Incorrectly matching hoses and fittings can lead to leaks, inefficiency, or catastrophic failures in a hydraulic system. Even slight mismatches in size or material compatibility can cause issues that compromise the entire system’s performance. A poor connection between the hose and fitting can result in pressure loss, contamination, and even equipment damage, making it essential to match the correct hose size and fitting type to maintain system reliability.
What is Hydraulic Hose Size?
Understanding hose size is key to designing and maintaining a hydraulic system that functions efficiently and safely. Hydraulic hoses come in a variety of sizes to accommodate the needs of different fluid types, pressure levels, and flow requirements. The size of a hydraulic hose directly impacts fluid flow, pressure rating, and overall system performance. Selecting the wrong hose size can lead to inefficiency, equipment damage, and even safety hazards.
Defining Hydraulic Hose Size: The Basics
Hose size refers to the internal diameter of the hose, which determines the flow capacity of the system. It’s usually specified in inches or millimeters. The hose’s size is typically denoted by two primary measurements: the inside diameter (ID), which is the actual opening where the fluid passes through, and the outside diameter (OD), which refers to the total size of the hose including its reinforcement layers. Hose size selection is critical as it influences not only the fluid flow but also the pressure rating and overall system efficiency.
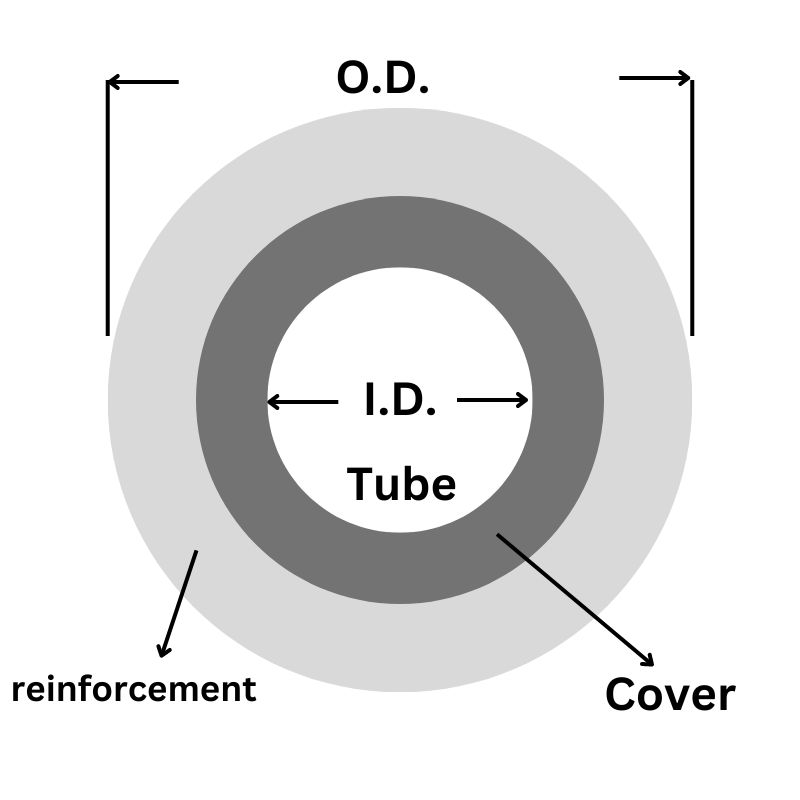
How Hose Size Affects Fluid Flow and System Efficiency
The hose size is directly related to how much fluid can flow through the system. A larger hose allows for greater fluid flow, which is necessary for high-flow systems, while a smaller hose is suitable for lower flow rates. However, the wrong size hose—either too large or too small—can cause performance issues:
Too Small: A hose with too small of a diameter creates resistance, causing friction loss and reducing the flow of fluid. This leads to pressure drop, overheating, and inefficiency, potentially damaging hydraulic components.
