Internal leakage occurs when the valve fails to completely seal, allowing fluid to pass through even when it is in the closed position. This can compromise the system’s efficiency, raise operational costs, and even lead to safety risks in critical systems.
Understanding Ball Valve Internal Leakage
Definition of Internal Leakage
Internal leakage in a ball valve occurs when fluid escapes within the valve body itself, passing through the ball and seat interface even when the valve is in the closed position. This is different from external leakage, where fluid leaks from the valve body into the surrounding environment due to issues with seals or body connections. Internal leakage typically occurs when the ball or seat seals within the valve wear down, corrode, or become damaged, compromising the valve’s ability to form a complete seal. The result is unintended flow through the valve, impacting the controlled flow that the system requires.
Impact on Systems
Internal leakage in a ball valve can have a significant impact on a fluid control system, leading to a range of operational and financial challenges:
Reduced Efficiency: When a ball valve leaks internally, it allows fluid to bypass the intended closed-off state, which can decrease the system’s efficiency. For example, in a pressurized system, internal leakage can reduce flow control precision and make it harder to maintain desired pressure levels.
Safety Risks: In systems handling hazardous or high-pressure fluids, internal leaks can pose serious safety risks. Uncontrolled leakage may lead to unplanned pressure build-up, overheating, or exposure to harmful substances, which can endanger personnel and equipment.
Increased Maintenance Costs: Constant internal leakage accelerates wear on the valve components, often leading to frequent repairs or replacements. Regular maintenance to address leakage issues can become costly, especially in systems with multiple valves.
System Downtime: When leaks go undetected or worsen, they can lead to unplanned downtime for repairs. In critical operations, this downtime can cause operational delays, impact production targets, and increase overall costs.
In severe cases, repeated internal leakage may require a full valve replacement if the issue cannot be resolved through regular maintenance or part replacements. Understanding these impacts underscores the importance of prompt detection and repair.
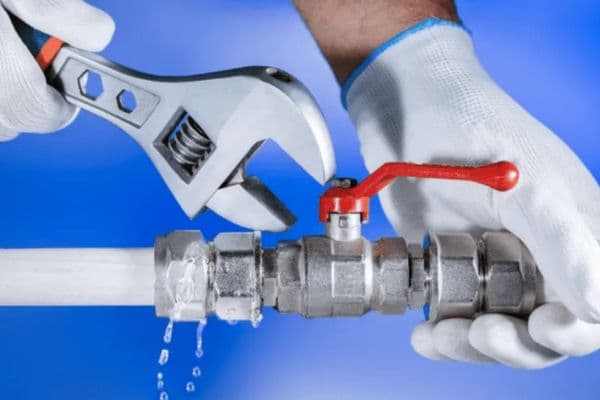
Symptoms of Internal Leakage
Identifying internal leakage early can prevent further system issues and allow for timely repairs. Here are some key indicators of internal leakage:
Unusual Pressure Drops: A sudden or unexplained drop in pressure could indicate that fluid is escaping within the valve. If pressure levels cannot be maintained or controlled as expected, it may be due to internal leakage within one or more ball valves in the system.
Continuous Flow When Closed: If a ball valve continues to allow fluid through even in its fully closed position, this is a clear sign of internal leakage. This could manifest as a small trickle or drip, which may increase over time if the valve components are further damaged or worn.
Irregular Fluid Levels: In closed systems where fluid levels are carefully monitored, unexpected fluctuations can indicate an internal leak. When fluid levels change without explanation, it could mean that fluid is escaping internally through a closed valve.
Temperature Variations: Internal leakage can cause unusual temperature fluctuations within a system, especially in applications where fluid flow affects cooling or heating. For instance, if coolant flow is leaking within a closed valve, temperatures may rise unexpectedly, impacting system stability.
Noise or Vibration: In some cases, internal leakage can produce subtle sounds or vibrations as fluid passes through small gaps. Listening for unusual sounds near closed valves during regular inspections can sometimes help identify leaks before they worsen.
Common Causes of Internal Leakage in Ball Valves
Worn Seals or Seats
How and Why Seals Become Worn
The seals or seats inside a ball valve are essential for achieving a leak-tight seal when the valve is in the closed position. Over time, these components are prone to wear, which can compromise their sealing ability and lead to internal leakage. Seals and seats wear down for several reasons:
Aging: As seals age, they become less resilient and may start to crack or harden. Elastomer-based seals, such as rubber, are especially susceptible to aging, which can lead to a decline in their sealing efficiency.
