Hydraulic hoses play a crucial role in industrial operations, transferring high-pressure fluids to power various equipment and machinery. Given their importance, ensuring safe and effective connection and disconnection is vital to maintaining operational efficiency and preventing potential hazards. Whether in construction, manufacturing, or agriculture, proper handling of hydraulic hoses not only protects equipment but also safeguards personnel working with these powerful systems.
Understanding Hydraulic Hoses and Their Connections
Overview of Hydraulic Hoses
Definition and Role of Hydraulic Hoses in Various Industries Hydraulic hoses are flexible, high-strength tubes engineered to transport hydraulic fluids under pressure, facilitating mechanical processes across diverse industries. These hoses are integral to the hydraulic systems of heavy machinery, construction equipment, industrial machines, and agricultural tools. Designed for flexibility, durability, and efficiency, they allow smooth fluid transfer even in dynamic and challenging environments, which is crucial for maintaining productivity and safety.
In construction, hydraulic hoses power excavators, bulldozers, and cranes enabling precise control over movements and lifting. In manufacturing, they facilitate assembly lines, pressing machines, and material handling equipment, ensuring seamless automation. The mining sector relies on hydraulic hoses to manage drilling rigs, loaders, and transport machinery, where robust and safe fluid transmission is essential due to the high pressures and rough conditions. In agriculture, they support the operation of tractors, harvesters, and irrigation systems, enhancing productivity and reducing manual labor.
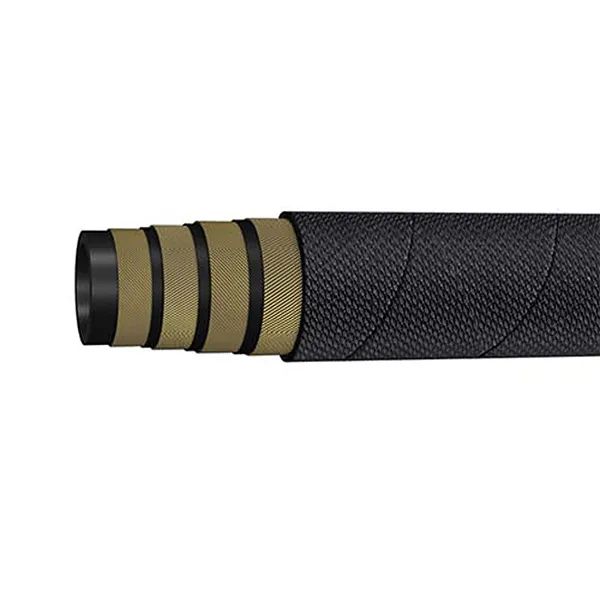
Common Types of Hydraulic Hoses Used
Hydraulic hoses are constructed using different materials, designs, and reinforcements to meet the specific needs of various applications. The most common types include:
Reinforced Rubber Hoses
Made from synthetic rubber, reinforced with either wire braiding or spiral layers, these hoses offer exceptional flexibility and high-pressure resistance.
- Applications: These hoses are widely used in construction, agricultural machinery, and material handling equipment. They can handle heavy-duty operations and tolerate frequent bending.
- Advantages: Good flexibility, high abrasion resistance, and reliable performance under varying temperatures.
- Limitations: They may degrade over time when exposed to harsh chemicals or extreme temperatures, requiring regular inspection and maintenance.
Thermoplastic Hoses
These hoses feature a nylon or polyester core and are typically reinforced with a synthetic fiber or steel wire layer.
- Applications: Ideal for medium- and high-pressure applications such as forklifts, aerial lifts, and mobile hydraulic equipment.
- Advantages: Lightweight, durable, and highly resistant to chemicals, making them suitable for both indoor and outdoor use.
- Limitations: They are not as flexible as rubber hoses, and sudden temperature changes may impact their performance.
PTFE (Polytetrafluoroethylene) Hoses
Also known as Teflon hoses, these are made from chemically inert PTFE and are often reinforced with stainless steel wire braiding.
- Applications: These hoses are commonly used in high-temperature applications, chemical processing, and food industries.
- Advantages: High resistance to chemicals, heat, and pressure, along with a longer lifespan compared to rubber hoses.
- Limitations: Limited flexibility compared to rubber and thermoplastic hoses; they are generally more expensive and require careful handling to avoid damage to the inner core.
