Hydraulic hoses are essential components in fluid power systems, responsible for transferring fluid between different parts of machinery and equipment. These flexible hoses are designed to withstand high pressure and convey hydraulic fluids, ensuring the smooth and efficient operation of various mechanical systems. Selecting the right hydraulic hose is crucial for optimal performance. A mismatch between the hose and its operating environment can lead to poor efficiency, equipment downtime, and even safety hazards. The right hose must be compatible with the system’s pressure, fluid type, and most importantly, temperature conditions.
Basics of Hydraulic Hose Construction and Temperature Ratings
Hydraulic Hose Construction
Hydraulic hoses are composed of three main layers, each playing a critical role in their functionality and durability:
Inner Tube:
The inner tube is the part of the hose that comes into direct contact with hydraulic fluids. It must be compatible with the specific type of fluid used, whether oil, water, or synthetic liquids. The material used in the inner tube varies depending on the hose’s application, and it must also withstand high pressures without breaking down or contaminating the fluid.
Reinforcement Layer:
Surrounding the inner tube is the reinforcement layer, which provides strength and flexibility to the hose. This layer can consist of multiple types of reinforcement, such as braided wire, textile yarn, or spiral wire, depending on the pressure and performance requirements. The reinforcement gives the hose the ability to handle high pressure without bursting or kinking.
Outer Cover:
The outer cover of a hydraulic hose protects the inner components from external damage such as abrasion, chemicals, and environmental exposure. This layer must also resist temperature fluctuations, as it will be exposed to external ambient temperatures. Various materials are used for the outer cover depending on the operational environment, such as weather-resistant rubber or abrasion-resistant thermoplastic.
Each of these layers is essential to the hose’s overall performance, and the materials used in their construction directly impact the hose’s ability to tolerate different temperature conditions.
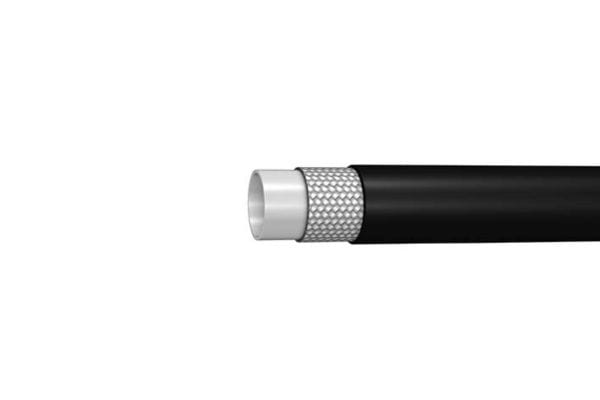
How Different Materials Affect Temperature Resistance
Rubber:
Rubber hoses are among the most commonly used due to their flexibility and resistance to a wide range of fluids. However, rubber’s temperature resistance is generally limited. It performs well in moderate temperature ranges but can degrade when exposed to extreme heat or cold for prolonged periods.
Thermoplastics:
Thermoplastic hoses are often used in applications where greater resistance to chemicals and extreme temperatures is required. These hoses can endure a broader range of temperatures compared to rubber hoses, offering more versatility in environments where temperatures fluctuate. However, thermoplastics can become brittle at very low temperatures.
Metals (such as stainless steel or PTFE):
PTFE (polytetrafluoroethylene) hoses are known for their high-temperature resistance, often used in applications that require operation in extremely hot environments. Metal hoses, typically made of stainless steel, are also highly durable in both extreme heat and cold. However, they lack the flexibility of rubber or thermoplastic hoses, limiting their use in certain dynamic applications.
Types of Hydraulic Hoses Based on Materials
Rubber Hydraulic Hoses:
Strengths: Rubber hoses are flexible, durable, and can handle a wide range of hydraulic fluids. They are widely available and generally cost-effective for most applications.
Weaknesses: Rubber tends to degrade in extreme heat or cold, making it less ideal for temperature-sensitive applications. Prolonged exposure to heat can cause rubber to crack or blister, while cold temperatures can lead to stiffening and brittleness.
Thermoplastic Hydraulic Hoses:
Advantages: Thermoplastic hoses are more resistant to chemicals and temperature extremes than rubber hoses. They offer enhanced durability in harsh conditions, including environments with varying temperature ranges.
Limitations: Thermoplastic hoses can be more expensive and less flexible than rubber hoses. At very low temperatures, they may become stiff and brittle, which could result in cracking or failure.
