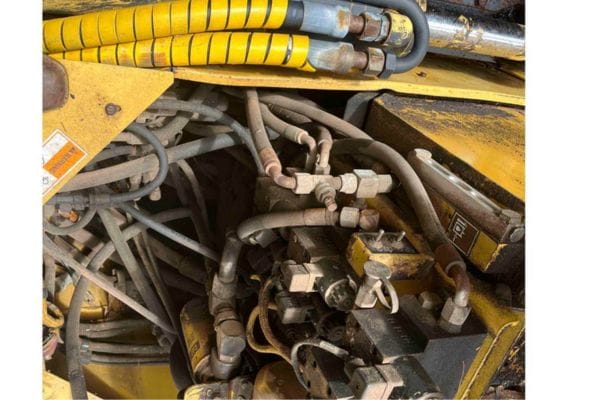
Tip 3: Minimize Pressure Drops
Pressure drop is a common issue in hydraulic systems, and it can severely affect system performance. Reducing pressure loss across hydraulic lines is critical to ensuring the system operates efficiently and reliably.
Reducing Friction: One of the primary causes of pressure loss in hydraulic lines is friction between the fluid and the inner surface of the line. Minimizing this friction is crucial for maintaining pressure and flow rates. Using smooth-bore hoses or tubes with low-friction materials can reduce the amount of resistance the fluid encounters, thus reducing pressure loss.
Correct Line Sizing: Line sizing plays a significant role in minimizing pressure drops. Hydraulic lines with a smaller inner diameter (ID) can restrict flow, leading to increased friction and pressure loss. Conversely, lines that are too large may reduce fluid velocity, causing inefficient system operation. The key is to model and select lines that are appropriately sized for the system’s flow rate and pressure requirements.
Smooth Bends and Routing: Hydraulic systems often require lines to be routed through tight spaces, which can lead to sharp bends. These bends cause turbulence and increase pressure drop. By using smooth, gradual bends instead of sharp angles, engineers can maintain a more consistent flow. Routing lines in a way that minimizes bends, loops, and intersections is essential for reducing resistance and ensuring smooth fluid movement.
Tip 4: Account for Fluid Properties
Fluid properties—such as viscosity and density—are integral to hydraulic line modeling. These characteristics influence how fluids move through lines, how pressure is maintained, and how the system performs under different operating conditions.
Viscosity: Fluid viscosity is a measure of its resistance to flow. Higher viscosity fluids (thicker fluids) will flow more slowly and encounter more resistance as they move through the system, which can lead to pressure loss and reduced efficiency. Conversely, low-viscosity fluids may flow too quickly, creating turbulence or cavitation issues. When modeling hydraulic lines, it’s important to consider how fluid viscosity changes with temperature. Cold environments increase viscosity, while hot environments decrease it. The model should account for these variations to maintain optimal system performance across different temperatures.
Density: Fluid density impacts the amount of force required to move the fluid through the system. Denser fluids require more energy to move, which can increase system pressure and stress on components. When modeling hydraulic lines, engineers should adjust line sizing and pressure settings based on the specific fluid’s density to ensure smooth operation.
By considering the properties of the hydraulic fluid, engineers can optimize line design, avoid common flow issues, and ensure the system operates efficiently across various conditions.
Common Challenges in Hydraulic Line Modeling and How to Overcome Them
Handling Complex Geometries
One of the biggest challenges in hydraulic line modeling is dealing with complex geometries, especially in systems with confined spaces, multiple bends, or irregular layouts. These complex configurations can significantly affect fluid flow, pressure distribution, and overall system efficiency.
Challenges in Complex Spaces: In confined or irregular spaces, hydraulic lines often need to navigate sharp corners, bends, and tight clearances, which can introduce issues like turbulence, pressure drops, and stress on the lines. Fittings, joints, and connections in these areas can further complicate the flow, as they create resistance and potential leak points.
Simplifying Geometry Without Compromising Accuracy: To overcome these challenges, hydraulic line modeling requires a balance between simplicity and accuracy. One approach is to use smooth, gradual bends rather than sharp angles, which helps maintain fluid flow and reduces turbulence. Additionally, designers can create simplified models that focus on key flow areas, such as bends and critical fittings, while minimizing the complexity of less crucial sections. Advanced software tools also allow for detailed 3D models that simulate fluid flow around bends and through tight spaces, providing insights into potential problem areas.
