The question of whether brass fittings are safe for drinking water has been a topic of increasing debate in the plumbing industry. While brass is a popular choice for plumbing due to its durability and corrosion resistance, concerns over its potential impact on water quality have prompted both homeowners and professionals to question its safety for potable water systems. Is brass safe for drinking water, or are hidden risks lurking in your plumbing system?
Can You Use Brass Fittings for Drinking Water? The Big Question
When it comes to choosing materials for plumbing systems, especially those that transport drinking water, brass fittings are often considered a go-to option due to their durability, versatility, and resistance to corrosion. However, the question remains: Can you safely use brass fittings for drinking water? This section explores the role of brass fittings in potable water systems, the regulatory framework that governs their use, and the risks that may come with their use in drinking water.
Overview of Brass Fittings in Drinking Water Systems
Brass fittings are commonly used in plumbing systems because of their strength and resistance to corrosion. Made primarily from copper and zinc, brass fittings are durable and can withstand high-pressure environments. These fittings are often used in various parts of the plumbing system, including pipe connections, valves, and faucets. Despite their popularity, the use of brass fittings in potable water systems has raised concerns due to the potential for lead contamination, which can affect water quality.
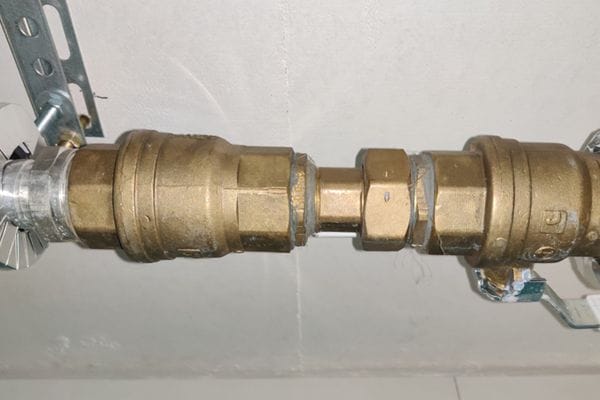
Regulatory Guidelines Around Brass Fittings for Potable Water
Some strict regulations and standards govern the materials used in potable water systems, particularly regarding lead content. The Safe Drinking Water Act (SDWA) in the United States sets limits on the amount of lead that can be present in plumbing materials that come into contact with drinking water. Additionally, brass fittings must meet NSF/ANSI 61 certification to be considered safe for drinking water. This certification ensures that materials used in plumbing systems will not leach harmful substances, including lead, into the water. However, not all brass fittings are certified lead-free, and some may still contain trace amounts of lead, posing a potential risk to health.
Understanding the Risks Associated with Using Brass for Drinking Water
The primary concern when using brass fittings in drinking water systems is the presence of lead. Although lead-free brass is now available, many older brass fittings or those not specifically marked as “lead-free” can still contain lead. Over time, lead can leach into the water, especially if the fittings corrode or degrade. This leaching can have serious health implications, particularly for children, pregnant women, and those with weakened immune systems. Additionally, corrosion of brass fittings can result in the breakdown of the material, further exacerbating the risk of contaminants entering the water supply. Understanding these risks is crucial when deciding whether to use brass fittings in drinking water systems.
Lead Content in Brass: A Hidden Danger for Drinking Water
Brass fittings are a popular choice for plumbing systems, but the presence of lead in many brass alloys has raised significant concerns regarding their use in drinking water.
How Brass Fittings Can Contain Lead
Brass is an alloy composed of copper and zinc, but lead is often added to improve the machinability and durability of the material. This is especially true for older or low-cost brass fittings. While lead is not inherently a part of the brass alloy, its inclusion in many brass fittings is what makes it a concern for drinking water systems. Depending on the ratio of copper, zinc, and lead, the lead content can vary significantly. The lead in brass fittings can leach into the water if it comes into contact with moisture over time, especially in systems that experience corrosion or wear and tear.
