Check valves are essential components in fluid systems, designed to allow fluid flow in one direction while preventing backflow. This crucial function helps maintain system pressure, protect equipment from damage, and ensure the efficient operation of hydraulic and pneumatic systems.
Understanding Check Valves
A. Function of Check Valves in Hydraulic Systems
Check valves play a critical role in hydraulic systems by ensuring fluid flows in a single direction, thereby preventing backflow. This function is essential for maintaining system pressure and protecting components from damage that could result from reverse flow. By allowing fluids to move only in the intended direction, check valves help to optimize system efficiency and reliability. They are significant in applications where fluid backflow can lead to contamination, equipment failure, or operational hazards.
B. Key Components of Check Valves
Check valves consist of several key components that work together to perform their function:
Body: The main structure of the valve, houses the internal components and provides the pathways for fluid flow.
Poppet: A movable element that opens and closes in response to fluid pressure. It allows flow through the valve when pressure is applied in the forward direction and closes to prevent backflow.
Spring: In spring-loaded check valves, the spring assists in closing the poppet when there is no flow or when back pressure occurs. The tension of the spring can affect the crack pressure, which is the minimum pressure required to open the valve.
Seals: Depending on the valve type, seals may be hard (metal) or soft (elastomeric), providing a tight closure to prevent leakage when the valve is closed.
These components work together to ensure the check valve operates effectively, balancing the need for flow with the need to prevent backflow.
C. Applications of Check Valves Across Various Industries
Check valves are utilized in a wide range of applications across multiple industries, including:
Oil and Gas: Used in pipelines and processing facilities to prevent backflow and protect equipment from high-pressure surges.
Water Treatment: Essential in water distribution systems to maintain pressure and prevent contamination from backflow.
Manufacturing: Employed in hydraulic systems for machinery, ensuring smooth operation and protecting sensitive components.
Food and Beverage: Used to maintain hygiene standards by preventing backflow in processing lines and ensuring safe fluid movement.
HVAC Systems: Check valves help manage fluid flow in heating and cooling systems, contributing to energy efficiency and system reliability.
Hard Seat Check Valves
A. Definition and Design
Hard seat check valves are engineered with a metal-to-metal sealing surface, typically made from materials such as stainless steel, brass, or other durable metals. This design ensures a robust connection that can withstand harsh conditions, making them ideal for a variety of industrial applications. The sealing mechanism relies on the contact between the valve’s poppet and the valve seat, which is often machined to precise tolerances to minimize leakage when the valve is closed.
In a hard seat check valve, the poppet is spring-loaded, allowing it to remain closed when no forward flow is present. When fluid flows in the intended direction and reaches a specified pressure, the poppet opens, permitting fluid to pass through. Upon cessation of flow or when back pressure is detected, the spring force closes the poppet tightly against the seat, effectively blocking any reverse flow.

B. Advantages of Hard Seat Check Valves
Durability and Wear Resistance:
Hard seat check valves are renowned for their durability. The metal-to-metal seal can withstand abrasive and corrosive environments, making these valves suitable for applications involving harsh fluids or extreme conditions. Their resilience against wear and tear translates to a longer operational lifespan, reducing the frequency of replacements.
Suitable for High-Pressure Applications:
These valves excel in high-pressure scenarios, where maintaining structural integrity is paramount. Hard seat check valves can handle significant pressure differentials without compromising performance. This capability makes them ideal for industries such as oil and gas, where pressures can exceed standard operating limits. Their robust design allows for reliable operation in demanding environments.
C. Disadvantages of Hard Seat Check Valves
Potential for Leakage in Low-Pressure Scenarios:
One of the main drawbacks of hard seat check valves is their potential for leakage at low pressures. The metal seal may not create an adequate barrier when fluid pressures are insufficient to keep the poppet firmly seated against the valve body. This characteristic can lead to fluid bypassing the valve, especially in systems that experience varying pressure conditions.
