A sudden, high-pressure spray of hydraulic fluid erupts from a piece of equipment. Operations grind to a halt, a hazardous cleanup begins, and profits are lost with every second of unscheduled downtime.
The vast majority of catastrophic hose failures are caused by preventable issues: external abrasion, improper routing, exposure to extreme temperatures, incorrect assembly, fluid incompatibility, and system contamination. Understanding these root causes is the key to prevention.

In any hydraulic system, the flexible hose assembly is often the component most exposed to damage and stress. While a hose may seem like a simple part, its failure can have consequences that ripple across an entire operation, ranging from expensive equipment repairs and environmental cleanup costs to, in the worst cases, serious personnel injury. These failures are rarely spontaneous or a result of simple bad luck. Instead, they are the predictable outcome of specific, identifiable conditions.
Is External Abrasion Silently Destroying Your Hoses?
A hose that appeared perfectly fine yesterday is suddenly leaking today. This slow, unseen wear from constant rubbing went unnoticed until it was too late, causing an unexpected and frustrating failure.
External abrasion occurs when a hose’s outer cover is worn away by rubbing against machine components or other hoses. This exposes the steel reinforcement to moisture and corrosion, severely weakening it and leading to a burst.
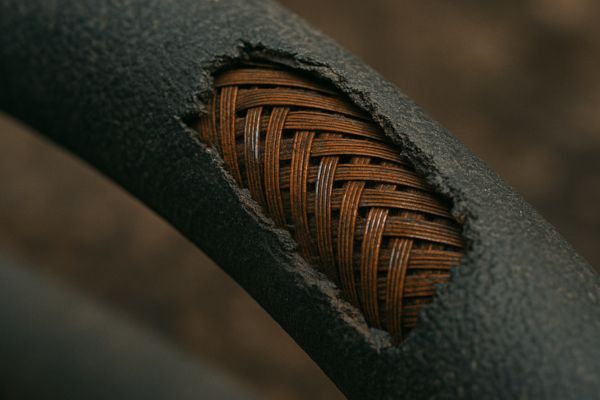
The Slow Grind to Failure
Abrasion is the single most common cause of hydraulic hose failure, yet it is also one of the most preventable. The process is deceptively simple. The hose’s synthetic rubber outer cover is its first line of defense, designed to protect the internal reinforcement layers from the elements. When a hose is routed in such a way that it continuously rubs against a piece of equipment’s frame, a bracket, or even another hose, this protective layer is slowly ground away. Once the high-tensile steel wire braid is exposed, the hose’s integrity is critically compromised. Moisture from the atmosphere, rain, or wash-downs causes the exposed steel to rust. Corroded wire has a fraction of the strength of protected wire. The hose can no longer contain the system’s operating pressure, and a burst is inevitable. Proactive prevention involves careful routing during installation and the use of protective measures.
Prevention Method | Description | Best For |
Proper Clamping | Using correctly sized P-clamps or brackets to secure the hose away from moving parts or sharp edges. | Securing long hose runs and preventing contact with frame members. |
Nylon Protective Sleeve | A woven fabric sleeve that slides over the hose, providing a durable, sacrificial layer against rubbing. | Bundling multiple hoses together or protecting against moderate, constant rubbing. |
Metal Spring Guard | A steel spring that wraps tightly around the hose, offering heavy-duty protection from impacts and severe abrasion. | High-risk areas on mobile equipment, like excavator arms. |
Are You Forcing Hoses into Failure with Improper Routing?
A brand-new hose assembly fails just weeks after installation. You blame the quality of the hose, but the hidden culprit is the immense stress created by a poor installation routing choice.
Bending a hose tighter than its specified minimum bend radius creates excessive stress on the reinforcement. This weakens the braid, can cause the inner tube to collapse, and ultimately leads to premature failure right at the bend.