The Impact of Lead on Water Quality and Health
Lead is a toxic metal, and even small amounts can have severe health consequences, particularly when it leaches into drinking water. Exposure to lead can result in a range of health issues, including neurological damage, kidney dysfunction, and high blood pressure. For vulnerable populations like young children and pregnant women, the effects are even more pronounced, leading to developmental delays, learning difficulties, and increased risk of miscarriage. Long-term exposure to lead-contaminated drinking water can cause irreversible damage, making it critical to limit exposure at all costs.
Lead can also compromise the overall water quality by introducing toxic elements into the water supply. In addition to health risks, lead contamination can result in unpleasant tastes or odors, making the water undrinkable and unpleasant for daily use. This underscores the importance of ensuring that the materials used in plumbing systems meet safety standards to avoid contamination.
Legal Limits and Regulations on Lead Content in Plumbing Materials
To protect public health, governments around the world have introduced stringent regulations regarding lead content in plumbing materials. In the United States, the Safe Drinking Water Act (SDWA) enforces a maximum allowable lead content in plumbing components, including brass fittings. According to the law, any fitting or fixture that comes into contact with drinking water must contain no more than 0.25% lead by weight to be considered compliant. Additionally, the NSF/ANSI 61 certification ensures that products used in potable water systems meet the necessary standards for safety, including limitations on lead leaching.
Lead-Free Brass: Is It the Safe Alternative?
As concerns over lead contamination in drinking water systems grow, many homeowners and professionals are turning to lead-free brass as a safer alternative for plumbing fittings. But what does “lead-free” really mean, and how does it compare to traditional brass fittings? This section explores what makes brass fittings “lead-free,” how they differ from conventional brass, and the role of NSF certification in ensuring safety.
What Makes Brass “Lead-Free”
“Lead-free” brass refers to brass alloys that contain little to no lead. According to the Safe Drinking Water Act (SDWA), a fitting or fixture is considered lead-free if it contains less than 0.25% lead by weight. This is a significant reduction compared to traditional brass, which often contains a higher percentage of lead to improve the machinability and durability of the material. Lead-free brass typically substitutes other metals, such as tin, phosphorus, or silicon, in place of lead to maintain the strength and corrosion resistance of the fitting while eliminating the toxic effects of lead. These alternative alloys offer similar benefits to traditional brass, but without the health risks associated with lead leaching into drinking water.
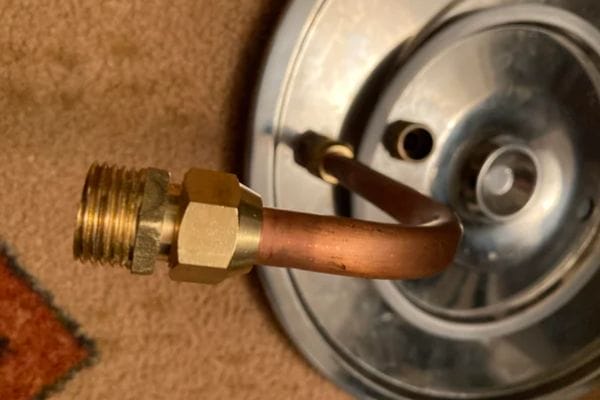
How Lead-Free Brass Compares to Traditional Brass Fittings
Lead-free brass offers several advantages over traditional brass fittings. The most important benefit is the elimination of lead contamination. In systems where lead-free brass is used, the risk of toxic lead leaching into drinking water is drastically reduced, making it a safer choice for potable water systems. In addition to being safer, lead-free brass is also highly resistant to corrosion and wear, maintaining the durability and longevity of the plumbing system.
However, while lead-free brass is a safer alternative, it can sometimes come at a higher cost compared to traditional brass due to the use of alternative metals. Additionally, machinability—the ease with which the metal can be shaped and installed—may vary between lead-free and traditional brass. Some plumbers report that lead-free brass is slightly more difficult to work with, but this is generally considered a minor issue compared to the health benefits.
