Torque refers to the rotational force applied to fasteners, such as bolts and nuts, to achieve a specific level of tightness. In hydraulic systems, maintaining proper torque on tube connections is crucial for creating secure seals that prevent fluid leaks.
Understanding Torque and Its Role
A. Definition of Torque
Torque is defined as the measure of rotational force applied to an object, typically described in units of Newton meters (Nm) or foot-pounds (ft-lbs). In mechanical engineering, it represents the effectiveness of a force to produce rotation around an axis. Mathematically, torque (τ) can be expressed as the product of force (F) and the distance (r) from the axis of rotation to the point where the force is applied: τ=F×r. This fundamental concept is crucial in applications involving fasteners and fittings, where the correct application of torque ensures that components are held securely together without compromising their integrity.
B. How Torque Affects Sealing
In hydraulic tube connections, the application of torque compresses the fitting and tubing materials, creating a tight seal. When a hydraulic fitting is torqued to the manufacturer’s specifications, it generates sufficient clamping force to deform the surfaces slightly, filling any microscopic gaps and imperfections. This deformation is key to achieving a leak-free connection. The appropriate amount of torque ensures that the seal is strong enough to withstand internal pressure without failing, while also preventing over-compression, which can lead to material fatigue or failure. The mechanics behind this sealing process emphasize the delicate balance between too little and too much torque, underscoring the importance of precise torque application in maintaining hydraulic integrity.
C. Common Misconceptions About Torque
There are several misconceptions surrounding torque that can lead to improper application and potential failures in hydraulic systems. One common myth is that “more torque is always better,” leading to over-tightening of fittings. In reality, excessive torque can deform fittings, leading to cracks and leaks. Another misconception is the belief that torque values are interchangeable across different materials and sizes. Each fitting type has specific torque requirements that depend on factors such as material properties, thread size, and intended application. Finally, some may assume that using lubricants can be disregarded when applying torque. However, lubricants can significantly affect torque values and must be considered to ensure accurate and effective fastening. By addressing these misconceptions, technicians can better understand the critical role of torque in maintaining leak-free hydraulic connections.
Identifying Proper Torque Specifications
A. Manufacturer Specifications
Adhering to manufacturer torque specifications is essential for ensuring the integrity and performance of hydraulic tube connections. Each fitting and component is designed with specific torque values that account for the materials used, the size of the threads, and the intended operating conditions. These specifications are determined through rigorous testing and engineering analysis to optimize sealing and performance while minimizing the risk of failure. Deviating from these guidelines can result in either under-torquing, which may lead to leaks, or over-torquing, which can cause deformation, material fatigue, or even catastrophic failure. Thus, referencing and strictly following the manufacturer’s torque settings is critical in maintaining the safety and efficiency of hydraulic systems.
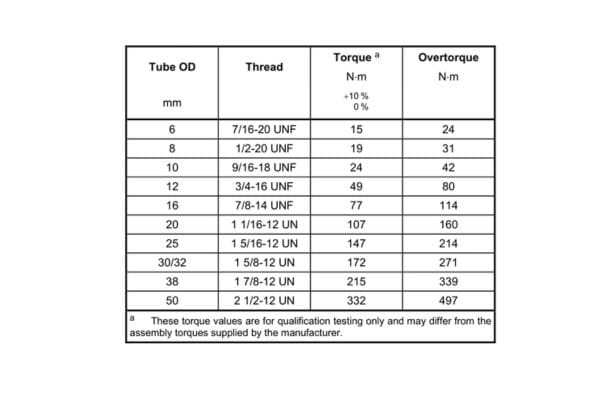
B. Tools for Measuring Torque
To achieve the proper torque specifications, various tools are available, with torque wrenches being the most commonly used. There are several types of torque wrenches:
Click Torque Wrenches: These emit a clicking sound when the preset torque level is reached, providing audible feedback to the user. They are widely used for their simplicity and effectiveness.
Beam Torque Wrenches: These utilize a beam that bends when torque is applied, with a scale indicating the applied torque. They require careful reading and are less common in professional settings.
Digital Torque Wrenches: These provide precise torque measurements on a digital display and often feature programmable settings. They are ideal for applications requiring high accuracy.
Torque Angle Gauges: These are used in conjunction with a standard torque wrench to apply a specific angle of rotation after an initial torque value is set, providing additional precision.