Higher Maintenance Needs:
While hard seat check valves are durable, they can require more maintenance compared to soft seat valves. Over time, wear on the metal seat can lead to decreased sealing effectiveness, necessitating regular inspections and potential refurbishments. Additionally, in applications where fluid contamination is a risk, the valve’s internal components may need frequent cleaning or replacement to maintain optimal performance.
D. Common Applications and Industry Usage
Hard seat check valves are widely utilized in various industries due to their unique advantages:
Oil and Gas: In exploration and production, hard seat check valves are critical for preventing backflow in pipelines and processing facilities. They are often found in high-pressure environments, ensuring safe fluid transport and operational efficiency.
Chemical Processing: These valves are commonly used in chemical plants where corrosive fluids are handled. Their ability to resist wear and contamination makes them suitable for maintaining the integrity of chemical processes.
Water and Wastewater Treatment: Hard seat check valves are employed in municipal water systems to prevent backflow and protect treatment equipment. Their durability ensures reliable operation in environments subject to variable flow and pressure conditions.
Power Generation: In power plants, hard seat check valves are essential for controlling fluid flow in cooling and hydraulic systems. They help maintain system stability and prevent unwanted backflow that could disrupt operations.
Mining and Mineral Processing: These valves are used to manage the flow of slurries and other abrasive materials. Their robust design allows them to handle the challenges presented by such environments effectively.
Soft Seat Check Valves
A. Definition and Design
Soft seat check valves are designed with a sealing mechanism that utilizes elastomeric or polymeric materials for the seat. Unlike hard seat check valves, which rely on metal-to-metal contact, soft seat valves feature seals made from materials such as rubber, nitrile, or other soft compounds. This design allows for a flexible and compressible interface between the valve’s poppet and seat, which enhances the sealing effectiveness.
The operation of a soft seat check valve is similar to that of a hard seat valve. The poppet opens under forward flow conditions, allowing fluid to pass through, and closes when back pressure is detected. The elastomeric seal compresses against the seat, creating a tight barrier that effectively prevents backflow. This design is particularly beneficial in applications where leakage prevention is critical.

B. Advantages of Soft Seat Check Valves
Enhanced Sealing Capabilities:
One of the primary advantages of soft seat check valves is their superior sealing performance. The elastomeric material conforms to the mating surfaces, creating a tighter seal than metal surfaces can achieve. This characteristic minimizes leakage, even under varying pressure conditions, making soft seat valves ideal for applications where backflow must be strictly prevented.
Better Performance in Cleanliness-Sensitive Applications:
Soft seat check valves are particularly well-suited for industries that require high levels of cleanliness, such as food and beverage processing, pharmaceuticals, and semiconductor manufacturing. The smooth surfaces of the elastomeric seals reduce the risk of fluid contamination, ensuring that the integrity of the fluid remains intact. Additionally, soft seat valves can be designed for easy cleaning and sanitization, further enhancing their suitability for hygienic applications.
C. Disadvantages of Soft Seat Check Valves
Limited Temperature and Pressure Ranges:
Soft seat check valves typically have more stringent operational limits regarding temperature and pressure compared to hard seat valves. The elastomeric materials used in their construction may degrade or lose their sealing properties when exposed to high temperatures or extreme pressures. Users must carefully evaluate the operational parameters of their applications to ensure that the selected soft seat valve is capable of performing reliably within those limits.
Vulnerability to Fluid Contamination:
While soft seat valves excel in cleanliness-sensitive environments, they are also susceptible to damage from certain fluids. For instance, aggressive chemicals or abrasive materials can degrade the elastomeric seals over time. This vulnerability necessitates a thorough assessment of the fluids being handled to prevent premature valve failure and ensure long-term operational reliability.
D. Common Applications and Industry Usage
Soft seat check valves find extensive use across various industries due to their unique advantages:
Food and Beverage: In processing and bottling applications, soft seat check valves are essential for maintaining hygiene and preventing contamination. Their enhanced sealing capabilities ensure that the quality of the product remains uncompromised.
Pharmaceuticals: Soft seat valves are commonly used in pharmaceutical manufacturing, where sterile conditions are paramount. They help maintain the integrity of sensitive compounds while preventing backflow that could introduce contaminants.