Exposure to Harsh Chemicals: In systems that handle corrosive or chemically reactive fluids, seals may degrade prematurely due to chemical exposure. Harsh chemicals can erode seal materials, causing them to break down faster than expected, which opens gaps for fluid to escape.
Regular Operation and Abrasion: Each time a ball valve is opened or closed, the seals or seats experience a degree of friction against the ball. Over time, this friction leads to abrasion, which gradually wears down the surfaces. This effect is amplified in high-cycle applications, where the valve is frequently operated.
How Worn Seals Lead to Leakage
When seals or seats wear down, they can no longer maintain a tight seal, allowing fluid to pass through when the valve is closed. This internal leakage can worsen as the seals degrade further, increasing maintenance needs and potentially requiring full replacement of the valve.
Corrosion and Erosion
Effects of Corrosive and Abrasive Fluids
Corrosion and erosion are significant causes of internal leakage, especially in systems handling chemically aggressive or abrasive substances. Corrosion occurs when the valve material reacts with corrosive fluids, leading to the gradual breakdown of metal components. Over time, this weakens the structural integrity of the ball, seats, and seals. Erosion, on the other hand, happens when abrasive particles in the fluid wear down valve surfaces, leading to gaps and pitting.
How Corrosion and Erosion Cause Leakage
As corrosion or erosion progresses, it creates tiny channels or pits in the valve’s internal components, preventing a complete seal. This creates points where fluid can bypass the closed valve, resulting in internal leakage. Corrosion and erosion can be especially problematic in high-pressure systems, where even small imperfections can quickly expand under force, making leaks worse over time.
Poor Installation Practices
Effects of Incorrect Installation
Proper installation is crucial for ensuring that a ball valve operates effectively. Mistakes during installation, such as misalignment of parts, incorrect tightening, or failure to follow recommended torque specifications, can lead to premature valve failure and internal leakage. Here’s how specific installation errors contribute to leakage:
Misalignment: When the valve components are not properly aligned, the ball may not sit flush with the seats, preventing an effective seal. This gap allows fluid to bypass the seal, even when the valve is closed.
Over- or Under-tightening: If bolts or other fasteners are overtightened, it can compress or damage the valve seats, impairing their ability to form a seal. Under-tightening, on the other hand, may lead to loose components that shift during operation, causing leakage.
How Installation Errors Lead to Leakage
These installation errors can prevent the ball from fully closing off the flow, creating gaps in the valve’s internal seal. To avoid these issues, it is essential to follow manufacturer guidelines for installation, torque settings, and alignment, and to use trained personnel for the installation process.
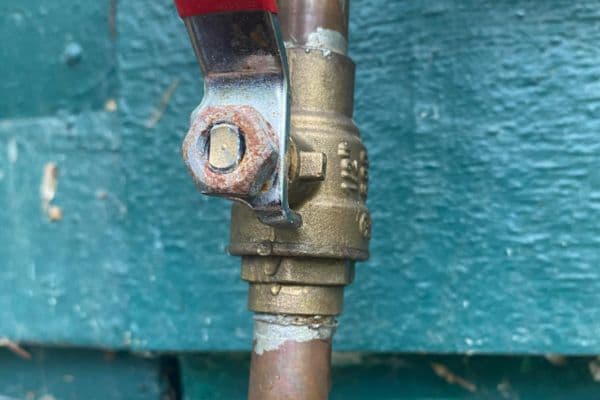
Pressure and Temperature Variations
Impact of Pressure and Temperature Extremes
Extreme or fluctuating pressures and temperatures can weaken valve components and contribute to internal leakage. High pressure can deform or warp valve seats and seals, especially if the valve is not rated for the specific operating pressure. Similarly, extreme temperatures can cause seals to expand, contract, or lose elasticity, leading to a compromised seal.
How Variations Cause Leakage
When pressure or temperature exceeds the valve’s design specifications, the integrity of the sealing surfaces is often compromised. For instance, high pressure can push the ball against the seats with excessive force, causing deformation. As the valve cycles through extreme temperatures, the expansion and contraction of materials can also create micro-gaps that allow fluid to bypass the closed valve. To avoid this, it’s essential to choose valves rated for the specific pressures and temperatures they will encounter.
Damage from Handling or Transportation
Risk of Damage During Shipping and Installation
Valves can sustain damage during shipping, handling, or installation, which may lead to internal leakage. Impacts, drops, or improper handling can damage the delicate sealing surfaces or misalign the internal components, which compromises the valve’s ability to achieve a tight seal.
How Handling Damage Leads to Leakage
If the ball or seats are damaged or misaligned, the valve may not close properly, resulting in leakage. Even minor dents or scratches can disrupt the valve’s ability to form a complete seal. Ensuring that valves are carefully handled during transport and storage is essential to maintain their performance.