Routing Considerations: Careful routing of hydraulic lines can alleviate many geometric challenges. Routing lines in parallel, reducing the number of fittings and sharp angles, and ensuring sufficient spacing between components all contribute to smoother fluid flow and reduced pressure losses.
Pressure Transients and Water Hammer
Pressure transients, also known as water hammers, occur when there is a sudden change in fluid velocity, causing shockwaves to propagate through the hydraulic system. These surges can cause significant damage to hydraulic lines, fittings, and system components, making it a crucial factor to consider in hydraulic line modeling.
Overview of Water Hammer Effects: Water hammer occurs when there is a rapid change in flow, such as when valves open or close suddenly, causing a pressure spike. This spike can travel through the hydraulic lines, leading to stresses on the system that can result in bursts, leaks, or component failure. In hydraulic systems, water hammer can also lead to cavitation, where vapor bubbles form and collapse, damaging the inner surfaces of the lines.
Mitigating Pressure Transients: Several techniques can be employed to mitigate the impact of water hammer in hydraulic line models:
Gradual Valve Operation: By designing models that account for gradual valve opening and closing times, fluid flow changes can be more controlled, reducing pressure spikes.
Using Surge Tanks or Accumulators: These devices can absorb pressure surges, reducing the impact of the water hammer on the system. Including them in hydraulic line models helps smooth out pressure transients.
Pressure Relief Valves: Placing pressure relief valves in the system can allow for controlled release of excess pressure, preventing damage from sudden surges.
Fluid Dampening: Modeling fluid dampeners can help absorb energy from pressure spikes, reducing the chance of water hammer effects.
By incorporating these techniques, models can better simulate real-world hydraulic systems and ensure that pressure transients are effectively mitigated.
Wear and Aging of Materials
Hydraulic lines and components are subject to wear and aging over time, which can impact system performance and lead to potential failures. Modeling the effects of wear and material degradation is crucial to predicting the lifespan of a hydraulic system and planning maintenance strategies.
Modeling Material Wear and Degradation: Over time, hydraulic lines experience wear due to friction, pressure cycling, temperature fluctuations, and environmental factors such as exposure to chemicals or UV radiation. This wear can cause thinning of the walls of hoses, pipes, or tubes, leading to leaks, bursts, or failure of fittings. In high-pressure systems, repeated stress can also cause micro-cracks to form, gradually weakening the material.
Incorporating Life Cycles into Modeling: To effectively account for wear and aging in hydraulic line modeling, engineers must consider the expected lifespan of materials under different operating conditions. This includes:
Pressure Cycling: Modeling how repeated pressure cycles cause material fatigue over time.
Temperature Stress: Understanding how temperature fluctuations contribute to material degradation, such as cracking in colder environments or softening in extreme heat.
Corrosion and Abrasion: In environments where hydraulic lines are exposed to harsh chemicals or abrasive particles, corrosion or abrasion can shorten the lifespan of the lines. Modeling should account for material degradation rates in these conditions.
Predictive Maintenance: By incorporating wear and aging data into hydraulic line models, engineers can predict when maintenance or replacement of components will be required. This proactive approach helps prevent unexpected failures and extends the lifespan of the system.
Conclusion
Accurate hydraulic line modeling plays a vital role in enhancing system performance, reliability, and safety. By predicting how fluid lines will behave under real-world conditions, engineers can prevent costly issues like pressure loss, water hammer, or premature material failure. With proper planning and modeling, hydraulic systems can operate more efficiently, reduce downtime, and extend the life of their components.
FAQ
What is hydraulic fluid line modeling?
Hydraulic fluid line modeling is the process of simulating the behavior of hydraulic fluid within hoses, pipes, and tubes to predict system performance and optimize design.
Why is accurate modeling important in hydraulic systems?
Accurate modeling helps prevent issues such as pressure loss, cavitation, and material failure, leading to improved efficiency, reliability, and longevity of hydraulic systems.
What are the key factors to consider in hydraulic line modeling?
Important factors include fluid dynamics, pressure, flow rate, material selection, line sizing, and thermal expansion.
What tools are used for hydraulic line modeling?
Common tools include SolidWorks, ANSYS, and MATLAB, which allow for simulations such as Finite Element Analysis (FEA) and Computational Fluid Dynamics (CFD).
How does pressure drop affect hydraulic systems?
Pressure drops can reduce the system’s efficiency, causing components to work harder and leading to overheating or system failure.
What is the role of fluid properties in modeling?
Fluid properties like viscosity and density affect flow behavior, pressure distribution, and system performance, making them crucial to consider in hydraulic line modeling.