Burst strength refers to the maximum pressure a hose can withstand before it fails. A hose with inadequate burst strength may rupture under high pressure, leading to costly replacements and frustrating water loss during critical tasks. Factors such as water pressure, material quality, and proper storage all influence a hose’s burst strength.
Understanding Burst Strength
A. Definition of Burst Strength
Burst strength is defined as the maximum internal pressure a garden hose can withstand before it ruptures. It is a critical performance metric, as hoses are often exposed to fluctuating water pressures during use. When a hose reaches its burst strength, it can fail catastrophically, leading to leaks or complete breaks. Understanding burst strength is essential for consumers to select hoses that are suitable for their specific watering tasks and environmental conditions.
A hose’s burst strength is typically expressed in pounds per square inch (psi). For example, a hose with a burst strength rating of 300 psi can handle water pressure up to that threshold before risking failure. This rating is influenced by various factors, including the materials used in the hose construction and the manufacturing process.
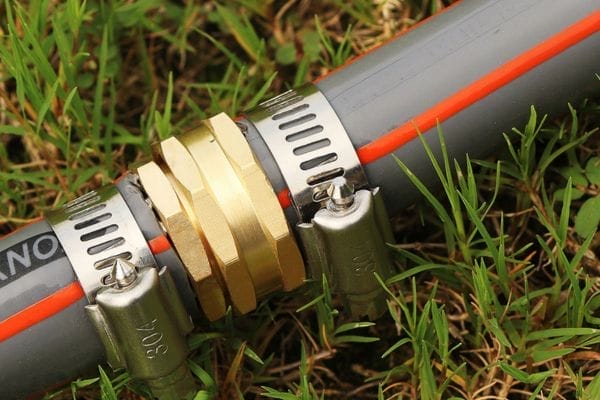
B. How Burst Strength is Measured
Burst strength is measured through standardized testing procedures. Typically, a hose is filled with water, and pressure is gradually increased until the hose ruptures. This process is usually conducted in a controlled environment to ensure accurate and repeatable results.
During the test, the pressure is monitored using a pressure gauge, and the point at which the hose fails is recorded. The results provide a clear indication of the hose’s capabilities and limitations. Manufacturers often provide burst strength ratings on the product packaging or specifications, allowing consumers to make informed choices.
It is important to note that the conditions under which a hose is tested may differ from real-world usage scenarios. Factors like temperature, hose length, and the presence of kinks or bends can affect a hose’s actual performance. Therefore, while burst strength ratings provide valuable guidelines, they should be considered alongside other factors when selecting a hose.
C. Importance of Burst Ratings in Hose Selection
The burst strength rating plays a crucial role in hose selection for several reasons. First, it helps consumers gauge whether a particular hose is suitable for their specific needs. For instance, if you plan to use a hose for high-pressure tasks such as power washing, selecting a hose with a high burst strength rating is essential to avoid potential failures.
Second, understanding burst strength can help prevent accidents and property damage. Using a hose that is not rated for the intended pressure can lead to sudden ruptures, resulting in water damage to surrounding areas or injury to users.
Finally, selecting a hose with an appropriate burst strength rating can enhance its longevity. Hoses that are consistently subjected to pressures exceeding their ratings are more likely to fail prematurely. By choosing a hose that can handle the expected pressures, users can extend its lifespan and reduce the frequency of replacements.
D. Overview of Typical Burst Pressure Ratings for Various Hoses
Different types of garden hoses come with varying burst strength ratings, which are influenced by the materials used and the intended applications. Here is an overview of typical burst pressure ratings for common hose types:
Light-Duty Hoses
Typically made of vinyl or lightweight materials, these hoses are suitable for general gardening tasks. Burst strength usually ranges from 150 to 200 psi. While they are easy to handle and store, they may not withstand high-pressure applications.
Medium-Duty Hoses
These hoses often feature reinforced construction, making them more durable than light-duty options. Their burst strength generally falls between 200 and 300 psi. They are suitable for a variety of tasks, including general watering and light-duty cleaning.
Heavy-Duty Hoses
Constructed from high-quality materials like rubber or reinforced vinyl, heavy-duty hoses are designed for demanding applications. Their burst strength typically ranges from 300 to 500 psi, making them ideal for tasks such as power washing and industrial use.
Specialty Hoses
Some hoses are specifically designed for unique applications, such as high-temperature or high-pressure environments. These hoses can have burst strength ratings that exceed 500 psi, making them suitable for specialized tasks in professional settings.
