Non-crimp hose fittings, also known as no-crimp fittings, are a crucial component in hydraulic systems, particularly for low-pressure applications. Unlike traditional crimp fittings, which require specialized tools for assembly, no-crimp fittings offer a straightforward push-on mechanism that simplifies the installation process. This ease of use makes them an attractive option for a variety of industries, including automotive, agriculture, and manufacturing.
What Are No Crimp Hose Fittings?
Definition and Basic Features
No-crimp hose fittings are designed for easy assembly without the need for crimping tools. These fittings utilize a simple push-on mechanism that allows the user to secure the fitting onto the hose with minimal effort. The design typically includes barbs or ridges that grip the inside of the hose, ensuring a tight seal without additional hardware.
Comparison with Crimp Fittings: Pros and Cons
When comparing no-crimp fittings to crimp fittings, several advantages and disadvantages emerge:
Pros of No-Crimp Fittings:
Ease of Installation: No specialized tools are required, making them user-friendly for quick assemblies.
Cost-Effective: Lower initial investment due to the lack of crimping equipment and lower labor costs.
Reusability: These fittings can be disassembled and reused, providing flexibility for adjustments or repairs.
Cons of No-Crimp Fittings:
Pressure Limitations: Generally suited for low-pressure applications, making them less ideal for high-pressure systems.
Potential for Leaks: If not properly installed, there may be a higher risk of leaks compared to crimp fittings, which offer a more permanent connection.
Common Applications in Low-Pressure Systems
No-crimp fittings are widely used in various low-pressure hydraulic applications. They are particularly suitable for:
Lubrication Lines: Facilitating the transfer of oils and lubricants in machinery.
Air Hoses: Connecting air supply lines in pneumatic systems, providing flexibility and ease of replacement.
Materials Used
No-crimp fittings are available in several materials, each offering distinct benefits:
Brass: Known for its corrosion resistance and durability, brass fittings are ideal for applications involving oils and low-pressure fluids.
Steel: Often used for its strength and cost-effectiveness, steel fittings are suitable for various industrial applications.
Stainless Steel: Provides excellent corrosion resistance, making it perfect for harsh environments or where sanitation is critical.
Understanding Hose and Fitting Compatibility
To ensure optimal performance and safety in hydraulic systems, understanding hose and fitting compatibility is essential, particularly when using no-crimp fittings. Proper sizing, material selection, and adherence to pressure ratings are key considerations for successful implementation.
Explanation of Hose Sizing for No-Crimp Fittings
No-crimp hose fittings are typically sized based on the inner diameter (ID) of the hose they are intended to fit. The sizing is generally expressed in fractions of an inch, such as 1/4″, 3/8″, or 1/2″. It is crucial to select a fitting size that matches the hose’s ID precisely to ensure a secure connection. The fitting’s barbs must align correctly with the hose’s inner wall to create a tight seal, preventing leaks and maintaining system efficiency.
When selecting a hose, it’s important to verify that it meets the manufacturer’s specifications for the no-crimp fitting you plan to use. Hose types compatible with no-crimp fittings include NC hoses designed for low-pressure applications, ensuring the fitting can securely grip the hose without additional clamping.
Selecting the Right Fitting Material for Specific Applications
Choosing the correct material for no-crimp fittings is crucial for both performance and longevity. Common materials and their typical applications include:
Brass: Often chosen for its excellent corrosion resistance, brass fittings are suitable for fluid transfer applications involving water, oils, or low-pressure hydraulic fluids. Brass is also ideal for use in environments where exposure to corrosive agents is possible but not extreme.
Steel: Steel fittings are strong and cost-effective, making them appropriate for general-purpose industrial applications. However, they may require protective coatings if used in corrosive environments.
Stainless Steel: For highly corrosive environments or where hygiene is critical (e.g., food processing or chemical industries), stainless steel fittings are the best option. They offer superior resistance to corrosion and maintain integrity under varying temperatures.
By selecting a fitting material compatible with the working fluid and environment, you can prevent premature wear and ensure the longevity of the hydraulic system.
