In the intricate world of fluid control, selecting the right valve is paramount to ensure efficiency, safety, and reliability. Among the myriad of valve types available, ball valves have carved out a significant niche due to their versatility and robust performance.
Ball Valve Basics: What They Are and How They Work
Ball valves are some of the most widely used valves in fluid control systems—and for good reason. Their design is simple, their operation is quick, and their performance is highly reliable across a wide range of applications. But let’s break this down step by step.
What Is a Ball Valve?
At its most basic, a ball valve is a type of on-off valve. It uses a round ball with a hole (called a bore) through the center. The position of that hole determines whether the valve is open or closed. It’s this simplicity that makes the ball valve such a trusted component in both residential and industrial fluid systems.
The main components of a ball valve include:
- Valve Body – the outer shell that houses all internal parts
- Ball – the rotating sphere inside with a central hole
- Seats – the sealing surfaces that the ball presses against
- Stem – connects the ball to the handle or actuator
- Handle/Actuator – allows manual or automated rotation of the ball
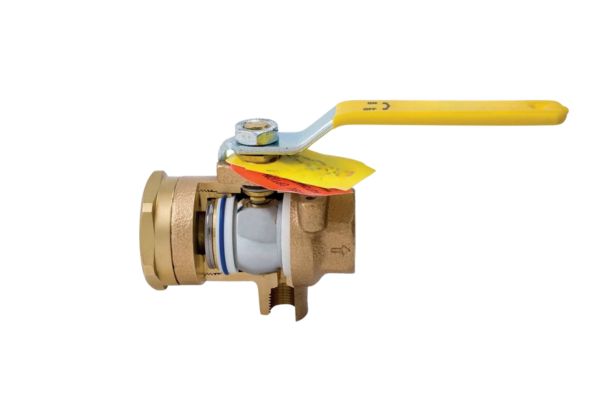
How Does a Ball Valve Work?
The operation of a ball valve is incredibly straightforward. Here’s what happens:
- Open Position: When the handle is aligned with the pipeline, the ball inside is also aligned—meaning the hole through the ball lines up with the flow direction. This allows liquid or gas to pass straight through the valve with minimal resistance.
- Closed Position: Turn the handle 90 degrees (a quarter turn), and the ball rotates so the solid side of the sphere blocks the flow path. This instantly shuts off the fluid, sealing the system.
This quarter-turn mechanism is what classifies it as a “quarter-turn valve,” and it’s one of the reasons why ball valves are so quick and easy to operate.
The Mechanics Behind the Seal
One of the most appreciated features of a ball valve is its tight seal. The ball presses against soft seats—often made of PTFE (Teflon) or other polymers—which conform to the shape of the ball to prevent leaks. Even under high pressure or high temperatures, this sealing design provides excellent leak-proof performance.
In higher-end models, you’ll also find options like metal seats or trunnion-mounted balls, which provide added sealing integrity and better performance in tough conditions.
Manual vs. Automated Operation
Ball valves can be operated in two main ways:
- Manual Operation: Most small-to-medium ball valves come with a lever handle that’s easy to turn by hand. Great for basic shutoff tasks.
- Actuated Operation: In larger systems, or when automation is needed, electric or pneumatic actuators can be used to control the valve remotely or on a schedule. These are common in process industries or facilities where safety and timing are crucial.
Why the Quarter Turn Makes All the Difference
Compared to multi-turn valves like gate or globe valves, the quarter-turn mechanism in ball valves offers:
- Faster operation – one quick motion opens or closes the valve
- Fewer wear points – reducing chances of mechanical failure
- Less effort – handy when space or physical access is limited
This design simplicity is one of the main reasons why ball valves are used everywhere—from backyard irrigation to chemical processing plants.
