Five Advantages of Quick Connect Fittings
Table of Contents
Introduction
Quick couplings have made a significant impact on a wide range of industries with their innovative design and functionality, and are specialized connectors designed for quick and easy connections and disconnections. These fittings are used in a variety of fluid and air delivery systems to make quick connections without the need for tools or extensive labor. This article will detail five key benefits of quick-connect couplings: time savings, cost savings, increased safety, application versatility, durability, and reliability, which help improve performance and productivity in a variety of industrial applications.
Ease of Use
Simplified Installation
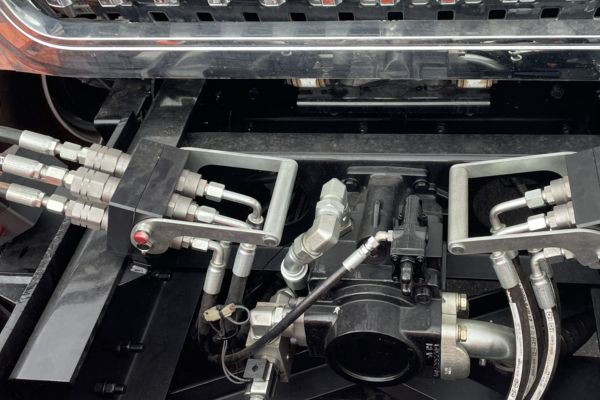
Quick connect fittings are designed with a plug-and-play mechanism that allows for rapid connection and disconnection without the need for extensive preparation or alignment. This intuitive design ensures that even users with minimal technical expertise can efficiently manage hydraulic systems. The fitting typically consists of two components: the male and female parts, which simply snap together, creating a secure and leak-proof connection.
Steps Illustrating How Easy It Is to Install These Fittings Compared to Traditional Methods:
Preparation:
Quick Connect Fittings: Clean the connecting surfaces and ensure that the fittings are the correct size for the hoses or pipes being used.
Traditional Fittings: Clean the connecting surfaces, gather necessary tools (wrenches, tape, sealant), and check the compatibility of threads or flanges.
Connection:
Quick Connect Fittings: Align the male and female components and push them together until you hear a click, indicating a secure connection.
Traditional Fittings: Align the components, apply sealant or tape to the threads, and use wrenches to tighten the connection securely.
Verification:
Quick Connect Fittings: Conduct a quick visual inspection to ensure the components are properly seated.
Traditional Fittings: Check for leaks by running the system and making any necessary adjustments with wrenches.
Adjustment:
Quick Connect Fittings: Easily disconnect and reconnect if adjustments are needed.
Traditional Fittings: Use tools to loosen, adjust, and retighten connections, which can be time-consuming.
The streamlined process for quick connect fittings highlights their efficiency and user-friendly nature, reducing installation time significantly compared to traditional methods.
Tool-Free Operation
One of the standout features of quick-connect fittings is their ability to be installed and removed without the need for special tools. This is achieved through a design that incorporates locking mechanisms such as push-to-connect or twist-and-lock, which eliminate the need for wrenches, pliers, or other tools typically required for traditional fittings. The absence of tools not only speeds up the installation process but also reduces the potential for incorrect tightening or damage to the fittings.
Examples of Scenarios Where Tool-Free Operation Is Beneficial:
Field Repairs and Maintenance:
In remote locations where carrying a full set of tools may be impractical, quick-connect fittings allow for fast and efficient repairs. For instance, agricultural machinery operating in the field can be quickly serviced without the need for transporting the equipment back to a workshop.
Emergency Situations:
In industrial settings, unexpected leaks or system failures require immediate attention. Quick connect fittings enable rapid response, minimizing downtime and potential damage. Maintenance crews can swiftly replace or repair components without scrambling for the right tools.
Frequent System Changes:
Industries that require frequent reconfiguration of their hydraulic systems, such as testing facilities or manufacturing plants with flexible production lines, benefit immensely from tool-free quick-connect fittings. The ease of connecting and disconnecting components supports agile operations and reduces setup times between different processes.
Time Efficiency
Faster Assembly and Disassembly
Quick connect fittings are engineered for speed, allowing for rapid connections and disconnections. Traditional fittings, such as threaded or flanged connections, often require precise alignment, sealing, and tightening using various tools, which can be time-consuming. In contrast, quick connect fittings typically involve a simple push or twist motion to secure the connection.
Reduced Downtime
Impact on Overall System Downtime During Maintenance and Repairs:
System downtime can be costly, impacting productivity and leading to revenue loss. Quick connect fittings minimize downtime by enabling faster maintenance and repairs. Traditional fittings often require shutting down the entire system, draining fluids, and using specialized tools to disassemble components, which can lead to extended periods of inactivity.
