Valves control, direct, and isolate fluids and are indispensable for maintaining system performance, safety, and efficiency. Of the various types of valves, globe valves and ball valves are two of the most common choices. Each type of valve excels in different aspects of operation, especially in fluid control management.
Overview of Globe Valves
Basic Definition
A globe valve is a type of valve commonly used in industrial and residential fluid systems for regulating the flow of liquids and gases. Unlike other valve types that are primarily designed for on/off control, globe valves are specifically built for throttling, or modulating the flow of fluids. This ability makes them especially useful in applications where precise control of flow rate is essential.
The globe valve’s design includes a spherical body with an internal baffle that directs the flow of fluid through a defined path, enabling fine control over the flow rate. The key components of a globe valve are the valve body, stem, disc, and seat, which work together to regulate the flow of the medium in a system.
Globe valves are widely used in systems where flow modulation is necessary, such as heating, cooling, water treatment, and steam systems. They are ideal for applications where flow needs to be adjusted continuously rather than simply turned on or off, making them critical in maintaining optimal system performance and efficiency.
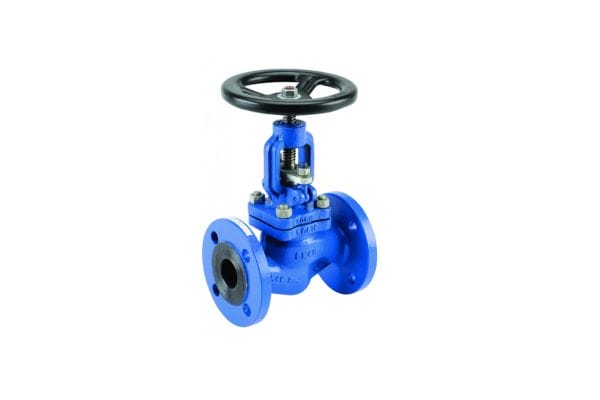
Types of Globe Valves
There are several variations of the globe valve, each suited for specific types of flow control or installation needs. The most common types include:
Straight Pattern Globe Valve: The simplest and most straightforward type of globe valve, where the flow moves directly through the valve along a straight path. This design is often used in applications where space is not constrained and where the flow control is the main priority.
Angle Pattern Globe Valve: In this variation, the inlet and outlet of the valve are at a 90-degree angle to one another. This design can be useful in applications where the flow direction needs to be changed, or where space constraints require a more compact design.
Y-Pattern Globe Valve: This type features a Y-shaped body design, which provides a more efficient flow path compared to the straight and angle patterns. The Y-pattern design reduces pressure drops, which makes it a better option for high-pressure systems and those requiring more efficient flow regulation.
Each type of globe valve offers specific advantages, but all share the same core function: precise flow regulation.
Working Principle
Globe valves operate by controlling the flow of fluids through the opening between the valve seat and the valve disc. When the valve is in the fully open position, the disc is lifted away from the seat, allowing the fluid to flow freely. As the valve is gradually closed, the disc moves closer to the seat, constricting the flow and allowing for more controlled regulation of the fluid’s movement.
The throttling capability of globe valves comes from the linear motion of the valve disc, which enables fine adjustments to the opening and closing mechanism. This feature makes globe valves ideal for applications requiring gradual flow control. The act of adjusting the valve stem changes the position of the disc, thereby altering the flow rate. The precision of the adjustment depends on the valve design and the sensitivity of the valve stem, allowing operators to fine-tune the system for optimal performance.
Key Features
Several key features of the globe valve contribute to its ability to regulate flow effectively:
Stem: The stem is the part of the valve that moves the disc in or out of the valve seat. It is usually operated by a manual handwheel, or by an actuator in automated systems. The stem’s motion allows for precise adjustments to the valve’s opening, making it critical for throttling.
Disc: The disc is the movable component that directly interacts with the seat to control the flow. It can have various designs depending on the specific valve type, but its primary function is to either block or allow fluid to pass through the valve.
Seat: The seat is the stationary part of the valve that provides a sealing surface for the disc to rest against when the valve is closed. The quality of the seat, along with the disc’s sealing mechanism, determines the tightness of the valve when closed and its ability to prevent leaks.
