Check valves are essentially mechanical devices designed to allow the flow of fluid or gas in one direction while preventing reverse flow. These valves operate automatically without the need for external control, relying on the pressure of the fluid or gas to open or close. Found in a wide range of applications, check valves are critical components in systems where backflow could cause damage, contamination, or inefficiency. Their primary role is to ensure that the media in a system flows smoothly in one direction, preventing any backward movement that could disrupt processes or damage equipment.
How Check Valves Work
Definition and Purpose
A check valve is a mechanical device that allows fluid or gas to flow in one direction while automatically preventing flow in the opposite direction. The main function of a check valve is to stop backflow, which can cause contamination, equipment damage, or process inefficiency. This ability to restrict reverse flow is crucial for maintaining the integrity and performance of fluid or gas systems in various industries. Check valves are used across many sectors to protect vital components like pumps, compressors, and pipelines from damage caused by backflow or pressure changes.
The role of check valves is especially important in systems where backflow can result in significant damage. For example, in pump systems, reverse flow can cause the pump to spin backward, leading to seal damage or overheating. In water treatment facilities, backflow can result in contamination of clean water with dirty or hazardous liquids. Therefore, the installation of check valves is vital for system reliability, safety, and protection against costly repairs or downtime.
Basic Mechanism
Check valves operate automatically without the need for manual control or external power. Their operation is dependent on the pressure differential between the forward (upstream) and reverse (downstream) flows. The valve opens when the forward pressure exceeds the reverse pressure, allowing fluid or gas to pass through. As long as the forward pressure is greater, the valve remains open, ensuring that the flow moves in the desired direction.
When reverse pressure increases and surpasses the forward pressure, the check valve closes. This closure happens due to gravity, spring force, or a pressure differential acting on the valve’s internal components, such as a disc, ball, or diaphragm. Once the valve is closed, it forms a tight seal, preventing any reverse flow. This simple yet effective mechanism ensures that the system is protected from backflow-related issues, without requiring constant monitoring or manual intervention.
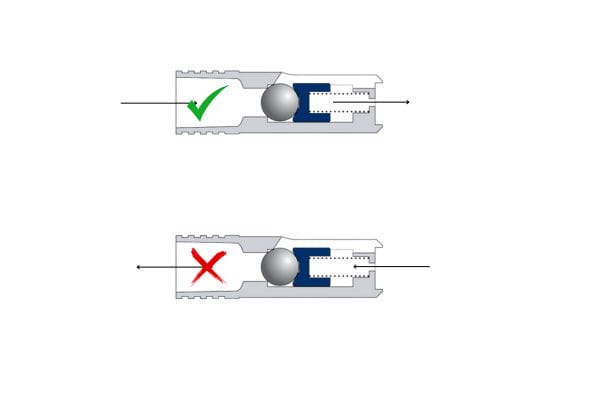
Applications Overview
Check valves are employed in a wide variety of industries, making them a critical component in numerous applications. In the oil and gas industry, check valves are used to prevent backflow in pipelines that transport crude oil, gas, and other petrochemicals, protecting against dangerous leaks or contamination. Chemical processing plants rely on check valves to maintain unidirectional flow and prevent the mixing of chemicals that could lead to hazardous reactions or equipment corrosion.
In water systems, check valves prevent the backflow of potentially contaminated water, ensuring the safety and purity of drinking water supplies. They are often installed in wastewater treatment systems to avoid mixing clean water with sewage or industrial waste. Similarly, in HVAC systems, check valves prevent backflow in heating, ventilation, and air conditioning units, protecting compressors and other essential components from damage due to reverse flow.
Additionally, check valves are widely used in marine applications, food and beverage industries, and pharmaceutical production, where controlling the flow of fluids is critical for maintaining safety, quality, and regulatory compliance. In all these applications, check valves ensure smooth operation, equipment longevity, and system efficiency by preventing reverse flow and protecting the integrity of the process.