Steel-Reinforced Teflon Hoses
These hoses are a specialized type of PTFE hose, reinforced with multiple layers of stainless steel wire braiding, designed to withstand extremely high pressures.
- Applications: Used in heavy-duty hydraulic systems, industrial processes, and equipment where consistent performance under extreme conditions is required.
- Advantages: Excellent pressure and temperature resistance, reduced risk of hose bursting, and enhanced durability.
- Limitations: Stiffer than other hoses, making installation and routing more complex; they may also have a higher initial cost.
Types of Hydraulic Connections
Efficient hydraulic systems depend not only on the hoses themselves but also on the types of connections used to secure and manage fluid flow.
Quick-Connect Couplings
Quick-connect couplings are designed to allow rapid and easy connection or disconnection of hydraulic lines without the need for tools.
Pros:
- Ease of Use: Quick-connect couplings enable fast and efficient attachment or detachment, which reduces downtime and improves workflow efficiency.
- Reduced Fluid Loss: Many designs incorporate automatic shut-off valves that minimize fluid spillage during disconnection, protecting both the operator and the environment.
- Versatility: Available in various configurations and materials, quick-connects can accommodate different types of hoses and equipment, making them suitable for diverse hydraulic systems.
- Time-Saving: In emergencies, quick-connects allow for fast isolation of equipment, reducing the risk of damage and injury.
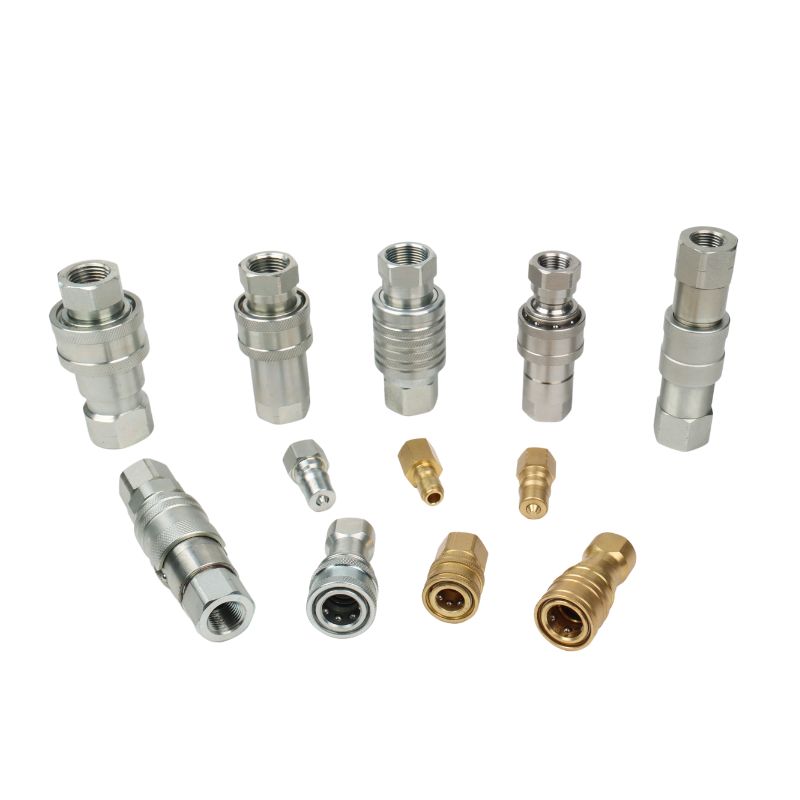
Cons:
Potential for Contamination: If the connectors are not properly cleaned and maintained, contaminants such as dust, dirt, or moisture can enter the hydraulic system, leading to equipment malfunctions.
- Pressure Sensitivity: Quick-connects may not be ideal for extremely high-pressure applications, as improper engagement can result in leaks or damage to the coupling, posing safety risks.
- Wear and Tear: Due to frequent connections and disconnections, quick-connects may experience wear over time, requiring regular inspection and possible replacement to ensure safe operation.
Threaded Connections
Threaded connections involve screwing the fittings onto the hose ends, creating a secure and robust seal. They are commonly used in applications where high-pressure resistance is required.
Safety Considerations:
- Proper Tightening: Ensuring the connections are properly tightened is crucial to prevent fluid leaks and potential hose failure. Over-tightening can damage the threads, while under-tightening can result in leaks.