Too Large: A hose that’s too large may allow fluid to flow too easily, reducing the required pressure in the system, potentially causing issues with hydraulic performance and causing an inefficient use of energy.
Ensuring the right hose size helps maintain consistent flow rates, reduces energy consumption, and ensures the system runs optimally without overworking the pump or causing unnecessary pressure fluctuations.
Common Terminology in Hydraulic Hose Sizing
Understanding the terminology used in hydraulic hose sizing helps ensure proper hose selection and installation. Some common terms include:
Inside Diameter (ID): The internal measurement of the hose through which fluid flows. It’s one of the most critical factors in determining how much fluid can pass through the hose.
Outside Diameter (OD): The external measurement of the hose, which is important for fitting compatibility and understanding how the hose fits within the system layout.
Nominal Size: Often used to simplify communication, the nominal size refers to the general size designation of a hose (e.g., ½ inch, 1 inch) but doesn’t always represent the exact internal diameter.
Pressure Rating: The maximum pressure that a hose can safely handle. Hydraulic hoses are rated for different pressure ranges, and the rating is usually tied to the size and material of the hose.
Reinforcement Layers: The layers of material (such as steel or textile) within the hose that provide strength and support to withstand internal pressure and external forces.
Factors to Consider When Selecting Hydraulic Hose Size
Selecting the correct hose size is crucial for the performance and safety of a hydraulic system. Several key factors influence this decision, ranging from the hose diameter to system design.
Hydraulic Hose Diameter and Its Role in System Flow
The hydraulic hose diameter plays a significant role in determining the flow rate of the system. The larger the internal diameter (ID) of the hose, the greater the volume of fluid that can flow through it. Here’s how diameter affects system performance:
Flow Rate: A larger hose diameter provides less resistance to fluid movement, allowing for a higher flow rate. This is crucial for high-flow applications where maintaining efficient fluid movement is necessary.
Pressure Drop: If the hose diameter is too small, it can cause a significant pressure drop, reducing the system’s overall efficiency. Fluid traveling through smaller hoses faces more resistance, leading to energy loss and potential overheating.
Friction Loss: A smaller hose diameter increases frictional resistance, which in turn reduces the efficiency of the system, leading to higher operating costs and potential equipment strain.
In summary, the hose diameter must be chosen in line with the required flow rate and pressure to ensure smooth, efficient system operation.
Pressure Rating: Why It Matters for Hose Size Selection
The pressure rating of a hydraulic hose is one of the most critical aspects of selecting the correct hose size. It determines the maximum pressure the hose can safely withstand before failure. Pressure ratings vary based on the hose’s material, construction, and diameter. Here’s why it’s important:
Matching Pressure Needs: Hydraulic systems operate at specific pressure levels. If the pressure exceeds the hose’s rating, the hose can burst, leading to fluid leaks, system damage, and safety risks. It’s crucial to match the hose’s pressure rating with the system’s requirements to avoid failure.
Impact of Hose Diameter on Pressure: Larger diameter hoses generally have a lower pressure rating compared to smaller diameter hoses. This is because larger hoses often have less reinforcement and are more susceptible to expanding under high pressure. Smaller hoses, on the other hand, can often handle higher pressure due to their reinforced construction.
Safety Factor: Always choose a hose with a pressure rating higher than the system’s operating pressure to provide a safety margin and prevent failure in unexpected conditions.
Fluid Type and Temperature: Influencing Hose Size and Material
The fluid type and temperature in a hydraulic system influence the material properties and sizing of the hose. Different fluids, such as water-based, oil-based, or synthetic fluids, interact differently with hose materials. Here’s how these factors affect hose selection:
FluidCompatibility: Certain hose materials are better suited for specific fluids. For example, hoses designed for petroleum-based fluids may not be compatible with water-based fluids, which can lead to hose degradation. Choosing a hose with compatible material properties is crucial to ensure long-term performance.
Temperature Range: Hydraulic systems often operate in a wide range of temperatures, from very low to extremely high. Hoses must be able to handle these temperature extremes without deteriorating. High temperatures can cause hoses to become brittle, leading to cracking, while low temperatures may make hoses more rigid and prone to failure.