Types of Check Valves
Ball Check Valves
Ball check valves are among the simplest and most commonly used types of check valves. They use a spherical ball to block the flow of fluid or gas in one direction and allow it to flow in the other. The ball sits on a seat, and when forward pressure is applied, the ball lifts to allow fluid to pass. When the pressure drops or reverses, the ball returns to the seat, sealing the valve and preventing backflow.
Uses: Ball check valves are typically found in low-pressure systems such as water pumps and wastewater applications. They are particularly effective in systems that handle clean liquids and gases with moderate flow rates.
Pros:
Simple design with few moving parts.
Durable and reliable for low-pressure applications.
Minimal maintenance is required.
Cons:
Prone to wear over time, especially in systems with particulate matter or high flow rates.
Not ideal for high-pressure or high-temperature environments.
Swing Check Valves
Swing check valves feature a disc that swings on a hinge or pivot to allow fluid to flow in one direction and close when the flow reverses. The swinging motion of the disc provides a full, unobstructed opening for fluid flow, making this type of valve suitable for systems with higher flow rates.
Uses: Swing check valves are widely used in moderate to high-flow systems such as HVAC (Heating, Ventilation, and Air Conditioning), water treatment plants, and large-scale fluid systems.
Pros:
Suitable for handling large volumes of fluid or gas.
Low pressure drop due to the full opening of the disc.
Cons:
The hinge mechanism can wear over time, requiring regular maintenance.
The valve may not close quickly in low-flow systems, potentially allowing some backflow.
Vulnerable to water hammer in high-pressure applications.

Lift Check Valves
Lift check valves operate using a piston or disc that lifts vertically when forward pressure is applied, allowing flow. The valve closes when reverse pressure occurs, as the disc or piston is pushed back into its seat by gravity or system pressure.
Uses: Lift check valves are ideal for high-pressure applications, such as steam systems and compressed air pipelines. Their robust design makes them well-suited for handling aggressive conditions like high pressure and temperature.
Pros:
Excellent for high-pressure systems.
Can handle high temperatures, making them suitable for steam and industrial processes.
Cons:
Not ideal for viscous fluids as the piston may have difficulty lifting.
More complex design compared to other types, leading to higher maintenance needs.
Diaphragm Check Valves
Diaphragm check valves use a flexible diaphragm that opens and closes to control the flow of fluid. The diaphragm flexes under forward pressure, allowing the flow to pass, and seals the valve when the pressure drops or reverses. These valves are highly suited for handling sensitive or corrosive fluids.
Uses: Diaphragm check valves are frequently used in systems that handle corrosive or chemical fluids, especially in low-pressure environments. They are popular in industries like pharmaceuticals, food processing, and chemical production.
Pros:
Excellent for handling corrosive fluids and chemicals.
The flexible diaphragm prevents leaks and ensures a tight seal, even with sensitive fluids.
Cons:
Less suitable for high-pressure systems due to potential diaphragm damage.
Diaphragms may require replacement after extended use, especially in harsh chemical environments.
Wafer Check Valves
Wafer check valves are compact and designed to fit between two flanges in a pipeline. They are typically much thinner and lighter than other valve types, making them ideal for space-constrained applications. Wafer check valves often use a disc or plate that moves forward and backward to control the flow of fluid.
Uses: These valves are commonly used in pipelines where space is limited, such as industrial systems, water distribution, and marine applications. They are also favored for their ease of installation and cost-effectiveness.
Pros:
Lightweight and compact, making them ideal for tight spaces.
Easier and faster to install compared to other check valves.
Cost-effective for applications with limited space or budget.
Cons:
Not suitable for all pressure ranges, particularly in high-pressure systems.
Limited durability in applications that experience frequent pressure fluctuations.
Piston Check Valves
Piston check valves use a cylindrical piston that moves vertically inside the valve body to control fluid flow. As forward pressure increases, the piston lifts, allowing flow. When reverse pressure occurs, the piston moves downward to close the valve. This design provides excellent sealing for high-pressure systems.
Uses: Piston check valves are commonly used in high-pressure applications, including steam and industrial fluid systems. Their robust construction makes them highly suitable for handling extreme conditions.
Pros:
Reliable in high-pressure environments.
Provides a tight seal, preventing any backflow in critical systems.
