Why Is Your AN Fitting Leaking? Top Reasons and Fixes
Introduction
However, despite their robust design, AN fittings can sometimes develop leaks, leading to potential system failures, increased maintenance costs, and even safety hazards. Understanding why these leaks occur and how to fix them is essential for anyone relying on AN fittings in their operations. This article aims to explore the top reasons behind AN fitting leaks and provide practical, actionable solutions to address and prevent these issues, ensuring the longevity and reliability of your systems.
Common Causes of AN Fitting Leaks
AN fittings are integral to maintaining the integrity and efficiency of hydraulic and fluid systems. However, leaks can occur due to various reasons, each stemming from different aspects of the fitting’s installation, maintenance, and quality. Understanding these common causes can help in diagnosing and resolving issues effectively.
Improper Installation
Improper installation is a primary cause of leaks in AN fittings. If fittings are not installed correctly, they may not create a proper seal, leading to leaks. Common installation mistakes include over-tightening or under-tightening fittings, misalignment of components, and incorrect use of tools.
Over-tightening can deform the fitting or the mating surface, leading to a compromised seal. Under-tightening can result in insufficient compression of the sealing surfaces, allowing fluid to escape. Misalignment between the fitting and the connecting parts can also cause leaks due to uneven pressure distribution.
Tips for proper installation:
Use the right tools: Ensure you are using the appropriate tools for tightening and aligning fittings. A torque wrench is often necessary to achieve the correct tightness.
Follow manufacturer guidelines: Always adhere to the manufacturer’s recommended torque specifications and installation procedures.
Check alignment: Ensure that the fitting is properly aligned with the connecting parts before tightening.
Inspect sealing surfaces: Clean and inspect sealing surfaces to ensure they are free of debris and damage before installation.
Worn or Damaged Fittings
Wear and tear can affect AN fittings over time, leading to leaks. Signs of wear include visible corrosion, cracks, or deformations. Corrosion can weaken the fitting material, while overuse or repeated stress can lead to physical damage.
Causes of damage:
Corrosion: Exposure to harsh chemicals or moisture can lead to rust and corrosion, degrading the fitting’s integrity.
Overuse: Continuous operation or excessive pressure can cause fittings to become worn out or damaged.
Physical damage: Impacts or mishandling can crack or distort fittings.
Inspection and maintenance tips:
Regular inspections: Routinely check fittings for signs of wear, corrosion, or damage.
Replace worn parts: Replace fittings showing signs of significant wear or damage to prevent leaks.
Use protective coatings: Apply anti-corrosive coatings or use fittings made from corrosion-resistant materials if exposed to harsh conditions.
Incorrect Fitting Size
Selecting the correct size of AN fittings is crucial for ensuring a secure and leak-proof connection. Mismatched sizes can lead to leaks because the fitting may not fit properly or create a secure seal.
How mismatched sizes cause leaks:
Improper seal: A fitting that is too large or too small may not properly seal against the connecting parts, allowing fluid to escape.
Increased stress: Incorrectly sized fittings can place undue stress on the connection, leading to potential leaks or failures.
Guide on measuring and choosing the correct size:
Measure accurately: Use precise measuring tools to determine the required fitting size. Measure both the internal and external diameters if needed.
Consult specifications: Refer to system or manufacturer specifications to select the correct size fitting.
Test fit: If possible, test fit the fitting before final installation to ensure it fits properly and securely.
Poor Quality Fittings
Using low-quality or counterfeit AN fittings poses significant risks. These fittings may not meet the required standards for pressure, durability, or material composition, leading to potential leaks.
Risks of poor-quality fittings:
Inconsistent performance: Low-quality fittings may not perform consistently, leading to leaks or failures.
Material weaknesses: Inferior materials can be more prone to damage or degradation, compromising the seal.
How to identify high-quality AN fittings:
Check certifications: Ensure that fittings are certified by recognized standards organizations.
Inspect materials: High-quality fittings are made from durable materials such as stainless steel or high-grade aluminum.
Verify supplier reputation: Purchase fittings from reputable suppliers known for their quality control and product standards.
Recommendations for trusted brands and suppliers:
Research suppliers: Look for suppliers with a strong reputation in the industry and positive customer reviews.
Request samples: Before making large purchases, request samples to verify the quality of the fittings.
Contaminants and Debris
Contaminants and debris can interfere with the sealing surfaces of AN fittings, leading to leaks. Dirt, dust, or other particles can prevent a proper seal, causing fluid to escape.
How contaminants lead to leaks:
Impaired sealing: Debris can create gaps or uneven surfaces that prevent a proper seal.
Increased wear: Contaminants can cause additional wear and tear on fittings over time.
Cleaning and maintenance practices:
Regular cleaning: Clean fittings and connecting surfaces regularly to remove contaminants.
Use filters: Implement filters or screens to prevent debris from entering the system.