- Use of Sealants: Threaded connections often require PTFE tape or thread sealants to maintain a leak-proof seal. It’s essential to apply these correctly to avoid contamination or residue inside the hydraulic system.
- High-Pressure Compatibility: Threaded connections are typically designed to withstand higher pressures than quick-connects, making them suitable for heavy-duty machinery and equipment.
- Inspection and Maintenance: Regular checks are necessary to ensure the integrity of threaded connections, as the threads can become worn or damaged, compromising the seal and increasing the risk of leakage.
Safety Preparations Before Handling Hydraulic Hoses
Pre-Operational Safety Check
Before starting any operation with hydraulic hoses, it’s essential to conduct a thorough pre-operational safety check. This helps prevent potential hazards and ensures the safe and efficient functioning of hydraulic systems.
Inspecting Hoses for Wear, Leaks, or Damages
- Visual Inspection: Begin by conducting a detailed visual inspection of all hydraulic hoses, checking for any visible signs of wear, such as cracks, abrasions, blisters, or bulges.
- Look for Leaks: Carefully examine the hose connections and fittings for fluid leaks. Leaks can be indicated by fluid residue around connection points or unusual dampness on the hose surface.
- Assessing Damage: Check for kinks, twists, or deformation that may have occurred during previous operations. Damaged hoses are more prone to bursting or leaking when under pressure, posing safety risks.
- Action: Replace any hose showing significant wear, damage, or leaks. Remember that using a damaged hose in high-pressure operations can lead to catastrophic failures.
Checking Pressure Ratings and Ensuring Compatibility with Equipment
- Verify Pressure Ratings: Confirm that the hose being used is rated for the system’s working pressure. Using hoses below the required pressure rating can result in leaks or bursts, which could cause injuries or damage to the equipment.
- Equipment Compatibility: Ensure that the hose material, length, and diameter are compatible with the specific hydraulic equipment in use. This helps maintain optimal fluid flow and system efficiency.
- Check Hose Fittings: Ensure the fittings and connections match the hose specifications and are securely attached. Mismatched fittings can lead to leaks, reduced pressure, or hose ejection during operation.
Importance of Safety Gear
- Personal Protective Equipment (PPE): Operators must wear the appropriate safety gear when handling hydraulic hoses to protect against potential hazards.
- Gloves: Wear cut-resistant, oil-resistant gloves to safeguard against leaks, spills, and sharp edges on fittings or damaged hoses.
- Goggles or Face Shields: Protect eyes and face from unexpected fluid sprays, which can be dangerous due to the high pressure of hydraulic systems.
- Protective Clothing: Wear long-sleeved garments made of durable materials to shield skin from high-pressure fluid leaks, which can penetrate the skin and cause serious injuries (hydraulic injection injuries).

Proper Work Environment Setup
A safe working environment is a crucial factor in ensuring hydraulic hose handling operations are conducted without incident.
Ensure a Clean, Dry, and Well-Ventilated Work Area
- Clean Work Area: Keep the workspace free of debris, dirt, and unnecessary tools to reduce the risk of contamination during hose connection or disconnection. Contaminants can enter the hydraulic system and cause blockages, wear, or equipment failure.
- Dry Surface: Avoid working in wet areas where spills can cause slips or falls. Fluid spills should be cleaned up immediately, and absorbent materials should be readily available for quick response.
- Ventilation: Ensure that the workspace is well-ventilated to prevent the buildup of any hazardous fumes, especially when working indoors or in confined spaces. Proper ventilation is essential when dealing with hydraulic systems that involve fluid maintenance or refilling.
Warning Signage and Barriers Around High-Risk Zones
- Display Warning Signs: Use clear, visible warning signs to indicate high-pressure zones, potential fluid leakage areas, or areas where hoses are actively being connected or disconnected.
- Barriers: Set up physical barriers or cones around the work area to restrict access to unauthorized personnel, reducing the risk of accidental injury.
- Emergency Preparedness: Ensure that safety showers, eyewash stations, and first-aid kits are easily accessible in case of hydraulic fluid exposure or accidental injuries.
Steps for Safely Connecting Hydraulic Hoses
Properly connecting hydraulic hoses is critical to maintaining system safety and operational efficiency. Follow these detailed steps to ensure a secure and effective connection:
Depressurizing the System Before Starting
Importance: Hydraulic systems operate under high pressure, and attempting to connect hoses without first relieving pressure can be extremely dangerous. It can cause sudden fluid release, leading to injuries or hose ejection.
