How to Install Hydraulic Flange Hose Fittings
Table of Contents
Introduction
Incorrectly installed fittings can lead to significant issues, including fluid leaks, pressure drops, and even complete system failures. These problems not only reduce the efficiency of the hydraulic system but can also lead to costly repairs and downtime. In extreme cases, improper installation may pose serious safety hazards to operators and equipment. Therefore, understanding the correct procedures for installing hydraulic flange hose fittings is essential for maintaining system integrity and ensuring safe and efficient operations.
Understanding Hydraulic Flange Hose Fittings
Components of a Hydraulic Flange Hose Fitting
Hydraulic flange hose fittings are composed of several key components, each playing a crucial role in ensuring a secure and leak-proof connection. The primary component is the flange head, which is typically a flat, circular piece of metal with holes around its perimeter. These holes accommodate bolts that secure the flange head to the corresponding flange on the equipment. The hose is connected to the flange head, providing the pathway for hydraulic fluid. To ensure a tight seal, an O-ring is placed between the flange head and the equipment’s flange surface, preventing fluid leaks. Finally, bolts and nuts are used to fasten the assembly together. The bolts pass through the holes in the flange head and are secured with nuts, which are tightened to the appropriate torque to ensure a strong and reliable connection.
Types of Hydraulic Flange Hose Fittings
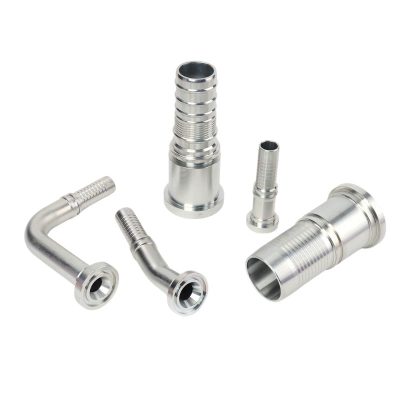
Hydraulic flange hose fittings come in various types, with the most common being Code 61 and Code 62 flanges. Code 61 flanges are designed for medium-pressure applications, typically up to 3,000 PSI, while Code 62 flanges are used in high-pressure systems, handling pressures up to 6,000 PSI. The choice between these two types depends on the specific requirements of the hydraulic system, such as the operating pressure and fluid type.
In addition to pressure ratings, hydraulic flange hose fittings are available in different sizes to accommodate various hose diameters and equipment specifications. The materials used for these fittings can also vary, with options including steel, stainless steel, and aluminum. Steel fittings are known for their strength and durability, making them ideal for heavy-duty applications. Stainless steel fittings offer excellent corrosion resistance, making them suitable for use in harsh environments or with corrosive fluids. Aluminum fittings are lightweight and offer good resistance to corrosion, making them a popular choice for applications where weight is a critical factor.
Applications of Hydraulic Flange Hose Fittings
Hydraulic flange hose fittings are widely used across various industries due to their robust design and reliable performance. Common industries that rely on these fittings include construction, manufacturing, oil and gas, agriculture, and heavy machinery. In these industries, hydraulic systems are often subjected to high pressures and demanding conditions, making the secure and leak-proof connections provided by flange fittings essential.
The benefits of using flange fittings over threaded or welded connections are significant. Flange fittings offer a more stable connection, reducing the risk of leaks and pressure drops. Unlike threaded fittings, which can loosen over time due to vibration or temperature changes, flange fittings remain secure even in challenging conditions. Additionally, flange fittings are easier to install and maintain compared to welded connections, which require specialized equipment and skills. This ease of installation and maintenance makes flange fittings a cost-effective solution for many hydraulic applications, particularly in systems where regular maintenance or component replacement is necessary.
Step-by-Step Installation Guide
Inspecting the Components
Before you begin the installation process, a thorough inspection of all components involved in the hydraulic flange hose fitting is crucial. This step ensures that each part is in optimal condition and ready for assembly. Here’s how to perform this inspection in detail:
Examine the Flange:
Visual Inspection: Start by closely inspecting the flange for any visible damage. Look for cracks, dents, warping, or any other deformities. A perfectly flat flange is essential to create a proper seal, so even minor imperfections can cause significant issues later on.