Material Incompatibility
Selecting the Right Materials for the Fluid Type
Using incompatible materials for specific fluid or environmental conditions can lead to premature valve failure and internal leakage. For instance, a valve designed for water may not perform well in a system carrying corrosive chemicals or abrasive slurries. Material incompatibility often results in accelerated degradation of the valve components, particularly the seals and seats.
How Incompatibility Leads to Leakage
When the valve’s materials are not suited to the fluids they are exposed to, chemical reactions or physical wear can damage internal components. This compromises the seal integrity and leads to leaks. For example, if a rubber seal is used with a hydrocarbon-based fluid, the seal may swell, harden, or deteriorate, resulting in leakage. Choosing materials specifically suited to the application’s fluid properties is essential for long-lasting performance and leak prevention.
Solutions for Fixing Internal Leaks in Ball Valves
Internal leakage in ball valves can disrupt system efficiency, increase maintenance costs, and compromise safety. Addressing the root causes of these leaks and implementing solutions tailored to your system’s needs can prevent recurring issues.
Replacing Worn Seals or Seats
Worn or degraded seals and seats are among the most common causes of internal leakage in ball valves. Replacing these parts can often restore the valve’s integrity.
Step-by-Step Guide to Replace Seals and Seats:
Preparation: Ensure the system is depressurized and drained. Close off any fluid flow to the valve and disconnect it from the pipeline.
Disassembly: Use the manufacturer’s instructions to disassemble the valve. Remove the handle or actuator, then access the valve body by removing bolts or screws.
Remove the Old Seals and Seats: Carefully extract the worn seals and seats from the valve body. Note their positions and orientation.
Inspect the Valve Components: Check for any other signs of damage, such as corrosion on the ball or scratches on the sealing surfaces.
Install New Seals and Seats: Place the replacement seals and seats in the correct positions. Ensure they are correctly aligned to provide a tight seal.
Reassemble the Valve: Reattach the valve body, handle, and any removed parts, following the manufacturer’s torque specifications.
Testing: Once the valve is reinstalled, conduct a leak test to verify that the internal leakage has been resolved.
Regularly inspecting and replacing seals can help maintain valve performance, especially in high-cycle or high-pressure applications.
Cleaning and Maintenance
Over time, debris, sediment, or chemical residues can accumulate inside ball valves, especially in systems handling abrasive or viscous fluids. Regular cleaning and maintenance are essential for preventing buildup that can wear down seals or interfere with proper closure.
Cleaning Routine for Ball Valves:
Flush the System: Periodically flush the system with a compatible cleaning agent to remove debris. This is especially important for systems handling viscous or particulate-laden fluids.
Inspect and Wipe Down Seals: During maintenance, inspect the seals and seats for buildup or wear. If buildup is present, clean the surfaces with a soft cloth and a solvent recommended for the seal material.
Lubrication: For valves with metal seats, apply a lubricant compatible with the valve material to reduce friction and prevent premature wear. Ensure that the lubricant does not degrade the seal material.
Corrosion Prevention: For valves exposed to corrosive environments, apply a corrosion inhibitor as recommended by the manufacturer. This will protect exposed metal parts and reduce the risk of leaks.
Tips for Maintaining Seal Materials:
For Rubber Seals: Avoid using solvents or cleaners that could cause swelling or hardening.
For PTFE Seals: PTFE is highly resistant to chemicals but should still be inspected for cracks or wear, especially in high-temperature applications.
For Metal Seals: Keep them lubricated and check for signs of corrosion, particularly in applications with aggressive chemicals.
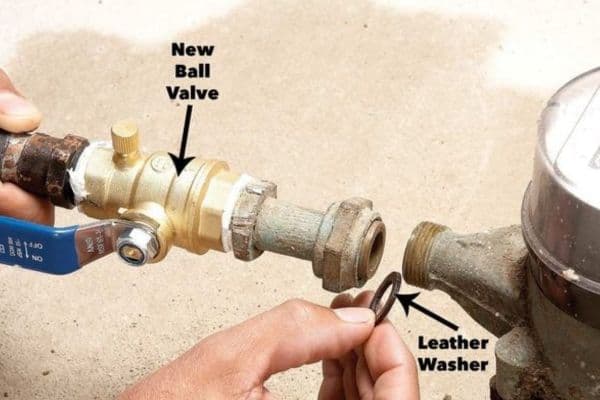
Correcting Installation Issues
Improper installation can result in misalignment or damage that leads to internal leaks. Follow this checklist to ensure proper valve installation.
