How Do Banjo Fittings Work?
Introduction
Banjo fittings, characterized by their distinctive round shape with a hollow bolt, are essential components in hydraulic and pneumatic systems. Their unique design allows for a fluid connection that can rotate 360 degrees, making them ideal for applications where space is limited, and flexible connections are necessary. This post aims to provide an in-depth understanding of how banjo fittings work. By exploring their design, working principles, applications, and maintenance, readers will gain comprehensive knowledge about these vital components.
Understanding Banjo Fittings
Banjo fittings are specialized connectors used in hydraulic and pneumatic systems to facilitate fluid flow between components. Their name derives from their distinctive shape, which resembles a banjo, with a circular fitting body and a bolt passing through its center. These fittings are crucial in applications where space constraints and flexibility are significant considerations, enabling a secure yet adaptable connection.
Design and Structure
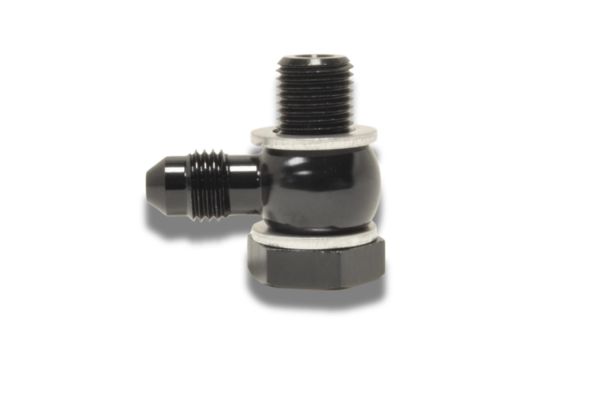
The design of banjo fittings is ingeniously simple yet highly effective, consisting of several key components that work together to ensure optimal performance:
Body: The body of a banjo fitting is typically circular with a hollow, cylindrical shape. It features an inlet and outlet for fluid flow, often connected to hoses or pipes. The body is designed to house the bolt and allow fluid to pass through while maintaining a secure connection.
Bolt: The bolt is a critical component that passes through the center of the fitting body. It is usually hollow, allowing fluid to flow through its center. The bolt has a threaded end that secures it in place and tightens the fitting. Holes along the bolt’s shaft enable fluid to pass into and out of the fitting body, ensuring continuous flow.
Eyelet: The eyelet, or the ring section of the fitting body, encircles the bolt. It allows the bolt to be secured within the fitting while providing an opening for fluid to flow through. The eyelet’s design ensures that the fitting can be tightened without restricting fluid flow.
Seals (O-rings): To prevent leaks and ensure a secure connection, banjo fittings are equipped with seals, typically made of rubber or synthetic materials. These O-rings fit snugly around the bolt and within the fitting body, creating a tight seal that prevents fluid from escaping and contaminants from entering the system.
Materials Used
Banjo fittings are constructed from various materials, chosen based on the application’s requirements and the fluids being transported. Common materials include:
Steel: Known for its strength and durability, steel banjo fittings are used in high-pressure applications and environments where robustness is essential.
Brass: Brass fittings offer excellent corrosion resistance and are often used in applications involving water or mildly corrosive fluids.
Aluminum: Lightweight and corrosion-resistant, aluminum banjo fittings are suitable for applications where weight reduction is crucial without sacrificing performance.
Sizes and Standards
Banjo fittings come in various sizes to accommodate different system requirements. Industry standards ensure compatibility and reliability across applications. Key standards include:
ISO: ISO standards provide globally recognized specifications for banjo fittings, ensuring quality and interoperability.
SAE: SAE standards are widely used in the automotive and aerospace industries, specifying dimensions, materials, and performance criteria for hydraulic fittings, including banjo fittings.
Working Principle of Banjo Fittings
Fluid Flow
The fluid flow within a banjo fitting is a key aspect of its functionality. The design allows fluid to enter and exit the fitting efficiently, maintaining a steady flow rate even under varying pressure conditions.
Pathway through the Bolt
The fluid enters the banjo fitting through the hollow bolt. This bolt is designed with a central passage that allows fluid to flow through its length. Along the bolt, there are strategically placed holes or ports that direct the fluid from the central passage into the fitting body. This design ensures that the fluid can move through the bolt without obstruction, facilitating a smooth and continuous flow.
Circular Flow within the Eyelet
Once the fluid exits the bolt through the ports, it enters the eyelet section of the fitting body. The eyelet provides a circular pathway around the bolt, allowing the fluid to flow freely in all directions. This circular flow ensures that the fluid can easily reach the outlet, even if the fitting is positioned in a tight or confined space. The design of the eyelet also helps to distribute the fluid evenly, reducing turbulence and maintaining a consistent flow rate.
Sealing Mechanism
The sealing mechanism in banjo fittings is critical to preventing leaks and ensuring the integrity of the hydraulic system.
