Hydraulic hoses are critical components in hydraulic systems, influencing efficiency, safety, and overall system performance. Proper selection ensures that hoses can withstand the pressures and environments they encounter, ultimately affecting machinery longevity and reliability. Despite their significance, many users make common errors when selecting hydraulic hoses. These mistakes can lead to system failures, increased maintenance costs, and unsafe operating conditions. Identifying these pitfalls is essential for optimal system performance.
A. Ignoring Pressure Ratings
1. Explanation of Pressure Ratings
Pressure ratings specify the maximum pressure a hydraulic hose can withstand without failing, typically measured in PSI (pounds per square inch). These ratings are crucial for determining the suitability of a hose for specific applications, as they reflect the hose’s design and material capabilities. Understanding these ratings helps ensure that the selected hose can handle the operational pressures expected in the system.
2. Consequences of Exceeding Ratings
Operating a hydraulic hose beyond its specified pressure rating can lead to catastrophic failures such as ruptures and leaks. Such incidents not only cause equipment damage but also pose serious safety risks to personnel and bystanders. Additionally, failures can lead to significant downtime, resulting in lost productivity and costly repairs.
3. Solutions and Best Practices
To mitigate risks associated with pressure ratings, always consult the manufacturer’s specifications when selecting a hose. It is advisable to choose hoses that can handle pressures exceeding the expected operational limits by at least 20-30%. This practice provides an added safety margin, ensuring reliable performance and reducing the likelihood of failure under unexpected conditions. Regularly inspect hoses for signs of wear and monitor system pressures to maintain operational safety.
B. Incorrect Hose Size
1. Importance of Correct Sizing
Choosing the proper hose diameter is critical for ensuring optimal flow rates within hydraulic systems. A correctly sized hose minimizes pressure drops and enhances system efficiency. When hoses are sized appropriately, they help maintain consistent fluid velocity, reducing turbulence and preventing potential cavitation, which can cause damage to hydraulic components. Proper sizing also allows hydraulic actuators to respond quickly and accurately, leading to improved overall performance. Furthermore, an adequately sized hose can reduce the wear and tear on both the hose and the connected components, prolonging the life of the entire hydraulic system.
2. Issues Caused by Improper Sizing
Using hoses that are too small can significantly restrict fluid flow, which can lead to overheating and eventual system malfunctions. Insufficient flow rates can result in sluggish actuator movements, reduced operational efficiency, and may even prevent hydraulic systems from reaching their peak performance capabilities. Additionally, restricted flow can cause increased wear on pumps and other hydraulic components due to higher operating pressures, potentially leading to costly repairs or replacements. Conversely, oversized hoses can create excessive pressure drops, which may lead to inefficient operation and increased energy consumption. This inefficiency can manifest as slower response times in actuators and an overall decline in system reliability, ultimately affecting the entire hydraulic system’s performance.