Using the appropriate tool is vital to ensure that the correct torque is applied. Additionally, other tools such as torque multipliers can be beneficial for high-torque applications, allowing for easier and safer torque application without excessive force.
C. Importance of Calibration
Regular calibration of torque measurement tools is crucial for ensuring accurate and reliable torque application. Over time, tools can become worn or damaged, leading to inaccurate measurements that can jeopardize the integrity of connections. Calibration involves comparing the tool’s measurements against a known standard and making necessary adjustments to ensure precision.
Calibration should be performed at regular intervals, based on the tool’s usage frequency and manufacturer recommendations. This practice not only helps maintain accuracy but also extends the lifespan of the tools by identifying wear or damage early. Furthermore, ensuring that torque wrenches are calibrated before significant projects can prevent costly errors and enhance safety in hydraulic systems. By prioritizing calibration, technicians can trust that their torque applications meet the necessary specifications, ultimately leading to leak-free and efficient hydraulic connections.
Consequences of Improper Torque
A. Common Signs of Over-Torquing
Over-torquing occurs when excessive force is applied during the tightening of hydraulic fittings, leading to various detrimental effects. Recognizing the signs of over-torquing is essential for maintaining system integrity and preventing failures. Common indicators include:
Deformation of Fittings: One of the most immediate signs of over-torquing is visible deformation of the fitting or connecting components. This can manifest as flattened or bent sections where the fitting has been tightened. Such changes compromise the fitting’s ability to seal properly, increasing the risk of leaks.
Cracking: Over-torqued fittings may develop cracks, particularly in materials that are more brittle, such as certain metals or plastics. These cracks can start small and propagate rapidly under pressure, leading to sudden failure. Even minor hairline fractures can severely weaken the structural integrity of a fitting.
Material Fatigue: Continuous exposure to excessive torque can lead to material fatigue, a process where the material undergoes cyclic loading and unloading that ultimately leads to failure. Symptoms of fatigue may include discoloration or visible wear patterns on the fitting surface.
Thread Damage: Over-torquing can strip threads on both the fitting and the receiving end, making it difficult or impossible to create a reliable connection. Stripped threads not only compromise the integrity of the connection but may also require costly replacements or repairs.
Failure of Sealing Surfaces: In many hydraulic systems, fittings rely on specific sealing surfaces to maintain pressure. Over-torquing can deform these surfaces, leading to improper sealing. As a result, fluid may leak past the joint, causing operational inefficiencies and potential system damage.
Recognizing these signs is crucial for maintenance personnel to take corrective actions before a catastrophic failure occurs. Regular inspections and monitoring can help identify over-torqued connections early.
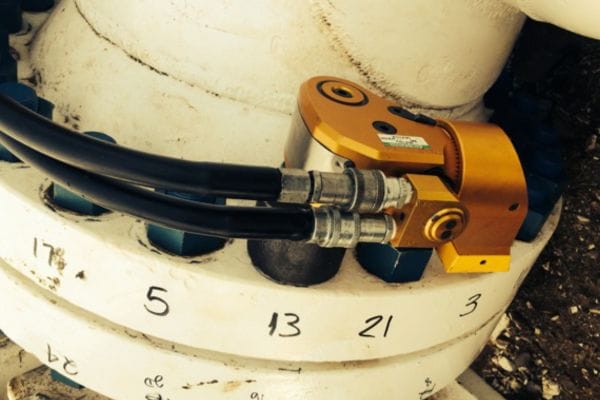
B. Signs of Under-Torquing
Under-torquing refers to insufficient tightening of hydraulic fittings, which can lead to significant operational issues. The consequences of under-torquing can often be just as severe as those caused by over-torquing. Common signs include:
Fluid Leaks: The most apparent sign of under-torquing is the presence of fluid leaks at connection points. Insufficient torque may fail to compress the O-rings or sealing surfaces adequately, allowing hydraulic fluid to escape. This not only leads to fluid loss but can also create hazardous conditions in the working environment.
Pressure Fluctuations: In hydraulic systems, maintaining consistent pressure is crucial for efficient operation. Under-torqued fittings can cause pressure drops, leading to inconsistent performance. Operators may notice fluctuations in system pressure readings, indicating that the connection is not secure.
