What Does NPT Mean in Plumbing System?
Introduction
It’s crucial to understand the concept of NPT because it’s a common standard used in plumbing systems to ensure a leak-proof seal in your plumbing system. This article will take a comprehensive look at NPT threads, explaining what they are, what they mean in the plumbing industry, and how they are used in various applications.
Understanding NPT
Definition of NPT
NPT, or National Pipe Tapered threads, is a standardized threading system used in plumbing and piping applications to ensure a secure, leak-proof connection. The term “National Pipe Tapered” indicates that the threads are tapered, meaning they gradually decrease in diameter along the length of the thread. This tapering allows for a tighter seal as the threads are screwed together, which is critical for preventing leaks in fluid and gas systems.
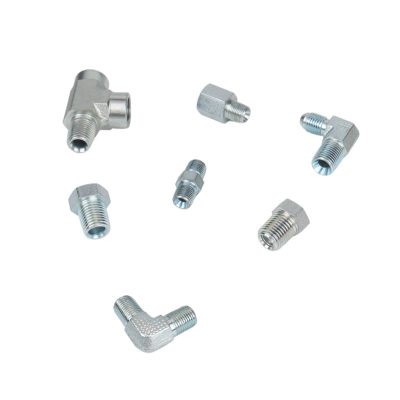
Historical Background and Development of NPT Standards
The NPT standard originated in the United States in the late 1800s during the industrial revolution, a time when the need for standardized piping systems became increasingly important due to rapid industrial growth. Before the establishment of NPT, there was a lack of uniformity in pipe threads, which led to frequent leaks and failures in piping systems. Engineers and industry leaders recognized the need for a consistent standard, which led to the development of NPT threads.
Technical Specifications
The tapered design of NPT threads is a key feature that distinguishes them from other types of pipe threads. The taper of NPT threads is designed at an angle of 1°47′ from the center axis. This design causes the diameter of the threads to decrease gradually along the length of the pipe, allowing the threads to form a tighter, more secure fit as they are engaged.
When two NPT-threaded components are screwed together, the taper causes the threads to compress and form a seal. This mechanical seal is enhanced when a thread sealant, such as PTFE tape or pipe dope, is applied to the threads before assembly. The sealant fills any small gaps between the threads, further preventing leaks.
The Role of NPT in Plumbing
Functionality of NPT Threads
NPT threads are specifically designed to create a tight, leak-proof seal through their unique tapered structure. As the threads of a male NPT component are screwed into a female NPT component, the taper causes the threads to compress against each other. This compression increases the surface contact between the threads, which helps to form a mechanical seal. Additionally, the use of thread sealants, such as PTFE tape (commonly known as Teflon tape) or pipe dope, enhances this seal by filling in any small gaps between the threads. The combination of the mechanical fit and the sealant ensures a secure, leak-proof connection that is essential in plumbing applications where fluid or gas leakage must be prevented.
Comparison with Straight Threads
Unlike NPT threads, straight threads (often referred to as parallel threads) maintain a consistent diameter along their entire length. While straight threads can provide a strong mechanical connection, they do not inherently create a seal. For straight threads to be leak-proof, additional sealing mechanisms, such as O-rings or gaskets, are typically required. In contrast, the tapered design of NPT threads eliminates the need for these additional sealing elements, as the taper itself creates the necessary compression to form a seal. This makes NPT threads particularly advantageous in plumbing applications where simplicity and reliability are critical.
Applications in Plumbing
NPT threads are widely used in both residential and commercial plumbing systems due to their reliability and ease of use. In residential settings, NPT threads are commonly found in water supply lines, gas lines, and various plumbing fixtures such as faucets and showerheads. The tapered threads ensure a tight seal, which is crucial for preventing leaks and maintaining the integrity of the plumbing system.
In commercial and industrial settings, NPT threads are used in a broader range of applications, including high-pressure steam systems, chemical processing lines, and large-scale water distribution networks. The ability of NPT threads to withstand high pressure and provide a secure seal makes them ideal for these demanding environments. Additionally, the standardized nature of NPT threads ensures compatibility across various components and systems, simplifying maintenance and repairs.