PTFE Hydraulic Hoses:
Unique Benefits: PTFE hoses are highly resistant to heat, making them ideal for high-temperature applications such as aerospace, chemical processing, and automotive industries. They offer excellent chemical resistance and do not degrade when exposed to extreme temperatures. PTFE hoses maintain their strength and flexibility even in environments exceeding 400°F (204°C).
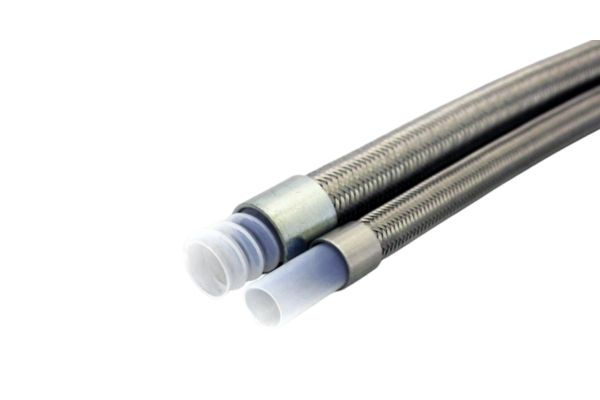
Temperature Rating Explained
Defining Temperature Limits:
Temperature limits refer to the minimum and maximum temperatures at which a hydraulic hose can safely operate. These limits are specified by the hose manufacturer and vary depending on the hose material, construction, and intended application. For example, a rubber hose may have a temperature range of -40°F to 212°F (-40°C to 100°C), while a PTFE hose may have a temperature range of -65°F to 450°F (-54°C to 232°C).
How Temperature Ratings Are Determined:
Manufacturers determine the temperature ratings for hydraulic hoses based on rigorous testing. Hoses are subjected to environmental simulations to evaluate their performance under different temperature conditions. These tests assess how temperature affects the hose’s material integrity, flexibility, pressure handling, and fluid compatibility. Manufacturers also factor in how temperature changes impact the hose’s resistance to wear and abrasion.
Temperature ratings are usually given in two categories:
Continuous Operation: The temperature range within which the hose can operate safely for extended periods without deterioration.
Intermittent Operation: The higher or lower temperature limits the hose can withstand for brief periods without failure, but not recommended for sustained use.
Factors Influencing Hydraulic Hose Temperature Limits
Ambient vs. Fluid Temperature
The Difference Between Ambient Temperature and Fluid Temperature in the System
Ambient Temperature: Refers to the temperature of the surrounding environment where the hydraulic system is operating. This could include external factors like outdoor weather conditions, the temperature inside a manufacturing facility, or the heat generated by nearby machinery.
Fluid Temperature: Refers to the temperature of the hydraulic fluid circulating inside the hose. This temperature can be significantly different from the ambient temperature due to the internal heat generated by the system’s operations, such as friction, pressure, and fluid movement.
Understanding the distinction between ambient and fluid temperatures is critical when selecting hydraulic hoses. A hose may be exposed to high ambient temperatures while maintaining a lower fluid temperature, or vice versa, leading to different stresses on the hose material. Hydraulic hoses need to be rated for both types of temperatures to ensure long-term performance and avoid premature failure.
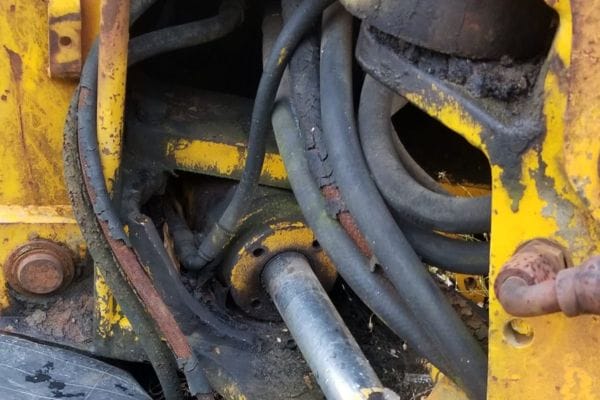
How Both Factors Contribute to the Overall Performance and Longevity of Hydraulic Hoses
Ambient Temperature Influence: High ambient temperatures can accelerate the aging and degradation of the hose’s outer cover, leading to cracking, blistering, or hardening of the material. Cold ambient temperatures can cause the hose to become rigid and lose flexibility, increasing the risk of cracking when bent or under stress.