Cons:
Regular inspection and maintenance are required to ensure optimal performance.
The piston mechanism can wear out over time, especially in harsh conditions.
Silent or Spring-Loaded Check Valves
Silent, or spring-loaded, check valves incorporate a spring mechanism that ensures quick closure when reverse flow is detected. The spring forces the valve shut almost immediately when the forward pressure drops, preventing backflow. These valves are particularly effective in systems where minimizing noise and preventing water hammer (the shockwave caused by sudden valve closure) is critical.
Uses: Silent check valves are used in systems requiring quick backflow prevention, such as HVAC systems, fuel lines, and applications where water hammer prevention is essential.
Pros:
Fast-acting closure prevents water hammer and other pressure-related issues.
Quiet operation, making them ideal for environments sensitive to noise.
Cons:
Higher initial cost compared to standard check valves due to the inclusion of the spring mechanism.
The spring may weaken over time, requiring replacement for continued effectiveness.
Key Uses for Check Valves in Different Industries
Water and Wastewater Systems
In water and wastewater systems, check valves play a critical role in maintaining clean and efficient operations. The primary function of check valves in these systems is to ensure unidirectional flow, preventing contamination from backflow. In potable water systems, it is crucial to avoid any reversal of flow that could introduce contaminants into the clean water supply. Check valves are installed at key points in the system to protect against potential backflow events caused by pressure fluctuations or pump failure.
In wastewater systems, check valves help maintain proper flow control, ensuring that sewage or industrial waste does not flow backward into the treatment plant or contaminate clean water supplies. Check valves in these applications are often used in combination with pumps to prevent damage from reverse flow when the pumps are not running. They ensure the consistent movement of water and wastewater, keeping treatment processes efficient and preventing environmental harm.
Oil and Gas Pipelines
In the oil and gas industry, pipelines carry valuable and often hazardous materials over long distances. Ensuring the safe and efficient transport of these materials is a top priority, and check valves play a vital role in preventing backflow, which could cause leaks, contamination, or even explosions. Check valves are commonly installed in both upstream and downstream operations to protect pumps and compressors from the risk of reverse flow, which could damage equipment or disrupt the entire system.
In oil and gas pipelines, check valves also prevent the mixing of different media within the system. For instance, in gas separation processes, the valves ensure that only the desired gas flows forward while preventing the backward movement of liquids or other gases that could compromise the integrity of the process. The reliability and durability of check valves in high-pressure environments make them indispensable in this industry.
Chemical Processing
The chemical processing industry requires precise flow control and protection from backflow to maintain safety and product quality. Check valves are essential in these systems, especially in handling corrosive chemicals that could damage equipment or cause dangerous reactions if not properly contained. The correct selection of check valves is crucial in this context, as the materials used for the valve must be compatible with the chemicals in the system to avoid corrosion or degradation over time.
In chemical plants, check valves prevent the backward flow of chemicals into sensitive equipment such as pumps, reactors, and mixers. This ensures that chemical processes remain stable and efficient, while also protecting workers and the environment from potential exposure to hazardous substances. Diaphragm check valves are often used in these applications due to their ability to handle corrosive fluids while maintaining a tight seal to prevent leaks.
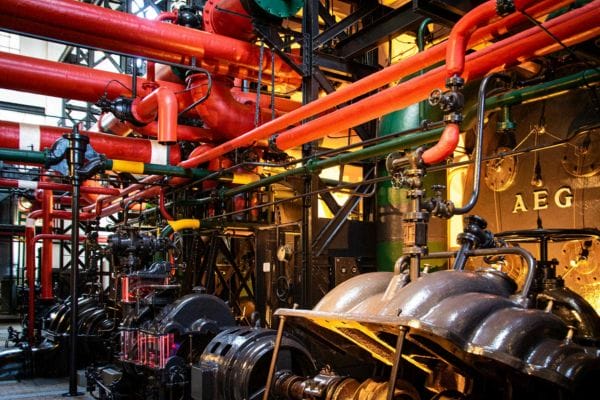
HVAC Systems
In heating, ventilation, and air conditioning (HVAC) systems, maintaining proper airflow and fluid circulation is essential for efficient operation. Check valves are commonly used in these systems to prevent the reverse flow of air or refrigerants, ensuring that HVAC units operate as designed without energy loss or mechanical damage. Swing check valves are often installed in ductwork or piping systems to maintain unidirectional flow, allowing air or fluids to circulate freely in the correct direction while closing off when flow reverses.