Surface Condition: Run your fingers along the flange surface to detect any irregularities that may not be visible to the naked eye. The flange surface should be smooth and free from any scratches or nicks that could compromise the seal.
Check the Hose:
Surface Integrity: Unroll the hose and examine it for any cuts, abrasions, or kinks. The hose should be flexible and free from any visible damage. A compromised hose can lead to leaks or failures in the hydraulic system.
Flexibility Test: Gently bend the hose along its length to ensure it retains its flexibility. Stiff or excessively worn hoses may not function properly under pressure.
Inspect the Sealing Surfaces:
O-Ring Groove: Carefully inspect the groove where the O-ring will sit. This area must be clean, smooth, and free from any debris or contamination. Even a small particle can prevent the O-ring from sealing correctly, leading to potential leaks.
Flange Face: Similarly, check the flange face where it will meet the mating surface. Ensure that there is no dirt, rust, or other contaminants present. Clean the surface with a lint-free cloth if necessary.
Preparing the Hose
Once all components have passed the inspection, the next step is to prepare the hose for assembly. Proper preparation of the hose is critical to ensuring a secure and leak-free connection. Follow these detailed steps:
Measure and Mark the Hose:
Accurate Measurement: Measure the hose to the required length based on your system’s specifications. Use a measuring tape and ensure accuracy to avoid any unnecessary adjustments later.
Marking the Cut: Use a permanent marker to clearly mark the point where the hose needs to be cut. This ensures precision during the cutting process.
Cutting the Hose:
Selecting the Right Tool: Use a hose cutter or a sharp blade specifically designed for cutting hydraulic hoses. A clean, straight cut is essential to ensure the hose seats are properly in the fitting.
Making the Cut: Position the hose cutter at the marked point and apply even pressure to make a clean cut. Avoid using saws or dull blades that could fray or damage the hose ends.
Cleaning the Hose Ends:
Inspect the Cut Ends: After cutting, inspect the hose ends to ensure they are clean, smooth, and free from any fraying. A clean cut is vital for creating a tight seal within the flange fitting.
Debris Removal: Use a lint-free cloth to wipe the hose ends. You can also use compressed air to blow out any small particles or debris. Ensure that no contaminants are present that could interfere with the sealing process.
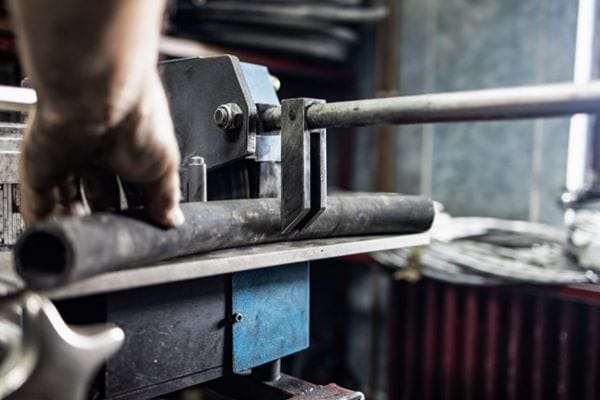
Assembling the Flange Fitting
With the hose prepared, you can now begin the assembly of the flange fitting. Proper alignment and placement of components are crucial in this step. Follow these detailed instructions:
Aligning the Hose with the Flange Head:
Proper Seating: Carefully insert the prepared hose end into the flange head. Ensure that the hose is fully seated within the fitting and that there are no gaps or misalignments.
Visual and Tactile Check: Visually confirm that the hose is aligned straight with the flange head. You can also feel the connection to ensure it is secure and snug.
Positioning the O-Ring:
Selecting the Correct O-Ring: Choose an O-ring that is compatible with the flange fitting and the hydraulic system’s specifications. Ensure that it is free from defects or damage.
Placing the O-Ring: Gently place the O-ring into the groove in the flange head. The O-ring should sit snugly without any twists, kinks, or deformations. Use your fingers to lightly press the O-ring into place, ensuring it is fully seated in the groove.
Lubrication (Optional): If recommended by the manufacturer, apply a light coating of hydraulic fluid or O-ring lubricant to the O-ring. This can help the O-ring slide into place without damage and improve the seal.