Common Causes of Hose Bursts
A. High Water Pressure
Definition and Typical Pressure Ranges
High water pressure refers to the force exerted by water flowing through a hose, typically measured in pounds per square inch (psi). Standard residential water pressure ranges from 40 to 60 psi. However, in some areas, it can exceed 80 psi, especially if multiple outlets are in use simultaneously or if the municipal water supply is pressurized beyond normal levels.
Consequences of Excessive Pressure
When water pressure exceeds a hose’s burst strength, the risk of rupture increases significantly. High pressure can lead to immediate failures, such as bursts or leaks, resulting in wasted water and potential property damage. Additionally, hoses under excessive pressure may weaken over time, leading to premature deterioration and reduced lifespan.
Solutions
To mitigate the risk of high water pressure, consider installing a pressure regulator at your water source. This device helps maintain consistent pressure, ensuring it stays within safe limits for your hose. Regularly check your hose’s specifications and select one with an appropriate burst strength rating based on your water pressure needs.
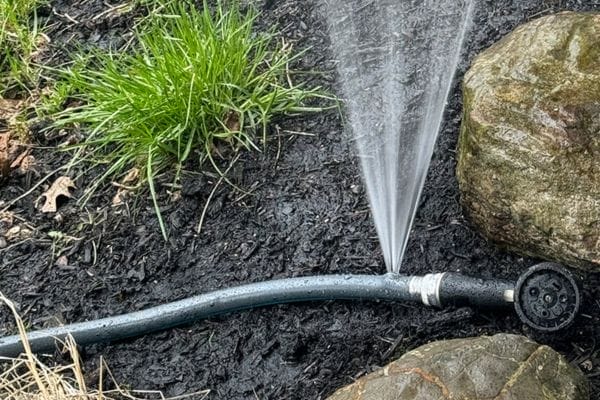
B. Improper Storage
Effects of Sun Exposure and Temperature Fluctuations
Improper storage can significantly impact a hose’s durability. Exposure to direct sunlight can cause materials, especially vinyl, to degrade and lose flexibility, leading to cracks and bursts. Similarly, extreme temperature fluctuations can cause hoses to expand and contract, weakening their structure over time.
Best Practices for Storage
To protect your hose, store it in a cool, shaded area, away from direct sunlight and extreme temperatures. Coil the hose neatly to avoid kinks, and consider using a hose reel or holder for easy storage. During winter, it’s advisable to bring hoses indoors to prevent damage from freezing temperatures.
C. Kinks and Twists
How Kinks Increase Internal Pressure
Kinks and twists in a hose restrict the flow of water, leading to increased internal pressure at the kinked area. This pressure can exceed the hose’s rated burst strength, causing sudden ruptures or leaks. Kinks not only compromise the hose’s structural integrity but also impede effective watering or cleaning.
Prevention Techniques
To prevent kinks, always lay hoses flat when uncoiling and avoid twisting them during use. Consider using hoses with a kink-resistant design, which typically feature reinforced materials that help maintain their shape. Additionally, using hose guides or stakes can help keep hoses untangled and reduce the likelihood of kinks.
D. Material Degradation
Effects of UV Rays
UV rays from the sun can significantly degrade the materials used in garden hoses, especially vinyl and rubber. Prolonged exposure leads to brittleness, discoloration, and cracks, all of which can compromise a hose’s burst strength and overall integrity.
Signs of Wear and Tear
Signs of material degradation include visible cracks, hardening of the hose surface, or a decrease in flexibility. Regular inspections can help identify these issues early, allowing for timely replacement or repairs before a burst occurs.
E. External Damage
Common Sources of Damage
Hoses can suffer damage from a variety of external sources, including garden tools, pets, and vehicles. Sharp objects can puncture or cut hoses, while heavy objects can crush them, leading to leaks or bursts.
Preventative Measures
To protect your hose from external damage, keep it out of high-traffic areas and store it securely when not in use. Use hose reels or racks to keep hoses off the ground and away from potential hazards. Additionally, educating family members and pets about hose safety can prevent accidental damage.
F. Freezing Conditions
How Freezing Leads to Hose Bursts
Water expands when it freezes, increasing pressure within a hose if it is filled with water. This expansion can cause hoses to split or rupture, particularly at weak points like fittings or previously damaged areas.
Tips for Winterizing Hoses
To winterize your hoses, drain all water completely before storing them. Coil them loosely and store them indoors to avoid exposure to freezing temperatures. If possible, use insulated covers for outdoor spigots and hoses during the winter months to protect against freezing damage.
Choosing the Right Hose Based on Burst Strength
A. Types of Hoses and Their Intended Uses
Light-Duty Hoses
Light-duty hoses are typically made from materials like vinyl and are designed for basic gardening tasks such as watering flowers, light cleaning, and filling small containers. These hoses are lightweight and easy to maneuver, making them ideal for casual gardeners. However, they usually have lower burst strength ratings, typically ranging from 150 to 200 psi, which limits their use in high-pressure applications. When selecting a light-duty hose, consider its intended use to ensure it meets your watering needs without risking premature failure.