Fluid Temperature Influence: Excessively high fluid temperatures can cause the inner tube of the hose to soften, swell, or even dissolve over time, while low fluid temperatures may cause the fluid to become viscous and lead to hose hardening. Both conditions can lead to diminished flow capacity, increased wear, and eventual failure of the hose.
Thermal Cycling and Temperature Spikes
Explanation of Temperature Fluctuations During Operation
Hydraulic systems rarely operate under consistent temperature conditions. The temperature of the fluid inside the hose often fluctuates due to system start-ups, shutdowns, pressure changes, or external environmental factors. This is known as thermal cycling, where the hose undergoes repeated cycles of heating and cooling over time.
Temperature spikes refer to sudden, short-lived increases in fluid or ambient temperature, often occurring during heavy loads, system malfunctions, or unexpected external influences. These spikes can cause stress on the hose materials if they exceed the hose’s maximum temperature rating.
The Impact of Temperature Cycling on the Life and Durability of Hydraulic Hoses
Repeated exposure to thermal cycling can cause hoses to become fatigued, leading to cracks, delamination, or even burst failures. The material may expand and contract with each temperature cycle, putting stress on the hose’s inner tube and reinforcement layers. Over time, this process can degrade the hose’s structural integrity, shortening its lifespan.
Temperature spikes can cause immediate damage if they exceed the hose’s maximum temperature limits, even if only for a brief period. These spikes can lead to localized overheating, weakening the hose material, and causing a rupture or blistering in the outer cover.
Ways to Manage Temperature Spikes
Use of Temperature Sensors: Installing temperature sensors within the hydraulic system can help monitor fluid temperatures in real time, alerting operators to potential temperature spikes.
Insulation and Protective Sleeves: For hoses operating in environments prone to thermal cycling or spikes, using insulation or protective sleeves can help mitigate temperature fluctuations and protect the hose from external heat sources.
Proper Hose Selection: Ensuring that the hose is rated for the highest possible temperature spikes, rather than just continuous operating temperatures, can prevent premature hose failure.
Pressure and Temperature Correlation
How Pressure Influences the Temperature Tolerance of Hydraulic Hoses
Pressure and temperature are closely linked in hydraulic systems. When fluid pressure increases, it generates more heat within the system, raising the fluid temperature. Similarly, higher operating temperatures can lead to increased internal pressure, as fluids expand when heated.
High-pressure environments place additional stress on hydraulic hoses, and if combined with elevated temperatures, can significantly reduce the hose’s performance and lifespan. The reinforcement layers of the hose, which are designed to handle pressure, can become compromised at higher temperatures, leading to failures such as blowouts or leaks.
Explanation of Derating
Derating refers to the process of adjusting the hose’s performance specifications based on external factors, such as temperature. As the operating temperature increases, the maximum pressure rating of the hose decreases. This is because higher temperatures cause the hose materials to weaken, reducing their ability to handle the same pressure loads they would under lower temperatures.
For example, a hose rated for 5,000 psi at 70°F (21°C) may only be capable of handling 3,500 psi at 180°F (82°C). The pressure rating must be reduced (or derated) to account for the weakening of the hose materials at elevated temperatures.
Choosing the Right Hydraulic Hose for Temperature-Sensitive Applications
Assessing Your Application’s Temperature Requirements
Key Questions to Consider:
When selecting a hydraulic hose, it is essential to thoroughly evaluate the temperature conditions of the intended application. Consider the following key questions:
What is the typical temperature range?: What are the normal operating temperatures for both the ambient environment and the hydraulic fluid within the system?
What are the extremes?: What are the potential minimum and maximum temperatures the hose may be exposed to, either through environmental factors or operational conditions?
Is there a possibility of thermal cycling or temperature spikes?: Does the system experience frequent temperature changes, or will there be occasional spikes that could push the temperature above the normal operating range?
How long will the hose be exposed to extreme temperatures?: Is the exposure to extreme temperatures continuous or intermittent? The duration of exposure will impact the hose’s material selection.
Examples of Industries and Applications with Specific Temperature Demands:
Oil and Gas: Hydraulic systems used in drilling and refining processes often encounter extreme temperatures, from the scorching heat of desert environments to the cold of offshore or arctic drilling. High-temperature resistance is critical to ensuring system reliability.
Agriculture: Agricultural machinery is often exposed to fluctuating outdoor temperatures, with systems needing to function in both hot summer months and freezing winter conditions. Selecting a hose with the appropriate temperature rating helps maintain performance throughout the year.
Automotive: Automotive hydraulic systems, such as heavy-duty vehicles, require hoses that can handle the heat generated by the engine and exhaust components, as well as the cooling conditions encountered in winter driving.
