Struggling with persistent leaks at your hydraulic ports? Choosing the wrong seal type leads to incorrect orders, frustrating trial-and-error, and a system that is simply not reliable.
The right hydraulic fitting seal depends on the port’s design. Use an ED seal for flat-faced ports, an O-ring for ports with a chamfer or groove, and only use tapered threads like NPT or BSPT when specified, as they are prone to leaks.
When is an ED Seal the Right Choice for Your Port?
Have you ordered a fitting that just won’t seal, no matter how tight you make it? You may be trying to use the wrong seal type for your port’s flat surface, leading to leaks and damaged components.
An ED (Elastomer Dowty) seal is the correct choice for ports with a perfectly flat machined surface and parallel threads, such as Metric (M) or BSPP (G). It uses a bonded washer to create an extremely reliable, high-pressure static face seal.
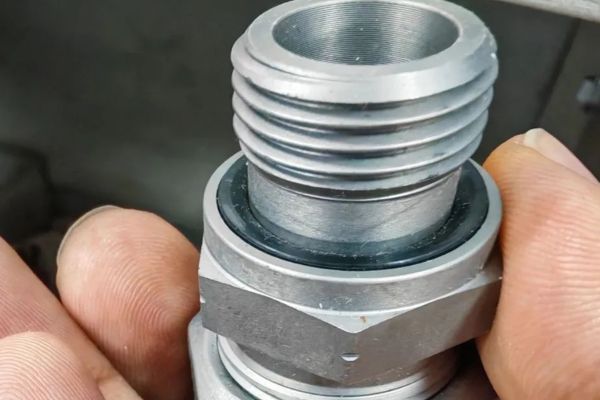
The ED seal, often called a bonded seal or Dowty washer, is a modern and highly effective sealing solution. It consists of a metal outer ring with a vulcanized rubber trapezoid ring bonded to the inside. When the fitting is tightened, the rubber part is compressed against the flat face of the port, creating a contained, high-pressure seal.
Key Characteristics and Application
The design is simple but precise. The metal ring prevents over-compression and extrusion of the rubber seal, while the rubber provides the flexible sealing element.
- Applicable Threads: This sealing method is used exclusively with parallel (straight) threads. The most common are Metric (M series) and British Standard Pipe Parallel (BSPP, or G threads). The threads themselves do no sealing; their only job is to provide the clamping force.
- Port Requirement: The single most important feature to look for is the port face. It must be a smooth, flat surface perpendicular to the threads. Any conical shape, chamfer, or groove indicates a different sealing method is required.
- Pressure Rating: ED seals are designed for high-pressure hydraulic systems. They provide a much more reliable seal under pressure spikes and vibration compared to older methods like tapered threads or simple combination washers. They offer a larger sealing surface area and better containment.
Why it Replaced Older Methods
The ED seal is a direct technological improvement over the older “combination washer,” which was a simple metal washer with a separate loose O-ring. The bonded design of the ED seal prevents the elastomer from being lost, incorrectly installed, or extruded under pressure, making it a much more robust and foolproof solution for modern hydraulic machinery.
Why Are O-Ring Seals So Common and Reliable?
Confused by ports that have a strange cone shape or groove in them? Trying to use a flat washer or ED seal on these ports will guarantee a leak and cause endless frustration.
O-ring seals are used for ports designed with a specific groove or chamfer to house the O-ring. This design allows the O-ring to be compressed in a controlled way, creating a highly effective and reusable seal that is common on SAE, JIC, and ORFS fittings.
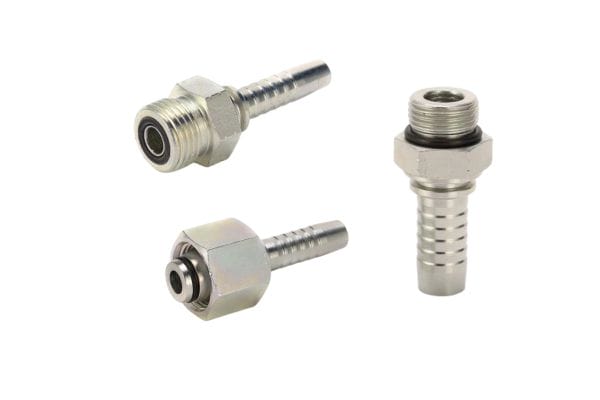
The O-ring is one of the most versatile and widely used seals in all of engineering, and hydraulics is no exception. It is a simple torus, or donut-shaped ring, made of an elastomeric material. Its sealing principle relies on mechanical deformation. When the hydraulic fitting is tightened, the O-ring is squeezed into a specially designed cavity, filling every microscopic gap and creating a formidable barrier against high-pressure fluid. The popularity of this method, especially in North American equipment (SAE standard), is due to its incredible reliability and reusability. A single glance at the port can tell you if an O-ring is needed.
Identifying Ports for O-Ring Seals
Unlike the flat face needed for an ED seal, O-ring ports have specific geometry.