Common Ball Valve Types and Their Features
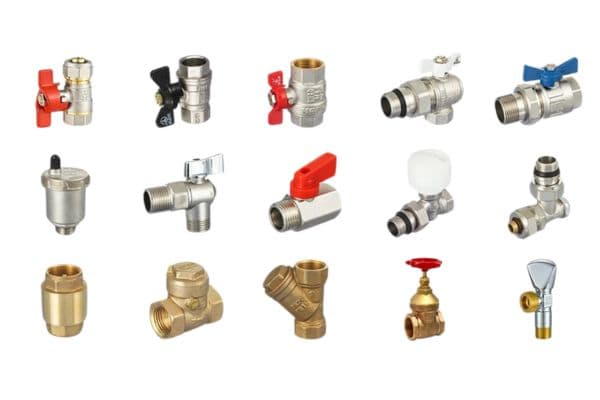
Understanding the different types of ball valves is crucial for selecting the right one for a specific application:
Full Port vs. Reduced Port Ball Valves:
Full Port (Full Bore): Features a ball with a bore diameter equal to the pipeline, ensuring minimal pressure drop and unrestricted flow. Ideal for applications where flow efficiency is critical.
Reduced Port (Reduced Bore): The ball’s bore is smaller than the pipeline diameter, causing a slight flow restriction. Suitable for systems where space and cost considerations are paramount.
One-Piece, Two-Piece, Three-Piece Ball Valves:
One-Piece: A single, solid cast body that is cost-effective but offers limited maintenance options.
Two-Piece: Consists of two separate pieces, allowing for easier maintenance and cleaning.
Three-Piece: Comprises three parts, facilitating comprehensive maintenance without removing the entire valve from the pipeline.
Floating Ball vs. Trunnion Mounted Ball Valves:
Floating Ball: The ball is held in place by the valve seats, allowing slight movement to maintain a tight seal. Common in low to medium pressure.
Trunnion Mounted: The ball is anchored by trunnions, providing additional support and making it suitable for high-pressure systems.
Material-Based Classification:
Stainless Steel: Offers excellent corrosion resistance, making it ideal for harsh environments.
Brass: Cost-effective with good durability, commonly used in residential and low-pressure applications.
PVC: Lightweight and resistant to a variety of chemicals, suitable for low-pressure and non-critical systems.
Specialty Ball Valves:
V-Port Ball Valves: Designed with a V-shaped ball or seat, allowing for precise flow control and throttling capabilities.
Multi-Port Ball Valves: Enable flow diversion, mixing, or shut-off in multiple directions, reducing the need for multiple valves in complex systems.
Key Advantages of Ball Valves for Reliable Flow Control
Ball valves are among the most preferred choices in fluid control systems—and for good reasons. From their efficient sealing capabilities to their low maintenance requirements, ball valves offer a suite of benefits that make them ideal for a wide range of applications.
Exceptional Sealing Performance
Thanks to their design, ball valves use tight-fitting seats (typically made from PTFE or similar materials) that press against the ball surface, creating a nearly leak-proof seal—even under high pressure.
This makes them ideal for applications where leakage isn’t an option—like natural gas, chemicals, or high-pressure hydraulic fluids. A properly installed ball valve can maintain its seal for years with minimal wear.
Quick Shut-Off and Easy Operation
Ball valves are quarter-turn valves, which means you only need to turn the handle 90 degrees to go from fully open to fully closed. This is not just convenient—it’s also safer and faster in emergency situations where time is critical.
The ease of operation also reduces user fatigue and error, especially in systems that require frequent manual operation. Whether it’s a handheld lever or an automated actuator, ball valves deliver smooth and responsive action every time.
Minimal Pressure Drop
Flow efficiency is a big deal in fluid systems, and ball valves, especially full port (or full bore) designs, shine in this area. With a full port ball valve, the hole through the ball is the same diameter as the pipeline, allowing fluids to pass through with minimal turbulence or restriction.
This design minimizes pressure drop, reduces pump energy consumption, and helps maintain optimal flow rates—especially important in high-volume or long-distance pipeline systems.
Durable and Long Lifespan
Ball valves are built to last. Whether made from stainless steel, carbon steel, brass, or high-performance plastics, these valves are designed to endure tough conditions—high pressures, extreme temperatures, corrosive chemicals, and more.
This durability translates into fewer replacements, less downtime, and a better return on investment. In fact, many industrial-grade ball valves can last over a decade with proper use.
Low Maintenance Requirements
Because of their simple design—with fewer internal components compared to globe or gate valves—ball valves require minimal maintenance. There’s less chance of internal wear, and seat replacements or lubrication are only needed occasionally.