Viscosity and Flow Characteristics: The type of fluid also impacts the viscosity, which affects how easily the fluid flows through the hose. More viscous fluids require larger diameter hoses to reduce resistance and maintain adequate flow rates. At high temperatures, viscosity decreases, potentially requiring adjustment in hose size to prevent fluid flow problems.
Environmental Conditions and Their Impact on Hose Selection
Environmental conditions such as exposure to UV rays, chemicals, abrasives, and extreme weather can significantly impact the performance and longevity of hydraulic hoses. When selecting a hose, consider the following environmental factors:
UV Exposure: Continuous exposure to sunlight can degrade hose materials, particularly rubber-based hoses. If your hydraulic system operates outdoors, it’s essential to choose hoses with UV-resistant materials or coatings to prevent premature wear.
Chemical Exposure: If the hydraulic system is used in an environment where the hose may come into contact with chemicals (e.g., oils, solvents, or acids), selecting a hose with the appropriate chemical resistance is crucial. Some hose materials are more resistant to certain chemicals than others.
Abrasion and Physical Damage: In environments where hoses may be exposed to sharp objects, dirt, or abrasives, it’s necessary to choose hoses with higher abrasion resistance. Hoses designed for high-abrasion areas often feature external covers made from materials like steel wire braid or a tough rubber layer.
Temperature Extremes: Hoses in extremely hot or cold environments must be chosen carefully to withstand temperature fluctuations without cracking, stiffening, or losing flexibility. Thermoplastic hoses are ideal for extreme temperature environments.
System Design and Its Role in Choosing the Right Hose Size
The overall system design is a critical factor in selecting the appropriate hose size. The layout, fluid flow requirements, pressure conditions, and expected operating environment all play a role in determining the best hose size. Key system design considerations include:
Layout and Routing: The path the hose takes in the system influences its size and flexibility. Tight bends and long routing may require hoses with smaller diameters or specific reinforcement to prevent kinking or damage.
Pressure and Flow Conditions: Hydraulic systems with higher pressure and flow demands may need larger hoses or more advanced materials to handle the increased load. Ensuring the hose size matches the system’s pressure and flow capacity is essential for optimal performance.
Space Constraints: In systems with limited space, a smaller diameter hose may be necessary to fit within the constraints of the design. However, the smaller hose must still meet the system’s flow and pressure requirements.
System Modularity: If the hydraulic system is modular and components are interchangeable, standardizing hose sizes across the system can simplify maintenance and repairs.
How to Match Hose Size to Fittings: A Step-by-Step Guide
When selecting the correct hose size for your system, it’s essential to follow a methodical approach. Matching the right hose size to fittings ensures optimal performance, safety, and system longevity.
Step 1: Determine Your System’s Fluid Flow and Pressure Needs
Before selecting the hose size, it’s crucial to understand the flow and pressure requirements of your system. The flow rate and system pressure dictate the size and type of hose needed to operate efficiently without overloading components.
Fluid Flow: Determine the flow rate required by your system, typically measured in gallons per minute (GPM) or liters per minute (LPM). The higher the flow rate, the larger the hose diameter you’ll need to ensure adequate fluid movement.
System Pressure: Identify the operating pressure of your system (usually measured in PSI or bar). The hose should be rated for the system’s maximum pressure to prevent hose failure.
Peak Pressure: Consider peak pressure or pressure spikes that may occur during startup or load changes. The hose should handle not only the typical operating pressure but also brief pressure surges that could exceed the normal levels.