- Conical or Chamfered Surfaces: The most common design for an O-ring port is a conical seat or a chamfer. The male fitting, which carries the O-ring, pushes the O-ring into this tapered surface, compressing it to form the seal. If you look into the port and see a cone, an O-ring seal is the first thing you should suspect. This is the principle behind SAE ORB (O-Ring Boss) ports.
- Grooves: Another common design is the O-Ring Face Seal (ORFS). In this case, the male fitting has a flat face with a groove for the O-ring. It seals against a flat-faced female port. The key identifier is the visible groove on the fitting end itself.
- Common Threads: O-rings are used with a wide variety of parallel threads, including SAE-ORB, Metric, and BSPP. In all these cases, the threads only provide the clamping force and are not part of the seal itself.
Advantages Over Other Methods
The O-ring offers several distinct advantages that make it a go-to choice for many manufacturers.
- High Reliability: When properly installed in a correctly designed port, O-ring seals are virtually leak-proof, even under high pressure and vibration.
- Excellent Reusability: As long as the O-ring itself is not nicked or damaged, the connection can be disassembled and reassembled multiple times without compromising the seal. It is always best practice to replace the O-ring during major services.
- Forgiveness: The soft, flexible nature of the O-ring allows it to seal effectively even if there are very minor imperfections on the metal sealing surfaces.
What Are the Risks of Using Tapered Thread Seals like NPT and BSPT?
Are you still using common pipe threads for high-pressure hydraulic lines? This old technology is a frequent source of leaks, thread damage, and system contamination, making it a risky choice for modern machinery.
Tapered thread seals, like NPT and BSPT, create a seal by wedging the threads together. This “dry seal” is prone to leakage under vibration, can damage ports if over-tightened, and requires sealant that can contaminate the system.

Tapered threads are one of the oldest sealing methods, carried over from general plumbing and pipe work. Unlike modern fittings where the threads provide clamping force and a separate element (like an O-ring or ED seal) does the sealing, tapered threads attempt to do both jobs at once. As the fitting is tightened, the male and female cones wedge together, creating a seal through metal deformation. The problem is that this is an imperfect, brute-force method that is not well-suited for the high pressures and dynamic loads of modern hydraulic systems. We manufacture them because they are still used in some applications, but we always advise caution.
Key Differences and Identification
It is critical to correctly identify and never mix the two main types of tapered threads.
- BSPT (British Standard Pipe Taper): Common codes are PT, R, RC, and ZG. It has a 55° thread angle.
- NPT/NPTF (National Pipe Taper / National Pipe Taper Fuel): The common code is NPT. It has a 60° thread angle.
Mixing NPT and BSPT fittings is absolutely forbidden. The different thread angles and pitches mean they will never form a proper seal and will leak immediately, while also damaging the threads on both the male and female components.
Why Tapered Threads Are Problematic in Hydraulics
While simple, this sealing method comes with significant drawbacks.
- The Spiral Leak Path: The root and crest of the threads never make perfect contact, leaving a spiral leak path. This is why thread sealant or PTFE tape is always required to fill this gap.
- Risk of Contamination: Small fragments of thread sealant or tape can break off during assembly and enter the hydraulic system. This debris can clog servo valves, damage pumps, and cause catastrophic component failure.
- Port Damage: The wedging action of the tapered threads creates immense outward (radial) force on the female port. It is extremely easy to over-tighten an NPT fitting and crack the port, which often means replacing an entire expensive manifold or cylinder.
- Poor Reusability: Each time the fitting is tightened, the threads deform. To reseal it, you must tighten it further, deforming the metal even more. After a few uses, the threads are permanently damaged and the connection is unreliable.
How Do ED Seals and O-Ring Seals Differ for Port Connections?
Not sure whether a parallel thread port requires an ED seal or an O-ring? Choosing incorrectly will prevent a proper seal and can damage the fitting or the port during tightening.
The key difference is the port’s face geometry. An ED seal requires a completely flat surface to seal against. An O-ring seal requires a corresponding feature, like a chamfer or groove, to be compressed into. Both use parallel threads for clamping force.
This is one of the most common points of confusion for technicians and engineers in the field. Both ED seals and O-ring seals are used with parallel threads (like BSPP and Metric), and both offer excellent, high-pressure performance. The choice between them is not about which is “better” in general, but which one is specifically designed for the machine’s port. The machine’s manufacturer has already made the decision by machining the port in a specific way. Your job is to correctly identify that design feature and use the corresponding fitting and seal.
A Simple Visual Identification Guide
The decision comes down to a quick visual inspection of the port you are connecting to.
Feature to Inspect | Corresponding Seal Type | Common Fitting Standards |
A perfectly flat, smooth port face | ED Seal (Bonded Seal) | DIN 3852-1, ISO 1179 |
A conical chamfer inside the port | O-Ring Seal | SAE J1926 (SAE-ORB), ISO 6149 |
A groove on the fitting’s face | O-Ring Face Seal | SAE J1453 (ORFS) |
Sealing Action
- ED Seal Sealing Action: The ED seal functions as a high-tech washer. The clamping force from the fitting squashes the bonded rubber ring directly against the flat equipment port. The seal is contained within the metal ring, preventing it from extruding outwards under pressure. This creates a very robust static seal that is excellent at resisting high pressures and pressure impulses. It’s a simple, reliable, and strong design.
