In hydraulic and industrial applications, hose assemblies are often subjected to extreme conditions—high-pressure systems, corrosive fluids, and intense vibrations—making the role of hose ferrules all the more important. These small but powerful components are designed to provide a tight, durable seal that ensures hoses stay securely attached to fittings, preventing leakage and potential system breakdowns.
What Is a Hose Ferrule?
A hose ferrule is a metal or plastic component that is used to secure the end of a hose to a fitting in order to create a tight, leak-proof seal. Ferrules are typically placed over the hose and then crimped or compressed to tightly hold the hose against the fitting, ensuring that the two components are firmly connected. They are essential in creating a reliable and durable connection in hose assemblies, especially in systems where high pressure, vibration, or extreme conditions are present.
Basic Function
The primary function of a hose ferrule is to secure the hose to the fitting in a way that prevents leakage and ensures the integrity of the connection. The ferrule is slid over the hose, usually after the hose has been cut to the required length and the fitting is placed at the other end. Once positioned, the ferrule is crimped or compressed using specialized tools, such as a crimping machine, to tightly grip the hose and the fitting. This process ensures that the hose is securely fastened, preventing any fluid or gas from leaking out of the connection.
Ferrules work by applying equal pressure around the hose, allowing the fitting to be securely held in place. This is particularly important in high-pressure systems, where leaks can lead to system failure, costly downtime, or even dangerous accidents. The hose ferrule creates a seal that withstands the internal pressure within the hose, effectively preventing leaks at the connection point. Depending on the application, ferrules may be made from materials like stainless steel, brass, or aluminum, which provide strength, corrosion resistance, and durability.
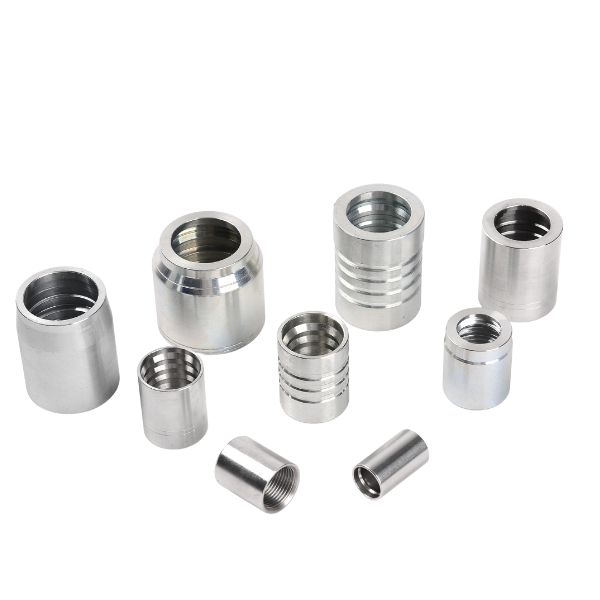
Why They Are Important
Hose ferrules are critical to the performance, durability, and safety of hose assemblies. Without a properly installed ferrule, hoses may become loose or detached from their fittings, leading to potential leaks or system malfunctions. In industrial settings, such as hydraulic, automotive, or chemical systems, even a small leak can cause significant damage, harm workers, or lead to costly repairs. The ferrule ensures that the hose and fitting remain tightly connected, preventing these risks.
Additionally, hose ferrules contribute to the efficiency of fluid and gas transfer within the hose assembly. A secure connection ensures that fluid flows freely without resistance or loss, improving the overall efficiency of the system. Moreover, the longevity of the hose assembly is greatly extended when ferrules are properly selected and maintained. In short, hose ferrules are integral to maintaining a secure, reliable, and efficient hose system, supporting safety, operational effectiveness, and cost savings across various industries.
Components of Hose Assemblies and the Role of Ferrules
Hose assemblies are crucial in many industrial systems where the transport of fluids, gases, or hydraulic pressure is needed. These assemblies are made up of several key components, each playing a specific role in ensuring the hose system functions safely and efficiently. The main components of a typical hose assembly include the hose, the fitting, the ferrule, and the coupling. Together, these components work in harmony to create a reliable, leak-proof connection.
Overview of Hose Assemblies
Hose: The hose is the flexible conduit that carries fluids or gases from one point to another in a system. It is typically made from materials like rubber, thermoplastic, or metal braided layers to provide flexibility and resistance to abrasion, pressure, and temperature. The hose’s inner lining is designed to handle specific types of fluids or gases, while the outer layers provide reinforcement and protection.
Fitting: A fitting is a mechanical component that connects the hose to another system component, such as a valve, pump, or machinery. Fittings are typically made of materials like stainless steel, brass, or aluminum and come in various shapes, sizes, and configurations, such as elbows, tees, and straight connectors. The fitting ensures that the hose securely connects to the system and provides a leak-tight seal.