How to Depressurize:
Turn off the power source and ensure the system is completely shut down.
Gradually release the pressure by opening the designated relief valve. In some cases, a bleed-off valve or hose will also need to be opened to drain residual pressure.
Confirm that there is no residual pressure before proceeding. Use a pressure gauge if necessary to verify that the system is at zero pressure.

Cleaning the Hose Ends and Connectors
Why It’s Important: Dirt, dust, or debris on hose ends and connectors can enter the hydraulic system during connection, potentially causing blockages, component damage, or reduced performance.
Cleaning Process:
Use a clean, lint-free cloth to wipe off any contaminants from both the hose end and the connector.
For stubborn debris or greasy residue, use a suitable solvent cleaner. Ensure the cleaning agent is compatible with the hose material to prevent degradation.
Cover the cleaned hose ends with protective caps until they are ready to be connected, minimizing contamination risks.
Aligning the Hose Correctly to Avoid Twisting or Bending
Importance: Proper hose alignment prevents unnecessary twisting, bending, or kinking, which can weaken the hose structure and lead to leaks or bursts during operation.
Alignment Tips:
Position the hose in the intended path, ensuring that it is free of sharp bends and excessive stretching.
The hose should be naturally aligned with the connection point, following the equipment’s routing layout.
Use hose clamps, brackets, or guides to secure the hose in place, maintaining alignment and minimizing movement during operation.
Engaging the Connector with a Firm, Secure Fit
Steps for Connection:
Begin by carefully aligning the hose fitting with the equipment’s receiving port, making sure that the threads or connectors match perfectly.
Firmly screw or push the connector until it is fully engaged, ensuring a tight seal. For threaded connections, hand-tighten first and then use a wrench to secure the fitting.
For quick-connect couplings, push or pull the connection until you hear a distinct ‘click,’ indicating that the coupling is securely locked.
Final Check:
Verify the connection’s tightness by gently pulling on the hose to ensure it’s securely attached.
Perform a pressure test after connection to confirm that there are no leaks and that the connection can withstand the system’s working pressure.
Common Mistakes During Connection
Proper awareness of potential mistakes during connection is essential to prevent accidents and system failures. Here are some common errors and how to avoid them:
Skipping Inspection and Cleaning
Risk: Failure to inspect and clean hose ends and connectors before connection can introduce contaminants into the hydraulic system, causing blockages, reduced performance, and increased wear.
Prevention: Make inspection and cleaning mandatory steps before every connection. Always keep clean clothes and suitable solvents on hand for quick cleaning.
Misalignment or Using Incompatible Connectors
Misalignment:
Twisting or bending the hose during connection can weaken its structure, leading to premature wear or bursting.
Avoid forcing the hose into position. If misalignment occurs, readjust the hose routing rather than attempting to bend it into place.
Using Incompatible Connectors:
Incompatible connectors can create gaps, resulting in leaks or hose detachment under pressure.
Always verify that the connectors match in size, thread type, and material compatibility before connection.
Steps for Safely Disconnecting Hydraulic Hoses
Safely disconnecting hydraulic hoses is as critical as the connection process, requiring proper techniques to avoid sudden fluid release, contamination, or equipment damage. Follow these steps for secure and effective disconnection:
Turn Off the Power and Release Pressure from the System
Importance: Hydraulic systems operate under high pressure, making it essential to eliminate residual pressure before disconnection. Failing to do so can result in sudden fluid release, causing severe injuries or damage.
How to Release Pressure:
Start by shutting down the hydraulic system and ensuring that the power source is completely turned off.
Locate the pressure relief valve and slowly open it to allow the pressure to dissipate gradually. For systems equipped with bleed-off valves or hoses, use them to safely drain any remaining fluid pressure.
Confirm that the system pressure has dropped to zero by checking the pressure gauge or by carefully attempting a small release at a nearby connection point.