- O-Ring Sealing Action: The O-ring’s action is more about controlled deformation. The port’s chamfer or the fitting’s groove provides a precisely shaped “house” for the O-ring. As the fitting is tightened, the O-ring is squeezed into this space, changing its cross-section from circular to D-shaped and pushing outwards in all directions to fill the cavity. This pre-compression creates the initial seal, which is then energized and strengthened by system pressure.
Are Older Sealing Methods Like Combination Seals Still Relevant?
Encountered an old fitting that uses a metal washer and a separate O-ring? While this technology works, it has been almost entirely replaced by more reliable and user-friendly sealing solutions.
Older methods like the “combination seal” (plain washer + O-ring) and the “composite bonded washer” are early-generation technologies. They are now considered obsolete and have been superseded by the superior, one-piece ED (Dowty) seal for most modern applications.
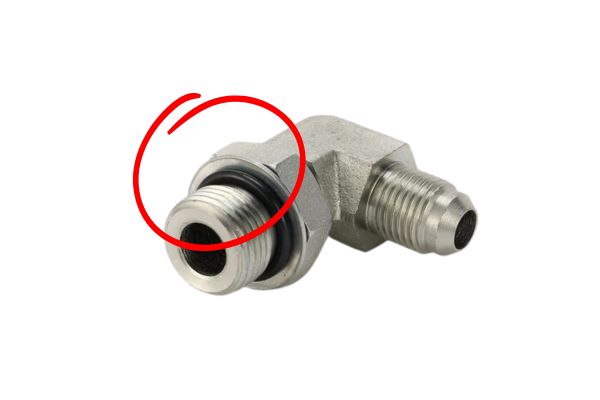
In the world of hydraulics, technology is always advancing to improve reliability and safety. The evolution of port sealing methods is a perfect example of this. While you might still encounter these older seals on legacy equipment or in certain niche applications, they are no longer the standard for new designs. As a supplier that supports both new and old machinery, we understand these legacy parts, but we also recognize why they were replaced. The modern ED seal solved the inherent problems of these earlier multi-part or weaker designs.
The Combination Seal (Washer + O-Ring)
- Design: This was the direct predecessor to the ED seal. It used a separate, flat metal washer and a separate O-ring. The idea was that the washer would provide the hard stop and the O-ring would provide the seal.
- Applicable Threads: It was used with the same parallel threads as the ED seal, such as BSPP and Metric.
- Weaknesses: The two-piece design was a major drawback. It was easy to forget the washer or the O-ring, or to install them in the wrong order. Under high pressure, the O-ring could become unseated or get extruded into the gap between the fitting and the port. This made it less reliable than the modern bonded ED seal a where the rubber element is permanently fixed.
- Current Status: Largely obsolete. Some adjustable elbow fittings may still utilize a similar principle with a retaining ring, but for standard port connections, the ED seal is the proper replacement.
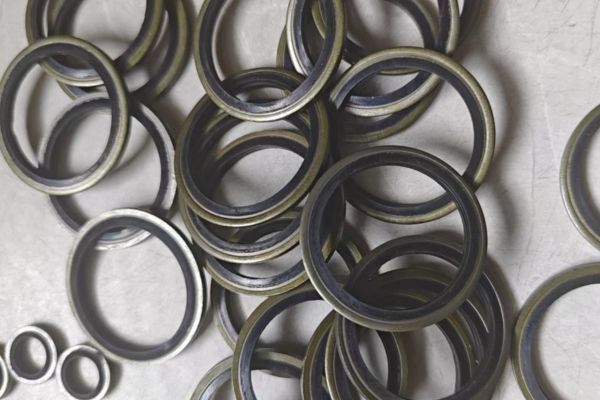
The Composite Bonded Washer (Old National Standard)
- Design: This was another early attempt at a one-piece seal, often found on older equipment built to previous national standards (like old Chinese GB standards). It consisted of a metal washer bonded to a rubber gasket.
- Weaknesses: The bonding technology and materials were less advanced than those used in modern ED seals. They were more susceptible to delamination and had lower pressure ratings. The rubber gasket design was less effective at preventing extrusion compared to the modern trapezoidal ring of an ED seal.
- Current Status: Completely phased out. It has been fully replaced by the ED seal in all modern standards and applications. If you encounter one, you should replace it with a modern ED seal of the correct size.
Conclusion
Choosing the correct hydraulic seal is not complex; it is a matter of careful observation. Matching the seal type—ED, O-ring, or tapered—to the port’s design is essential for a leak-free, reliable system.
At Topa, we provide a full range of high-quality hydraulic fittings and seals to meet any standard. Our team offers expert guidance and fast quotations to ensure you get the right component for the job, every single time.