Operational Inefficiencies: When leaks occur due to under-torquing, the hydraulic system may have to work harder to maintain desired pressure levels. This can lead to increased wear and tear on components, decreased efficiency, and higher energy consumption. Over time, these inefficiencies can result in costly downtime and maintenance.
Increased Noise Levels: Leaks can also create unusual sounds in hydraulic systems. Under-torqued fittings may produce hissing or bubbling sounds as fluid escapes. This noise is often a clear indicator that further investigation is necessary.
Potential for Catastrophic Failure: In extreme cases, under-torqued fittings can lead to catastrophic failure, especially in high-pressure applications. If a fitting fails suddenly, it can result in the loss of control of hydraulic machinery, posing a severe safety risk to operators and nearby personnel.
Best Practices for Applying Proper Torque
A. Step-by-Step Torque Application Guide
Applying the correct torque to hydraulic fittings is critical for ensuring leak-free connections. Follow these steps for a reliable torque application process:
Gather Necessary Tools: Ensure you have the right tools on hand, including a calibrated torque wrench, a suitable socket or attachment for the fitting, and any required protective equipment (e.g., gloves, and safety goggles).
Inspect Fitting and Connection Surfaces: Thoroughly inspect both the hydraulic fitting and the surface it connects to for any signs of damage, debris, or corrosion. Clean surfaces as necessary to ensure a proper seal.
Initial Hand Tightening: Start by hand-tightening the fitting to ensure that it is seated correctly. This step helps align the threads and eliminates any cross-threading issues that could lead to improper torque application.
Apply Torque in a Controlled Manner: Using the torque wrench, apply torque gradually. Start by setting the wrench to a lower torque value (usually about 30-50% of the final specification) to establish a baseline seal.
Increase Torque Gradually: After achieving the initial torque, increase the setting to the manufacturer-recommended value. Turn the wrench slowly and smoothly, avoiding sudden movements that could cause over-torquing.
Use a Torque Pattern: For applications with multiple fittings, employ a specific torque pattern (discussed in section B) to ensure an even distribution of pressure and avoid misalignment.
Double-Check Torque: Once the final torque is reached, re-check the torque using the wrench to confirm that the setting is maintained. If adjustments are necessary, always loosen the fitting slightly before re-tightening to the correct specification.
Document the Process: Keep records of the torque values used for each fitting. Documentation can help with future maintenance and inspections.
By following these steps meticulously, technicians can ensure that torque is applied correctly, thus preventing leaks and failures in hydraulic systems.
B. Recommended Torque Patterns
In multi-bolt applications, the sequence in which torque is applied plays a significant role in achieving a secure seal. Here are key points regarding torque patterns:
Importance of Torque Sequence: Applying torque in a specific sequence helps distribute stress evenly across all fittings. This is particularly crucial for large assemblies where uneven pressure can lead to warping or leaks.
Common Torque Patterns:
Criss-Cross Pattern: For circular or rectangular bolt arrangements, start from the center and work outward in a criss-cross fashion. This approach minimizes stress concentration and ensures uniformity.
Star Pattern: Similar to the criss-cross method, the star pattern is effective for flanged connections. Start with one bolt, then move to the opposite bolt, followed by adjacent ones. This sequence helps maintain an even seal.
Incremental Steps: Apply torque in increments, gradually increasing to the final specification. This method allows for adjustments if any misalignment occurs during the tightening process.
Visual Aids: Utilize diagrams or charts to illustrate recommended torque sequences. Having a visual reference can help technicians remember the correct order, especially in complex installations.
By adhering to these torque patterns, technicians can enhance the reliability of tube connections, reducing the risk of leaks and system failures.
C. Regular Maintenance and Inspections
To maintain the integrity of torque settings and ensure leak-free operations, regular maintenance and inspections are essential. Here are the best practices for ongoing checks:
Routine Inspections: Schedule regular inspections of hydraulic fittings and connections, particularly in high-pressure systems. This helps identify any signs of wear, damage, or loosening before they lead to failures.
Re-torquing: Periodically re-check torque values, especially after initial installation or following significant operational changes (e.g., pressure adjustments, temperature fluctuations). Re-torquing helps ensure that connections remain secure over time.