Installation Checklist:
Alignment: Confirm that the valve is aligned correctly with the pipeline. Misalignment places stress on the seals and seats, compromising their ability to seal fully.
Torque Requirements: Tighten bolts and connectors to the manufacturer’s recommended torque. Over-tightening can deform seals, while under-tightening may leave components loose.
Seating Adjustments: Ensure that the ball and seats are properly aligned during installation. Misaligned seats can lead to internal leakage.
Avoid Excessive Force: Use the correct tools and avoid applying excessive force when handling sensitive parts like seals and seats.
By following proper installation procedures, operators can prevent premature valve wear and improve the longevity of the seals and seats, minimizing the risk of internal leaks.
Material Upgrades
The materials used in ball valves play a critical role in their ability to withstand specific operating conditions. Upgrading to more durable materials can help reduce the risk of leaks, especially in aggressive or high-pressure environments.
Choosing the Right Materials:
Stainless Steel: For systems exposed to corrosive fluids or extreme temperatures, stainless steel provides excellent corrosion resistance and can withstand temperature fluctuations.
PTFE-Coated Seals: PTFE coatings offer high chemical resistance and reduce friction. PTFE seals are ideal for applications with chemical exposure or high temperatures.
Hardened Metal Seals: In high-pressure or abrasive environments, hardened metal seals may be preferred over softer materials like rubber or elastomers, which wear down more quickly.
Ceramic Coatings: For particularly harsh environments, ceramic-coated balls and seats offer exceptional durability against erosion and chemical attack.
By selecting materials that match the operating environment, operators can enhance the valve’s performance and reduce the frequency of internal leaks.
Pressure and Temperature Adjustments
Extreme or fluctuating pressures and temperatures can stress valve components, leading to deformation, wear, and leakage. Adjusting these parameters can help protect valve components.
Adjustments to Reduce Stress on Valve Components:
Pressure Dampening: Use pressure dampening devices or adjust system pressure settings to reduce the impact on valve components. This is especially useful in systems with high-pressure surges.
Temperature Control: Maintain consistent temperatures or install temperature controls to prevent excessive expansion or contraction of valve materials. In some cases, insulating the valve or pipeline can help maintain a stable temperature.
Pressure Relief Valves: Install pressure relief valves to prevent excessive pressure buildup within the system, which can protect seals and seats from damage.
By optimizing pressure and temperature settings, operators can significantly reduce the stress on valve components, extending the life of the valve and reducing leakage.
Reinforcing Valve Design
For systems under high pressure or where frequent leaks have been an issue, upgrading to a more robust valve design may be a practical solution. Trunnion-mounted ball valves and reinforced seals are examples of design improvements that can reduce leakage risks.
Advantages of Reinforced Valve Designs:
Trunnion-Mounted Ball Valves: Unlike floating ball valves, trunnion-mounted designs secure the ball in place, reducing wear on the seals and seats. This design is ideal for high-pressure applications as it minimizes the stress placed on sealing surfaces.
Double Block and Bleed: For critical applications, a double block and bleed design allows for a secondary seal, reducing leakage risks. This setup provides additional isolation and enables operators to detect and relieve any trapped pressure.
Metal-Reinforced Seals: In applications with high wear or chemical exposure, metal-reinforced seals provide additional durability and can handle higher pressures without deforming.
Conclusion
Proactive inspection and maintenance are key to extending the life of your ball valves and preserving system efficiency. By addressing potential issues early, you can avoid costly repairs, unplanned downtime, and operational disruptions. Schedule regular inspections, stay vigilant for signs of internal leakage, and take prompt action when needed.
FAQ
What causes internal leakage in ball valves?
Internal leakage is often caused by worn seals, corrosion, improper installation, extreme pressure or temperature fluctuations, and material incompatibility.
How can I tell if a ball valve is leaking internally?
Signs of internal leakage include unusual pressure drops, continuous flow when the valve is closed, irregular fluid levels, and strange noises or vibrations near the valve.
Can internal leakage be fixed by replacing seals or seats?
Yes, replacing worn or damaged seals and seats is a common solution to restore a ball valve’s sealing capability and stop internal leaks.
What maintenance can prevent internal leakage in ball valves?
Regular inspections, cleaning, lubrication, and checking for proper alignment during installation can help prevent internal leakage.
What materials are best to avoid internal leakage?
Materials like stainless steel, PTFE-coated seals, and corrosion-resistant alloys are excellent choices for preventing leaks in harsh conditions.
When should I consider replacing a leaking ball valve?
If a valve has persistent leaks despite repairs, or if it shows significant wear, corrosion, or structural damage, it may be time to replace it.