Ferrule: A ferrule is a small yet vital component used to secure the hose to the fitting. It is usually made from metal, such as stainless steel, or other materials like brass or plastic, and is placed over the hose where it meets the fitting. The ferrule is then crimped or compressed to create a tight seal that prevents fluid or gas leakage. The ferrule also helps to reinforce the hose and prevent the fitting from being damaged during operation.
Coupling: A coupling is used in some hose assemblies to provide a quick disconnect or to facilitate easier connection and disconnection between the hose and the equipment. Couplings often incorporate valves to prevent leakage when disconnected.
Ferrule’s Function in Assemblies
The ferrule’s primary function is to securely attach the hose to the fitting, ensuring that the connection is tight and leak-proof. When installed, the ferrule is placed around the hose and fitting and is then crimped or compressed using a crimping tool. This process applies pressure, creating a secure bond between the hose and the fitting, which prevents the hose from slipping off or leaking.
Ferrules are critical in maintaining the integrity of hose assemblies, especially in high-pressure systems, where even the slightest gap can lead to dangerous leaks. By tightly compressing the hose against the fitting, the ferrule ensures that the connection remains secure under a wide range of conditions, including fluctuating pressures, vibrations, and temperature changes. Without the ferrule, the hose could easily detach or loosen, leading to potential failure in the system.
Interaction with Other Components
The ferrule’s role is intertwined with that of the hose and fitting, as it directly interacts with both to ensure a leak-proof, high-performance hose assembly.
Hose and Ferrule Interaction: The hose itself is designed to handle specific pressures, temperatures, and types of fluid or gas. The ferrule, when properly installed, compresses the hose in a way that maximizes the contact area between the hose and fitting. This increases the strength of the connection and helps distribute pressure evenly, reducing the chances of hose failure. The ferrule also reinforces the hose by preventing it from deforming under pressure or exposure to environmental stressors.
Fitting and Ferrule Interaction: The fitting is responsible for connecting the hose assembly to the rest of the system. It must be compatible with the ferrule to ensure a proper fit. The ferrule works with the fitting to create a mechanical seal that can withstand high pressures, minimizing the risk of leaks. In addition, the ferrule provides a cushioning effect that prevents damage to the fitting due to excessive pressure or vibration. The correct choice of ferrule material is crucial, as it must be compatible with the material of the fitting to avoid issues like corrosion or wear.
Types of Hose Ferrules
Crimp Ferrules
Crimp ferrules are the most commonly used type of ferrule in industrial hose assemblies. These ferrules are typically made of metal (such as stainless steel or brass) and are designed to be crimped tightly around the hose and fitting using a crimping tool.
How They Work: When a crimp ferrule is placed over the hose, a crimping tool is used to compress the ferrule, forcing it to tightly grip both the hose and the fitting. This creates a secure, leak-proof connection that is resistant to pressure and external stress. Crimp ferrules are often used in high-pressure hydraulic systems and other applications where a strong, permanent connection is required.
Advantages:
Strong and Durable: Crimp ferrules provide a high level of security, even in systems that experience high pressure, vibration, or harsh operating conditions.
Leak Prevention: The tight seal created by crimping ensures that no fluids or gases escape from the connection.
Permanent Connection: Once crimped, the ferrule forms a permanent, tamper-resistant bond, ensuring the integrity of the hose assembly.
Crimp ferrules are ideal for applications that require high pressure resistance, such as in hydraulic systems, fuel systems, and industrial machinery.
Reusable Ferrules
Reusable ferrules are designed for systems where the hose connections need to be disassembled and reassembled without compromising the connection’s integrity. Unlike crimp ferrules, reusable ferrules can be removed, inspected, and reattached multiple times, making them ideal for applications where hoses need to be replaced or serviced regularly.
How They Work: Reusable ferrules are typically designed with threads, a clamping mechanism, or a compression ring that can be easily tightened or loosened without requiring specialized crimping tools. After the ferrule is loosened, the hose can be removed, inspected, and replaced if needed, then the ferrule can be reattached to the fitting.
Advantages:
Cost-Effective: Since they can be reused, these ferrules are more economical in systems where hoses require frequent changes.
Ease of Maintenance: Reusable ferrules allow for easier maintenance and servicing of hose assemblies without the need to replace the ferrule each time the hose is changed.
Flexibility: They can be disassembled for cleaning, inspection, or part replacement, reducing downtime and increasing operational efficiency.
Reusable ferrules are commonly used in industries like automotive, food and beverage, or pharmaceutical applications where hoses are regularly replaced or cleaned.
Push-on Ferrules
Push-on ferrules are a more straightforward type of ferrule. They are typically used in low-pressure applications or where the connection does not need to withstand extreme pressure or stress. Push-on ferrules are made to fit over the hose and fitting with minimal effort, requiring no crimping or additional tools.
How They Work: Push-on ferrules are designed with a flexible, tight-fitting mechanism that “snaps” or slides over the hose and fitting. Once in place, they create a secure enough connection to hold the hose in place under moderate conditions. However, these ferrules are generally not suitable for high-pressure systems.