Visual Checks for Signs of Wear: During inspections, look for visual indicators such as fluid leaks, corrosion, or signs of fatigue. Early detection can prevent more significant issues from developing.
Record-Keeping: Maintain a detailed log of inspections, including torque values, observed conditions, and any corrective actions taken. This documentation serves as a valuable reference for future maintenance activities.
Tool Calibration: Regularly calibrate torque wrenches and other measuring tools to ensure accuracy. Using improperly calibrated tools can lead to incorrect torque application, increasing the risk of leaks.
Troubleshooting Torque-Related Issues
A. Diagnosing Torque Problems
Identifying torque-related failures in hydraulic systems requires a systematic approach to accurately diagnose the issue. Follow these steps:
Initial Observation: Begin by visually inspecting the hydraulic fittings for any obvious signs of leaks or damage. Look for fluid pooling, discoloration, or corrosion around the fittings, which may indicate a problem.
Pressure Testing: Conduct a pressure test to check for leaks. By applying pressure to the system and monitoring for pressure drops, you can determine if a fitting is leaking. This test can help isolate the problem areas.
Torque Verification: Use a calibrated torque wrench to verify that the fittings are tightened to the manufacturer’s specifications. If the torque is below the recommended levels, this may be a direct cause of leaks.
Sequential Tightening Check: If multiple fittings are involved, verify that they were tightened in the proper sequence. Any irregularities in the tightening order may contribute to misalignment or leaks.
Review Historical Data: Check maintenance logs for past torque values and any previous issues with the fittings. Patterns may emerge that can help identify if torque-related problems are recurring.
Environmental Assessment: Consider the operating environment. Factors such as temperature fluctuations, vibrations, or exposure to corrosive substances can exacerbate torque issues and contribute to fitting failures.
Functional Testing: Finally, conduct functional tests on the hydraulic system to observe how it performs under load. Sudden pressure drops or fluctuations may indicate torque-related problems.
By systematically following these steps, technicians can effectively diagnose torque-related issues and implement appropriate corrective measures.
B. Tools and Techniques for Diagnosis
Several tools and techniques can assist in diagnosing torque-related issues in existing connections:
Torque Wrench: A calibrated torque wrench is essential for measuring the tightness of fittings accurately. This tool ensures that fittings are torqued to the correct specifications, reducing the risk of leaks.
Pressure Gauges: These devices measure the pressure within the hydraulic system. A sudden pressure drop can signal a leak or failure in the fittings, warranting further investigation.
Leak Detection Fluids: These special fluids change color or create bubbles when they come into contact with escaping fluids. Applying leak detection fluid around fittings can help pinpoint the source of a leak.
Ultrasonic Leak Detectors: These advanced devices can detect high-frequency sounds produced by gas or fluid leaks. They are especially useful in noisy environments where traditional methods may fail.
Visual Inspection Tools: Use magnifying glasses or borescopes to closely inspect hydraulic fittings for cracks, wear, or corrosion that may not be visible to the naked eye.
Vibration Analysis Tools: Monitoring vibrations in hydraulic systems can help identify misalignments or issues related to torque. Changes in vibration patterns can indicate a developing problem.
Conclusion
By committing to these practices, you can enhance the reliability and safety of your hydraulic systems, ultimately contributing to smoother operations and reduced operational costs. Let’s work together to ensure our systems remain leak-free and perform at their best.
FAQ
What is torque, and why is it important in hydraulic systems?
Torque is a measure of rotational force applied to fasteners. In hydraulic systems, proper torque ensures tight and secure connections, preventing leaks and maintaining system efficiency.
What are the consequences of improper torque?
Improper torque can lead to leaks, system failures, material fatigue, and safety hazards, potentially resulting in costly downtime and maintenance.
How can I determine the correct torque specifications for my system?
Always refer to the manufacturer’s specifications for torque settings. These guidelines are based on the specific materials and design of the fittings.
What tools can I use to measure torque accurately?
Torque wrenches are the primary tools for measuring and applying the correct torque. Digital torque wrenches can provide more precise readings.
What signs indicate that torque may be improperly applied?
Common signs of over-torquing include deformation or cracking of fittings, while under-torquing may result in visible leaks or unstable pressure readings.
How often should I check and calibrate my torque tools?
It’s recommended to calibrate torque tools regularly, typically at least once a year, or more frequently if used extensively in critical applications.