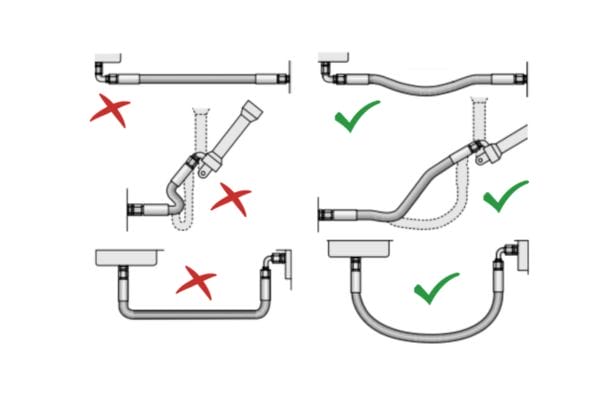
Stress, Strain, and the Bend Radius
Every hydraulic hose has a “minimum bend radius,” a specification determined by the manufacturer that dictates the tightest curve it can handle without sustaining damage. Forcing a hose into a sharper bend is a guarantee of premature failure. When a hose is bent too tightly, the reinforcement wires on the outside of the curve are stretched to their tensile limit, while the wires on the inside are compressed. This creates immense internal stress and metal fatigue. Furthermore, a sharp bend can cause the inner tube to pinch or kink, restricting flow, generating heat, and creating turbulence. This not only robs the system of efficiency but also accelerates the degradation of the hose’s inner liner. The solution is to always respect the manufacturer’s specification, which can be found in the product catalog. As a best practice, avoid routing hoses with sharp bends immediately after the fitting. Instead, use 45° or 90° angled fittings (like elbows) to accommodate the turn, allowing the hose itself to have a much more gradual, stress-free path.
Is Extreme Heat Cooking Your Hoses from the Inside Out?
Your hydraulic hoses are becoming hard, brittle, and covered in fine cracks. You keep replacing them, failing to diagnose that the system’s temperature is the real root cause of the problem.
Excessively high temperatures, either from the hydraulic fluid (internal) or the operating environment (external), cause the hose’s rubber compounds to lose their flexibility. The hose hardens, cracks, and can no longer withstand pressure changes or flexing.
A Two-Pronged Thermal Attack
Heat is a relentless enemy of the synthetic rubber compounds used to make hydraulic hoses. The damage can come from two sources. Internal heat is generated by the hydraulic fluid itself. If a system’s cooler is inefficient or the fluid level is low, oil temperatures can soar beyond the hose’s rated limit (typically 100°C / 212°F). This intense heat essentially “bakes” the rubber from the inside, breaking down the chemical bonds that give it flexibility. External, or ambient, heat is just as damaging. Routing a hose too close to an engine block, exhaust manifold, or other hot component will have the same effect. The result is a hose that loses its pliability and becomes stiff. As the equipment moves and the hose attempts to flex, the hardened rubber simply cracks open, leading to leaks and eventual rupture. Prevention involves regular checks of the hydraulic system’s cooling circuit and careful routing to maintain distance from heat sources. In unavoidable hot-zone applications, specifying high-temperature hoses and using protective fire sleeves is essential.
Is the Wrong Hydraulic Fluid Dissolving Your Hoses?
Upon inspection, a failed hose’s inner tube is found to be soft, gummy, and swollen. This indicates a chemical attack, which has not only destroyed the hose but also contaminated the entire system with rubber particles.
Using a hydraulic fluid that is chemically incompatible with the hose’s inner tube material will cause the tube to break down. The material can swell, soften, or delaminate, leading to a complete loss of integrity and system-wide contamination.
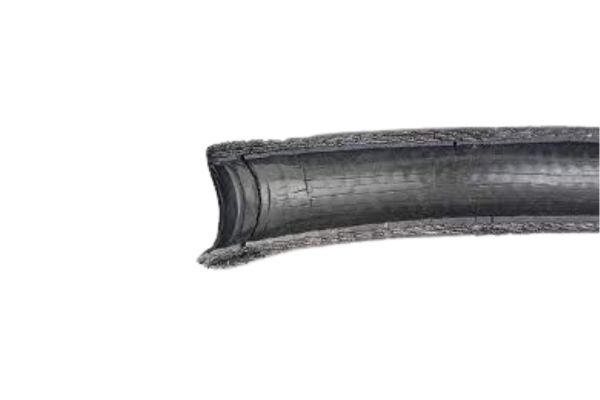
The Importance of Chemical Compatibility
The inner tube of a hydraulic hose is engineered from a specific synthetic rubber compound to be compatible with a certain class of fluids. The most common material, Nitrile (NBR), is excellent for use with standard petroleum-based hydraulic oils. However, the industrial world uses a wide variety of fluids, including water-based fluids, environmentally friendly biodegradable oils, and specialized synthetic fluids like phosphate esters. If a standard Nitrile hose is used with an incompatible fluid like a phosphate ester, a chemical reaction will occur. The inner tube will begin to swell, lose its hardness, and may even dissolve or “leach” into the fluid. This not only causes the hose to fail but also sends a stream of rubber debris throughout the entire hydraulic system, which can clog filters, jam valves, and damage pumps. The only way to prevent this is to rigorously verify compatibility. Always consult the manufacturer’s chemical compatibility chart to match the fluid type with the correct inner tube material (e.g., EPDM for phosphate esters, etc.) before specifying a hose.