Water Treatment: In municipal water systems, soft seat check valves are employed to prevent backflow in systems handling treated water. Their effective sealing characteristics help maintain the quality of potable water.
HVAC Systems: Soft seat check valves are used in heating, ventilation, and air conditioning systems to manage fluid flow and maintain system efficiency. Their ability to prevent backflow contributes to improved energy efficiency.
Key Factors for Selection
A. Assessing Operational Requirements
Pressure and Temperature Conditions:
When selecting check valves, it’s crucial to assess the specific pressure and temperature conditions of the application. Each type of check valve, whether hard seat or soft seat, has defined operational limits that must be adhered to for optimal performance. Hard seat check valves are generally suitable for high-pressure environments, while soft seat valves are better for moderate-pressure applications. Understanding the maximum and minimum pressures and temperatures the valve will encounter ensures that the chosen valve can maintain its integrity and functionality under operational stress.
Fluid Characteristics (Viscosity, Corrosiveness):
The characteristics of the fluid being handled significantly influence valve selection. Viscosity impacts flow rates and the pressure drops across the valve, which can affect performance and sealing capabilities. For instance, highly viscous fluids may require valves with larger openings or specific design features to facilitate adequate flow. Additionally, the corrosiveness of the fluid should be evaluated, as it affects material compatibility. Soft seat valves may not withstand aggressive chemicals, whereas hard seat valves might be more appropriate in such environments. Consulting fluid compatibility charts and considering the specific properties of the fluids involved is essential in making informed selections.
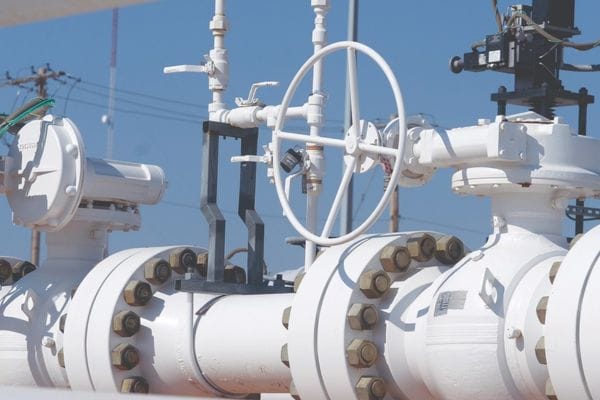
B. Evaluating Application Needs
Importance of Leakage Prevention:
In many applications, preventing leakage is a critical factor. Soft seat check valves excel in this regard due to their enhanced sealing capabilities, making them suitable for applications where even minimal leakage could lead to significant issues, such as contamination or loss of product quality. Conversely, if the application involves high pressures and the risk of leakage is less critical, hard seat valves may be the preferred option. Understanding the consequences of potential leakage in the specific application helps guide the selection process.
Frequency of Operation and Maintenance Considerations:
The operational frequency of the valve also plays a role in the selection process. For systems that require frequent cycling, the chosen valve should be capable of withstanding the wear associated with high cycle rates. Soft seat check valves may be preferable in applications that demand cleanliness and minimal leakage, but they may require more frequent inspections and replacements due to wear. In contrast, hard seat valves might be more durable but may necessitate more maintenance if they become worn over time. Evaluating the maintenance requirements alongside the operational demands ensures that the selected valve aligns with the overall system needs.
C. Comparing Lifecycle Costs and Maintenance Requirements
When selecting check valves, it’s vital to consider not just the initial purchase cost but the total lifecycle costs associated with each valve type.
Lifecycle Costs:
Lifecycle costs encompass the initial purchase price, installation expenses, operational costs, and maintenance or replacement costs over time. While hard seat check valves may have a higher upfront cost, their durability can result in lower maintenance expenses and a longer lifespan, making them cost-effective in the long run. Conversely, while soft seat check valves might be less expensive initially, their potential need for more frequent replacements and repairs could lead to higher overall costs.