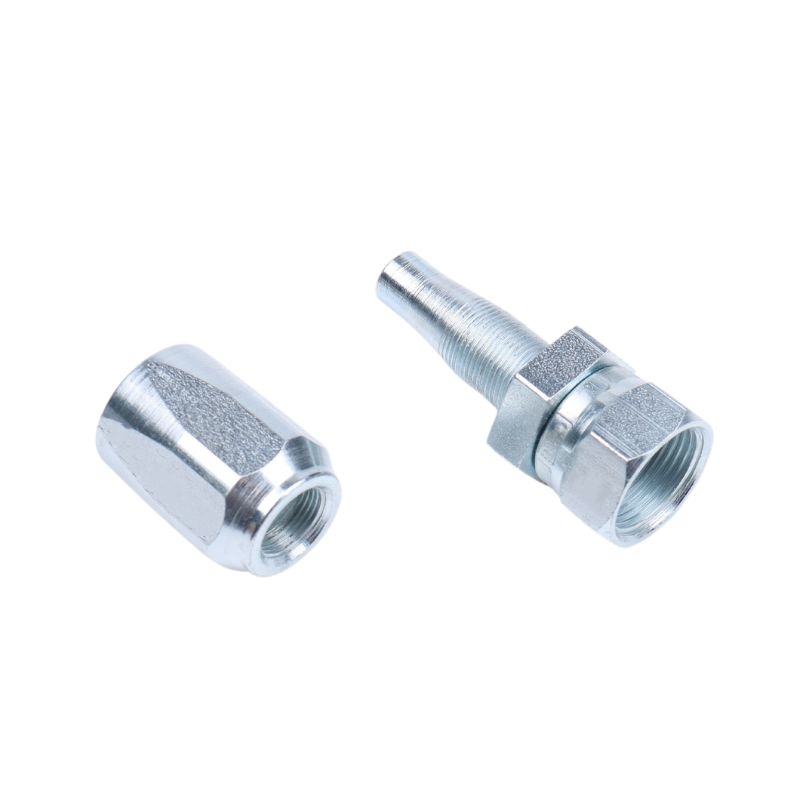
Pressure Rating Guidelines: 250 psi and 300 psi Applications
No-crimp fittings are typically rated for low-pressure applications. The most common pressure ratings for these fittings are 250 psi and 300 psi. Here’s a breakdown of how these ratings apply:
250 psi Rating: Suitable for standard air and lubrication lines where operational pressures remain within this limit. This rating provides enough flexibility for typical shop or industrial use without compromising safety.
300 psi Rating: Often used in systems that may experience slightly higher pressure variations or when a greater safety margin is needed. It is appropriate for more demanding low-pressure applications where slight fluctuations above 250 psi are anticipated.
When selecting fittings and hoses, always verify that both components share the same or compatible pressure ratings to maintain system safety and performance standards. It’s also essential to consider the maximum pressure rating of the entire assembly rather than just individual components.
Step-by-Step Assembly Guide for No-Crimp Fittings
Assembling no-crimp fittings is a straightforward process, but it requires careful attention to detail to ensure a secure and leak-free connection.
Preparation
Tools Required:
Cutting Tools: A sharp utility knife or hose cutter is essential for making clean, straight cuts on the hose.
Light Oil: This will be used for lubrication to facilitate the insertion of the fitting into the hose.
Measuring Tape: Accurate measurement is crucial for cutting the hose to the right length and ensuring proper fitting size.
Measuring and Cutting the Hose Accurately:
Measure the required length of the hose based on your application needs. Consider any additional length needed for the fittings themselves.
Mark the hose clearly where you plan to cut, ensuring the measurement is precise.
Use your cutting tool to make a straight, square cut at the marked point. A clean cut will help the fitting seat properly and prevent leaks.
Assembly Process
Lubrication Guidelines for Smooth Fitting Insertion:
Apply a small amount of light oil to the inside of the hose and the outside of the fitting. This lubrication reduces friction and makes it easier to insert the fitting without damaging the hose.
Ensure that you do not use heavy oils or greases, as they can affect the fitting’s sealing capabilities.
Proper Technique to Push Fittings into Hoses and Secure Them:
Align the fitting with the hose’s opening, ensuring that it is positioned straight.
Gently push the fitting into the hose until the first barb of the fitting is inside the hose. You may need to twist it slightly to help it slide in.
Once the fitting is partially inserted, grip the hose approximately one inch from the end and apply steady pressure to push the fitting further in until the hose covers the yellow plastic cap at the fitting’s end.
Ensure the fitting is seated fully and securely, as this will help maintain a tight seal.
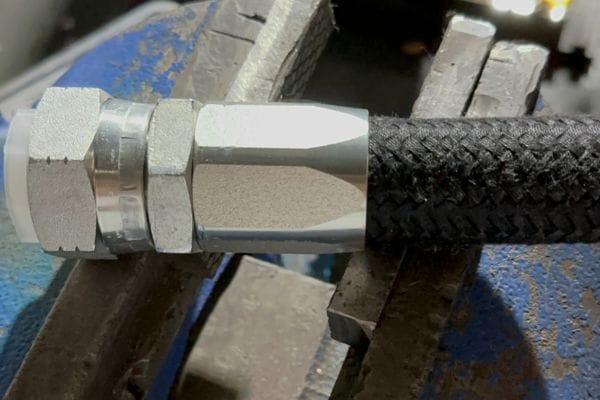
Safety Tips
Avoiding Heavy Oils/Grease and Using Only Recommended Lubricants:
Always use light oils or soapy water for lubrication. Heavy oils or greases can compromise the integrity of the fitting and lead to leaks.