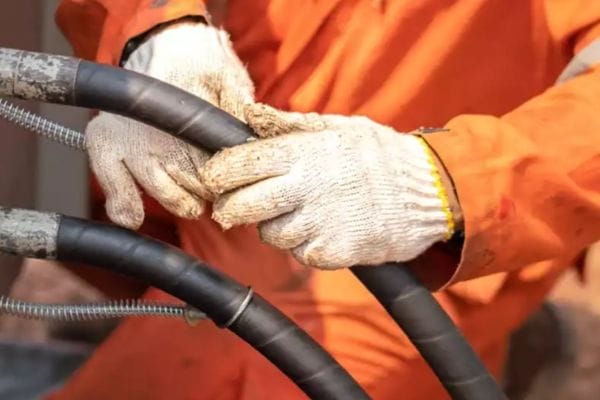
Matching Hoses to Your Needs
Choosing the Right Materials for High-Temperature Environments:
For applications operating in high-temperature conditions, material selection is paramount. PTFE (Polytetrafluoroethylene) hoses, for example, are highly resistant to heat and can handle temperatures up to 450°F (232°C).
Stainless steel braided hoses are another good option for high-temperature environments. These hoses have metal reinforcement that provides extra protection and heat resistance, making them ideal for applications exposed to extreme heat.
Considerations for Extreme Cold Conditions and Hose Flexibility at Low Temperatures:
In cold environments, hoses must remain flexible without becoming brittle. Thermoplastic hoses, which can endure lower temperatures than many rubber hoses, provide flexibility in freezing conditions. These hoses are commonly used in snow plowing, refrigeration, and other outdoor equipment that must function in subzero environments.
Rubber hoses are generally less effective in extremely cold conditions, as they tend to stiffen.
Examples of Hydraulic Hoses Rated for Different Temperature Ranges:
Standard Rubber Hydraulic Hoses: Typically rated for temperatures between -40°F to 212°F (-40°C to 100°C). These hoses are suitable for a variety of general-purpose applications, but they may not withstand extreme temperatures over time.
Thermoplastic Hydraulic Hoses: Often rated for temperatures between -70°F to 250°F (-57°C to 121°C). These hoses are designed for cold-weather environments and are suitable for outdoor applications where extreme flexibility in freezing temperatures is needed.
PTFE and Stainless Steel Braided Hoses: Rated for temperatures ranging from -65°F to 450°F (-54°C to 232°C). These hoses are ideal for high-temperature applications and extreme environments where reliability is critical.
Viton®-Covered Hoses: For ultra-high-temperature environments, some hoses are covered with materials like Viton®, offering temperature ratings of up to 400°F (204°C). These hoses are used in specialty applications, such as chemical processing or high-performance automotive systems.
Common Temperature-Related Hydraulic Hose Failures
Signs of Overheating and Heat Damage
Visible Signs That a Hydraulic Hose Is Experiencing Heat-Related Failure:
Blistering: One of the most noticeable signs of heat damage is blistering on the outer cover of the hydraulic hose. Excessive heat causes the materials to soften and swell, leading to the formation of blisters on the hose surface.
Cracking: Prolonged exposure to high temperatures can cause the outer layer of the hose to become brittle and crack. These cracks can eventually spread to the reinforcement layers, leading to leaks or hose failure.
Discoloration: A change in the color of the hose, particularly darkening or browning, is a clear indicator of heat degradation. The heat can cause the outer cover to scorch or fade, signaling that the hose is no longer performing within its intended temperature range.
Impact of Exceeding Temperature Limits on Hose Performance:
Exceeding a hydraulic hose’s temperature rating can significantly compromise its performance. At high temperatures, the inner tube material can soften and degrade, leading to fluid permeation or hose bursting. Heat can also break down the hose’s reinforcement layer, reducing its ability to withstand pressure. The combination of temperature and pressure stress often leads to premature failure, costly repairs, and potential safety hazards.