Examples of NPT threaded Components
Pipes: NPT threads are commonly used on the ends of pipes to allow for secure connections with other pipes or fittings. These threaded pipes are available in various materials, including galvanized steel, stainless steel, brass, and PVC, to suit different applications and environmental conditions.
Fittings: NPT-threaded fittings, such as elbows, tees, and couplings, are essential for directing the flow of fluids and gases within a plumbing system. These fittings are designed to connect pipes at various angles and configurations, making it possible to create complex plumbing networks.
Valves: Valves with NPT threads are used to control the flow of fluids and gases in a plumbing system. Examples include ball valves, gate valves, and check valves. The threaded connections ensure that the valves can be securely installed and easily replaced or serviced when needed.
Pressure Gauges: In many plumbing systems, pressure gauges with NPT threads are used to monitor the pressure of fluids or gases. These gauges provide critical information for maintaining system safety and efficiency, and the threaded connections ensure accurate readings and easy installation.
Pipe Nipples: These short lengths of pipe with NPT threads on both ends are used to connect other threaded components, such as fittings or valves, within a plumbing system. They come in various lengths and materials to match the specific requirements of the application.
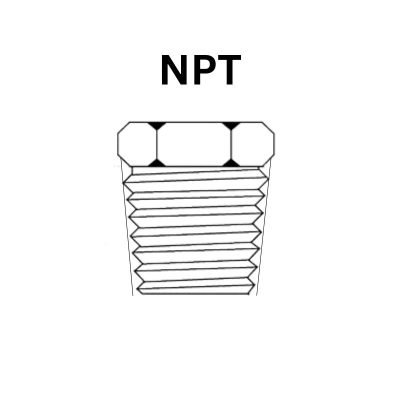
Types of NPT Thread
Understanding the different types of NPT threads is essential for selecting the right components for various plumbing applications. While all NPT threads share the same basic tapered design, they can be categorized based on their specific features and applications. Here are the main types of NPT threads:
NPTF
Also known as “Dryseal” threads, NPTF threads are designed to provide a leak-proof seal without the need for sealants such as PTFE tape or pipe dope. The threads are manufactured to closer tolerances than standard NPT threads, allowing them to form a dry mechanical seal.
Application: Often used in hydraulic and pneumatic systems where the use of sealants is undesirable or where a more reliable seal is required. NPTF threads are ideal for applications involving fuel and other fluids where leakage cannot be tolerated.
NPS
Unlike NPT threads, NPS threads are straight (parallel) threads and do not taper. They do not create a seal on their own and typically require an O-ring or gasket to form a leak-proof connection.
Application: Used in mechanical joints that do not require a seal through the threads themselves, such as in certain types of conduit or mechanical fittings. NPS threads are often used in conjunction with NPT threads for specific applications where a straight thread is necessary.
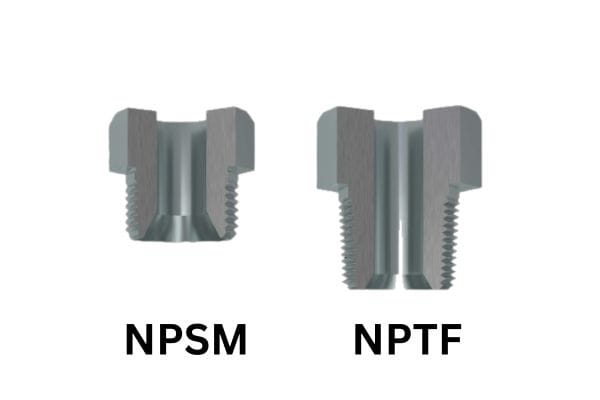
NPSC
NPSC threads are a subtype of NPS threads specifically designed for coupling applications. These threads are straight and are used to join two pipes or fittings together.
Application: Commonly used in piping systems where straight-threaded couplings are required. They are often used in conjunction with NPT-threaded components to provide a secure connection.