O-rings: O-rings made from rubber or synthetic materials are used to create a tight seal around the bolt and within the fitting body. These O-rings are positioned at the points where the bolt passes through the fitting body, effectively sealing the connection. The elasticity of the O-rings allows them to compress and expand slightly, accommodating variations in pressure and temperature while maintaining a secure seal.
Compression Seals: In addition to O-rings, some banjo fittings use compression seals that are tightened as the bolt is secured. These seals create a tight fit between the bolt and the fitting body, preventing fluid from leaking out of the connection. The combination of O-rings and compression seals ensures a robust and reliable sealing mechanism, even under high-pressure conditions.
Pressure Handling
Banjo fittings are designed to handle varying levels of pressure, making them suitable for a wide range of applications.
High-Pressure Tolerance: Banjo fittings made from materials like steel and brass are capable of withstanding high pressures, often encountered in hydraulic systems. The design of the bolt and the eyelet ensures that the fitting can maintain its integrity under significant pressure without deforming or failing.
Low-Pressure Applications: For low-pressure applications, such as in certain fuel lines or medical equipment, aluminum banjo fittings are often used. These fittings are lightweight yet strong enough to handle the required pressure levels, ensuring reliable performance.
Pressure Ratings: Each banjo fitting comes with a specific pressure rating, indicating the maximum pressure it can handle safely. These ratings are determined based on industry standards and testing, ensuring that the fittings can perform as expected under specified conditions. It is essential to choose a banjo fitting with the appropriate pressure rating for your application to ensure safety and efficiency.
Applications of Banjo Fittings
Automotive Industry: Banjo fittings are extensively used in the automotive industry, particularly in brake systems and fuel lines.
Brake Systems: In automotive brake systems, banjo fittings are crucial for connecting the brake lines to the brake calipers. The compact and flexible design of banjo fittings allows for easy installation in the confined spaces around the wheels and suspension components. The secure and leak-proof connections provided by banjo fittings ensure reliable brake performance and safety.
Fuel Lines: Banjo fittings are also employed in fuel lines, particularly in high-performance and racing vehicles. Their ability to handle high pressure and provide a reliable seal makes them ideal for fuel delivery systems. The fittings ensure that fuel flows smoothly from the tank to the engine, contributing to the overall efficiency and performance of the vehicle.
Hydraulic Systems
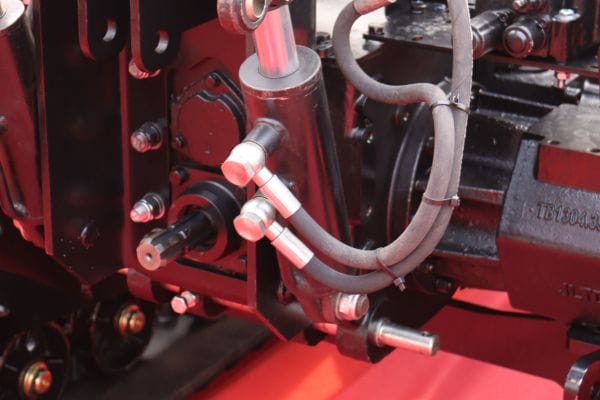
Banjo fittings play a vital role in various hydraulic circuits, where precise fluid control and robust connections are essential.
Hydraulic Pumps and Motors: In hydraulic systems, banjo fittings are used to connect hydraulic pumps and motors to the rest of the circuit. Their design allows for easy integration into tight spaces and ensures that fluid can flow efficiently between different components. The reliable sealing provided by banjo fittings prevents leaks and maintains the integrity of the hydraulic system.
Actuators and Cylinders: Banjo fittings are also used to connect hydraulic actuators and cylinders, ensuring smooth and controlled movement. The fittings’ ability to handle high pressure and provide flexible connections makes them ideal for these applications, where precise fluid control is crucial.
Step-by-Step Guide
Preparing the Components
Inspect the Components: Before starting the installation, inspect the banjo fitting, bolt, and O-rings for any signs of damage or defects. Ensure that all components are clean and free from debris.
Clean the Connection Points: Use a cleaning cloth to thoroughly clean the surfaces where the banjo fitting will be connected. This includes the fitting body, bolt, and the surfaces on the hose or pipe. Removing any dirt or contaminants will help ensure a secure and leak-free connection.
Apply Thread Sealant (if required): If the application requires it, apply a suitable thread sealant or PTFE tape to the threads of the bolt. This will help create a tighter seal and prevent leaks.
Assembling the Fitting
Position the O-rings: Place the O-rings onto the bolt, ensuring they are seated correctly in their grooves. The O-rings are crucial for creating a seal between the bolt and the fitting body.
Insert the Bolt into the Fitting Body: Slide the bolt through the eyelet of the banjo fitting body. Ensure that the bolt is aligned correctly and that the O-rings remain in place.
Align the Fitting with the Hose or Pipe: Position the banjo fitting assembly against the connection point on the hose or pipe. Align the holes in the fitting body with the inlet or outlet on the hose or pipe.