Heavy-Duty Hoses
Heavy-duty hoses are constructed from more robust materials, often reinforced with additional layers to withstand higher pressures and more demanding tasks. These hoses are suitable for a wide range of applications, including extensive garden watering, pressure washing, and industrial use. With burst strength ratings typically ranging from 300 to 500 psi, heavy-duty hoses offer greater durability and longevity. When choosing a heavy-duty hose, evaluate the specific tasks you plan to perform to select a hose that will endure regular use without bursting.
Specialty Hoses
Specialty hoses are designed for specific applications, such as high-temperature or high-pressure environments. These hoses may include features tailored for unique tasks, like handling hot water or being resistant to chemicals. Burst strength ratings for specialty hoses can exceed 500 psi, making them suitable for professional and industrial settings. When considering a specialty hose, assess the specific requirements of your project to choose one that can safely handle the conditions it will face.
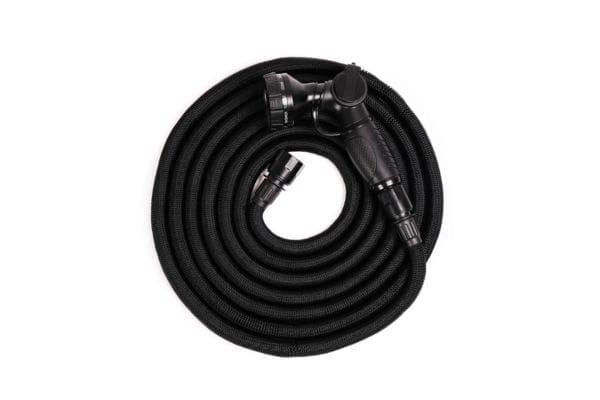
B. Understanding Material Differences
Vinyl vs. Rubber
Vinyl hoses are lightweight, flexible, and generally less expensive, making them a popular choice for casual gardeners. However, they are less durable and can degrade more quickly under UV exposure or extreme temperatures. Rubber hoses, on the other hand, are heavier and more robust, offering superior resistance to kinks, UV rays, and temperature fluctuations. They typically have higher burst strength ratings, making them suitable for more demanding tasks. When deciding between vinyl and rubber, consider factors such as durability, flexibility, and intended use to make an informed choice.
Reinforced Hoses
Reinforced hoses feature additional layers of material or structural designs that enhance their durability and burst strength. These hoses are designed to withstand higher pressures and are less prone to kinking or bursting under stress. Reinforcement can be achieved through various methods, such as adding braided fibers or using thicker walls. When selecting a reinforced hose, pay attention to the specific type of reinforcement and the hose’s burst strength rating to ensure it meets your needs for durability and performance.
C. Assessing Your Specific Needs
Gardening Tasks
When choosing a hose, consider the specific gardening tasks you will be performing. For light watering or container gardening, a light-duty hose may suffice. However, if you need to water larger areas, clean driveways, or operate attachments like pressure washers, a heavy-duty hose with a higher burst strength rating is essential. Additionally, evaluate the frequency and intensity of use; regular heavy use necessitates a more durable hose to avoid the frustration of frequent replacements.
Environmental Considerations
Environmental factors also play a crucial role in hose selection. If you live in an area with extreme temperatures, high UV exposure, or abrasive conditions, choosing a hose that can withstand these elements is vital. For instance, a rubber or reinforced hose may be more suitable for regions with intense sunlight or fluctuating temperatures, as they offer greater durability. Furthermore, consider local water pressure conditions; if your area experiences high pressure, opt for hoses specifically rated for higher burst strengths to prevent potential failures.
Practical Tips for Hose Maintenance
A. Regular Inspections
What to Look For
Conducting regular inspections of your garden hose is essential for identifying potential issues before they lead to significant problems. During your inspections, check for visible signs of wear and tear, such as cracks, kinks, or bulges in the hose. Pay attention to the fittings and connections as well, looking for any rust, corrosion, or damage that could lead to leaks. Additionally, inspect the hose for discoloration or stiffness, which can indicate material degradation due to UV exposure or age.
Importance of Routine Checks
Routine inspections help you catch issues early, allowing for timely repairs or replacements. This proactive approach not only extends the lifespan of your hose but also ensures reliable performance during critical tasks. Regular checks can save you from the inconvenience of sudden hose failures and the resulting water waste, helping you maintain a more efficient and enjoyable gardening experience.