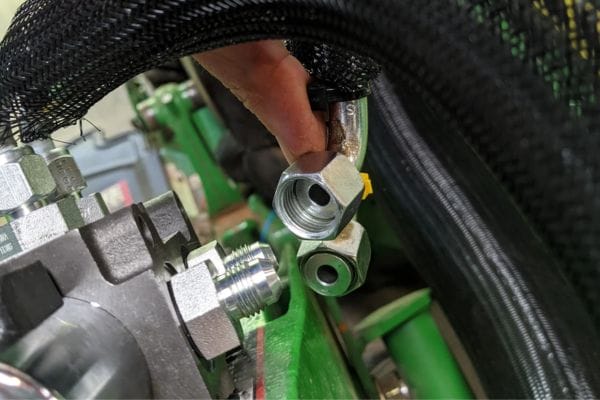
Loosen the Connectors Gradually to Prevent Sudden Bursts
Importance: Rapid disconnection can cause sudden bursts of fluid, posing risks of high-pressure injection injuries, fluid spills, and contamination.
Disconnection Process:
Use two wrenches: one to hold the hose in place and the other to slowly loosen the connector. This method ensures stability and reduces the risk of sudden hose movement.
For quick-connect couplings, firmly press the release mechanism and allow any trapped pressure to vent before fully detaching the connection.
If any fluid begins to leak during the process, pause the disconnection to allow the pressure to stabilize further.
Cover the Disconnected Hose Ends to Prevent Contamination
Why It’s Important: Open hose ends are vulnerable to contamination by dust, dirt, and moisture, which can enter the hydraulic system when reconnected, leading to blockages or equipment damage.
Covering Process:
Immediately after disconnection, cap both the hose ends and equipment ports using clean, protective caps or plugs. This practice keeps contaminants out and maintains system integrity.
If contamination is suspected during the disconnection, flush and clean the hose before the next connection to ensure proper operation.
Precautionary Measures
While following the disconnection steps, implement additional safety measures to protect both the operator and the hydraulic system:
Use of a Secondary Safety Measure (e.g., a Safety Block)
Safety Blocks: Install a safety block or isolation valve to ensure the system is completely depressurized before starting the disconnection. This adds an extra layer of safety by physically separating the hydraulic fluid flow from the hose being disconnected.
Emergency Shut-off Valves: Some systems are equipped with emergency shut-off valves that can be used as an extra precaution to isolate the system from residual pressure, reducing the risk of sudden fluid release.
Avoiding Direct Contact with Leaking Fluids or Hot Surfaces
Fluid Leaks: Hydraulic fluids are often under high pressure and can be hot. Direct contact with leaking fluids can result in burns, skin irritation, or hydraulic injection injuries.
Always wear appropriate personal protective equipment (PPE), including gloves, goggles, and long-sleeved clothing, when working with hydraulic hoses.
Position yourself at a safe distance from the hose and use tools or absorbent materials to manage leaks instead of direct contact.
Hot Surfaces: Hydraulic components can become very hot during operation. Allow the system to cool down before starting disconnection to avoid burns.
Use thermal gloves when handling hoses or connections that may still be warm.
If the hose surface remains hot after shutdown, wait for the equipment to cool, or apply cooling methods if necessary.
Managing High-Pressure Situations
Dealing with High-Pressure Hoses
Handling high-pressure hoses requires a heightened level of safety awareness, as these hoses operate at extremely high pressures and pose greater risks of injury or damage if not managed properly.
Special Safety Tips for High-Pressure Hydraulic Systems
- Understand the Pressure Rating: Always check and confirm that the hose’s pressure rating is suitable for the intended application. The working pressure of the hose should match or exceed the system’s maximum operating pressure to prevent sudden failure.
- Regular Inspection: Inspect high-pressure hoses more frequently for any signs of wear, bulging, leaks, or weak spots, as they are more susceptible to stress and pressure fluctuations.
- Proper Hose Routing: Ensure high-pressure hoses are routed correctly, avoiding sharp bends, tight curves, or kinks, as these can weaken the hose structure and lead to potential bursting.
- Avoid Abrasion: High-pressure hoses are often subject to abrasion due to their placement in heavy-duty operations. Use protective sleeves or guards to minimize wear and extend hose life.
- Safe Handling: Never attempt to kink, twist, or forcefully bend a high-pressure hose during operation. This can create weak points that may lead to sudden failure when under high pressure.
Use of Pressure-Relief Valves and Pressure Indicators
Pressure-Relief Valves:
- Install pressure relief valves as part of the hydraulic system design to prevent over-pressurization. These valves automatically release excess pressure, protecting hoses, fittings, and other components from damage.