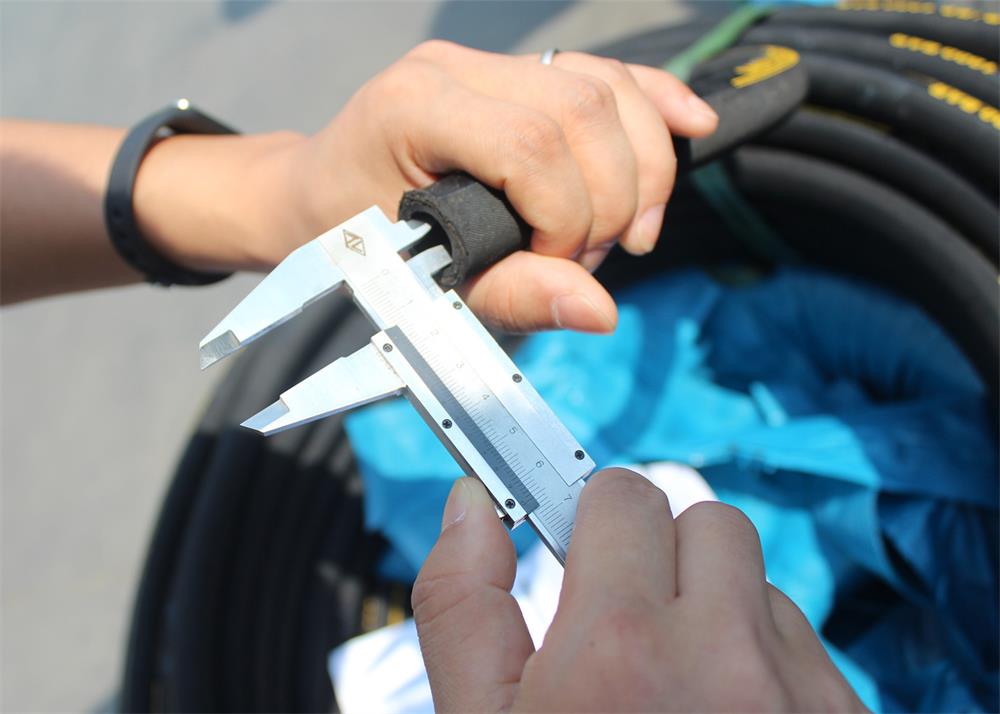
Step 2: Choose the Appropriate Hose Type for Your Application
Not all hoses are suitable for every application, so it’s important to select the right hose material and type based on the fluid being transported and environmental conditions. Here’s what to consider:
Fluid Type: Choose a hose compatible with the fluid in your system, such as oil, water, chemicals, or air. Some hoses are specially designed to resist certain fluids, such as petroleum-based oils or water-based fluids.
Temperature Range: Select a hose that can withstand the temperature of the fluid and environmental conditions. High temperatures can degrade hose material, while low temperatures can make hoses brittle.
Environmental Factors: Consider external factors like UV exposure, chemicals, abrasion, and mechanical stress. For example, hoses used outdoors or in harsh environments should be resistant to UV rays and chemicals.
Reinforcement: Some applications may require a reinforced hose to handle high pressures or provide better flexibility. Consider if your system needs a braided, spiral, or textile-reinforced hose.
Step 3: Select the Correct Hose Diameter Based on Pressure and Flow
The diameter of the hose directly impacts fluid flow and system efficiency. To select the correct diameter, use the following formula and guidelines:
Flow Rate Formula: Use the flow rate and the pressure drop (the loss of pressure as the fluid travels through the hose) to determine the right hose diameter. A common formula for flow rate in a pipe or hose is:
Q=A×V
Where:
Q is the flow rate (in GPM or LPM),
A is the cross-sectional area of the hose (in square inches or square millimeters),
V is the fluid velocity (in feet per second or meters per second).
Note: The ideal flow rate should balance between sufficient flow and preventing excessive pressure drop.
Pressure Considerations: If your system requires higher pressures, you’ll need a smaller diameter hose to maintain the appropriate pressure levels. Conversely, a hose that’s too large can reduce the system’s pressure, resulting in inefficiency.
