Pressure Washer Hose Fitting Types: A Comprehensive Guide
Introduction
Choosing the right hose fittings is crucial for ensuring optimal performance of your pressure washer. They not only influence the efficiency and effectiveness of your pressure washing tasks but also impact the safety and longevity of your equipment. Missteps in selecting the appropriate fittings can lead to leaks, bursts, and even equipment damage, potentially causing costly repairs and downtime. This comprehensive guide aims to cover everything you need to know about pressure washer hose fitting types.
What are Pressure Washer Hose Fittings?
Pressure washer hose fittings are essential components that connect the various parts of a pressure washer system, including hoses, guns, nozzles, and other accessories. These fittings ensure a secure and leak-proof connection, allowing water to flow at high pressure without interruption. They come in various shapes, sizes, and types to accommodate different hose diameters and pressure requirements. Their primary function is to maintain the integrity of the pressure washer system by providing a robust and reliable link between components.
Common Materials Used
Pressure washer hose fittings are typically made from materials that offer durability and resistance to corrosion and wear. The most common materials used are:
Stainless Steel
Stainless steel fittings are known for their exceptional resistance to corrosion and rust, making them ideal for environments where exposure to moisture and chemicals is common. These fittings are extremely durable and can withstand high pressures and temperatures, ensuring they maintain their integrity under demanding conditions. This makes stainless steel a preferred choice for industrial and commercial applications where reliability is crucial. However, stainless steel fittings are generally more expensive than those made from other materials.
Brass
Brass fittings strike a balance between durability and cost, making them a popular choice for many pressure washer systems. They are corrosion-resistant and offer good strength, which makes them suitable for medium to high-pressure applications. Brass fittings are relatively inexpensive compared to stainless steel, providing a cost-effective solution without sacrificing much in terms of performance.
Types of Pressure Washer Hose Fittings
Pressure washer hose fittings come in various types, each designed to meet specific needs and applications. Understanding the differences between these fittings is essential for selecting the right one for your pressure washer system. Here, we will explore the most common types of pressure washer hose fittings available on the market.
Quick Connect Fittings
Quick connect fittings are popular for their ease of use and convenience. These fittings allow users to quickly attach and detach hoses and accessories without the need for tools. Quick connect fittings typically consist of a plug and a socket. The plug inserts into the socket, and a simple push-and-click mechanism secures the connection. This type of fitting is ideal for those who frequently change attachments, such as different spray nozzles or extension wands. Quick connect fittings are available in various sizes and materials, including stainless steel, brass, and plastic, making them versatile and suitable for a range of pressure washer models and applications.
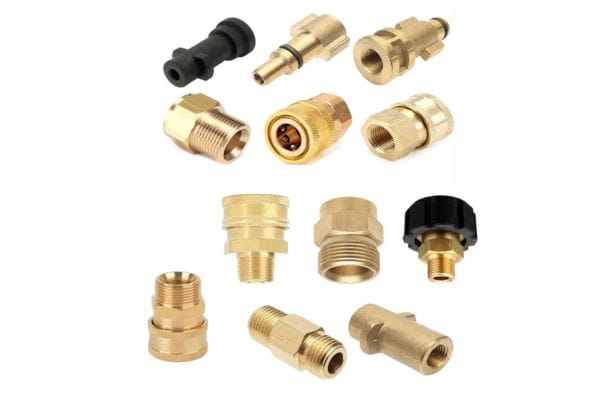
Threaded Fittings
Threaded fittings, also known as screw fittings, are another common type of pressure washer hose fitting. These fittings use a threaded mechanism to create a secure connection. The two main types of threaded fittings are National Pipe Thread (NPT) and British Standard Pipe (BSP). NPT fittings are standard in the United States, while BSP fittings are commonly used in Europe and other parts of the world. Threaded fittings are known for their reliability and ability to withstand high pressures, making them suitable for both residential and commercial applications. However, they require more effort to connect and disconnect compared to quick connect fittings, often needing tools like wrenches to ensure a tight seal.