Silent or spring-loaded check valves are also popular in HVAC systems due to their ability to close quickly and quietly, preventing the occurrence of water hammer or other pressure surges that could damage equipment. These valves are essential in preventing refrigerant from flowing backward in cooling systems, ensuring the compressor remains protected. The fast closure of silent check valves reduces system noise, making them a preferred choice in noise-sensitive environments such as offices or residential buildings.
Key Selection Tips for Check Valves
Pressure and Flow Considerations
When selecting a check valve, one of the most critical factors to consider is the system’s pressure and flow rate. Each type of check valve operates differently under varying pressure conditions, and choosing the right one ensures efficient and reliable performance.
Pressure: Check valves must withstand the system’s operating pressure without failure. For high-pressure systems, such as steam applications or hydraulic lines, robust valves like pistons or lift check valves are more suitable due to their ability to handle high pressure. In contrast, low-pressure systems, such as water pumps or HVAC systems, can utilize ball or swing check valves, which are typically more cost-effective and designed for moderate pressure conditions.
Flow Rate: The flow rate of the system determines how easily the fluid or gas will pass through the check valve. Valves like swing check valves are ideal for systems with higher flow rates since they allow full, unobstructed flow. On the other hand, ball and piston check valves can handle moderate to lower flow rates but may restrict flow more than other types. Ensure that the valve selected does not cause a significant pressure drop in the system by impeding flow.
To properly size the valve, evaluate the system’s flow rate and pressure requirements in conjunction with the valve’s specifications. If the flow rate is too high for a given valve, it could result in damage or inefficient operation, while choosing a valve with a lower capacity could lead to restricted flow or premature failure.
Material Compatibility
The material of the check valve is another crucial consideration, especially when dealing with corrosive or abrasive environments. The valve’s material must be compatible with the fluid or gas it will control to avoid corrosion, wear, or degradation over time.
Stainless Steel: Stainless steel valves are highly resistant to corrosion, making them ideal for handling aggressive fluids, such as chemicals, seawater, or acidic solutions. Stainless steel check valves are commonly used in chemical processing plants, marine applications, and food processing industries where sanitary conditions and corrosion resistance are vital.
Brass: Brass check valves are widely used in plumbing and water systems due to their affordability, good corrosion resistance, and durability. They are effective in moderate-temperature environments but may not perform well with highly corrosive fluids.
Plastic (PVC or Polypropylene): For lower-pressure systems and applications handling mildly corrosive fluids, plastic check valves can be a cost-effective solution. They are often used in wastewater treatment, aquariums, and certain chemical processing applications. However, plastic valves are not suitable for high-temperature or high-pressure environments due to their lower heat and pressure tolerance.
Other Materials: In some cases, other specialized materials like bronze, carbon steel, or alloy materials may be required based on specific industry needs. For example, bronze valves are often used in marine applications for their superior resistance to seawater corrosion.
Selecting the correct material ensures the longevity of the valve and prevents potential leaks or failures due to corrosion or chemical incompatibility. Always check the chemical compatibility of the material with the system fluid.
Valve Type Selection
Selecting the right valve type depends on the characteristics of the system, including flow rate, pressure, and the desired function of the valve. Each type of check valve offers unique benefits, and choosing the wrong one can lead to inefficiency or system failure.
Ball Check Valves: Ball check valves are simple, reliable, and best for low-pressure systems with clean fluids. However, they may not be suitable for systems with high flow rates or viscous fluids, as the ball mechanism can create resistance.
Swing Check Valves: Swing check valves are ideal for high-flow systems, such as HVAC or water treatment plants. Their disc swings open fully, allowing unrestricted flow. However, they may require more frequent maintenance due to the wear on the hinge or pivot.