Double-Checking the Assembly:
Final Inspection: Before moving on, double-check the alignment of the hose and the placement of the O-ring. Ensure that all components are correctly positioned and that there are no visible issues.
Securing the Flange with Bolts and Nuts
Once the flange fitting is assembled, it is time to secure it to the equipment using bolts and nuts. This step requires precision to ensure a leak-proof connection. Here’s how to do it:
Inserting the Bolts:
Proper Alignment: Align the flange head with the corresponding flange on the equipment. Insert the bolts through the holes in the flange head, ensuring that each bolt is properly aligned with the corresponding hole in the mating flange.
Hand-Tightening the Bolts: Start by hand-tightening the bolts. This helps to bring the flange components together without causing misalignment. Tighten each bolt a little at a time, working in a crisscross pattern to ensure even pressure distribution.
Tightening the Bolts with a Torque Wrench:
Selecting the Correct Torque Setting: Refer to the manufacturer’s specifications for the recommended torque settings. Using the correct torque is crucial to prevent over-tightening or under-tightening, both of which can cause leaks or damage.
Using the Torque Wrench: Begin tightening the bolts with a torque wrench, again working in a crisscross pattern. Apply even pressure and tighten the bolts gradually, checking the torque setting with each turn. Ensure that all bolts are tightened to the specified torque without exceeding the recommended limits.
Final Check:
Uniform Tightening: After all bolts have been tightened, do a final check to ensure that they are uniformly tightened and that the flange is properly seated against the mating surface. There should be no visible gaps or misalignment.
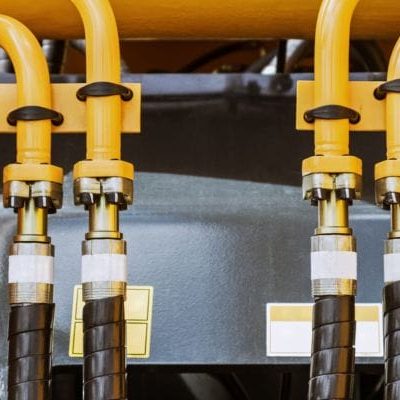
Final Inspection and Testing
With the flange securely fastened, the installation process is nearly complete. However, a final inspection and pressure testing are essential to confirm the integrity of the installation. Follow these steps:
Final Visual Inspection:
Alignment Check: Inspect the assembly to ensure that the flange, hose, and bolts are properly aligned. There should be no visible gaps or misalignment.
O-Ring Inspection: Confirm that the O-ring is correctly seated and has not shifted during the tightening process.
Pressure Testing:
Gradual Pressurization: Gradually pressurize the hydraulic system to the operating pressure. Monitor the flange fitting closely for any signs of fluid leakage or pressure drops.
Leak Detection: Use a leak detection solution or sensor to identify any small leaks that might not be visible to the naked eye. Pay close attention to the areas around the flange and hose connection.
Addressing Issues:
Leak Response: If any leaks are detected, depressurize the system immediately and recheck the installation. Pay particular attention to the O-ring placement and bolt torque. Adjust as necessary and retest until no leaks are present.
Common Installation Mistakes and How to Avoid Them
Incorrect Torque Application
Incorrect torque application is a prevalent issue that can have serious consequences for the integrity of your hydraulic system. When bolts are over-tightened, the excessive force can cause the flange to deform, which in turn compromises the flatness required for a proper seal. This deformation can also damage the O-ring by either flattening it too much or even causing it to extrude from its groove, both of which can lead to leaks. Over time, the stress caused by over-tightening may weaken the bolts themselves, leading to potential failures under pressure.
Conversely, under-tightening the bolts poses its risks. Without sufficient torque, the flange and hose may not be securely fastened, leading to inadequate sealing. This can allow hydraulic fluid to seep out, which not only reduces system efficiency but also creates a safety hazard due to fluid leaks. Additionally, under-tightened bolts can loosen over time, particularly in systems subject to vibration, further exacerbating the problem.
To ensure the correct torque is applied:
Use a calibrated torque wrench: This is essential for applying the precise amount of torque specified by the manufacturer. Regular calibration checks on the wrench are necessary to maintain accuracy.