B. Proper Hose Use
Guidelines for Connecting and Disconnecting
When connecting and disconnecting hoses, it’s crucial to follow best practices to prevent damage. Always ensure that the hose is completely drained of water before disconnecting it to avoid splashing and potential injury. When connecting, make sure the threads of the hose and faucet fit securely to prevent leaks. Avoid over-tightening the fittings, as this can cause stress on the hose material, leading to premature wear.
Recommendations for Using Nozzles and Attachments
When using nozzles or attachments, ensure they are compatible with your hose size and type. Heavy-duty hoses are better suited for high-pressure attachments, while light-duty hoses may not withstand such pressure. Always check the nozzle settings before use to ensure they are appropriate for your watering tasks, as improper settings can lead to increased internal pressure and potential hose bursts. After using attachments, disconnect them carefully and store them properly to prevent damage to both the hose and the attachments.
C. Importance of Proper Fittings and Clamps
Choosing the Right Size
Selecting the correct fittings and clamps is essential for maintaining a secure connection between your hose and water source. The fittings should match the diameter of your hose to ensure a tight fit, which helps prevent leaks. Using adapters can help if you have hoses and fittings of different sizes, but be cautious, as improper fittings can create weak points that may lead to bursts or leaks. Always opt for high-quality fittings made from durable materials to enhance the longevity of your hose system.
Regular Checks for Leaks
Periodically check all connections and fittings for leaks, especially after prolonged use or during seasonal changes. Look for water seepage around the fittings or any damp spots along the hose. If you notice a leak, it may be a simple matter of tightening the connection or replacing a worn washer in the fitting. Addressing leaks promptly not only prevents further damage to the hose but also conserves water, making your gardening practices more sustainable.
A Note on Using Garden Hoses with Pressure Washers
When connecting a garden hose to a pressure washer, here are the key points to keep in mind:
1. Function of the Garden Hose
The garden hose only supplies water from your faucet to the pressure washer.
It does not experience high pressure—the high pressure happens after the pump, on the outlet side.
2. Risk of Flow Interruption
The most common problems:
- Kinks
- Twists
- Obstructions or debris in the hose
These issues can restrict water flow, which may:
- Damage the pressure washer pump
- Reduce performance
- Cause overheating due to lack of water for pump cooling
3. Importance of Uninterrupted Water Supply
Pressure washers require a consistent water flow to:
- Maintain proper operation
- Protect internal pump components from overheating or failure
4. Burst Strength Still Matters
While garden hoses connected to pressure washers don’t need extremely high burst strength, it’s still important to:
- Choose a hose with at least 200–300 psi burst strength to ensure durability
- Avoid cheap hoses that may rupture under temporary surges
5. Maintenance Tips
Always check for kinks before starting
Use a hose reel or hanger to prevent bending damage
Inspect hose ends and washers regularly for leaks or wear
6. Make an Informed Choice
Whether you’re watering plants or feeding water to a pressure washer:
- Choose a hose with the right burst strength for your tasks
- Maintain it well to extend its lifespan and reliability
- Consider environmental factors like UV exposure and temperature changes
Conclusion
Prioritizing burst strength in your hose selection is essential for ensuring reliability and longevity. A hose that meets your needs in terms of burst strength not only enhances your gardening experience but also saves you time and resources in the long run. If you need high-quality garden hose, please contact Topa, we can provide the best products!
FAQ
What is burst strength in a garden hose?
Burst strength refers to the maximum pressure a hose can withstand before failing or bursting. It is measured in pounds per square inch (psi) and is crucial for determining the hose’s suitability for various tasks.
How do I know the right burst strength for my needs?
Consider the water pressure in your area and the tasks you’ll be performing. For light gardening, a hose with a burst strength of 150-200 psi may suffice, while heavy-duty tasks may require hoses rated for 300 psi or more.
What materials are best for garden hoses?
Rubber hoses are generally more durable and resistant to UV rays and kinks compared to vinyl hoses. Reinforced hoses offer additional strength and longevity, making them suitable for demanding tasks.
How can I prevent my garden hose from bursting?
Regular inspections for wear and tear, proper storage away from sunlight, avoiding kinks, and using the correct fittings can help prevent hose bursts. Additionally, installing a pressure regulator can manage water pressure effectively.
What should I do if I notice a leak in my hose?
Check the fittings for tightness and replace any worn washers. If the leak persists, assess the hose for damage. Small punctures can sometimes be repaired with hose tape, but larger damages may require a hose replacement.
How should I store my garden hose during winter?
Drain all water from the hose to prevent freezing and store it indoors in a cool, dry place. Coiling it properly and keeping it away from extreme temperatures will help maintain its integrity.