Lift Check Valves: Lift check valves, with their piston or disc mechanism, are designed for high-pressure environments, such as steam or compressed air systems. They are excellent for handling high-pressure fluids but are less effective for viscous or particulate-laden fluids.
Diaphragm Check Valves: For handling corrosive or sensitive fluids, diaphragm check valves are an excellent choice. Their flexible diaphragm design prevents leaks and can handle abrasive or chemically aggressive fluids, making them ideal for chemical processing.
Wafer Check Valves: Wafer check valves are compact and suitable for space-constrained applications like pipelines, but they are not always suitable for very high-pressure systems.
Silent or Spring-Loaded Check Valves: These valves are best suited for systems requiring quick backflow prevention, such as HVAC or fuel lines. They close rapidly and quietly, preventing water hammers but come at a higher cost.
Installation Space
Space constraints can significantly influence the choice of check valves. In many industrial systems, particularly pipelines or marine environments, there may be limited space for valve installation. Compact valve types, such as wafer check valves or piston check valves, are ideal in such scenarios. Wafer check valves are thin and designed to fit between two flanges, minimizing the need for extra space while still offering reliable performance.
If space is not a constraint, more traditional valve designs like swing or ball check valves can be used. However, always consider how the valve’s size and shape will affect the installation and the system’s layout. Failure to account for space limitations can lead to installation difficulties or necessitate system redesigns.
Maintenance Requirements
Maintenance is an important factor to consider when selecting a check valve. Depending on the system and environment, some valve types may require more frequent maintenance, while others can offer longer service intervals.
Swing Check Valves: These valves often require more maintenance due to the wear and tear on the hinge or pivot. Regular inspection is needed to ensure the disc swings freely and seals properly.
Ball Check Valves: These are low-maintenance valves due to their simple design with few moving parts. However, over time, the ball or seat may experience wear, especially in systems with particulate matter.
Diaphragm Check Valves: The diaphragm may require replacement in chemical applications where exposure to harsh fluids can degrade the material. However, they offer excellent sealing and reduced maintenance in many low-pressure systems.
Silent Check Valves: Spring-loaded check valves are low-maintenance but may require occasional inspection to ensure the spring mechanism functions correctly. They are known for long service life with minimal intervention.
Selecting a valve that aligns with your system’s maintenance capabilities can reduce downtime and operating costs. If regular maintenance is challenging, selecting a low-maintenance valve type may be more advantageous.
Special Considerations for Vertical or Horizontal Installations
The orientation of the valve during installation is another critical factor. Some check valves are designed to function best in horizontal installations, while others are suitable for both vertical and horizontal orientations.
Horizontal Installations: Valves like swing check valves typically perform well in horizontal pipelines, as the disc can swing freely with gravity.
Vertical Installations: Lift check valves, ball check valves, and spring-loaded check valves are often more effective in vertical installations, where gravity or spring force assists with valve closure. In these installations, it is crucial to ensure that the flow direction corresponds with the valve’s design.
Conclusion
Understanding the specific function of each check valve type allows you to make informed decisions based on your system’s needs, whether dealing with corrosive chemicals, high-pressure environments, or space-constrained installations. Regular maintenance requirements should also be factored in, ensuring that the chosen valve is not only efficient but also manageable for ongoing serviceability.
FAQ
What is a check valve?
A check valve is a mechanical device that allows fluid or gas to flow in one direction while preventing reverse flow.
Where are check valves commonly used?
Check valves are used in industries like water treatment, oil and gas, chemical processing, HVAC systems, and food and beverage processing.
How does a check valve prevent backflow?
Check valves use a disc, ball, or piston that closes when reverse pressure is applied, stopping the flow from going backward.
What factors should be considered when choosing a check valve?
Key factors include system pressure, flow rate, material compatibility, valve type, installation space, and maintenance needs.
Can check valves be installed vertically or horizontally?
Yes, certain types of check valves, such as ball and lift check valves, can be installed vertically or horizontally, depending on the design.
What materials are check valves made from?
Check valves are made from materials like stainless steel, brass, plastic, and other alloys, chosen based on the fluid and environmental conditions they will handle.