Fluid Type | Recommended Tube Material | Incompatible Tube Material |
Petroleum-Based Oils | Nitrile (NBR) | EPDM |
Phosphate Esters (e.g., Skydrol) | EPDM | Nitrile (NBR) |
Water Glycol | Nitrile (NBR), EPDM | – |
High-Temp Hydrocarbons | Viton (FKM) | Nitrile (NBR) |
Is a Poorly Assembled Fitting the System’s Weakest Link?
A newly made hose assembly blows off violently at the fitting connection. This dangerous failure not only causes immediate downtime but also casts serious doubt on the quality and safety of the repair work.
An incorrectly crimped or attached fitting creates a fatal flaw at the connection point. Under-crimping results in insufficient grip for the hose to blow off, while over-crimping can fracture the reinforcement wires, leading to a burst under pressure.
A Science, Not an Art
Creating a reliable hose assembly is a precise manufacturing process, not guesswork. The connection between the hose and the fitting is designed to be as strong as the hose itself, but only if it is assembled correctly. For crimped assemblies, this means adhering strictly to the manufacturer’s specified crimp diameter. Using calipers to verify that the crimp is within the specified tolerance (typically +/- a few thousandths of an inch) is non-negotiable. An under-crimped fitting lacks the mechanical grip to hold the hose against the immense forces generated by high pressure. An over-crimped fitting is equally dangerous; the excessive force crushes and damages the steel wire reinforcement under the fitting collar, creating a weak point that will fail under pressure surges. For reusable fittings, the same principles apply: using mismatched brands, failing to skive when required, or not seating the hose correctly will all result in a faulty connection. The hose and fitting must be treated as a matched, engineered system.
Is ‘Dirty’ Oil Sandblasting Your Hoses from Within?
A hose fails with a pinhole leak, yet there is no sign of external damage, heat exposure, or incorrect routing. The confused technician is unaware of the invisible enemy flowing through the system: contamination.
High-velocity hydraulic fluid containing abrasive particles acts like a slow-motion sandblaster on the inner tube of the hose, especially at bends. This steady erosion gradually thins the tube wall until it can no longer contain the pressure.

The Unseen Abrasive
While external abrasion is easy to spot, internal erosion is a silent killer. Hydraulic fluid should be pristine, but it can become contaminated with microscopic particles of dirt, sand, and metal from component wear. As this contaminated fluid travels through the hose at high speeds (often exceeding 20 feet per second), these particles become tiny projectiles. The effect is most pronounced at hose bends, where the fluid stream impacts the outer wall of the inner tube. Over thousands of hours of operation, this constant bombardment erodes the rubber, literally wearing it away from the inside. Eventually, the tube wall becomes so thin that it develops a pinhole leak or ruptures completely. Prevention focuses entirely on system cleanliness. This includes implementing a strict filtration schedule, using high-quality filters, ensuring new fluid is filtered before being added to the system, and always capping open hoses and ports during maintenance to prevent the ingress of dirt. A clean system is a reliable system.
Conclusion
Catastrophic hose failures are not random events but the result of specific, manageable causes. Proactive inspection and correct procedures for routing, assembly, and system maintenance are the keys to preventing costly and dangerous failures.
The foundation of a reliable hydraulic system is built on high-quality components. At Topa, we manufacture a complete range of hydraulic hoses and fittings engineered for safety and durability. Contact our team to source the dependable parts your business requires to prevent failure before it happens.