Twist Connect Fittings
Twist connect fittings combine elements of both quick connect and threaded fittings. They feature a twist-and-lock mechanism that allows for secure connections without the need for tools. Users simply twist the fitting to lock it in place, providing a quick and easy way to connect hoses and accessories. Twist connect fittings are designed to prevent accidental disconnections, ensuring a reliable connection during use. These fittings are commonly used in medium to high-pressure applications and are available in various materials to suit different needs.
Snap Coupler Fittings
Snap coupler fittings are designed for ease of use and secure connections. These fittings use a snap-on mechanism, similar to quick connect fittings, but with added security features to prevent accidental disconnections. Snap couplers are often used in high-pressure applications where a reliable connection is critical. They are available in different sizes and materials, including stainless steel and brass, making them suitable for various pressure washer systems. Snap coupler fittings are favored for their durability and ease of use, particularly in professional and industrial settings.
Bayonet Fittings
Bayonet fittings are less common but still an important type of pressure washer hose fitting. These fittings use a bayonet-style locking mechanism, similar to those found on camera lenses. The fitting is inserted and then twisted to lock it in place. Bayonet fittings provide a secure connection that is easy to engage and disengage, making them suitable for various pressure washer applications. They are often used in residential and light commercial settings where quick and secure connections are needed.
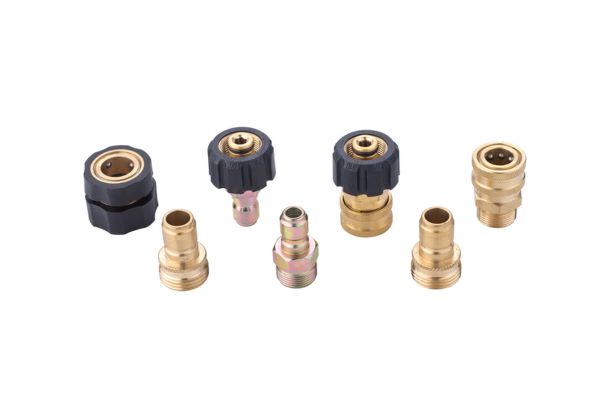
M22 Fittings
M22 fittings are a specific type of threaded fitting commonly used in pressure washers. They have a 22mm diameter and are often found on consumer-grade pressure washers and accessories. M22 fittings are known for their reliability and ease of use, providing a secure connection for hoses and attachments. They are typically made from brass or plastic and are suitable for a range of pressure washer applications.
Specific Applications and Compatibility
Choosing the right pressure washer hose fittings depends significantly on the specific application and compatibility with your equipment. Different settings, such as residential and commercial use, as well as varying pressure requirements, necessitate the use of different fitting types to ensure optimal performance and safety.
Residential vs Commercial Use
The requirements for pressure washer hose fittings differ considerably between residential and commercial applications. Residential pressure washers are typically designed for lighter-duty tasks, such as cleaning patios, vehicles, and home exteriors. These washers usually operate at lower pressures and flow rates compared to commercial units. Consequently, the fittings used in residential systems are often made from materials like plastic or brass, which are sufficient for lower pressure and less frequent use.
High-Pressure Applications
High-pressure applications require fittings that can safely handle elevated PSI (pounds per square inch) ratings without compromising performance or safety. Fittings suitable for high-pressure applications are typically made from strong, durable materials such as stainless steel or high-grade brass. These materials can withstand intense pressure and reduce the risk of leaks or bursts. Quick-connect fittings made from stainless steel are often used in high-pressure settings because they provide a secure, leak-proof connection that can be easily and quickly changed as needed.
Low-Pressure Applications
Low-pressure applications, such as light cleaning tasks, garden irrigation, or washing delicate surfaces, require fittings that are easy to handle and install, without the need for the heavy-duty durability required by high-pressure systems. Plastic and brass fittings are commonly used in low-pressure applications due to their sufficient strength for lower PSI ratings and their cost-effectiveness.