Body: The valve body is the main structure that houses the seat, disc, and stem. The shape and design of the body contribute to the flow characteristics of the valve. For globe valves, the body is typically spherical or cylindrical, with internal passages designed to guide the fluid in a specific direction.
Overview of Ball Valves
Basic Definition
A ball valve is a type of valve that uses a hollow, perforated, and pivoting ball to control the flow of fluids through a pipeline. When the valve is open, the ball is rotated so that the hole is aligned with the flow path, allowing fluid to pass through. When the valve is closed, the ball is rotated 90 degrees to block the flow, providing a tight seal. Ball valves are primarily used for on/off control of the fluid flow, although some designs also offer flow regulation capabilities, particularly in applications with larger pipe sizes.
The ball valve’s simplicity and ability to create a quick, tight shut-off make it one of the most popular choices in many industries. It is commonly used in systems requiring minimal maintenance and high reliability, including applications in oil and gas, chemical processing, water treatment, and HVAC systems.
Types of Ball Valves
There are several variations of ball valves, each designed for specific applications and performance needs. Some of the most common types include:
Floating Ball Valve: This is the most common type of ball valve. In a floating ball valve, the ball is not fixed to the valve stem. Instead, it is held in place by the pressure of the fluid and the two seats on either side of the ball. When the valve is closed, the ball is pushed into the seat by the pressure differential. Floating ball valves are ideal for lower-pressure systems or those where full-tight shutoff is required.
Trunnion-Mounted Ball Valve: In this design, the ball is fixed in place by two trunnions (supports) on either side, allowing the ball to rotate but preventing it from moving axially (up and down). This design is used for larger valves or high-pressure applications, where the floating ball design may not be able to handle the stress of the flow pressure. Trunnion-mounted ball valves are ideal for large pipeline systems or applications where high flow rates and pressure are present.
V-Port Ball Valve: This variation features a ball with a “V” shaped notch, allowing for controlled, throttling-type flow regulation. The V-port ball valve is suitable for applications that require more control over the flow rate, though it is still predominantly used for on/off service.
Multi-Port Ball Valve: These ball valves have more than two ports and can direct flow in multiple directions. Multi-port ball valves are often used in systems requiring the flow to be directed to more than one location or where flow needs to be diverted.
Each type of ball valve has its specific advantages based on the application’s flow and pressure requirements.
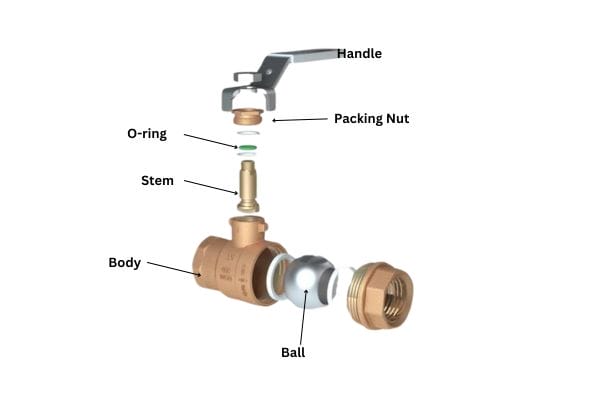
Working Principle
The working principle of a ball valve is simple yet effective. The valve consists of a ball with a hole or port through its center, which can rotate inside the valve body. The ball is mounted on a stem that allows it to rotate when the valve is actuated.
On/Off Control: In the fully open position, the hole in the ball is aligned with the flow path, allowing fluid to pass through. When the valve is turned 90 degrees, the hole is perpendicular to the flow path, and the ball blocks the flow, effectively closing the valve. This quick and efficient mechanism provides a rapid shutoff, making ball valves ideal for applications where the fluid needs to be quickly stopped or started.
Flow Regulation: While ball valves are primarily designed for on/off control, certain types, like the V-port ball valve, allow for partial opening and regulation of the flow. In these cases, the flow is controlled by adjusting the rotation of the ball to allow more or less fluid to pass through the opening. However, ball valves generally provide less precise flow regulation than globe valves.