Advantages:
Ease of Installation: Push-on ferrules are easy to install and remove, making them ideal for quick hose changes in low-pressure applications.
Cost-Effective: Since they do not require crimping tools, they are more affordable than other types of ferrules.
Light-Duty Use: These ferrules are best for non-critical applications where the pressure and fluid types do not require the additional durability provided by crimp or reusable ferrules.
Push-on ferrules are commonly used in applications like air systems, low-pressure water hoses, or applications that do not require the same level of performance as hydraulic or high-pressure systems.
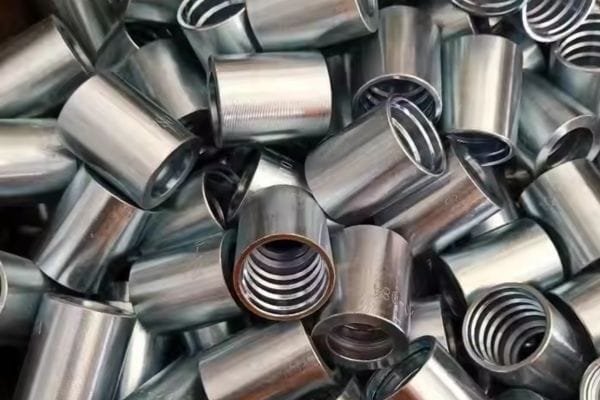
Material Variations
The material used to manufacture hose ferrules significantly impacts their performance and suitability for specific environments. Below are some of the most common materials used for hose ferrules and their advantages:
Stainless Steel: Stainless steel ferrules are highly resistant to corrosion, making them ideal for applications in harsh or corrosive environments, such as chemical processing, food and beverage, or marine applications. Stainless steel ferrules are durable, strong, and capable of withstanding high-pressure conditions, making them a popular choice in hydraulic systems.
Brass: Brass ferrules are also corrosion-resistant and are often used in lower-pressure applications, such as in plumbing systems, fuel lines, or air conditioning systems. Brass is more affordable than stainless steel, but it may not perform as well in high-pressure systems or aggressive chemical environments.
Aluminum: Aluminum ferrules are lightweight, corrosion-resistant, and relatively inexpensive. They are commonly used in industries like automotive or low-pressure hydraulic systems. However, they may not offer the same strength or durability as stainless steel, especially under extreme pressure or temperature conditions.
Plastic: Plastic ferrules are typically used in light-duty applications where flexibility, ease of installation, and cost are primary concerns. They are suitable for low-pressure systems, such as water hoses or garden hoses, but may not withstand harsh chemical exposure or high-pressure environments.
Choosing the Right Type of Ferrule
Selecting the right hose ferrule for a hose assembly depends on several factors, including the application’s specific needs:
Pressure Requirements: For high-pressure applications (e.g., hydraulic systems), crimp ferrules made from stainless steel or brass are usually the best choice due to their strength and durability. For low-pressure applications, push-on ferrules or reusable ferrules can be sufficient.
Fluid Type: Different fluids can affect the materials of the ferrule. For instance, if the hose is carrying chemicals or high-temperature fluids, a stainless steel ferrule is recommended for its corrosion resistance.
Temperature Conditions: In high-temperature applications, materials like stainless steel or brass perform better. Plastic ferrules are not suitable for high-temperature conditions.
Reusability: If frequent maintenance or hose replacement is required, reusable ferrules are an excellent choice, as they allow for easy disassembly and reassembly.
Conclusion
We encourage all industry professionals to carefully evaluate the needs of their hose assemblies and choose the right ferrules accordingly. By understanding the different ferrule types and materials, and selecting the most suitable option for each application, you ensure that your systems operate efficiently, safely, and with minimal risk of failure.
Take action today—choose the right ferrule for secure and reliable hose assemblies in your systems!
FAQ
What is a hose ferrule?
A hose ferrule is a metal or plastic component used to secure the hose to the fitting, ensuring a leak-proof connection in hose assemblies.
What types of hose ferrules are available?
The main types include crimp ferrules (permanent connection), reusable ferrules (allow disassembly and reassembly), and push-on ferrules (easy installation for low-pressure systems).
Why is it important to use the correct hose ferrule?
Using the right ferrule ensures the hose assembly is secure, leak-proof, and able to withstand pressure, temperature, and fluid conditions, enhancing safety and system performance.
Can I reuse a hose ferrule?
Some ferrules, like reusable ferrules, are designed for disassembly and reassembly, while others, like crimp ferrules, are permanent once installed.
What materials are hose ferrules made from?
Hose ferrules are typically made from materials such as stainless steel, brass, aluminum, or plastic, chosen based on factors like corrosion resistance and strength.
How do I choose the right ferrule for my hose assembly?
Consider factors like the system’s pressure, fluid type, temperature, and whether the hose needs to be serviced or replaced frequently to determine the appropriate ferrule type.