Viscosity and Flow Resistance: If your fluid is more viscous (e.g., oil-based fluids), you may need a larger hose diameter to reduce resistance and maintain the desired flow rate. For low-viscosity fluids, such as water, you can generally use a smaller diameter hose.
Nominal Size: The hose’s nominal size refers to its general size designation (e.g., ½ inch, 1 inch), but keep in mind that the internal diameter (ID) is the critical measurement for accurate sizing.
Step 4: Match the Fitting Type and Size to Your Hose
Now that you’ve determined the required hose diameter and selected the right hose material and type, it’s time to focus on matching the fitting size with your hydraulic hose. This step ensures a proper connection between the hose and the fitting, preventing leaks, pressure loss, and other system inefficiencies.
Here’s how to calculate the correct fitting size:
Determine the Hose Inside Diameter (ID)
The inside diameter (ID) of the hose is the critical measurement for matching with the fitting. The ID directly impacts fluid flow and pressure ratings. Ensure that the fitting’s internal diameter matches or slightly exceeds the hose’s ID to maintain smooth fluid flow and prevent restriction.
Identify the Fitting Type and Size
Hydraulic fittings come in various types and sizes, each designed to fit specific hose types and applications. Some common fitting types include:
BSP (British Standard Pipe) fittings
NPT (National Pipe Thread) fittings
JIC (Joint Industry Council) fittings
SAE (Society of Automotive Engineers) fittings
Metric fittings
The fitting type and size should align with the hose’s size and system requirements. Be sure to know the thread type (e.g., BSPP, NPTF) and connection style (e.g., flare, swivel, crimp) when selecting the fitting.
Measure the Fitting‘s Outside Diameter (OD)
For most fittings, the outside diameter (OD) will be the important measurement to ensure it fits snugly into the hose’s fitting port. The OD of the fitting should match the hose’s fitting port size (which may be determined by the system connection or valve port size).
Thread Compatibility: Ensure that the threads of the fitting match the corresponding threads inside the hose end or the coupling system. Mismatched threads can result in leaks and loss of pressure.
Fitting Length: The length of the fitting is important, especially for compression and crimp fittings. Longer fittings may offer more secure connections, while shorter ones may be better for space-constrained systems.
Select the Correct Fitting Size Based on Hose Diameter
Once you have the correct hose diameter and material, you can match it to the appropriate fitting size. The fitting should have:
An ID that matches or is slightly larger than the hose’s inside diameter for a smooth flow of fluid.
The OD should fit the port or connection point where it will be attached in the system.
For example:
A 1/2-inch hose will typically require a 1/2-inch fitting or appropriate-sized fitting to ensure a tight and secure connection.
For smaller or larger hoses, ensure that the fitting type and size match the hose’s ID and OD.
Conclusion
Optimizing the performance of a hydraulic system begins with the proper selection and matching of hydraulic hoses and fittings. If you are unable to select the right size hose for your existing fittings, contact Topa and we have experts to help you make the best choice!
FAQ
How do I determine the right hose size for my hydraulic system?
Start by identifying the required flow rate and system pressure. Then, choose a hose diameter that can accommodate the flow without causing excessive pressure loss.
What happens if I use the wrong hose size?
Using the wrong hose size can lead to reduced flow, increased pressure drops, system inefficiency, and even hose failure, which may result in leaks or costly repairs.
Can I use any fitting with any hose?
No. Fittings must be matched to the hose diameter, thread type, and connection style to ensure a secure and leak-free connection.
How do I match hose fittings to the hose?
Select fittings that match the hose’s inside diameter (ID), outside diameter (OD), and the thread type (e.g., BSP, NPT, JIC) to prevent leaks and ensure proper fluid flow.
What factors should I consider when choosing a hose material?
Consider the fluid type, temperature range, and environmental conditions (e.g., UV exposure, abrasion) to ensure the hose material is compatible and durable for your application.
Why is it important to match the hose to the fittings?
Proper hose and fitting matching ensures efficient fluid flow, minimizes pressure drops, prevents leaks, and increases system safety and longevity.