Sealing and Pressure Handling: The ball valve uses two seats (usually made of a material like Teflon, metal, or elastomers) to create a seal around the ball when it is in the closed position. The pressure exerted by the fluid against the ball helps ensure a tight seal. In floating ball valves, the ball is pushed against the downstream seat by the fluid pressure, while in trunnion-mounted valves, the fixed trunnion design helps support the ball and reduce the load on the seals.
Key Features
Several critical components of the ball valve contribute to its performance and reliability in controlling fluid flow:
Ball: The central component of the ball valve, the ball is a hollow, spherical piece with a hole through its center. The ball’s rotation determines whether the valve is open or closed. The material and design of the ball influence the valve’s ability to handle different types of fluids, pressures, and temperatures. For example, metal balls are used for high-temperature applications, while plastic balls are used for corrosive or non-pressurized systems.
Seats: The seats are the surfaces that the ball seals against to block the flow when the valve is closed. The quality of the seat materials (such as PTFE or metal) directly affects the performance and durability of the valve. In some designs, the seats are spring-loaded to ensure that the ball remains firmly seated and provides a tight shutoff.
Stem: The stem connects the ball to the valve handle or actuator and controls the rotation of the ball. The movement of the stem is what causes the ball to rotate 90 degrees between the open and closed positions. The stem is often sealed with packing to prevent fluid leakage along the shaft.
Valve Body: The body of the valve houses the ball, stem, and seats, and it is designed to withstand the pressure and temperature conditions of the system. It is typically made from durable materials such as stainless steel, brass, or carbon steel, depending on the application.
Control Capabilities: Globe Valve vs Ball Valve
Throttling Control
Globe valves are designed with throttling or flow modulation in mind. Their internal components, particularly the stem and disc, allow for gradual adjustments to the flow rate. By precisely moving the disc closer to or away from the seat, the valve can control the flow in small increments. This makes globe valves especially well-suited for throttling—a process that involves controlling the amount of fluid passing through the valve at any given time.
Globe Valve: The ability of a globe valve to control flow gradually is its main advantage. As the valve is partially closed, the disc moves in a linear motion toward the seat, reducing the flow proportionally. This precise control allows for continuous adjustment, making globe valves ideal for processes where steady, regulated flow is crucial, such as in heating or cooling systems, or in steam lines.
Ball Valve: While ball valves can be used for throttling, their design is optimized for on/off control, not gradual flow modulation. In a ball valve, the ball moves through a 90-degree rotation, with the hole either fully aligned with the flow path (open) or perpendicular to it (closed). While V-port ball valves are a variation designed for throttling, they still lack the same level of fine control as globe valves. The flow adjustment in a ball valve is more abrupt, making it unsuitable for precise flow regulation in applications where gradual or fine control is required.
In summary, globe valves are the better choice for throttling, offering superior precision in gradual flow control, while ball valves are typically used for situations requiring full flow or complete shutoff.
Pressure Drop
Pressure drop refers to the reduction in pressure that occurs as a fluid flows through a valve. It is an important consideration in valve selection because excessive pressure drop can result in inefficiencies, increased energy consumption, and potential damage to other components in the system.
Globe Valve: One disadvantage of globe valves is their high pressure drop, especially when partially closed. The flow must navigate a convoluted path through the valve body, creating more resistance and causing a greater loss in pressure. This pressure drop can be significant in systems where maintaining pressure is important or in large diameter pipelines. Therefore, globe valves are generally not recommended for low-pressure systems or when minimizing energy loss is a priority.
Ball Valve: Ball valves, on the other hand, are designed for minimal resistance to flow when fully open. The ball’s streamlined, unobstructed design creates less friction with the fluid, leading to a low pressure drop. This makes ball valves an excellent choice for applications where pressure stability is critical, such as in oil and gas pipelines or high-flow systems. Even when ball valves are used for throttling (in the case of V-port ball valves), the pressure drop is still generally lower than in globe valves.
In conclusion, ball valves are more effective in maintaining low pressure drop, making them preferable for applications that require maintaining pressure over long distances or in high-flow systems. Globe valves have a higher pressure drop, which can reduce efficiency in such cases.
Flow Regulation
When it comes to flow regulation, both types of valves have distinct abilities to modulate fluid flow, but their performance varies significantly depending on the application.