NPTR
NPTR threads are tapered threads similar to standard NPT, but they are specifically designed for use in railing systems. The thread design provides a secure, tight fit for the assembly of railings.
Application: Primarily used in the construction of metal railings, including handrails and guardrails. The tapered threads ensure a strong, stable connection in these structural applications.
NPSM
NPSM threads are straight threads that are typically used in mechanical and low-pressure applications. Like other straight threads, they do not form a seal on their own and usually require a sealing element.
Application: Used in applications where a mechanical connection is needed, but the threads themselves do not need to create a seal. Commonly found in various types of fittings and connectors in hydraulic and pneumatic systems.
NPT vs BSP
Thread Design:
NPT: Features a tapered thread design that provides a tight, leak-proof seal through the compression of threads as they are tightened. The taper angle is 1°47′.
BSP: Includes both parallel (BSPP) and tapered (BSPT) threads. BSPP threads are parallel and require a gasket or O-ring to seal, whereas BSPT threads are tapered and seal similarly to NPT threads.
Angle and Pitch:
NPT: Threads have a 60-degree angle.
BSP: Threads have a 55-degree angle.
Measurement:
NPT: Measured in inches, following the imperial system.
BSP: Measured in inches, but follows the Whitworth standard.
Standards:
NPT: Governed by ANSI/ASME B1.20.1.
BSP: Governed by various British and international standards, including ISO 228-1 (for BSPP) and ISO 7-1 (for BSPT).
Regional preferences and applications:
NPT: Predominantly used in the United States and Canada for plumbing, gas, and hydraulic systems.
BSP: Widely used in the United Kingdom, Europe, Asia, Australia, and other parts of the world. Commonly found in water and gas plumbing applications and hydraulic systems in these regions.
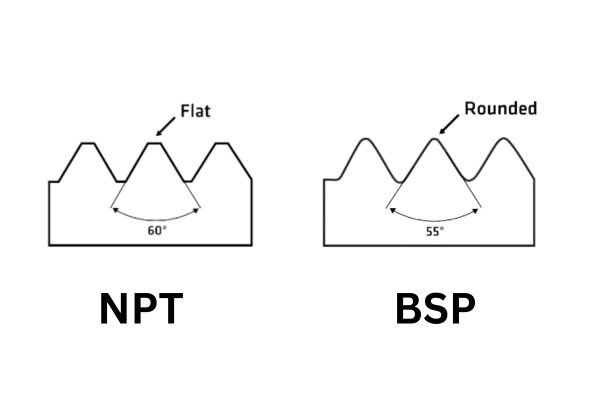
NPT vs Metric Threads
Thread Design:
NPT: Tapered threads that create a seal through thread compression.
Metric Threads: Generally straight (parallel) threads that require an additional sealing mechanism, such as an O-ring or gasket.
Angle and Pitch:
NPT: 60-degree thread angle.
Metric Threads: 60-degree thread angle, but the thread pitch (distance between threads) is measured in millimeters.
Measurement:
NPT: Measured in inches.
Metric Threads: Measured in millimeters, following the metric system.
Applications:
NPT: Common in North American plumbing and piping systems.
Metric Threads: Used internationally, particularly in automotive, machinery, and industrial applications where the metric system is standard.
NPT vs JIC
Thread Design:
NPT: Tapered threads designed to create a seal through thread compression.
JIC: Features a 37-degree flare-fitting design. JIC threads are straight and do not seal through the threads but rather through the metal-to-metal contact of the flared surfaces.
Sealing Mechanism:
NPT: Seals through the compression of tapered threads and often requires a sealant.
JIC: Seals through the flared surfaces of the fittings, creating a strong, reusable connection without the need for additional sealants.
Measurement:
NPT: Measured in inches.
JIC: Also measured in inches, but the fitting dimensions are standardized separately from thread measurements.
Understanding the differences between NPT and other thread standards like BSP, metric threads, and JIC is crucial for selecting the right components for your plumbing and piping systems. Each thread standard has unique features and applications, and choosing the correct type ensures compatibility, reliability, and efficiency in your specific use case.
