Annealed fittings are treated through a heat process that softens the material, improving flexibility and making it more resistant to cracking and stress. On the other hand, unannealed fittings maintain their natural hardness, making them more rigid and potentially less prone to deformation but also more prone to cracking under high stress or pressure.
What Does “Annealed” Mean in the Context of Hydraulic Fittings?
When we talk about “annealed” hydraulic fittings, we’re referring to the process used to treat the metal before it’s shaped into a fitting. Annealing involves heating the metal to a specific temperature and then allowing it to cool slowly, a process that alters the metal’s structure to improve its properties. In the context of hydraulic fittings, annealing helps ensure the material is more flexible, ductile, and resistant to stress, making it ideal for use in high-pressure fluid systems.
The Annealing Process: A Simple Explanation
Annealing is a heat treatment process that involves heating a metal—usually steel or copper alloys—up to a certain temperature and then allowing it to cool gradually. This slow cooling helps relieve internal stresses, soften the material, and improve its ability to be shaped or bent. During this process, the material’s grain structure is also altered, which leads to improved mechanical properties like increased toughness and reduced brittleness. For hydraulic fittings, this means that the metal becomes more malleable and less likely to crack or fail under pressure.
How Annealing Affects the Metal Structure
The primary effect of annealing is the transformation of the metal’s crystal structure. The heating and slow cooling process allows the metal’s molecules to reorganize into a more stable, uniform arrangement. This leads to a decrease in hardness but an increase in ductility and flexibility. For hydraulic fittings, these changes mean that the fittings are less prone to failure, especially in environments that involve fluctuating pressures and temperatures. The softer material can also better absorb stress, reducing the chances of cracks or leaks developing over time.
Benefits of Annealing for Hydraulic Fittings
The benefits of annealing for hydraulic fittings are significant, especially in high-pressure systems. Here are some of the key advantages:
Increased Flexibility: Annealed fittings are more malleable, making them easier to install and less likely to break under pressure or stress.
Improved Durability: The enhanced toughness from annealing helps hydraulic fittings withstand repeated cycles of pressure changes without failing.
Resistance to Cracking: The process reduces the brittleness of the material, preventing cracks that could lead to leaks or system failure.
Better Sealing Performance: The softer material creates better seals, reducing the risk of leaks in hydraulic systems and enhancing the overall efficiency of the system.
In summary, annealing not only improves the material properties of hydraulic fittings but also plays a crucial role in ensuring the longevity and reliability of hydraulic systems.
Annealed vs. Unannealed Hydraulic Fittings: A Side-by-Side Comparison
When choosing between annealed and unannealed hydraulic fittings, it’s essential to understand how each type of fitting performs in terms of material properties, durability, and cost.
Material Properties Comparison
Annealed Fittings: Annealing enhances the material’s flexibility, making it less prone to cracking under pressure or stress. The softening effect allows the metal to better absorb shocks and handle fluctuating pressures, improving its durability over time. However, while annealed fittings are more flexible, they are generally less strong than unannealed fittings when subjected to extreme conditions.
Unannealed Fittings: Unannealed fittings, by contrast, retain a higher level of hardness and strength due to the lack of heat treatment. While this makes them more rigid and resistant to deformation, it also makes them more brittle and susceptible to cracking under sudden pressure changes or heavy impacts. They’re often preferred in applications where strength is a critical factor, but their lack of flexibility can be a disadvantage in some hydraulic systems.
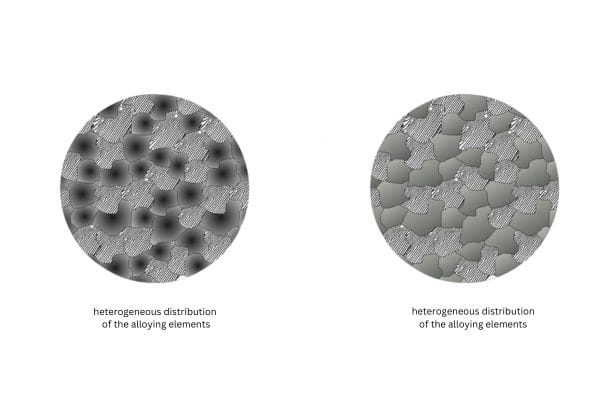
Performance in High-Pressure Environments
Annealed Fittings: Annealed fittings excel in environments where pressure and temperature fluctuate frequently. The flexibility and enhanced durability reduce the likelihood of failure, making them ideal for dynamic systems where the fittings need to absorb pressure changes. In high-pressure systems, the ability to bend slightly without cracking ensures a longer lifespan and fewer maintenance issues.