Protective measures: Cover fittings with protective caps when not in use to prevent contamination.
Diagnosing AN Fitting Leaks
Diagnosing leaks in AN fittings requires a systematic approach to identify the source and cause of the leak. This process involves using the right tools, performing a visual inspection, and conducting pressure testing if necessary. Here is a step-by-step guide to help you accurately diagnose leaks in AN fittings.
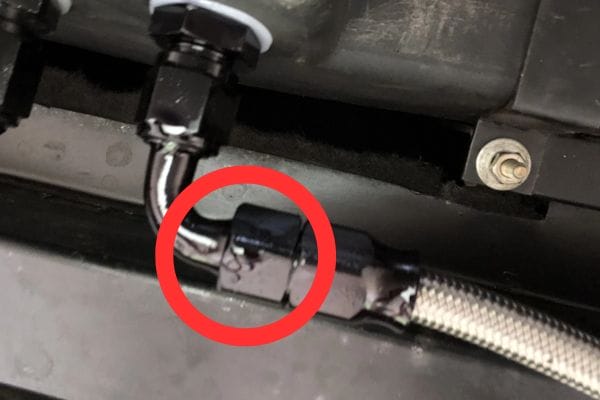
Step-by-Step Guide to Identifying Leaks in AN Fittings
Gather Necessary Tools and Equipment
Flashlight: To help illuminate dark areas and see better.
Clean Cloth: For wiping down fittings and connections.
Inspection Mirror: To view hard-to-reach areas.
Pressure Gauge: To measure system pressure and detect drops.
Leak Detection Fluid: To help visually identify leak locations.
Wrenches and Pliers: For tightening and loosening fittings.
Preparation
Turn Off the System: Ensure the hydraulic or fluid system is turned off and depressurized before beginning the inspection.
Clean the Area: Wipe down the fittings and surrounding areas to remove dirt, oil, and other contaminants that could obscure the leak.
Visual Inspection
Inspect the Fittings: Use a flashlight and inspection mirror to closely examine the AN fittings. Look for obvious signs of wear, corrosion, cracks, or damage.
Check Connections: Ensure all fittings are properly seated and aligned. Misaligned or loose connections can cause leaks.
Identify Wet Spots: Look for any wet spots, drips, or stains around the fittings and connections, that indicate a leak.
Using Leak Detection Fluid
Apply Fluid: Spray or brush leak detection fluid around the suspected leak areas.
Observe: Watch for bubbles forming at the leak site. The fluid will react with escaping air or fluid, making the leak location more visible.
Pressure Testing
Repressurize the System: Carefully turn on the system and allow it to build pressure.
Monitor Pressure: Use a pressure gauge to monitor the system pressure. A pressure drop may indicate a leak.
Check for Leaks: While the system is under pressure, use the leak detection fluid again to check for leaks around the fittings.
Listen for Hissing: Sometimes, you can hear a hissing sound, which indicates escaping air or fluid from a leak.
Evaluate and Document Findings
Record Observations: Take notes of any leaks found, including their exact location and potential cause.
Photographic Evidence: Take photos of the leaks for reference and to assist with repairs.
Fixing AN Fitting Leaks
Fixing leaks in AN fittings involves several key steps, including reinstalling fittings, replacing worn or damaged fittings, ensuring a proper fit, and implementing regular maintenance and preventative measures. Each of these steps is crucial to maintaining the integrity and efficiency of your hydraulic or fluid system.
Reinstalling Fittings
Detailed Instructions on How to Reinstall AN Fittings Correctly
Preparation:
Turn Off and Depressurize the System: Ensure the system is off and depressurized to avoid fluid or air escaping during reinstallation.
Clean the Area: Wipe down the fitting and surrounding area with a clean cloth to remove any debris or fluid residues.
Remove the Existing Fitting:
Use Appropriate Tools: Use a wrench or pliers to carefully loosen and remove the existing fitting. Take care not to damage the fitting or surrounding components.
Inspect the Threads and Sealing Surface: Check for any damage or wear on the threads and sealing surfaces of both the fitting and the connection point.
Install the New Fitting:
Apply Lubricant: Lightly lubricate the threads of the fitting with a suitable lubricant to ensure smooth installation and prevent galling.
Align the Fitting: Carefully align the fitting with the connection point to ensure a proper fit.
Hand-Tighten: Start by hand-tightening the fitting to avoid cross-threading.
Use a Torque Wrench: Finish tightening the fitting with a torque wrench to the manufacturer’s specified torque value. This ensures the fitting is neither over-tightened nor under-tightened.
Common Pitfalls to Avoid During Reinstallation:
Over-Tightening: Can damage threads and sealing surfaces, leading to leaks.
Under-Tightening: May result in insufficient sealing pressure, causing leaks.