This low-maintenance nature not only saves on repair costs but also ensures system reliability. For businesses, that means reduced operational disruptions and lower long-term ownership costs.
Versatility and Compatibility
Ball valves are used in a wide range of industries, from oil & gas and chemical processing to HVAC systems and water treatment plants. They are compatible with various types of media—including liquids, gases, and slurries—and can be installed in vertical or horizontal pipelines.
Plus, with different body materials, seat options, and connection styles (threaded, flanged, welded), ball valves can be customized to meet virtually any operational requirement.
Drawbacks and Limitations of Ball Valves
While ball valves bring many strengths to the table, they aren’t a one-size-fits-all solution. Like any component in a fluid control system, they have limitations that should be carefully considered during the design or selection process. Let’s take a look at the most common challenges associated with ball valves.
Not Ideal for Precise Throttling
Although ball valves can technically be used to regulate flow, they aren’t built for precision control. The flow characteristics of a ball valve are inherently nonlinear—meaning small changes in handle position can result in large flow variations. This makes it difficult to fine-tune flow rates, especially at lower flow volumes.
Other valve types, like globe valves or needle valves, are better suited for applications requiring accurate modulation of flow. Ball valves are typically designed for full open or full close scenarios, and using them in partially open positions over long periods can accelerate seat wear and reduce sealing effectiveness.
Potential for Seat Damage in Dirty or Abrasive Systems
Ball valves rely on a tight seal between the ball and the seats—usually made from soft materials like PTFE or reinforced polymers. In systems that carry dirty, abrasive, or particulate-laden fluids, small solids can get trapped between the ball and the seat. Over time, this can lead to:
- Scratches or grooves on the ball surface
- Seat deformation or erosion
- Increased friction during operation
- Poor sealing or eventual leakage
To mitigate this, some industries install strainers or filters upstream of the valve or opt for metal-seated ball valves in more aggressive environments.
Size and Weight Considerations in Large Diameter Applications
As the size of a ball valve increases, so do its physical dimensions and weight. Large-diameter ball valves can be significantly heavier and bulkier than other valve types of the same size, which leads to:
- Higher shipping and installation costs
- The need for specialized lifting equipment or structural support
- Challenges in confined or suspended pipeline systems
This is particularly important in overhead installations or mobile equipment where weight and space are limited. In such cases, designers may consider alternative valve types or opt for reduced-port configurations to minimize bulk.
Cost of Specialty Ball Valves
While standard ball valves are relatively cost-effective, specialized models—such as trunnion-mounted, metal-seated, or multi-port ball valves—can be considerably more expensive. These premium features are often essential for demanding applications, but the higher upfront cost may be a drawback for projects with tight budgets.
That said, the long-term savings in maintenance and durability often balance out the initial expense, especially in critical systems.
Thermal Expansion Issues in High-Temperature Environments
In high-temperature applications, thermal expansion of the ball can lead to jamming or excessive seat wear. If the materials aren’t rated correctly, the valve may become difficult to operate or fail to close tightly.
To prevent this, it’s essential to choose ball valves with proper temperature ratings and consider live-loaded or pressure relief seats for systems with extreme heat.
Where Ball Valves Excel: Common Industrial and Commercial Applications
Ball valves are trusted across industries for their dependable shutoff, fast operation, and versatility. Their design simplicity and performance make them the preferred valve type in many critical systems. Let’s take a closer look at where ball valves shine the most.
Oil and Gas Industry
In the oil and gas sector, equipment durability and safety are non-negotiable. Ball valves are used extensively in:
Pipeline isolation – Providing a secure shut-off for crude oil, natural gas, and refined products
Refining operations – Controlling high-temperature and high-pressure streams
Storage facilities – Offering rapid shut-off in emergency conditions
Their ability to handle corrosive fluids and maintain a tight seal under pressure makes them indispensable in upstream, midstream, and downstream operations.