Installation and Maintenance Tips
Preparing the Threads
Cleaning and Preparing Threads Before Assembly:
Proper preparation of threads is crucial for ensuring a secure and leak-proof connection. Here are the steps to follow:
Inspect the Threads: Before assembly, inspect both the male and female threads for any signs of damage, such as nicks, dents, or deformations. Damaged threads can compromise the seal and lead to leaks.
Clean the Threads: Use a wire brush or thread-cleaning tool to remove any debris, dirt, or old sealant from the threads. Clean threads ensure that the new sealant can adhere properly and that the threads can engage smoothly.
Dry the Threads: Ensure that the threads are dry before applying any sealant. Moisture can interfere with the effectiveness of the sealant and reduce the integrity of the seal.
Using Thread Sealant
PTFE Tape (Teflon Tape):
Application: Wrap the PTFE tape around the male threads in a clockwise direction (as viewed from the end of the pipe). Start from the end of the threads and overlap each wrap slightly. Typically, 2-3 wraps are sufficient for most applications.
Benefits: PTFE tape is easy to use, provides a good seal, and is suitable for a wide range of temperatures and pressures.
Pipe Dope (Thread Sealant Paste):
Application: Apply a thin, even layer of pipe dope to the male threads using a brush or applicator. Be careful not to apply too much, as excess sealant can squeeze out and contaminate the system.
Benefits: Pipe dope provides a strong seal and is often used in high-pressure and high-temperature applications. It remains pliable, making it ideal for applications where vibration or movement is expected.
Anaerobic Thread Sealant:
Application: Apply a small amount of anaerobic thread sealant to the male threads. This type of sealant cures in the absence of air, forming a strong bond.
Benefits: Anaerobic sealants provide excellent resistance to vibration and thermal cycling, making them suitable for industrial and automotive applications.
Proper Tightening Techniques
Avoiding Over-tightening and Ensuring a Proper Fit:
Hand Tightening: Start by hand-tightening the threaded components until they are snug. This ensures that the threads are properly engaged without cross-threading.
Using a Wrench: After hand-tightening, use a wrench to further tighten the connection. Generally, an additional 1-2 turns with a wrench are sufficient. Be cautious not to over-tighten, as excessive force can damage the threads and compromise the seal.
Checking for Proper Fit: After tightening, check that the connection is properly aligned and that the threads are fully engaged. If the connection feels loose or uneven, disassemble and inspect the threads for damage or debris before reassembling.
Conclusion
By mastering the basics of NPT threads and applying best practices for installation and maintenance, you can greatly improve the performance and reliability of your plumbing projects. Proper preparation, correct selection of sealants, and regular maintenance are key success factors. We invite you to share your experiences and insights on using NPT threads in your plumbing projects. Have you encountered specific challenges or found tips that have been beneficial to others? Please feel free to contact us and we will do our best to help you!
FAQ
NPT stands for National Pipe Tapered. It is a standardized threading system used in plumbing to create a tight, leak-proof seal through tapered threads.
NPT threads create a seal through their tapered design. As the threads are tightened, they compress against each other, forming a mechanical seal. Using a thread sealant like PTFE tape or pipe dope enhances the seal by filling any gaps.
Yes, PTFE tape is commonly used on NPT threads to enhance the seal. Wrap the tape clockwise around the male threads 2-3 times before assembling the connection to ensure a leak-proof fit.
NPT threads have a 60-degree angle and a tapered design, while BSP threads have a 55-degree angle and can be either parallel (BSPP) or tapered (BSPT). NPT is primarily used in North America, whereas BSP is widely used in Europe, Asia, and other regions.
NPT threads are tapered, meaning they gradually decrease in diameter. You can measure the threads with a thread gauge or visually inspect the taper. The pitch (distance between threads) is also measured in inches.
If an NPT connection leaks, depressurize the system and re-tighten the connection. Apply additional thread sealant if necessary. Check for any damage to the threads, clean them thoroughly, and ensure proper engagement before reassembling.