Unannealed Fittings: These fittings perform well in consistently high-pressure applications, where the demand for strength and resistance to deformation is paramount. However, due to their brittleness, they may not fare as well in systems where there are frequent pressure spikes or fluctuating temperatures. If not correctly handled, unannealed fittings can crack under sudden pressure changes, leading to leaks and system failure.
Resistance to Wear and Corrosion
Annealed Fittings: The softness of annealed fittings means they can wear out more quickly in abrasive environments, especially if exposed to rough handling or contaminants. However, their improved ductility allows them to handle small amounts of wear without failing. In terms of corrosion resistance, the treatment process does not directly affect corrosion but can improve the overall performance of seals, which helps reduce the risk of leaks and corrosion over time.
Unannealed Fittings: Due to their hardness, unannealed fittings are more resistant to wear and abrasion. The tough material can withstand physical stress better and maintain its structural integrity in harsh environments. When it comes to corrosion, however, both annealed and unannealed fittings made from similar materials will perform similarly unless they have additional coatings or corrosion-resistant treatments.
Cost Difference: Is It Worth the Investment?
Annealed Fittings: While annealed fittings tend to be slightly more expensive than their unannealed counterparts due to the additional heat treatment process, they often provide a better long-term value. Their flexibility, durability, and better sealing performance mean fewer replacements, less downtime, and lower maintenance costs over time. For systems where flexibility and stress resistance are critical, the investment in annealed fittings can be worthwhile.
Unannealed Fittings: Unannealed fittings are usually more affordable upfront because they don’t undergo the additional heating process. However, their rigidity and susceptibility to cracking under stress may result in higher maintenance costs in the long run, especially in systems that experience fluctuating pressures or temperatures. If your system is prone to high stresses or rough handling, investing in annealed fittings may ultimately save you more money by reducing the risk of failure.
How the Annealing Process Impacts Hydraulic Fittings
The annealing process plays a significant role in enhancing the performance and longevity of hydraulic fittings. Through controlled heat treatment, the metal is altered in ways that directly influence its properties, including flexibility, durability, and strength. Understanding how this process works will help you appreciate why annealed hydraulic fittings are often the preferred choice in demanding applications.
Heat Treatment Methods and How They Alter the Material
The annealing process begins with heating the metal—typically steel or copper alloys—up to a specific temperature, just below its melting point. Once heated, the metal is held at that temperature for a set period of time, allowing the molecules within the material to rearrange themselves. Afterward, the metal is cooled slowly, which helps prevent the formation of internal stresses that could lead to brittleness.
This heat treatment alters the material’s grain structure, transforming it from a hardened, brittle form to a more malleable, flexible one. This process not only softens the material but also enhances its overall stability, reducing the risk of cracking or failure under pressure. The result is a fitting that is better suited to handle dynamic, high-stress conditions common in hydraulic systems.
The Effect of Annealing on Ductility, Toughness, and Fatigue Resistance
Ductility: One of the most significant impacts of annealing is the increase in ductility. Annealed hydraulic fittings become more flexible and capable of withstanding deformation without breaking. This added ductility allows the fittings to better absorb forces and adjust to pressure changes, making them ideal for applications where there are fluctuating stresses or vibration.
Toughness: Annealing also improves the toughness of the material, meaning the hydraulic fitting can endure greater impacts or loads without cracking. This is particularly important in high-pressure systems where fittings are exposed to constant stress. Tougher fittings are less likely to fail, providing a longer service life and reducing the need for frequent replacements.
Fatigue Resistance: Fatigue resistance refers to the material’s ability to withstand repeated loading and unloading cycles without failing. Hydraulic systems often experience cyclical pressures, which can cause unannealed fittings to crack or fatigue more quickly. Annealed fittings, however, are much better equipped to handle these cycles thanks to the heat treatment process that helps the material resist fatigue and prolong its operational lifespan.
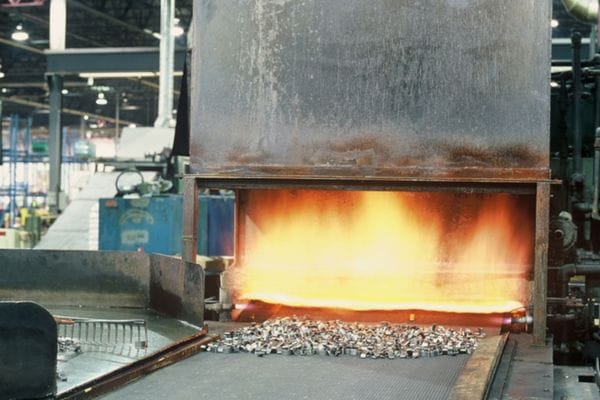
How the Annealing Process Enhances Sealing and Fitting Integrity
The annealing process not only impacts the structural integrity of hydraulic fittings but also enhances their sealing capabilities. The softer, more ductile nature of annealed fittings allows them to form more secure, tighter seals with hoses, pipes, and other components. This improved seal integrity is crucial in preventing leaks and ensuring that the hydraulic system operates at peak efficiency.