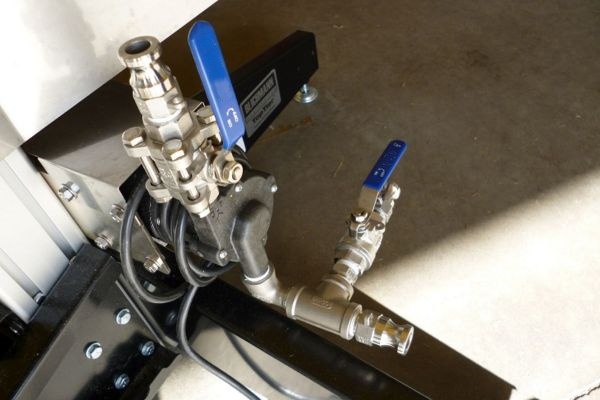
Chemical and Petrochemical Processing
Chemical plants deal with a wide variety of harsh, corrosive, or volatile media. Ball valves made from materials like stainless steel, Hastelloy, or PTFE-lined components are ideal for this environment. Benefits include:
Superior chemical resistance
Leak-proof sealing to prevent hazardous exposure
Compatibility with automated systems for precise control
From acid dosing to solvent flow management, ball valves are a core part of chemical processing infrastructure.
Water and Wastewater Treatment
Municipal water systems and treatment plants rely heavily on ball valves to manage water flow. They’re used in:
Filtration systems
Disinfection units (chlorination/UV)
Distribution and discharge points
Ball valves in this sector are prized for their corrosion resistance (especially PVC and stainless steel models), easy maintenance, and ability to function reliably even after long periods of disuse.
HVAC and Building Automation
In commercial buildings and industrial facilities, HVAC systems depend on fluid control valves for effective temperature management. Ball valves are commonly found in:
Chilled and hot water loops
Cooling towers and heat exchangers
Pump isolation valves
Their quick shut-off, compatibility with motorized actuators, and low-pressure drop help keep building systems efficient and energy consumption low.
Pharmaceutical and Food Industries
When cleanliness and sterility are mission-critical, ball valves rise to the challenge. In food processing and pharmaceutical manufacturing, sanitary ball valves are designed with:
Smooth internal surfaces to prevent bacteria buildup
Tri-clamp or hygienic ends for easy disassembly and cleaning
FDA-approved materials that meet strict health regulations
These valves maintain the purity of consumable products while allowing fast, repeated operation without contamination risk.
Marine and Offshore: Corrosion-Resistant Performance at Sea
Marine applications demand components that can withstand saltwater, high humidity, and constant vibration. Ball valves, particularly marine-grade stainless steel versions, are used in:
- Bilge and ballast systems
- Fire suppression lines
- Freshwater and fuel distribution systems
Their compact size, corrosion resistance, and reliability make them an excellent fit for shipboard installations.
Conclusion
Ball valves combine simplicity, durability, and efficiency—making them an essential component in modern fluid control systems. Whether you’re managing high-pressure industrial pipelines or precision-sensitive applications, understanding both the advantages and limitations of ball valves allows for smarter, more reliable system design. With the right selection, they deliver long-term performance, minimal maintenance, and maximum control.
FAQ
Are Ball Valves Suitable for Throttling Applications?
Ball valves typically aren’t ideal for precise throttling due to potential seat erosion. However, specialized V-ball designs enable moderate throttling.
How Often Should You Maintain Ball Valves?
Routine inspections are recommended every 6-12 months, depending on usage and fluid type. Heavy-duty applications might require more frequent inspections.
Can Ball Valves Handle Corrosive Fluids?
Yes, ball valves made from corrosion-resistant materials like stainless steel or alloy with compatible seat materials (e.g., PTFE) effectively handle corrosive substances.
What’s the Difference Between Manual and Actuated Ball Valves?
Manual valves require physical operation by turning a handle or lever, while actuated valves use electric, pneumatic, or hydraulic mechanisms for remote or automated control.
Do Ball Valves Work Well in High-Temperature Applications?
Yes, ball valves with appropriate materials, like stainless steel bodies and reinforced seat materials, effectively manage fluids in high-temperature environments, ensuring reliable operation.
What is the main purpose of a ball valve?
Ball valves are primarily used for on/off control of fluid flow. They provide a reliable seal and quick shutoff with a simple quarter-turn operation.