Follow the manufacturer’s torque specifications: These guidelines are provided to ensure the bolts are tightened to the exact pressure needed for a secure seal without damaging the components.
Tighten bolts in a crisscross pattern: This method evenly distributes pressure across the flange, preventing warping and ensuring a uniform seal. Gradually increase the torque in small increments until the specified value is reached.
Improper O-ring Placement
The O-ring plays a crucial role in sealing the connection between the flange and the hose. Improper placement of the O-ring is a common mistake that can compromise the entire system. If the O-ring is twisted or pinched during installation, it will not sit flat in its groove, leading to an incomplete seal and potential leaks. Additionally, if the groove contains any dirt or debris, the O-ring may not seat properly, further increasing the risk of leaks.
To avoid improper O-ring placement:
Inspect and clean the O-ring groove: Before installing the O-ring, thoroughly inspect the groove to ensure it is clean and smooth. Use a lint-free cloth to remove any debris or particles.
Position the O-ring correctly: Carefully place the O-ring into the groove, ensuring it sits flat without any twists or pinches. Take your time during this step to avoid misalignment.
Use lubricant if necessary: A light coating of hydraulic fluid or a recommended O-ring lubricant can help the O-ring slide into place more easily and form a better seal. This also reduces the risk of the O-ring getting damaged during installation.
Misalignment of Flange Components
Misalignment during the assembly of flange components is another frequent issue that can lead to uneven pressure distribution and improper sealing. Misalignment often occurs when the bolts are not tightened in the correct sequence or when the hose is not properly aligned with the flange head during assembly. This can cause the flange to warp, resulting in leaks and potential system failure.
To ensure proper alignment:
Align the hose with the flange head: Before inserting the bolts, make sure the hose is properly seated within the flange head. This initial alignment is crucial for preventing misalignment during the tightening process.
Tighten bolts in a crisscross pattern: As with torque application, tightening the bolts in a crisscross pattern helps to evenly distribute pressure across the flange. This method prevents one side from being pulled tighter than the other, reducing the risk of warping or misalignment.
Use alignment tools if available: If available, use alignment tools or jigs to hold the flange components in place during the initial tightening. These tools can help maintain alignment and ensure a more accurate assembly.
Skipping Pre-Installation Inspection
Skipping the pre-installation inspection is a critical mistake that can lead to numerous problems during and after installation. Failing to inspect components thoroughly can result in the use of damaged or contaminated parts, which can compromise the integrity of the entire hydraulic system. For example, a small crack in the flange or a tiny particle in the O-ring groove can lead to leaks, failures, and even catastrophic system issues.
To avoid these pitfalls:
Conduct a detailed inspection of all components: Before starting the installation, thoroughly inspect each component. Look for any signs of damage, such as cracks, warping, or corrosion on the flange. Check the hose for cuts, abrasions, or wear that could compromise its integrity.
Ensure cleanliness: Cleanliness is crucial in hydraulic systems. Make sure the O-ring and sealing surfaces are clean and free from any contaminants. Use appropriate cleaning methods, such as wiping with a lint-free cloth or blowing out debris with compressed air.
Conclusion
Properly installed fittings provide a secure and durable connection, which is essential for maintaining the integrity and safety of the entire system. A well-installed flange hose fitting contributes not only to the smooth operation of machinery but also to the overall safety of the workplace, protecting both equipment and personnel from potential hazards.
FAQ
Hydraulic flange hose fittings are components used to securely connect hoses to hydraulic equipment, ensuring a leak-proof seal and stable fluid flow.
Choose a fitting based on the pressure rating (e.g., Code 61 or Code 62), size, material (e.g., steel, stainless steel), and compatibility with your hydraulic system.
Proper torque ensures that the bolts are neither too tight nor too loose, preventing damage to the flange and ensuring a secure, leak-free connection.
Inspect the flange, hose, and O-ring for any damage or contamination, and ensure all components are clean and in good condition before installation.
Leaks can be caused by improper O-ring placement, misalignment of components, or incorrect torque application during installation.
Regular inspections should be conducted according to your system’s maintenance schedule, with immediate attention given to any signs of wear, damage, or leaks.