Downtime Comparison:
Quick Connect Fittings:
Maintenance: Minimal downtime due to quick disconnection and reconnection
Repairs: Rapid replacement of faulty components without the need for extensive system shutdowns
Traditional Fittings:
Maintenance: Extended downtime due to lengthy disassembly and reassembly processes
Repairs: Longer repair times due to the need for draining systems and using specialized tools
Enhanced Safety
Minimized Risk of Leaks
Quick connect fittings are specifically designed to create a secure and leak-proof seal. The engineering behind these fittings focuses on precision and reliability, ensuring that once connected, the fitting maintains a robust seal under various conditions. Key features that help minimize leaks include:
Precision Machining: Quick connect fittings are manufactured with tight tolerances, ensuring a perfect fit between the male and female components. This precision reduces the risk of gaps or misalignments that can cause leaks.
O-Ring Seals: Many quick connect fittings incorporate O-ring seals that compress upon connection, creating a watertight barrier. These seals are often made from materials resistant to the fluids being transported, further reducing the risk of leaks.
Self-Sealing Mechanisms: Some quick connect fittings feature self-sealing valves that automatically close when disconnected, preventing fluid loss and contamination. This mechanism ensures that even during disconnection, there is minimal leakage.
Safety Mechanisms Integrated into Quick Connect Fittings:
Locking Mechanisms: Quick connect fittings often include locking features such as clips, rings, or levers that secure the connection. These locks prevent accidental disconnection, which could otherwise lead to sudden leaks or spills.
Pressure Relief Valves: In high-pressure systems, quick connect fittings may have integrated pressure relief valves that release excess pressure safely, reducing the risk of burst connections.
Color-Coding and Markings: To prevent mismatched connections, quick connect fittings can be color-coded or marked with specific identifiers, ensuring that only compatible parts are connected.
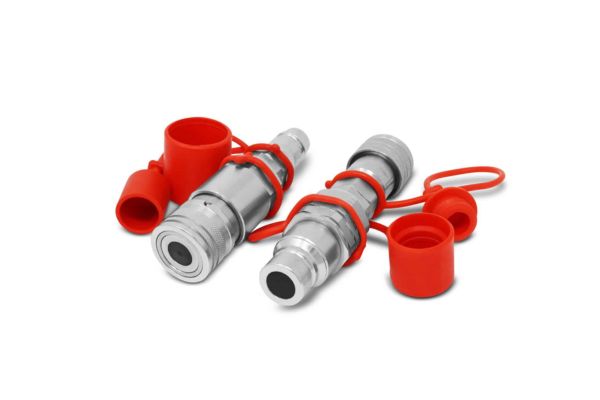
Improved Workplace Safety
Reduced Risk of Slips and Falls:
Leak Prevention: By minimizing leaks, quick connect fittings help prevent fluid spills on the floor, which can be a major cause of slips and falls in industrial environments. A dry, clean workspace is inherently safer for all employees.
Lower Exposure to Hazardous Fluids:
Sealed Connections: Quick connect fittings ensure that fluids remain contained within the system. This reduces the risk of workers coming into contact with hazardous substances, which can cause skin irritation, respiratory issues, or other health problems.
Decreased Risk of Equipment Damage:
Reliable Connections: The secure connections provided by quick connect fittings reduce the likelihood of hydraulic fluid leaks that can damage equipment. This leads to fewer instances of machinery failure and associated hazards, such as fires or mechanical breakdowns.
Enhanced Emergency Response:
Rapid Disconnection: In emergency situations, such as a system malfunction or fire, the ability to quickly disconnect hydraulic lines can be crucial. Quick connect fittings allow for fast and safe disconnections, enabling prompt response to emergencies.
Versatility
Compatibility with Various Systems
Quick connect fittings are designed to be versatile and adaptable, making them suitable for a wide range of systems and applications across various industries. These fittings can be used in hydraulic, pneumatic, and fluid transfer systems, among others. Their design allows them to be easily integrated into existing setups or new installations, providing a seamless connection solution.
Specific Examples of Industries and Use Cases:
Automotive Industry:
Applications: Fuel lines, brake systems, coolant systems
Example: Quick connect fittings are used in automotive manufacturing for rapid assembly of fuel lines, ensuring a secure and leak-proof connection that can withstand the pressures and vibrations of vehicle operation.
Manufacturing Industry:
Applications: Assembly lines, robotic arms, hydraulic presses
Example: In manufacturing plants, quick connect fittings facilitate the quick changeover of hydraulic tools and equipment, reducing downtime and increasing production efficiency.