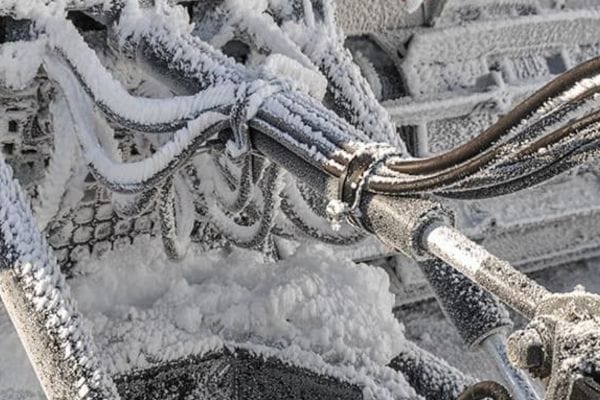
Cold Weather Failures
How Extreme Cold Can Cause Hose Brittleness, Cracking, and Failure:
Hydraulic hoses are also vulnerable to failures in extremely cold environments. Low temperatures cause materials like rubber and thermoplastics to stiffen and lose their flexibility. When a hose becomes brittle, it is more prone to cracking, especially when subjected to bending or pressure fluctuations. In severe cold conditions, hydraulic fluid may thicken, increasing the internal pressure and stressing the already brittle hose, resulting in a higher likelihood of rupture or leaks.
Solutions to Prevent Cold-Related Failures:
Using Specially Formulated Hoses: Selecting hoses specifically designed for low-temperature conditions is essential. Cold-weather hydraulic hoses are made from materials that retain their flexibility and strength even in freezing temperatures. These hoses are engineered to handle the stress of expanding and contracting fluids without becoming brittle.
Insulation and Protective Sleeves: Insulating hydraulic hoses with protective sleeves or wraps help maintain fluid temperature and reduce exposure to cold air. This extra layer of protection minimizes the effects of freezing temperatures and prevents hoses from becoming brittle.
Preventive Maintenance Tips for Temperature-Related Issues
Best Practices to Monitor Hydraulic Hose Conditions Under Extreme Temperature Conditions:
Regular Inspection: Frequently inspecting hydraulic hoses for signs of heat or cold damage is crucial for maintaining system integrity. Look for visible indicators such as cracking, blistering, or discoloration, as well as any unusual stiffness in the hose that might indicate cold-related brittleness.
Check Temperature Ratings: Always verify that the hoses in use are rated for the specific temperature conditions of the application. Review the manufacturer’s temperature ratings and ensure that both the ambient and fluid temperatures remain within the hose’s specified limits.
Monitor Fluid Temperatures: Installing temperature sensors within the hydraulic system helps continuously monitor fluid temperatures. These sensors provide real-time data, allowing operators to adjust system conditions before exceeding the hose’s temperature rating.
Recommendations for Regular Inspections and Maintenance to Prevent Temperature-Induced Failures:
Proactive Replacement: Even before visible damage occurs, consider replacing hoses that have been exposed to extreme temperatures for extended periods. This preventive measure can avoid catastrophic failures that occur due to long-term temperature exposure.
Maintain Proper Storage Conditions: When hoses are not in use, store them in environments where temperature fluctuations are minimized. Avoid exposure to direct sunlight or freezing conditions during storage, as these can degrade hose materials over time.
Fluid Maintenance: Ensure that hydraulic fluid is kept at optimal levels and that the system includes temperature control mechanisms, such as cooling units or heaters, depending on the operating environment.
Conclusion
By making the correct hydraulic hose selection based on temperature limits, you can prevent costly failures, reduce maintenance costs, and ensure your hydraulic systems continue to operate reliably, even under the most demanding temperature conditions. Proper hose selection is a long-term investment in the performance and safety of your hydraulic equipment.
FAQ
What is the maximum temperature a hydraulic hose can handle?
The maximum temperature a hydraulic hose can handle depends on the hose material. For example, rubber hoses typically handle up to 212°F (100°C), while PTFE hoses can withstand up to 450°F (232°C).
How does cold weather affect hydraulic hoses?
Cold weather can make hydraulic hoses brittle, causing them to crack or become less flexible. Specially designed cold-weather hoses are recommended for such conditions.
Can a hydraulic hose fail due to overheating?
Yes, overheating can cause the hose to blister, crack, or degrade, leading to leaks or system failure. It’s important to select hoses that meet the temperature requirements of your application.
How do I know if my hydraulic hose is overheating?
Signs of overheating include blistering, discoloration, or cracking of the hose’s outer layer. Regular inspections can help detect these signs early.
What materials are best for high-temperature hydraulic hoses?
PTFE and stainless steel braided hoses are excellent choices for high-temperature applications due to their ability to withstand extreme heat without degrading.
How can I protect my hydraulic hose from extreme temperatures?
You can protect hydraulic hoses from extreme temperatures by using insulation, protective sleeves, or selecting hoses specifically rated for high or low temperatures.