The improved material flexibility allows the fitting to better conform to irregularities in the sealing surfaces, creating a more uniform and effective seal. This reduces the chances of leaks, which can be costly and hazardous in fluid systems. Additionally, the annealed fitting’s enhanced toughness helps maintain its sealing integrity over time, even under extreme pressure or temperature fluctuations.
The Role of Material Selection in Hydraulic Systems
Material selection is one of the most critical decisions when designing or maintaining a hydraulic system. The materials used in hydraulic fittings directly influence the system’s performance, durability, and safety. Choosing the wrong material can lead to premature wear, system failures, or even catastrophic leaks. Let’s dive into why material choice matters and what factors to consider when selecting materials for hydraulic fittings.
Why the Choice of Material Affects Performance
The material selected for hydraulic fittings dictates how well they will perform under different conditions. Factors such as pressure, temperature, environmental exposure, and the type of fluids being transported all affect how the fitting material behaves. For example, softer materials may be better suited to environments with fluctuating pressures, while harder materials might be more appropriate for systems requiring resistance to abrasion and high mechanical stress.
The right material ensures that fittings maintain their structural integrity, prevent leaks, and offer reliable performance over the life of the system. Additionally, materials affect the ease of installation, maintenance requirements, and the fitting’s ability to withstand corrosive elements, extreme temperatures, or wear from constant motion.
The Most Common Materials Used in Hydraulic Fittings
Hydraulic fittings come in a variety of materials, each offering specific advantages depending on the application. The most common materials include:
Stainless Steel: Known for its excellent corrosion resistance, stainless steel is often used in hydraulic systems that deal with aggressive fluids or harsh environmental conditions. It also provides good strength, durability, and fatigue resistance, making it a reliable choice for high-pressure systems.
Carbon Steel: Carbon steel is widely used in hydraulic systems due to its strength and affordability. It performs well in environments that are not excessively corrosive and can withstand high-pressure conditions. However, it’s prone to rust and corrosion, which limits its use in harsher environments unless coated or treated.
Brass: Brass fittings are common in lower-pressure hydraulic systems. They offer excellent corrosion resistance and are relatively easy to machine, making them a good choice for precision applications. However, brass may not be suitable for high-pressure or high-temperature environments due to its lower strength compared to steel.
Aluminum: Aluminum fittings are lighter and resistant to corrosion, making them suitable for specific hydraulic systems where weight is a critical factor. However, aluminum has lower strength than steel, so it’s typically used in systems with moderate pressure levels and less demanding conditions.
Copper Alloys: Copper is often used in hydraulic systems that require resistance to both corrosion and high temperatures. It’s commonly found in applications like refrigeration or systems handling oils and chemicals. Copper alloys offer good thermal conductivity but may not be as durable as steel in high-pressure systems.
Material Properties to Consider for Different Hydraulic Applications
When selecting a material for hydraulic fittings, several properties must be taken into account to ensure the material is fit for the specific application:
Strength and Hardness: Fittings need to be strong enough to withstand the pressures of the hydraulic system without cracking, deforming, or breaking. For high-pressure systems, stronger materials like stainless steel or carbon steel are often necessary.
Corrosion Resistance: In many hydraulic applications, fittings are exposed to harsh chemicals, moisture, or extreme temperatures. Materials like stainless steel and brass are chosen for their excellent resistance to corrosion, reducing the risk of leaks and system failure.
Flexibility and Ductility: Some hydraulic systems require fittings that can handle minor shifts in pressure or position. Materials with high ductility, such as annealed steel, are better able to absorb stress and adjust to pressure fluctuations without cracking.
Fatigue Resistance: Hydraulic fittings are subject to repeated cycles of pressure changes, which can cause materials to fatigue over time. Materials that are tougher and more resilient to cyclic loading, such as annealed stainless steel, perform better in environments with high fatigue stress.
Temperature Tolerance: Hydraulic systems can operate in extreme temperatures, from freezing conditions to high heat. Selecting materials that can withstand these temperature fluctuations without losing strength or becoming brittle is crucial. Stainless steel and copper alloys are often preferred for their temperature resistance.
Annealed vs. Unannealed Materials in Real-World Scenarios
The choice between annealed and unannealed materials plays a significant role in how hydraulic fittings perform in specific scenarios:
Annealed Materials: Annealed fittings are ideal for systems where flexibility, toughness, and resistance to cracking are essential. They are often used in applications with fluctuating pressures, such as in construction machinery or agricultural equipment, where vibrations and pressure spikes are common. The enhanced ductility of annealed fittings also makes them suitable for environments where there may be a need to bend or adjust the fittings during installation.