Agriculture:
Applications: Irrigation systems, tractor hydraulics, sprayer equipment
Example: Farmers use quick connect fittings in irrigation systems to easily connect and disconnect hoses, allowing for efficient management of water distribution and equipment maintenance.
Adaptability to Different Fluids
Quick connect fittings are designed to be highly adaptable, capable of handling a wide variety of fluids. The materials and seals used in these fittings are chosen based on their compatibility with different types of fluids, ensuring that they maintain a secure and leak-proof connection regardless of the fluid type.
Oils:
Materials: Typically made from metals like stainless steel or brass, which are resistant to oil corrosion and high pressures.
Seals: O-rings made from materials such as Viton or Buna-N, which are resistant to oil swelling and degradation.
Benefits: Provides reliable connections in hydraulic systems and lubrication lines, ensuring consistent performance.
Gases:
Materials: Often made from metals or high-strength plastics that can withstand high pressures and prevent gas permeation.
Seals: Specially designed O-rings and gaskets that ensure a tight seal to prevent gas leaks.
Benefits: Essential for applications such as gas delivery systems in medical and industrial settings, where preventing leaks is critical for safety and efficiency.
Water:
Materials: Corrosion-resistant materials like stainless steel or plastics that are safe for potable water use.
Seals: EPDM or silicone O-rings that are resistant to water and provide a long-lasting seal.
Benefits: Used in irrigation, cooling systems, and food and beverage applications, where cleanliness and durability are key.
Cost Efficiency
Reduced Labor Costs
Quick connect fittings are designed to simplify and expedite the process of connecting and disconnecting components within hydraulic systems. This streamlined approach translates directly into reduced labor costs in several ways:
Installation Time:
Traditional Fittings: These require multiple steps, including aligning components, applying sealants, and using tools to tighten connections. This process can be time-consuming and labor-intensive.
Quick Connect Fittings: Offer a plug-and-play mechanism that significantly reduces the time required for installation. The simple push or twist motion to secure connections can be completed in seconds, allowing workers to move on to other tasks more quickly.
Maintenance and Repairs:
Traditional Fittings: Maintenance often involves draining systems, disassembling components, and using specialized tools, which can extend downtime and require more labor hours.
Quick Connect Fittings: Allow for rapid disconnection and reconnection, enabling faster repairs and maintenance. This reduces the amount of time systems are offline and minimizes labor costs associated with extended downtime.
Long-Term Savings
Quick connect fittings are designed with materials and engineering standards that ensure long-term reliability and durability. These fittings often outperform traditional fittings in terms of longevity, which contributes to substantial long-term savings.
Material Quality:
Quick Connect Fittings: Typically made from high-quality materials such as stainless steel, brass, or high-strength plastics, which are resistant to corrosion, wear, and environmental factors.
Traditional Fittings: While also made from durable materials, the frequent need for sealants and tools can lead to wear and potential damage over time.
Durability:
Quick Connect Fittings: Engineered to withstand repeated connections and disconnections without compromising the integrity of the seal. The robust design ensures that the fittings remain leak-proof and secure over many cycles.
Traditional Fittings: Subject to wear and tear from repeated tightening and loosening, which can lead to thread damage, leaks, and the need for replacements.
In conclusion, while quick-connect fittings may have a higher initial cost, the long-term savings in maintenance, replacement, and labor costs make them a more cost-effective solution. Their durability and ease of use contribute to significant financial benefits over the lifespan of the fittings, ensuring that businesses can operate more efficiently and economically.
Conclusion
In summary, quick connect fittings offer significant advantages, including ease of use, time efficiency, enhanced safety, versatility, and cost efficiency. These fittings simplify installation and maintenance, reduce downtime, improve workplace safety, adapt to various systems and fluids, and provide long-term financial benefits. Choosing the right fittings is crucial for optimizing hydraulic system performance.
FAQ
Quick connect fittings are components designed to easily connect and disconnect fluid lines without the need for tools, ensuring a secure and leak-proof connection.
Quick connect fittings simplify the installation process with a plug-and-play mechanism, significantly reducing the time required compared to traditional fittings that need tools and alignment.
Yes, quick connect fittings incorporate safety mechanisms like locking features and self-sealing valves to prevent leaks and ensure secure connections, enhancing overall workplace safety.
Yes, quick connect fittings are versatile and can handle various fluids, including oils, gases, and water, making them suitable for a wide range of applications.
Industries such as automotive, manufacturing, agriculture, medical, aerospace, and food and beverage benefit from the efficiency and reliability of quick connect fittings.
Yes, despite a higher initial cost, quick connect fittings offer long-term savings through reduced maintenance, lower labor costs, and increased durability, making them a cost-effective solution over time.
Contact Topa
Have a question or suggestion? Fill out the form below to get in touch with one of our experts.