NSF Certification and Its Role in Ensuring Safety
One of the most reliable ways to ensure that brass fittings are indeed safe for drinking water is to look for NSF/ANSI 61 certification. This certification indicates that the product has been tested and meets safety standards for drinking water quality, including limits on lead content and other harmful substances. Products with NSF certification are rigorously tested to ensure that they will not leach dangerous levels of lead or other contaminants into the water supply. When choosing lead-free brass fittings, make sure they carry the NSF logo or the NSF/ANSI 61 label to guarantee they meet the necessary safety standards for potable water use.
How to Identify Lead-Free Brass Fittings in the Market
With the increasing demand for safer plumbing materials, it’s important to know how to identify lead-free brass fittings when purchasing plumbing supplies. Here are a few tips for recognizing lead-free brass in the market:
Look for Certification Labels: Always check the packaging or product labeling for NSF/ANSI 61 certification, which indicates the product is safe for potable water systems.
Check the Alloy Composition: Many manufacturers now indicate the specific alloy composition of their brass fittings. Lead-free brass will typically list lead content as less than 0.25%.
Verify Manufacturer Claims: Ensure that the manufacturer explicitly states that the fittings are lead-free and suitable for drinking water. Do not rely solely on the word “brass”—confirm the product’s compliance with lead-free standards.
Is Brass Fittings Safe for Drinking Water? What the Experts Say
The safety of brass fittings for drinking water systems is a topic that has garnered attention from both plumbing experts and health organizations. With concerns about lead contamination and corrosion, many professionals offer insight into the risks and benefits of using brass in potable water systems.
Insights from Plumbing Experts and Health Organizations
Plumbing professionals and health experts agree that brass fittings, particularly older or improperly labeled ones, can pose significant risks to drinking water quality. Experts from organizations like the American Water Works Association (AWWA) and the Plumbing-Heating-Cooling Contractors Association (PHCC) have emphasized the importance of using lead-free materials in potable water systems. According to many plumbing experts, while brass has been a reliable material for years, its safety for drinking water has become increasingly questionable due to lead content and its susceptibility to corrosion over time.
Health organizations, including the Centers for Disease Control and Prevention (CDC) and the World Health Organization (WHO), have raised alarms about the dangers of lead exposure from plumbing systems, particularly in children and pregnant women. These organizations recommend that all plumbing materials used in drinking water systems should be thoroughly tested for safety and compliance with national standards to prevent contamination. They support the transition to lead-free brass and other safer materials as a means of reducing health risks associated with metal contaminants.
Government and Health Agency Guidelines on Brass Fittings in Potable Water Systems
Government regulations play a crucial role in determining the safety of materials used in drinking water systems. In the United States, the Safe Drinking Water Act (SDWA) mandates that plumbing materials used in potable water systems must contain no more than 0.25% lead by weight to be considered lead-free. The NSF/ANSI 61 certification ensures that products used in water systems will not leach harmful substances, including lead, into drinking water. This certification is particularly important for brass fittings, as many traditional brass alloys exceed the allowable lead limits and are therefore unsuitable for potable water systems.
Furthermore, the EPA sets standards for the maximum allowable concentrations of various metals in drinking water, including lead, copper, and zinc. These standards are designed to protect consumers from the health risks posed by contaminants that can leach from plumbing materials. Brass fittings that do not meet these standards can contribute to water contamination, which may have serious health consequences.
How to Avoid Common Pitfalls When Using Brass Fittings for Drinking Water
Choosing the right materials for drinking water systems is essential for ensuring the safety and quality of the water supply. While brass fittings can be durable and reliable, it’s crucial to avoid common pitfalls that can compromise the integrity of your plumbing and potentially expose you to harmful contaminants.