Globe Valve: Globe valves offer precise flow regulation, thanks to their linear motion. The gradual adjustment of the disc allows for fine-tuned control over flow rates, which is particularly useful in low-flow applications or systems where flow control must be adjusted in small steps. The design of the globe valve, with its specific flow path, ensures that even partial openings result in controlled, stable flow, which is why these valves are widely used in water treatment plants, chemical processes, and HVAC systems.
Ball Valve: Ball valves, in contrast, are better suited for full-flow control. Their design excels when it comes to providing an open or closed flow path with minimal intermediate control. The flow adjustment in a ball valve is typically all-or-nothing, so it is less suitable for systems requiring fine-tuned modulation. However, V-port ball valves can be used for some level of throttling, but still, they do not offer the precision of globe valves in this regard. Ball valves can be used for flow control in large pipelines or applications where a quick and efficient adjustment between fully open and fully closed is sufficient.
Therefore, globe valves are the ideal choice for precision flow regulation, especially in systems where continuous, fine-tuned flow adjustments are required.
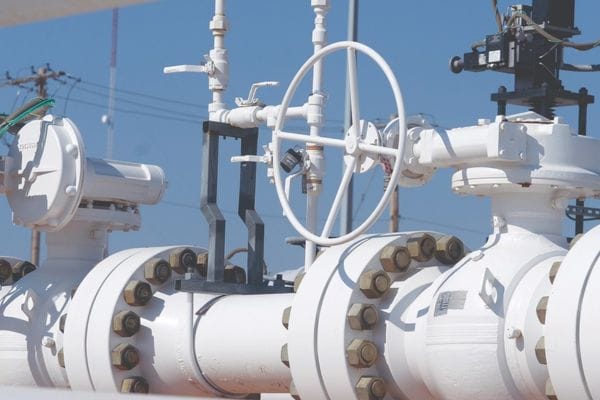
Applications Requiring Control
Certain industries demand valves that offer precise flow regulation for efficiency, safety, and reliability. Here’s a look at which valve is best suited for such applications:
Globe Valves: Due to their ability to regulate flow in a controlled, gradual manner, globe valves are often used in applications requiring precise control over fluid flow. These include:
HVAC systems: For controlling air and water temperature and flow rates in heating and cooling systems.
Water treatment: For controlling the flow of water infiltration and chemical dosing systems.
Steam systems: Globe valves are used in regulating the flow of steam in power plants and other industries requiring high-temperature fluid regulation.
Ball Valves: While ball valves are primarily used for on/off control, they also find use in applications where high flow rates are required and precision is less of a concern. Examples include:
Oil & Gas: Ball valves are commonly used in pipelines where flow control is needed quickly and efficiently.
Chemical processing: For high-flow applications requiring minimal pressure drop.
Water distribution systems: Where rapid opening and closing are essential, such as in irrigation or industrial water treatment systems.
Conclusion
For precise flow regulation and throttling, a globe valve will provide the most effective solution. However, for high-flow, quick shutoff needs with minimal pressure drop, a ball valve is the ideal choice. Choosing the right ball valve will ensure optimal performance, operational efficiency, and cost-effectiveness in your fluid handling system.
FAQ
What is the main difference between a globe valve and a ball valve?
Globe valves are ideal for gradual flow regulation (throttling), while ball valves are designed for quick on/off control with minimal pressure drop.
Can a ball valve be used for throttling flow?
Yes, but ball valves are not as precise for throttling as globe valves. V-port ball valves can modulate flow, but globe valves offer more accurate control.
Which valve is better for high-pressure systems?
Ball valves are typically better for high-pressure systems due to their design, which causes less pressure drop compared to globe valves.
Are globe valves more expensive than ball valves?
Globe valves tend to be more expensive due to their more complex design and ability to provide fine flow control. Ball valves are generally more cost-effective for simple on/off applications.
What industries use globe valves?
Globe valves are commonly used in industries that require precise control, such as water treatment, chemical processing, and HVAC systems.
Can a ball valve be used for precise flow regulation?
While ball valves can regulate flow in specific designs (e.g., V-port ball valves), they are generally less precise than globe valves for continuous, fine adjustments.