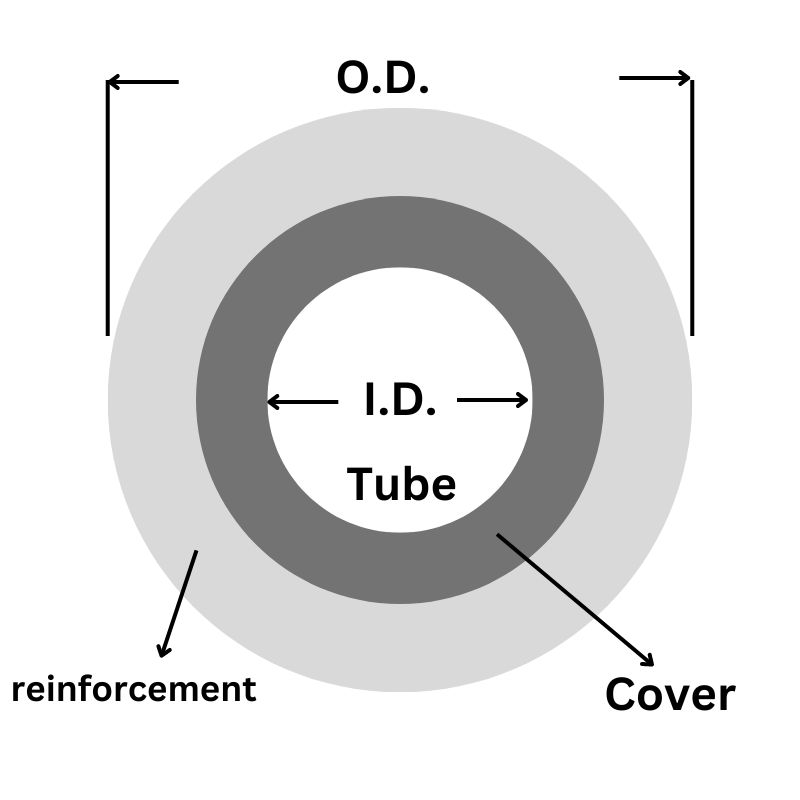
3. Guidelines for Determining the Right Size
To determine the appropriate hose size for specific applications, it is essential to evaluate the required flow rates and refer to hydraulic system design guidelines. Begin by calculating the system’s maximum flow demand, taking into account the operating conditions and hydraulic fluid properties. Key factors to consider include the length of the hose run, the type of fluid being used, and the specific requirements of connected components. It’s also important to assess the expected temperature and pressure conditions, as these can influence the selection of hose materials and sizes. Consulting with hose manufacturers and utilizing their sizing charts can provide valuable insights into proper sizing, ensuring that the hose selected will optimize system performance and reliability. Additionally, utilizing simulation tools or software designed for hydraulic system design can aid in accurately determining the most effective hose size for the application.
C. Not Considering Fluid Compatibility
1. Different Types of Hydraulic Fluids
Hydraulic systems utilize a diverse range of fluids, including mineral oils, water-based fluids, and biodegradable options. Mineral oils are commonly used due to their excellent lubricating properties and wide availability. Water-based fluids, such as water-glycol mixtures, offer fire-resistant properties but can lead to corrosion if not managed correctly. Biodegradable fluids are gaining popularity for their environmental benefits, particularly in applications where fluid leaks can harm ecosystems. Each type of hydraulic fluid possesses unique chemical and physical properties, such as viscosity, pH, and temperature stability, which can significantly influence the performance and longevity of the hose materials in contact with them.
2. Effects of Incompatible Materials
Selecting hoses that are not compatible with the hydraulic fluid can have serious repercussions, leading to the degradation of the hose materials. This incompatibility can manifest in various ways: swelling may occur if the hose material absorbs the fluid, while exposure to certain chemicals can cause the hose to crack or become brittle. Leaks may develop as the integrity of the hose is compromised, which not only leads to loss of hydraulic fluid but can also create hazardous working conditions. Such failures can result in unexpected downtime, costly repairs, and, in some cases, safety incidents. Therefore, understanding the compatibility of hose materials with the specific hydraulic fluids used is essential for maintaining system reliability.
3. How to Choose Compatible Hoses
To ensure the selected hose material is appropriate for the hydraulic fluid in use, always consult the manufacturer’s compatibility charts. These charts typically provide valuable information on which materials are suitable for various fluids. Additionally, consider both the chemical properties of the fluid and the operating conditions, such as temperature and pressure, which can affect material behavior. When selecting hoses, it is also beneficial to consider the full range of conditions the hose may encounter, including potential exposure to contaminants or other chemicals in the environment. Engaging with suppliers or manufacturers who can provide expert advice on compatibility and offering samples for testing can further help ensure that the chosen hose will maintain performance and durability in the specific hydraulic application. Regular monitoring and inspection of the hose condition of the fluids being used is also advisable to catch any signs of degradation early.
D. Overlooking Temperature Ratings
1. Importance of Temperature Ratings
Temperature ratings are a critical consideration in the selection of hydraulic hoses. Hoses must be capable of withstanding not only the temperature range of the hydraulic fluid but also the environmental conditions they will encounter. Operating at extreme temperatures can affect the hose’s material properties, compromising its performance and safety. Properly rated hoses ensure that they can function effectively without degrading, maintaining system efficiency and reliability over time.