Unannealed Materials: Unannealed fittings, with their higher strength and rigidity, are often chosen for applications where the fittings need to resist deformation under constant, high pressure. For instance, in heavy industrial machinery or high-pressure fluid transfer systems, unannealed fittings are used for their strength and ability to maintain integrity under high stress. However, the lack of flexibility means these fittings are more vulnerable to cracking in environments where pressure fluctuations occur regularly.
Can Unannealed Fittings Be Used in High-Pressure Hydraulic Systems?
Unannealed fittings, while often more affordable and rigid, present unique challenges when used in high-pressure hydraulic systems. Understanding these challenges and assessing the risks associated with their use is essential for ensuring system safety, reliability, and performance.
Examining the Risks and Challenges
While unannealed fittings are known for their strength and resistance to deformation, their use in high-pressure hydraulic systems is not without potential drawbacks:
Brittleness Under Stress: One of the main risks of using unannealed fittings is their brittleness. Unannealed materials, due to their hardened structure, are more prone to cracking under stress, particularly in high-pressure environments. Sudden pressure spikes, temperature fluctuations, or mechanical shocks could cause these fittings to fail prematurely, leading to leaks or system failure.
Risk of Fatigue Cracking: In high-pressure systems that experience repeated pressure cycles, unannealed fittings may be susceptible to fatigue cracking. Their lack of flexibility makes it harder for them to absorb the repetitive stresses, which can lead to microfractures over time. These fractures can expand, leading to leaks or complete fitting failure.
Sealing Issues: The rigidity of unannealed fittings also means that they may not conform as effectively to the sealing surfaces, potentially causing poor sealing and leaks. In high-pressure systems, even a small leak can compromise system performance, causing fluid loss and lowering system efficiency.
Difficulty in Handling Stress Variations: Hydraulic systems with fluctuating pressures—such as those that experience spikes, drops, or surges—place extra demands on fittings. Unannealed fittings are less able to absorb these variations, making them more likely to fail in systems where pressure is constantly changing.
Ideal Conditions for Using Unannealed Fittings
Despite the risks, there are scenarios where unannealed fittings may still be appropriate, especially if certain conditions are met. Here are the ideal situations where unannealed fittings could perform adequately:
Steady High-Pressure Environments: Unannealed fittings are best suited for hydraulic systems that operate under consistent, stable pressure. In these systems, the pressure doesn’t fluctuate frequently, reducing the likelihood of the material’s brittleness causing issues. If your system operates under relatively constant, predictable pressure, unannealed fittings could perform well.
Low-Vibration Systems: Unannealed fittings are less suited to systems that experience high levels of vibration, as this can exacerbate their brittleness. However, in systems where vibration is minimal and stress is constant, unannealed fittings may offer the necessary strength without compromising performance.
Systems Without Frequent Thermal Cycles: Unannealed fittings are more likely to fail under temperature fluctuations due to their lack of flexibility. Systems that operate within a narrow, controlled temperature range without significant temperature changes are more likely to see good performance from unannealed fittings.
Conclusion
Ultimately, choosing the right hydraulic fittings isn’t just about price, it’s about performance, longevity, and ensuring that your hydraulic system operates at peak efficiency. If you would like to find out if Topa offers annealed hydraulic fittings, contact us with your requirements.
FAQ
What is the difference between annealed and unannealed hydraulic fittings?
Annealed hydraulic fittings undergo a heat treatment process that makes them more flexible, durable, and resistant to cracking. Unannealed fittings, on the other hand, are harder and stronger but more brittle, making them less suited to systems with fluctuating pressures or temperature variations.
Are annealed fittings better for high-pressure systems?
Yes, annealed fittings are generally better for high-pressure systems that experience fluctuating pressure, temperature changes, or vibrations. Their flexibility and improved toughness help them withstand these conditions without cracking or failing.
Can unannealed fittings be used in hydraulic systems?
Yes, unannealed fittings can be used in hydraulic systems, especially those that operate under steady, high-pressure conditions. However, they are more prone to cracking and fatigue under fluctuating pressures or temperature changes.
What are the advantages of annealing hydraulic fittings?
Annealing improves the ductility, toughness, and fatigue resistance of hydraulic fittings. It reduces the risk of cracking under stress and enhances the fitting’s ability to absorb pressure changes, making it ideal for dynamic systems.
Are annealed fittings more expensive than unannealed ones?
Yes, annealed fittings are generally more expensive because of the heat treatment process. However, their increased durability and resistance to failure may result in lower long-term maintenance and replacement costs.
How do I know if I need annealed or unannealed fittings?
If your hydraulic system experiences frequent pressure changes, temperature fluctuations, or requires high flexibility, annealed fittings are usually the better choice. For systems with stable pressure and minimal temperature variation, unannealed fittings may be sufficient.