Cross-Threading: Misaligned threads can damage both the fitting and the connection point, leading to leaks and difficulty in achieving a proper seal.
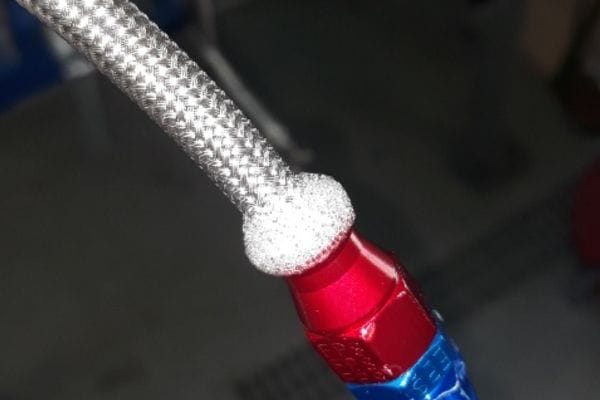
Replacing Worn or Damaged Fittings
How to Safely Remove and Replace Worn or Damaged Fittings
Turn Off and Depressurize the System: Ensure the system is safe to work on by turning it off and releasing any pressure.
Remove the Damaged Fitting:
Use Appropriate Tools: Use a wrench or pliers to carefully loosen and remove the damaged fitting.
Inspect the Connection Point: Check for any signs of damage or wear at the connection point. Clean the area thoroughly.
Select a Replacement Fitting:
Match the Size and Type: Ensure the replacement fitting matches the size and type of the original fitting.
Choose High-Quality Parts: Opt for high-quality fittings from reputable manufacturers to ensure durability and reliability.
Install the Replacement Fitting:
Apply Lubricant: Lightly lubricate the threads of the new fitting.
Align and Hand-Tighten: Align the fitting with the connection point and hand-tighten to avoid cross-threading.
Torque to Specifications: Use a torque wrench to tighten the fitting to the manufacturer’s specifications.
Ensuring Proper Fit
Methods to Ensure a Secure and Proper Fit
Correct Sizing:
Measure Accurately: Use precise measuring tools to ensure the fitting size matches the connection point.
Check Manufacturer Specifications: Refer to manufacturer guidelines to confirm the correct size and type of fitting.
Alignment:
Proper Alignment: Ensure the fitting is perfectly aligned with the connection point to prevent cross-threading and ensure a proper seal.
Use Alignment Tools: Utilize alignment tools if necessary to achieve correct alignment.
Tightening:
Hand-Tighten First: Begin by hand-tightening the fitting to prevent cross-threading.
Torque to Specifications: Finish tightening with a torque wrench to the specified torque value.
Maintenance and Preventative Measures
Routine Maintenance Tips to Prevent Future Leaks
Regular Inspections:
Visual Checks: Routinely inspect fittings for signs of wear, corrosion, or damage.
Pressure Testing: Conduct regular pressure tests to ensure the system maintains its integrity.
Cleaning:
Remove Debris: Keep fittings and surrounding areas clean to prevent contaminants from affecting the seal.
Use Protective Caps: Cover unused fittings with protective caps to prevent dirt and debris from entering.
Lubrication:
Apply Lubricant During Installation: Use appropriate lubricants on threads during installation to ensure smooth tightening and prevent damage.
Sealing:
Thread Sealant: Use thread sealant or tape on threaded connections to enhance the seal and prevent leaks.
Use of Lubricants and Sealants:
Thread Lubricants: Apply thread lubricants to reduce friction and prevent galling during installation.
Sealants: Use thread sealants or tape to enhance the seal on threaded connections and prevent leaks.
By following these detailed steps for reinstalling, replacing, and maintaining AN fittings, you can effectively prevent leaks and ensure the long-term reliability and efficiency of your hydraulic or fluid systems. Proper installation, routine maintenance, and the use of high-quality components are key to maintaining leak-free AN fittings.
Conclusion
By adhering to best practices, using high-quality components, and conducting regular inspections, you can significantly reduce the risk of leaks and ensure the longevity and reliability of your systems. Taking these preventative measures not only enhances system performance but also minimizes downtime and maintenance costs. Follow these guidelines diligently to keep your AN fittings leak-free and your operations running smoothly.
FAQ
Signs of a leak include visible fluid around the fitting, a drop in system pressure, or the presence of bubbles when using leak detection fluid.
Essential tools include a wrench, torque wrench, inspection mirror, flashlight, leak detection fluid, and a clean cloth.
Yes, over-tightening can damage the fitting or sealing surface, leading to leaks.
It’s recommended to inspect AN fittings regularly, such as during routine maintenance checks or whenever the system is serviced.
Replace the worn or damaged fitting with a high-quality replacement that matches the size and specifications of the original.
Thread sealants can be used on non-flared threaded connections to enhance the seal and prevent leaks. Always follow manufacturer recommendations.