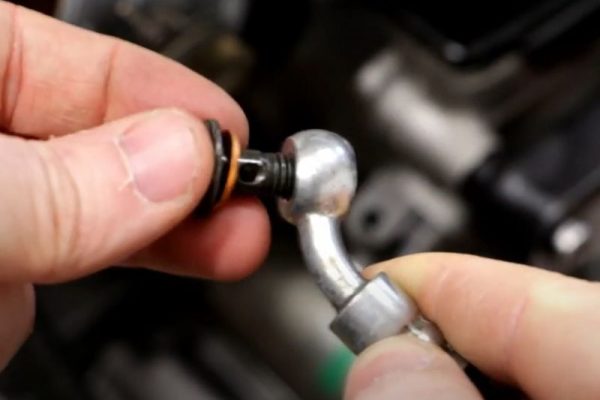
Tightening and Securing the Bolt
Insert the Bolt into the Connection Point: Begin threading the bolt into the connection point by hand, ensuring that it engages smoothly and does not cross-thread.
Tighten the Bolt: Use a wrench to tighten the bolt further, ensuring it is snug but not overtightened. Over-tightening can damage the threads or the O-rings.
Use a Torque Wrench (if required): For applications requiring precise torque settings, use a torque wrench to tighten the bolt to the manufacturer’s specified torque value. This ensures that the connection is secure without risking damage to the components.
Checking for Leaks
Pressurize the System: Once the banjo fitting is securely tightened, pressurize the system by turning on the hydraulic or fluid system. This will allow you to check for any leaks.
Inspect for Leaks: Carefully inspect the connection points around the banjo fitting for any signs of leaks. Use an inspection mirror if necessary to check hard-to-reach areas.
Tighten if Necessary: If you detect any leaks, slightly tighten the bolt further, ensuring not to over-tighten. Recheck for leaks after making adjustments.
Final Inspection: Once no leaks are detected, perform a final inspection to ensure that all components are securely in place and that the system operates correctly.
Common Issues
Identifying and addressing common problems with banjo fittings can prevent downtime and costly repairs. Here are some typical issues and their solutions:
Leaks:
Cause: Leaks can be caused by damaged O-rings, loose bolts, or cracks in the fitting body.
Solution: Replace damaged O-rings and ensure bolts are tightened to the correct torque. If the fitting body is cracked, replace the fitting.
Corrosion:
Cause: Corrosion can occur due to exposure to harsh chemicals or moisture.
Solution: Use fittings made from corrosion-resistant materials such as stainless steel or brass. Apply anti-corrosion coatings if necessary and ensure the system is properly sealed to prevent moisture ingress.
Cracks and Deformation:
Cause: Cracks and deformation can result from over-tightening, high pressure, or mechanical stress.
Solution: Replace any cracked or deformed fittings. Ensure that fittings are installed correctly and that the system’s pressure does not exceed the fitting’s rated capacity.
Blocked Fluid Flow:
Cause: Blockages can be caused by debris or contaminants in the fluid.
Solution: Regularly clean the system and use filters to prevent debris from entering the fittings. Inspect and clean the fitting’s internal passages if necessary.
Replacement Guide:
Knowing when and how to replace banjo fittings is essential for maintaining the integrity of the hydraulic system. Follow these guidelines for effective replacement:
When to Replace:
Visible Damage: Replace fittings that show visible signs of cracks, corrosion, or deformation.
Persistent Leaks: If leaks persist despite replacing seals and tightening connections, it may be time to replace the fitting.
Worn Seals: If seals are frequently worn or damaged, it may indicate that the fitting itself is compromised.
System Upgrades: During system upgrades or overhauls, consider replacing older fittings to ensure compatibility and reliability.
Conclusion
In this article, we explore the intricate details of banjo fitting, including its design, operating principles, applications, installation process, and maintenance. We compare them to live-connect swivel joints to highlight their unique benefits and discuss common problems and troubleshooting methods to ensure their optimal performance. We hope this comprehensive guide has been informative and helpful. Feel free to share this article with your colleagues and network, comment below with your experiences or questions, and email Topa.
FAQ
Banjo fittings are commonly used in hydraulic and pneumatic systems for applications such as automotive brake lines, fuel systems, industrial machinery, and medical devices.
Banjo fittings prevent leaks using O-rings and compression seals that create a tight seal around the bolt and fitting body, ensuring fluid does not escape from the connection.
Yes, banjo fittings, especially those made from materials like steel and brass, are designed to handle high-pressure environments commonly found in hydraulic systems.
The tools typically required for installing banjo fittings include adjustable wrenches, a torque wrench, hex keys, thread sealant, and cleaning cloths.
Banjo fittings should be inspected regularly, ideally during routine maintenance checks, to look for signs of wear, leaks, or corrosion.
Replace a banjo fitting if you notice visible damage, persistent leaks despite seal replacement, frequent seal wear, or during system upgrades to ensure compatibility and reliability.