How to Choose the Right Pressure Washer Fitting
Selecting the right pressure washer hose fittings is essential for ensuring the efficiency, safety, and longevity of your pressure washer system. Here, we will guide you through the process of choosing the best fittings for your needs by assessing various factors, ensuring compatibility with your equipment, and considering future-proofing your setup.
Assessing Your Needs
When choosing pressure washer fittings, it’s crucial to consider several factors to ensure they meet your specific requirements:
Pressure Rating: The PSI rating of your pressure washer is one of the most critical factors. Ensure that the fittings you choose are rated to handle the maximum pressure your washer can produce. Using fittings with a lower PSI rating than required can lead to failures and safety hazards.
Material: The material of the fittings should match the demands of your application. For high-pressure and commercial use, stainless steel fittings are ideal due to their durability and resistance to corrosion. Brass fittings are suitable for medium to high-pressure applications and offer a good balance of durability and cost. For low-pressure and residential use, plastic fittings are often sufficient and more cost-effective.
Size: Fittings come in various sizes, and it’s essential to select the correct size to ensure a secure and leak-proof connection. Common sizes include 1/4″, 3/8″, and 1/2″ fittings. Check your pressure washer and accessories to determine the appropriate size.
Type of Fitting: Consider the type of fitting that best suits your needs. Quick-connect fittings are convenient for frequent changes, while threaded fittings offer a secure connection for high-pressure applications. Push-lock fittings are easy to install for low-pressure tasks, and swivel fittings provide maneuverability to prevent hose kinks.
Matching Fittings to Equipment
Ensuring compatibility between your fittings and pressure washer equipment is crucial for seamless operation:
Hoses: Verify the diameter and threading of your hoses to match them with the appropriate fittings. For example, if your hose has a 3/8″ diameter with NPT threading, choose fittings that correspond to these specifications.
Guns and Wands: Check the connections on your pressure washer gun and wand to ensure they are compatible with the fittings you plan to use. Quick connect fittings are often used for ease of attachment and detachment.
Nozzles and Accessories: Ensure that the fittings are compatible with various nozzles and other accessories you may use. This includes checking for the correct threading and connection types to avoid leaks and ensure a secure fit.
Adapters: In some cases, you may need adapters to bridge different types or sizes of fittings. Ensure that any adapters used are rated for the pressure and application requirements.
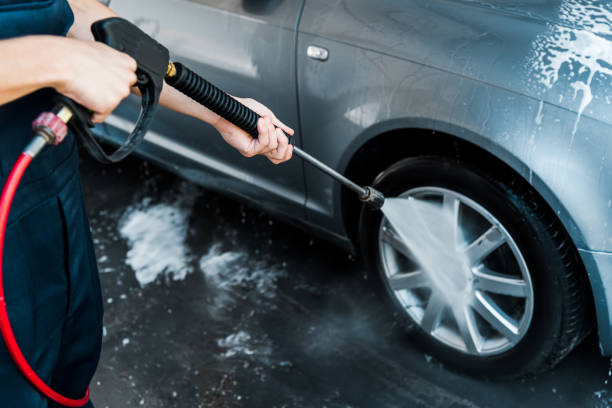
Future-Proofing Your Setup
Choosing versatile fittings can help future-proof your pressure washer setup, allowing for adaptability and longevity:
Universal Fittings: Opt for fittings that are compatible with a wide range of equipment and accessories. Universal fittings provide flexibility and make it easier to switch out components as needed without compatibility issues.
Durable Materials: Invest in high-quality fittings made from durable materials such as stainless steel or high-grade brass. These materials are more resistant to wear and corrosion, ensuring a longer lifespan and reducing the need for frequent replacements.
Standard Sizes and Types: Stick to standard sizes and types of fittings, such as NPT or quick connect, which are widely used and readily available. This makes it easier to find replacement parts and accessories in the future.