Follow the manufacturer’s recommendations for lubricants to ensure compatibility and performance.
Ensuring Proper Fit and Seal Integrity:
After assembly, visually inspect the connection to ensure the fitting is fully seated and that there are no gaps or misalignments.
Perform a gentle tug on the hose to verify that it is securely attached to the fitting. If it detaches easily, it may not be properly seated, and reassembly may be necessary.
Before putting the assembly into service, conduct a pressure test (if applicable) to confirm that there are no leaks under operational conditions.
Troubleshooting Common Issues
Even with careful assembly, issues can arise when using no-crimp fittings. Here’s a guide to troubleshooting common problems, including leak prevention, hose detachment, and maintenance advice.
Leak Prevention
Causes of Leaks and How to Address Them:
Misalignment: If the fitting is not aligned properly with the hose during insertion, it can create gaps that lead to leaks. To prevent this, always ensure the fitting is straight and properly seated before pushing it into the hose.
Improper Lubrication: Insufficient lubrication can cause the fitting to bind, making it difficult to insert fully. Always use light oil or soapy water, as heavy oils can damage the seal. If leaks occur, check the fitting’s insertion depth and reapply lubricant as necessary.
Worn or Damaged Hose: Over time, hoses can wear out or develop cracks. Regularly inspect hoses for signs of wear and replace them if necessary. A damaged hose will not create a proper seal with the fitting.
Hose Detachment
Tips for Ensuring Secure Connections:
Proper Insertion Depth: Ensure the fitting is pushed into the hose until it reaches the specified depth indicated by the manufacturer. A fully inserted fitting reduces the risk of detachment.
Correct Fitting Size: Always match the hose and fitting sizes correctly. Using an incorrectly sized fitting can compromise the connection and lead to detachment.
Identifying Signs of Improper Assembly:
Look for gaps between the fitting and the hose. If visible, the fitting may not be seated properly.
Check for any movement or looseness at the connection point; if the fitting can be easily pulled out, it requires reassembly.
Observe for any fluid leaking from the connection, indicating a need for immediate inspection and possible reinstallation.
Maintenance Advice
Routine Checks and Adjustments to Maintain Sealing Effectiveness:
Regular Inspections: Periodically check all connections for signs of leaks, wear, or damage. Visual inspections can help catch issues before they escalate.
Tightening Connections: If you notice any loosening of fittings, recheck their assembly. While no-crimp fittings do not require crimping, they should still be snug.
Environmental Considerations: If hoses and fittings are exposed to harsh chemicals or extreme temperatures, ensure they are compatible with such conditions. Regularly replace any components that show signs of degradation.
Documenting Maintenance: Keep a log of inspections and maintenance performed. This helps in tracking performance and identifying recurring issues that may need further attention.
Comparing No-Crimp Fittings to Crimp Fittings
When choosing between no-crimp and crimp fittings, it’s essential to understand their distinct features, applications, and requirements. This section provides an overview of crimp fittings, compares the two types directly, and offers guidance on selecting the appropriate option based on system needs.
Overview of Crimp Fittings and Their Use in High-Pressure Systems
Crimp fittings are a type of hydraulic fitting that requires crimping or compressing the fitting onto the hose using specialized equipment. This method provides a robust and secure connection, making crimp fittings ideal for high-pressure hydraulic systems, where durability and leak-proof performance are critical. They are commonly used in industrial applications, heavy machinery, and high-pressure fluid transfer systems such as those found in construction or agriculture.
Applications: Crimp fittings are primarily used where system pressures exceed the capabilities of no-crimp fittings, providing a higher level of safety and reliability in these demanding environments.
Materials: Crimp fittings are typically made from durable metals like steel or stainless steel to withstand higher operational pressures and environmental stresses.
Direct Comparison Between No-Crimp and Crimp Fittings
a. Installation Process: Tools, Time, and Skill Level Required
No-Crimp Fittings:
Tools: Minimal tools required; typically, a cutting tool and light oil for lubrication.
Time: Installation is quick and straightforward, suitable for users without specialized skills.
Skill Level: Designed for ease of use, making it accessible for quick repairs and low-pressure applications.
Crimp Fittings:
Tools: Requires specialized crimping equipment, such as a hydraulic or manual crimping tool.
Time: Takes longer due to the need for precise crimping and preparation of the hose and fitting.
Skill Level: More technical expertise is needed to ensure proper crimping and secure attachment, as incorrect crimping can lead to leaks or failure under pressure.
b. Pressure Capabilities and Sealing Effectiveness
No-Crimp Fittings:
Pressure Capability: Best suited for low-pressure systems (e.g., 250-300 psi). They rely on the hose’s elasticity and the barb design for sealing.