- Test pressure-relief valves regularly to ensure they function properly, as malfunctioning valves can create significant risks in high-pressure systems.
Pressure Indicators:
- Use pressure gauges or digital pressure indicators to monitor system pressure continuously. This allows operators to detect pressure fluctuations early, enabling preventive measures before pressure builds up to dangerous levels.
- Mount pressure gauges at easily visible locations along the system, especially near connection points and high-pressure zones. This enhances monitoring and quick response capabilities during operation.
Handling Hose Failures or Unexpected Pressure Release
High-pressure hydraulic systems can fail suddenly, making it crucial to have emergency protocols in place to manage potential accidents effectively.
Emergency Response Protocols for Sudden Leaks or Hose Failures
- Immediate Shutdown: In case of a sudden leak or hose failure, immediately shut down the hydraulic system using the nearest emergency stop button or shut-off valve. This helps reduce pressure buildup and prevents further fluid loss.
- Evacuate the Area: If the leak is substantial, evacuate the immediate area to protect personnel from potential fluid injection injuries, burns, or exposure to hazardous fluids.
Contain the Leak:
- Use absorbent materials or spill kits to contain leaking fluid and prevent it from spreading. Quick containment also minimizes environmental damage and makes the area safer for emergency responders.
- In case of a major failure, create a temporary barrier using safety cones or caution tape to mark off the affected area and prevent unauthorized access.
Assess the Damage:
- Once the area is secure, carefully assess the extent of the hose failure. Look for possible reasons such as pressure overload, material fatigue, or improper installation.
- Ensure that the pressure has been completely released before conducting any inspections. Use pressure indicators to verify the absence of residual pressure in the system.
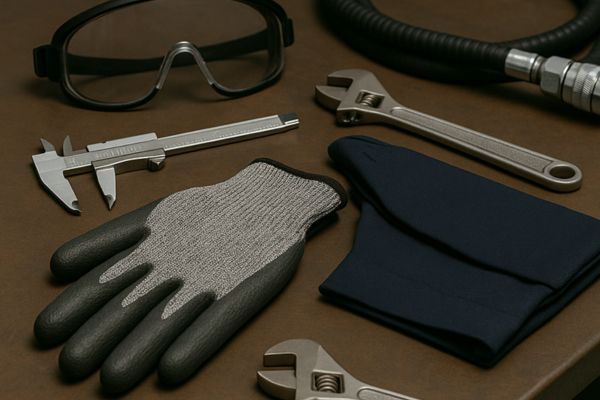
Preventing Further Damage or Injuries
- Protective Gear: Ensure all personnel involved in handling the failure are equipped with personal protective equipment (PPE), such as gloves, goggles, and face shields, to prevent contact with high-pressure fluids.
- Notify Maintenance Personnel: Alert the maintenance team to initiate repairs or replacement of the failed hose. Use hoses with pressure ratings that match or exceed the system’s requirements to prevent similar incidents.
Conclusion
Safety must always be the top priority when handling hydraulic hoses. Even minor oversights can result in serious injuries, costly equipment damage, or unexpected downtime. A proactive approach to safety not only protects personnel but also ensures operational efficiency and system longevity. Share this information with colleagues, team members, and other operators to promote safety awareness and prevent accidents in hydraulic systems. Together, we can enhance safety standards and contribute to a safer, more efficient workplace.
FAQ
What should I do first before connecting hydraulic hoses?
Always depressurize the system completely before attempting any connection. This prevents sudden fluid release and potential injuries.
How often should I inspect hydraulic hoses for wear or damage?
Inspect hoses regularly—ideally before each use. For high-pressure systems, more frequent checks are recommended.
What personal protective equipment (PPE) should I use when handling hydraulic hoses?
Wear gloves, goggles, and protective clothing to safeguard against high-pressure fluid leaks, hot surfaces, and potential hydraulic injection injuries.
What are the main risks of improperly aligned hoses?
Misaligned hoses can twist or kink, leading to leaks, reduced flow, or even hose bursts during operation.
What should I do if a hydraulic hose suddenly bursts?
Shut down the system immediately, contain the leak with absorbent materials, and evacuate the area to prevent injuries.
Can I use any connector type for hydraulic hoses?
No, connectors must match the hose’s size, thread type, and pressure rating to ensure a secure, leak-proof seal.