2. Risks of High Temperatures
Excessive temperatures pose significant risks to hydraulic hoses. High thermal exposure can lead to the weakening of hose materials, making them more susceptible to failure. Common consequences of overheating include bulging, which indicates internal pressure issues, and bursting, which can create hazardous conditions within the hydraulic system. These failures not only disrupt operations but can also result in costly repairs, safety incidents, and potential environmental damage due to fluid leaks. Thus, understanding and adhering to temperature ratings is essential to prevent these issues and ensure the safe operation of hydraulic systems.
3. Recommendations for Selecting Temperature-Resistant Hoses
When selecting hoses for hydraulic applications, it is crucial to consider those rated for higher temperatures than those anticipated in the application. This safety margin accounts for unexpected spikes in temperature and ensures reliable performance under varied conditions. Additionally, utilizing insulation or protective sleeves can provide an extra layer of protection against thermal extremes, especially in environments where temperatures can fluctuate significantly. Always refer to the manufacturer’s specifications for temperature ratings and consult with experts when necessary to make informed choices. Regular monitoring of operating temperatures can further aid in identifying potential risks and ensuring that hoses continue to perform safely and effectively over time.
E. Neglecting Environmental Factors
1. Impact of Environmental Conditions on Hoses
Hydraulic hoses often operate in harsh environments that can significantly impact their performance and lifespan. Exposure to extreme temperatures can cause materials to become brittle or overly flexible, compromising their integrity. UV radiation can degrade rubber and plastic materials, leading to cracks and premature failure. Additionally, hoses may come into contact with various chemicals that can corrode or weaken their structure. Mechanical abrasion from constant movement or contact with abrasive surfaces can also wear down hoses, leading to leaks and failures. Understanding these environmental challenges is essential for ensuring the longevity and reliability of hydraulic systems.
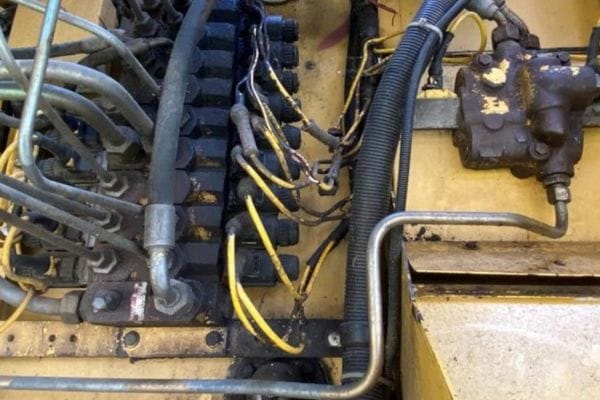
2. Choosing Hoses for Different Environments
Selecting hoses specifically designed to withstand environmental challenges is crucial for maintaining system integrity. For instance, in rugged terrains, hoses with abrasion-resistant covers can provide the necessary protection against physical wear. In outdoor applications, choosing UV-stabilized materials can help prevent degradation due to prolonged sun exposure. Additionally, hoses should be selected based on their chemical resistance properties to ensure they can withstand any fluids they may encounter in their environment. Consulting manufacturer specifications and compatibility charts can guide the selection of hoses suited for specific environmental conditions.
F. Poor Installation Practices
1. Common Installation Errors
Improper installation of hydraulic hoses can lead to a range of issues that compromise both their integrity and functionality. Common errors include kinks, twists, and undue tension, which can restrict fluid flow and create points of weakness in the hose. These mistakes often result in early wear and can trigger sudden failures within hydraulic systems, leading to costly downtime and repairs. Understanding and addressing these potential pitfalls is crucial for maintaining optimal performance and safety in hydraulic applications.