Sealing Effectiveness: Adequate for low-pressure environments; however, they may not provide the same reliability in high-pressure conditions, where a tighter, more secure seal is necessary.
Crimp Fittings:
Pressure Capability: Suitable for high-pressure systems (e.g., several thousand psi). The crimping process compresses the fitting onto the hose, forming a leak-proof connection capable of withstanding high-pressure and heavy-duty use.
Sealing Effectiveness: Superior sealing performance, as the crimping process ensures a permanent, tight seal that minimizes the risk of leaks even under extreme conditions.
When to Choose Each Type Based on System Requirements
No-Crimp Fittings:
When to Use: Ideal for low-pressure applications where ease of assembly, quick installation, and reusability are priorities. They are suitable for use in shop air lines, lubrication systems, or any scenario where the system’s operational pressure remains below 300 psi.
Advantages: Cost-effective, requiring minimal tools and setup time, making them a convenient solution for users who need to perform frequent hose replacements or repairs.
Crimp Fittings:
When to Use: Recommended for high-pressure systems where reliability and safety are paramount, such as in construction equipment, agricultural machinery, and heavy-duty hydraulic circuits.
Advantages: Provides a secure, leak-proof connection that can withstand high pressure and harsh environmental conditions, ensuring long-term system integrity.
Best Practices for Selecting and Maintaining No-Crimp Fittings
Selecting and maintaining no-crimp fittings properly is essential for ensuring the longevity and performance of hydraulic systems. Here are some best practices to follow.
Criteria for Selecting the Right Fittings
Material:
Choose the right fitting material based on the application. For instance:
Brass is excellent for general lubrication and non-corrosive environments.
Steel is cost-effective and durable but may require protection against corrosion.
Stainless Steel is ideal for harsh environments where corrosion resistance is critical.
Size: Ensure that the fitting size matches the hose’s inner diameter (ID) precisely. Refer to manufacturer specifications to confirm compatibility and ensure a secure fit.
Pressure Rating: Select fittings rated for the specific pressure levels of your application. Ensure that both the fittings and hoses are rated for the same or higher pressures than those expected during operation to prevent leaks or failures.
Guidelines for Regular Maintenance
Routine Inspections: Regularly check fittings and hoses for signs of wear, leaks, or damage. Look for cracks, abrasions, or corrosion that could compromise the seal.
Lubrication Checks: Periodically reapply light oil or the recommended lubricant to ensure ease of assembly and prevent wear. This is especially important if the fittings have been in service for an extended period.
Pressure Testing: If applicable, conduct pressure tests to confirm the integrity of the fittings under operational conditions. Address any leaks immediately to maintain system performance.
Tips for Storing and Handling Hoses and Fittings
Storage Conditions: Store hoses and fittings in a cool, dry place away from direct sunlight and extreme temperatures. UV exposure can deteriorate rubber materials over time.
Avoid Crushing: Ensure that hoses are not bent or crushed during storage. Use appropriate reels or hangers to keep them organized and prevent kinks or twists that could lead to damage.
Handle with Care: When installing or removing fittings, avoid using excessive force that could damage the hose or fitting. Follow proper assembly techniques to ensure a secure connection without causing harm.
Conclusion
To maximize the safety and efficiency of no-crimp fittings, proper assembly, and regular maintenance are crucial. Ensuring that fittings are properly aligned, securely seated, and compatible with the hose type and pressure rating will help prevent leaks and system failures. Routine inspections and adherence to best practices for storage and handling are also essential for extending the lifespan of the fittings and hoses.
FAQ
What are no-crimp hose fittings?
No-crimp hose fittings are connectors that can be easily assembled without the need for crimping tools. They are designed for low-pressure applications, offering quick and straightforward installation.
What materials are used for no-crimp fittings?
Common materials include brass, steel, and stainless steel. The choice of material depends on the application and environmental conditions, such as corrosion resistance.
How do I know the right size fitting for my hose?
Select a fitting that matches the inner diameter (ID) of your hose precisely. Always refer to manufacturer specifications for compatibility.
What pressure ratings are suitable for no-crimp fittings?
No-crimp fittings are typically rated for low-pressure applications, usually up to 300 psi. Ensure both the hose and fitting share the same pressure rating.
How can I prevent leaks in no-crimp fittings?
To prevent leaks, ensure proper alignment during assembly, use the recommended lubricants, and regularly inspect for wear or damage.
What is the best way to maintain no-crimp fittings?
Regularly inspect fittings and hoses for signs of wear, reapply lubricants as needed, and conduct pressure tests to ensure sealing effectiveness. Store fittings in a cool, dry place to avoid damage.