Key Mistakes to Avoid in Choosing Fittings for Potable Water Systems
Selecting the wrong brass fittings or failing to verify their safety can lead to significant risks, including lead contamination and plumbing failures. Here are some common mistakes to avoid when choosing brass fittings for drinking water systems:
Not Checking for Lead-Free Certification: One of the biggest mistakes is failing to confirm that the brass fittings are lead-free or compliant with NSF/ANSI 61 standards. Always look for the NSF certification label, which guarantees that the fittings meet the safety criteria for potable water use. Brass fittings without this certification may still contain lead, which can leach into the water supply.
Choosing Old or Non-Compliant Brass Fittings: Using outdated or non-compliant brass fittings can lead to higher lead content and increased corrosion risks. It’s important to replace old brass fittings with newer, certified lead-free options to minimize health risks. Even if the fitting looks functional, it may still pose hidden dangers due to the wear and tear from years of exposure to water.
Ignoring Manufacturer Specifications: Not all brass fittings are created equal, even if they appear similar. Always read the manufacturer’s specifications to ensure the material composition meets local plumbing codes and safety standards. Some brass fittings may be suitable for gas or other non-potable uses but are not safe for drinking water.
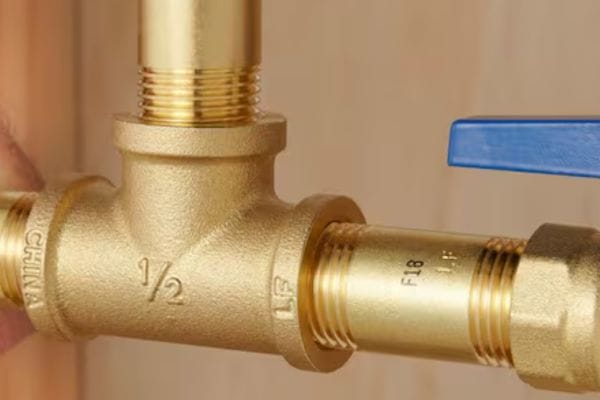
How to Test for Lead Content in Your Plumbing Materials
If you are unsure about the lead content in your existing brass fittings, testing is a critical step to ensure the safety of your drinking water. Here are a few ways to check for lead in your plumbing materials:
Lead Test Kits: You can purchase lead test kits from hardware stores or online, which are designed to detect the presence of lead in water or on plumbing surfaces. These kits are easy to use and provide quick results, helping you identify if lead is leaching into your drinking water.
Professional Water Testing: For a more thorough analysis, you can hire a professional plumber or water quality testing service to conduct a comprehensive water test. This will not only identify lead contamination but also measure other harmful elements, such as copper or zinc, which could be leaching from the brass fittings.
Inspecting the Fittings: If you’re dealing with older brass fittings, it’s a good idea to have them inspected by a licensed plumber. Over time, the internal surfaces of brass fittings can become corroded, which may increase the likelihood of lead leaching. A plumber can recommend whether the fittings need to be replaced based on their condition.
Conclusion
While brass fittings have historically been the preferred choice, the risks associated with lead contamination and corrosion make it imperative to carefully evaluate their suitability for potable water systems. By choosing lead-free brass fittings or alternative materials that meet the latest NSF standards, you can protect your home’s water quality and the health of its occupants. If you need quality lead-free brass, contact Topa and we can provide it!
FAQ
Are brass fittings safe for drinking water?
Brass fittings can be safe for drinking water if they are lead-free and meet NSF/ANSI 61 standards.
What is lead-free brass?
Lead-free brass refers to brass alloys that contain less than 0.25% lead by weight. These fittings are specifically designed to meet safety standards for potable water and reduce the risk of lead contamination.
How can I tell if my brass fittings are safe for drinking water?
To ensure that your brass fittings are safe, look for NSF certification or the label “lead-free”.
What are the risks of using brass fittings with lead content?
Brass fittings with lead content can leach harmful amounts of lead into drinking water, which is a neurotoxin.
How do I prevent lead contamination from brass fittings?
To prevent lead contamination, use lead-free brass fittings and regularly maintain your plumbing system.
Are there alternatives to brass fittings for drinking water?
Yes, copper and plastic pipes (like PEX) are common alternatives to brass fittings.