Maintenance Requirements:
Different valve types come with varying maintenance needs. Hard seat valves might require regular inspections to ensure the integrity of the metal seat, while soft seat valves might need more frequent checks due to wear on the elastomeric seals. Understanding the maintenance protocols, potential downtimes for repairs, and the costs associated with maintaining each valve type is essential for making a financially sound decision.
Practical Considerations
A. Installation Guidelines for Both Valve Types
Proper installation is crucial for ensuring the effective operation of both hard seat and soft seat check valves. Here are key guidelines for each type:
Hard Seat Check Valves:
Orientation: Ensure that the valve is installed in the correct orientation, as indicated by flow direction arrows on the valve body. This ensures that the valve opens and closes appropriately with the intended flow.
Alignment: Maintain proper alignment with piping to prevent undue stress on the valve body, which can lead to leaks or failure.
Support: Provide adequate support for the valve and piping to reduce vibrations and mechanical stress.
Soft Seat Check Valves:
Avoid over-tightening: When installing soft seat valves, avoid over-tightening the connections, as excessive pressure can damage the elastomeric seal.
Debris Inspection: Before installation, inspect the valve and the connecting pipes for any debris or contaminants that could compromise sealing.
Temperature Considerations: Ensure that the installation environment does not exceed the temperature limits of the elastomeric material.
B. Maintenance Practices for Longevity
Routine maintenance is essential for both types of check valves to ensure longevity and reliable performance:
Hard Seat Check Valves:
Regular Inspections: Conduct regular visual inspections to identify any signs of leakage or corrosion around the valve body and connections.
Cleaning: Keep the valve clean and free from debris that could interfere with operation. Periodic cleaning may be necessary, especially in harsh environments.
Soft Seat Check Valves:
Seal Inspection: Regularly inspect the elastomeric seals for signs of wear, cracking, or degradation, as these can lead to leakage.
System Checks: Monitor the fluid flow and pressure to identify any changes that could indicate valve performance issues. Address any abnormalities promptly.
C. Signs of Wear or Failure to Watch For in Each Valve Type
Identifying signs of wear or failure early can prevent larger issues in the system:
Hard Seat Check Valves:
Leakage: Noticeable leakage around the valve body is a primary indicator of wear or failure. If leakage occurs even under normal operational pressures, the valve may need replacement.
Difficulty in Operation: If the valve becomes increasingly difficult to open or close, it may indicate internal wear or misalignment.
Soft Seat Check Valves:
Fluid Contamination: Any signs of contamination in the fluid could suggest that the elastomeric seal is compromised and fails to provide an adequate seal.
Inconsistent Performance: Fluctuations in flow rates or pressure drops may indicate seal degradation, leading to backflow issues.
Conclusion
As you consider your options for check valves, we encourage further research into the nuances of both hard seat and soft seat designs. Professional consultation can provide invaluable guidance, helping you navigate the complexities of valve selection and ensuring that your choices align with best practices in fluid management.
FAQ
What is the main difference between hard seat and soft seat check valves?
Hard seat check valves use metal-to-metal sealing, making them durable and suitable for high-pressure applications. Soft seat check valves feature elastomeric seals that provide better sealing performance and are ideal for cleanliness-sensitive environments.
When should I choose a hard seat check valve?
Opt for a hard seat check valve when your application requires high pressure, durability, and resistance to wear. They are also preferred in environments where fluid contamination is a concern.
What are the advantages of soft seat check valves?
Soft seat check valves offer enhanced sealing capabilities, minimizing leakage and providing better performance in systems requiring high cleanliness levels. They are often used in applications involving sensitive fluids.
How do I know which type of check valve to select for my application?
Assess factors such as pressure and temperature conditions, fluid characteristics, and the importance of leakage prevention. Evaluating these criteria will guide you in choosing the most suitable valve type.
What maintenance practices should I follow for check valves?
Regular inspections for leaks, cleaning to remove debris, and monitoring for signs of wear are essential maintenance practices. For soft seat valves, check seals frequently for degradation.
Are there any signs that indicate a check valve needs replacement?
Yes, signs include noticeable leakage around the valve, difficulty in operation, fluid contamination, and inconsistent flow rates. Addressing these issues promptly can prevent further complications in your system.