2. Importance of Proper Techniques
Utilizing correct installation techniques is vital for minimizing wear and enhancing the longevity of hydraulic hoses. Proper installation not only helps to prevent immediate issues like kinks and twists but also ensures that the hose can withstand operational stresses over time. By following established installation practices, technicians can mitigate the risk of premature failure, thereby protecting both the hose and the entire hydraulic system. Moreover, investing time in proper installation techniques can lead to significant long-term cost savings through reduced maintenance and replacement needs.
3. Installation Best Practices
To achieve optimal results when installing hydraulic hoses, it is essential to follow manufacturer guidelines closely. Begin by selecting the appropriate fittings that match the hose and application requirements. Ensure that the hose is adequately supported along its run to prevent sagging or movement that can lead to stress points. Avoid sharp bends and twists, as these can create high-stress areas that may lead to leaks or ruptures. Additionally, regularly inspect the installation to ensure that no movement or tension develops over time, and make adjustments as necessary to maintain hose integrity. By adhering to these best practices, you can enhance the reliability and performance of hydraulic systems significantly.
G. Ignoring Maintenance and Inspection
1. Importance of Regular Checks
Regular maintenance and inspection of hydraulic hoses are essential for identifying signs of wear and potential failures before they escalate into serious issues. Proactive checks can significantly reduce the risk of unexpected breakdowns, which can lead to costly repairs and operational downtime. By routinely assessing the condition of hoses, operators can catch minor problems early on, allowing for timely interventions that preserve the overall health of the hydraulic system. This proactive approach not only enhances system reliability but also extends the lifespan of the hoses, making maintenance a critical component of effective hydraulic management.
2. Signs of Wear and Failure
Being vigilant for indicators of wear is crucial for maintaining hydraulic hose integrity. Common signs include cracks, leaks, discoloration, and bulging. Cracks may indicate material fatigue, while leaks can signal severe degradation or ruptures that could lead to system failures. Discoloration often results from exposure to harsh environmental conditions or incompatible fluids, and bulging can signify internal pressure issues or excessive heat. Recognizing these signs early is vital, as they can indicate that a hose is nearing the end of its service life and may require immediate replacement to prevent catastrophic failure.
3. Recommended Maintenance Routines
To ensure the longevity and reliability of hydraulic hoses, establish a routine inspection schedule. This schedule should include cleaning hoses to remove contaminants that can cause wear and testing them under operational conditions to verify performance. Regularly inspect for any signs of wear or damage, and check all fittings and connections for leaks. Additionally, keep documentation of inspections and maintenance performed to track hose condition over time. Implementing these maintenance routines not only helps ensure that hoses remain in good condition and meet safety standards but also fosters a culture of preventive care that enhances the overall reliability and efficiency of the hydraulic system.
Conclusion
Proper hose selection is crucial for enhancing both the performance and safety of hydraulic systems. By considering factors such as pressure ratings, fluid compatibility, temperature tolerances, and environmental conditions, operators can ensure that their hydraulic hoses will perform reliably under various operational scenarios. This careful selection process not only improves efficiency but also minimizes the risk of unexpected failures, contributing to the overall success of hydraulic applications.
FAQ
What is the most important factor to consider when selecting a hydraulic hose?
The most critical factor is ensuring the hose can handle the pressure ratings required for your specific application. Always refer to the manufacturer’s specifications.
How can I tell if my hydraulic hose is the correct size?
Ensure the hose diameter matches the flow rate requirements of your system. Improper sizing can lead to inefficiencies and potential failures.
Why is fluid compatibility important for hydraulic hoses?
Using hoses that are not compatible with the hydraulic fluid can cause material degradation, leading to leaks and system failures.
What temperature ratings should I look for in hydraulic hoses?
Choose hoses rated for temperatures higher than those encountered in your application to provide a safety margin against overheating.
How often should I inspect my hydraulic hoses?
Regular inspections are recommended, ideally on a monthly basis, to identify signs of wear, leaks, or damage before they lead to failures.
What are the common signs that a hydraulic hose needs to be replaced?
Look for cracks, leaks, discoloration, or bulging in the hose. Any of these signs may indicate that the hose is nearing the end of its service life.