Expandable Systems: Consider the potential for expanding your pressure washer system. Choose fittings that can accommodate additional hoses, guns, and accessories as your needs grow. Swivel fittings, for example, can enhance maneuverability, making it easier to use longer hoses without tangling.
Installation and Maintenance Tips
Proper installation and maintenance of pressure washer hose fittings are crucial for ensuring optimal performance, safety, and longevity. This section provides step-by-step instructions for installing various fitting types, best practices for maintenance, and tips for troubleshooting common fitting-related issues.
Installation Guidelines
Installing pressure washer hose fittings correctly is essential to prevent leaks and ensure a secure connection. Here are step-by-step instructions for installing the most common fitting types:
Quick Connect Fittings:
Step 1: Ensure both the plug and socket are clean and free of debris.
Step 2: Pull back the collar on the socket.
Step 3: Insert the plug into the socket.
Step 4: Release the collar to lock the plug in place. Tug gently to ensure it is securely connected.
Threaded Fittings (NPT/BSP):
Step 1: Apply Teflon tape or pipe thread sealant to the male threads. Wrap the tape in the direction of the threads to prevent it from unraveling.
Step 2: Insert the male fitting into the female fitting.
Step 3: Hand-tighten the connection.
Step 4: Use a wrench to tighten the fitting further, taking care not to over-tighten and strip the threads.
Twist Connect Fittings:
Step 1: Align the fitting with the connection point.
Step 2: Insert the fitting and twist it to lock it in place.
Step 3: Ensure it is securely connected by giving it a gentle tug.
Troubleshooting Common Issues
Identifying and resolving fitting-related problems quickly can save time and prevent damage to your pressure washer system. Here are some common issues and how to address them:
Leaks at the Connection:
Cause: Loose fitting, worn threads, or damaged O-rings.
Solution: Tighten the fitting securely. If the threads are worn, apply Teflon tape or replace the fitting. Replace damaged O-rings.
Difficulty Connecting or Disconnecting Fittings:
Cause: Debris in the fitting, worn components, or lack of lubrication.
Solution: Clean the fitting thoroughly. Lubricate metal fittings. Replace worn components.
Reduced Water Pressure:
Cause: Blocked fitting, kinked hose, or incorrect fitting size.
Solution: Clean the fitting to remove blockages. Ensure the hose is not kinked. Verify the fitting size is appropriate for your pressure washer system.
Fittings Coming Loose During Use:
Cause: Improper installation, incompatible fittings, or damaged threads.
Solution: Reinstall the fitting correctly, ensuring a secure connection. Check compatibility and replace incompatible fittings. Replace fittings with damaged threads.
Conclusion
In this comprehensive guide, we’ve explored the various types of pressure washer hose fittings, their specific applications, and the importance of choosing the right materials and sizes. We also provided detailed instructions for installation and maintenance, ensuring your fittings remain in top condition for optimal performance and safety. Remember, selecting the appropriate fittings for your pressure washer not only enhances efficiency but also ensures safe and reliable operation.
FAQ
The most common types include quick connect fittings, threaded fittings (NPT/BSP), twist connect fittings, snap coupler fittings, push-lock fittings, and bayonet fittings.
Check the diameter and threading specifications of your pressure washer hoses and accessories. Common sizes are 1/4″, 3/8″, and 1/2″.
No, plastic fittings are generally suitable for low-pressure applications. For high-pressure applications, stainless steel or brass fittings are recommended due to their durability and ability to withstand high pressures.
Ensure fittings are properly installed and tightened. Use Teflon tape or pipe thread sealant on threaded fittings, and regularly inspect and replace worn or damaged O-rings and fittings.
Regularly inspect fittings for wear and damage, clean them to remove debris, apply a light lubricant to metal fittings, store them in a dry place, and replace worn or damaged fittings promptly.
Matching fittings to your equipment ensures a secure, leak-proof connection, maintains optimal water pressure, and prevents damage to both the fittings and the pressure washer system.